Archives: Projects
Great Hydro Network
Three Double Shield TBMs tunnel on a Grand Scale
Project Overview
At 5,464 km long, the Yellow River is the second longest in China and provides water to over 12 percent of the country’s 1.4 billion people. Its reach falls short, however, in chronically dry Shanxi Province—a region that only receives about 473 mm of rainfall annually, and has in recent years experienced severe droughts coupled with rapid economic growth.
Sprawling equally long at thousands of kilometers, the province’s Great Hydro Network (GHN) is a mind-boggling feat of human engineering in the making. The network of tunnels will source water from the Yellow River to benefit up to 24 million people in the drought-ridden region. Once complete the tunnels will supply 2.3 billion cubic meters of water per year, improving both capacity and reliability of water supply.
Tunnels throughout the GHN project are being excavated mostly by drill & blast, with four designated TBM-driven tunnels. About half of all the tunnels under construction are very deep underground. The terrain and geological structure in the area is complex; some tunnels cross coal seams and below protected areas, underground springs and other unique geological structures. The tunnels carry construction risks including methane gas, groundwater and rock bursting.
Robbins has supplied three Double Shield machines on various lots. Contractor China Railway 18 Bureau Group Co. Ltd. is responsible for Tunnel 1 (T1), a 26 km long drive through limestone, dolomite, mudstone, amphibolite, and gneiss. Tunnels 2 and 4 (T2 and T4) are using 5.0 m and 4.2 m Double Shields, respectively, on 25 km and 15.6 km long drives. Both sites are operated by Shanxi Hydraulic Construction Engineering Bureau. Tunnel 3 (T3) is using a TBM from another manufacturer.
Geology
All three Robbins TBM-driven tunnels are located in Class III to Class V rock, and excavation was expected to be challenging from the outset. In particular the rock at T4 tested as over 27% Class V and nearly 23% softer soils, with just 36% of the tunnel in Class III rock.
Rugged TBM Design
The trio of TBMs have been designed to meet the geological challenges and long tunnel lengths. All three machines were assembled at Robbins China in Shanghai, then reassembled at the jobsites. The TBMs were built with components from Italy, Germany, Switzerland, China, and the U.S.
The machines were optimized to transport large segments quickly and safely into position to form a segment ring. The hexagonal segments are built in rings of four, each 1.2 m long. No steel reinforcement is included in the design, but gaskets between each segment help to seal them. Afterwards pea gravel is pumped into the annulus through a port in the segments to backfill voids, while a layer of grout seals them into place.
The TBMs have a uniquely long back-up system design due to the inclusion of redundant support systems– each machine is trailed by between 45 and 50 decks. Each deck is 6 to 10 m long. The redundant systems include different grout systems and at least one additional pea gravel system. This was done if one system needs maintenance or is shut down, so that the contractor can continue to bore and not affect the production of the entire line. Additional extras include redundant air compressors, as well as a rescue chamber, cafeteria, and toilet. A specialized car mover on the back-up allows two empty muck cars to be brought in with each supply train. The cars can be slid into place without needing a locomotive so that downtime in the long tunnel is minimized. The two extra muck cars have enough capacity for about two machine pushes or five rings, and can be pulled out with the next muck train.
The different diameters of the machines also necessitated unique design features. On all of the machines, squeezing the internal elements, particularly the hydraulics, into a small diameter was a challenge. The T1 and T2 machines, at 5.06 m in diameter, were able to use conventional torque cylinders in their design. The T4 machine, however, at just 4.16 m in diameter, required a redux of an old design—the lattice cylinder arrangement. The design is reminiscent of earlier Double Shield designs and offers a distinct advantage for machines less than 6 m in diameter: space. Torque arms normally occupy a large amount of space on Double Shield TBMs, and the design opens up more area to position the motors on smaller machines. It also leaves the invert open, which can aid in maintenance such as cutter changes.
Excavation and Breakthrough
T4
The small Double Shield for T4 was the first to launch in summer 2014. The machine began boring in two eight-hour shifts, with a third 8-hour shift dedicated for maintenance. The vast jobsite covers an area of 133 square kilometers and employs an army of workers. Obstacles presented themselves nearly from the outset, as ground changed quickly between soft, weak rock and hard, abrasive rock—a condition that caused frequent cutter changes. Clay clogged the cutterhead, while water inflows occurred from a lake overhead. Despite this, the machine achieved its best monthly advance of 840 m in April 2016, and by spring 2017 had excavated more than 70% of its tunnel. This machine along with T2 completed its epic bore at China’s Great Hydro Network in 2019.
T1
The machine at T1 was the next to launch in early 2015—the assembly of which was a challenge due to timing. Winter temperatures reached -25℃ while assembling, testing and launching the TBM. Heating equipment was employed and a greenhouse was installed to keep the whole TBM warm. With those strategies the TBM testing and launch ran smoothly. Since startup, the TBM has encountered very hard rock–up to 160 MPa in some areas and progress has been slow. In areas of good ground the machine has achieved as much as 1,402 m per month and as of spring 2017 the TBM had excavated about 36% of the total tunnel length.
T2
The last of the machines, for T2, was launched in spring 2015. About 320 people work and live on the jobsite that covers 20 square kilometers. The T2 machine experienced similar varying ground conditions to those at T4, vacillating between soft rock and hard, abrasive rock. Water inrushes have been encountered multiple times and have slowed down the excavation speed. Polyurethane grouting is being done to control the water inflows. The TBM has been able to achieve up to 720 m in one month, and as of Spring 2017 had excavated more than two-thirds of the total tunnel length. This machine along with T4 completed its epic bore at China’s Great Hydro Network in 2019.
Updates of this project will be posted as boring continues.
Delaware Aqueduct Repair
Single Shield TBM will bore through Difficult Conditions to fix the World’s Longest Continuous Tunnel
Project Overview
At 137 km (85 mi) long, the Delaware Aqueduct is cited in the Guinness Book of World Records as the world’s longest continuous tunnel. On any given day, it supplies 50-60% of New York City’s drinking water—a metropolis of 8.5 million people—in addition to a further 1 million that live north of the city. It is the largest such water supply tunnel in the United States. In the 1990’s, the New York City Department of Environmental Protection (NYCDEP) discovered that a section of the aqueduct below the Hudson River was leaking 75 million liters of water per day.
The NYCDEP took the decision to repair the tunnel in the largest such project to take place in the 175-year history of New York’s water supply system. A key component of the plan is a bypass tunnel that will connect up with structurally sound portions of the aqueduct and run deep below the Hudson for 3.8 km (2.5 mi). Notably, the tunnel will be bored while the aqueduct is still in service—only after excavation of the bypass will the flow be switched off to allow for the new tunnel to be connected to the existing tunnel. That shutdown is expected to last for five to eight months.
Geology
At 183 m (600 ft) below the riverbed of the Hudson, the bypass tunnel in faulted, crumbly limestone will be subject to water inflows at high pressures of up to 20 bar. A specialized 6.8 m (22.3 ft) diameter Single Shield TBM, manufactured by Robbins for JV contractor Kiewit-Shea Constructors (KSC), will bore the tunnel using components aimed at enabling efficient excavation in the difficult geological conditions.
Machine Design
The machine was designed with Difficult Ground Solutions (DGS) features for the unique conditions.
Water Inflow Control Features
Due to the 20 bar static water pressure expected on the project, a new main bearing sealing system was engineered for the project and is comprised of multiple rows of traditional lip type seals and emergency inflatable seals. In the event of a sudden inrush of high-pressure water, the TBM was designed to be quickly sealed. Knife gates over the muck chute are closed, followed by retraction of the conveyor frame and the belting from the cutting chamber. The bulkhead sealing plate is retracted and finally the stabilizer doors are closed.
Drilling & Grouting Systems
he machine is equipped with two drills in the shields for drilling through the head in 16 different positions and a third drill on the erector to drill through the shields in an additional 14 positions. Drilling and pre-excavation grouting will be a routine job to control and minimize water inflows. In addition, water-powered, high pressure down-the-hole-hammers will allow for drilling 60 to 100 m ahead of the machine at pressures up to 20 bar if necessary.
Pressure-Compensating Disc Cutters
The NYCDEP required that the TBM be capable of withstanding 30 bar of hydrostatic pressure. As such, the use of pressure compensated disc cutters became a necessity. Their unique design incorporates a pressure equalization system to keep water out and protect their bearings when the pressure is high.
Site Preparations
Two massive shafts were constructed—launch shaft 5B in Newburgh, New York, and a retrieval shaft in Wappinger on the other side of the Hudson. The shafts were constructed by drill and blast with concrete lining installed every 30 m (100 ft). Their construction was completed in March 2016, resulting in a 270 m (885 ft) deep, 9 m (30 ft) diameter shaft at Newburgh and a 197 m (646 ft) deep shaft at Wappinger.
The TBM will be launched from a bell-out chamber with a 12 m high ceiling currently under construction. The Newburgh shaft features a complex logistical setup including an elaborate hoisting system designed to service the shaft. The hoisting system will provide a lifting capacity of up to 90 metric tons to be used during TBM assembly.
Robbins worked closely with KSC to ensure that TBM components were designed and sized so all parts were less than 90 metric tons and could be lifted with the contractor’s hoist system to fit down the narrow, deep shaft window. A factory acceptance test was held in February 2017 After being shipped to the site, the TBM was assembled on a moving cradle at the bottom of the shaft, and then moved to the tunnel face.
In August 2019, The NYCDEP completed excavation of the Delaware Aqueduct Bypass Tunnel, a significant milestone in the USD $1 billion effort to repair leaks in the longest tunnel in the world. The TBM broke through a wall of shale bedrock nearly 700 feet (210 m) below the surface. Excavation of the tunnel was completed on budget and ahead of schedule.
Bahce-Nurdag High Speed Rail Tunnels
Robust Single Shield Navigates Turkey’s Hardest Rock
Project Overview
Gaziantep province, in Southeastern Turkey, is an important center of agriculture and trade divided into nine districts. With a population of nearly 1.7 million, the province is overhauling its public transportation with a rail line between the town of Bahçe and the Nurdağı district. The Bahce-Nurdag Railway Tunnel will consist of two parallel 10.1 km (6.3 mi) tunnels, excavated by both drill and blast (2.9 km/1.8 mi) and TBM (7.2 km/4.5 mi).
Geology
The complex geology of the region is affected by the East Anatolian Fault zone, making ground conditions unpredictable. Mixed ground conditions prevail on the project, and range from interbedded sandstone, quartzite, and mudstone to highly weathered shale and dolomitic limestone. High water ingress is predicted with several springs directly overhead.
Machine Design
The customized Single Shield TBM was designed with Difficult Ground Solutions (DGS). Closure gates and an emergency sealing system effectively seal off high-pressure inrushes of water. The system reduces or eliminates the amount of mud or water that can pass through the machine and gives the crew time to safely grout off the water inflows. During such an event the machine would be stopped until water inflows are reduced to the point that the TBM could begin excavation once again.
Onsite Assembly & Excavation
The Single Shield TBM was assembled at the jobsite using Onsite First Time Assembly (OFTA). The jobsite location about 20 miles (32 km) from the Syrian border complicated shipping of some parts but the assembly was completed and a launch ceremony held in January 2016.
The TBM encountered a very high strength rock mass—perhaps the highest strengths yet encountered in Turkey. Samples of meta-sandstone and meta-mudstone have tested at 223 Mpa UCS.
Breakthrough
On July 24, 2020 the first TBM-driven portion of tunneling was completed. The 8.9 km (5.5 mi) long tunnel that was excavated had some of the hardest and most abrasive rock encountered in Turkey. The TBM achieved up to 456 m (1,500 ft) per month, a result achieved with the help of a Robbins Continuous Conveyor System for muck removal.
San Francisco Central Subway
Robbins EPBs Bore Twin Tunnels Below Active BART Line
Project Overview
San Francisco’s Central Subway rail tunnels, snaking through downtown areas, were required to be driven below the existing Bay Area Rapid Transit (BART) line. Robbins provided two 6.3 m (20.7 ft) diameter EPBs to bore twin tunnels for the city’s newest rail route. The machines, operated by contractor Barnard/Impregilo/Healy JV, were nicknamed “Mom Chung” and “Big Alma”, after local historical figures.
Geology
Geological testing revealed layers of mixed ground. Two 2.5 km (1.5 mi) long tunnels were excavated through ground ranging from soft soils to thinly bedded siltstone, shale and sandstone bedrock, as well as concrete diaphragm walls. The TBMs were designed with a number of special features to efficiently manage the varied geology, navigate the steep and turning alignment, and bore in what has been rated as “Potentially Gassy with Special Conditions” by Cal/OSHA.
Machine Design and Excavation
Steering the TBMs accurately through tight curves was one of the key challenges of the project. A mixed face cutterhead was selected and designed to excavate the anticipated wide variety of ground, while active articulation was integrated between the TBM shields to lessen the risks of segment damage, ring deformation, and settlement during boring through curves. Both machines were designed to enable smooth excavation around tight turns with active articulation to excavate curves as small as 137 m (450 ft) in radius. Robbins continuous conveyors offered efficient muck removal throughout tunneling.
Low cover, nearby utilities, and sensitive structures required analyses and design precautions in order to limit settlement impact. This was especially true of a crossing directly below live rail tunnels for the Bay Area Rapid Transit (BART). Compensation grout pipes were put into place as a contingency, but were not needed as the machines passed just 3.4 m (11 ft) below the rail lines with minimal settlement. Careful monitoring of the key TBM parameters ensured that boring did not impact the critical structures over the tunnel that ran through the heart of downtown San Francisco.
Breakthrough
The first of the two machines holed through on June 2, 2014, the second followed close behind and broke through on June 11, marking the completion of the twin tunnels. Both Robbins machines achieved swift advance rates of up to 40 m (131 ft) in 24 hours and 513 m (1,683 ft) in one month.
Mumbai Water Tunnel
A National Record in Urban, Hard Rock Conditions
Project Overview
The Mumbai Water Supply Tunnel runs between the Kapurbawdi and Bhandup areas. The tunnel provides the city’s approximately 20.5 million residents with a reliable water supply, even during the seasonal monsoons that regularly contaminate Mumbai’s water resources. The basalt rock tunnel alleviates Mumbai’s current leakage problems from its aging lines and provide inhabitants with a consistent flow of clean drinking water.
Geology
Abrasive basalt rock and some fractured ground with potential for water inflows.
Onsite First Time Assembly
Onsite First Time Assembly (OFTA) was used to assemble the main bearing, lube system, back-up decks and horizontal, vertical and stacker conveyors. OFTA saved the contractor both time and money by assembling the parts at the jobsite and eliminating pre-assembly at the manufacturing facility in Shanghai, China. The OFTA process took place at the shaft bottom in a 100 m (328 ft) long starter chamber and a 50 m (164 ft) long tail tunnel. TBM components were lowered into the shaft using mobile and gantry cranes.
Excavation and Breakthrough
Due to the urban location of the tunnel, the TBM was launched from a 109 m (357 ft) deep shaft, and its launching sequence included an initial start-up excavation of 50 m (164 ft) with vital back-up decks connected to the TBM using cables. The first bore began March 30, 2012 and upon completion, the decks were lowered and a continuous conveyor system was installed for muck haulage and storage.
Robbins provided both the TBM and conveyor system for the project, as well as Field Service personnel to monitor the equipment and assist with daily upkeep and inspection.
Although the machine was ultimately a success, it did experience its fair share of challenges during the 21-month bore. Difficult ground, including basalt rock, fractured ground, and water inflows, was encountered throughout the tunnel. The tunnel team took all precautionary measures and advanced slowly. The crew maintained good ventilation throughout execution and utilized consistent dewatering to deal with water inflows.
Ground support also played a critical role in poor ground: The rock support system and ring beam erector reduced downtime and stabilized rock. Challenging ground conditions, combined with the sheer depth of the 109 m (357 ft) tunnel, made the machine’s excellent advance rates a particular achievement.
By the end of TBM tunneling, the Robbins machine had reached high rates of 870 m (2,855 ft) per month and 58 m (188 ft) per day, both records for TBM tunneling in India. The contractor stated that the good rates were achieved because of “good performance of the machine and a conveyor system for muck haulage in place of conventional methods.”
Gerede Water Transmission Tunnel
Robbins Crossover Excels in Turkey’s Most Demanding Tunnel to Date
Project Overview
The Gerede Water Transmission Tunnel is arguably one of the most difficult projects attempted in the world of tunneling. Dozens of fault zones and intense water pressures up to 20 bar are just a couple of the challenges to overcome. Prior to Robbins involvement, three standard Double Shield TBMs, originally supplied by a European manufacturer, attempted to bore the tunnel. Of the three, two became irretrievably stuck following massive inflows of mud and debris. In 2016, a Robbins Crossover XRE machine was launched to excavate the final 9 km (5.6 mi) of the 31.6 km (19.6 mi) long water supply tunnel. Due to severe and chronic droughts in the capital city Ankara, the water line has been deemed a national priority. Once complete, the supply line will draw water from the Gerede River and will be the longest water tunnel in Turkey.
Geology
Turkey is in a tectonically active region controlled on a grand scale by the collision of the Arabian Plate and the Eurasian Plate. At a more detailed level, a large piece of continental crust almost the size of Turkey, called the Anatolian block, is being squeezed to the west. The block is bounded to the north by the North Anatolian Fault and to the south-east by the East Anatolian fault. Geology in the fault zones tends to be highly variable and unstable.
At Gerede, the Anatolian Fault Zone certainly presented many obstacles. Geologic testing and borehole samples showed a mix of volcanic rock including tuff, basalt, and breccia, giving way to sedimentary formations like sandstone, shale, and limestone, all punctuated by fault zones that contained clay and alluvium. The Crossover machine also faced an aquifer system that caused high-pressure water inrushes of 26 bar.
Machine Design
Due to the geology, the Gerede machine required a convertible cutterhead optimized for hard rock. The cutterhead was designed for ease of conversion between hard rock and EPB modes, and cutter housings can be fitted with either disc cutters or tungsten carbide tooling. In addition, the cutterhead is designed to operate in a single direction. The setup, which is used on all XRE machines, allows for greater efficiency while excavating, with lower power requirements and less chance of regrind. To cope with difficult ground, the Gerede machine was also equipped with special gearing.
In order to protect the machine from the expected high water pressure, an extensive sealing system was put into place. Around the main bearing, there is an outer row of six seals and an inner row of three seals. Between each seal, the cavity is filled with grease to ensure a constant pressure. In the event that the machine is shut down and an inrush of water overtakes the machine, a pressure sensor will detect this presence of water and flush the seal system with grease in order to continually protect the seals. The articulation joint and the gripper and stabilizer shoes are sealed off in the same manner.
Perhaps one of the most important parts of the Gerede TBM design is the screw conveyor. Because of the potential for massive amounts of water, the machine must have a sealed screw conveyor. However, running rock through a screw conveyor can be highly abrasive. To account for potential wear, the screw was been designed with replaceable wear plates along its entire length. The screw itself was also made up of short sections that can be removed and replaced if needed. Multiple access hatches were included for maintenance of the wear plates, while two large, removable outer casings could accommodate the change-out of entire screw sections.
Due to the unpredictable ground conditions, it was necessary to detect and grout off zones of concern wherever possible in order to protect the machine from loose ground and water pressure. The machine utilized a standard array of twelve Ø100 mm ports angled at 7° that are equally spaced around the rear shield. Each port was sealed by a ball valve until it was needed for probing. Ten of the same-sized ports were also located straight through the forward shield for probing and grouting. Six additional hatches were built into the pedestal at the front of the machine. The hatches could be used with a pneumatic percussive drill in the center section of the cutterhead.
Excavation
The Robbins XRE TBM was launched in summer 2016, using some components from the original Double Shield TBM back-up, as well as the remaining segments being stored for the project. Crews excavated a bypass tunnel to one side of the stuck Double Shield TBMs and the Robbins TBM components were walked in through the south portal. The machine was assembled using Onsite First Time Assembly (OFTA) in an underground launch chamber. Water flow made it difficult to get the materials to the machine, but this was overcome by designing custom flat cars equipped with hydraulic lifts to transport bigger sections of the TBM through the tunnel to the build chamber.
The Robbins machine began boring at a slight angle to the rest of the tunnel, bypassing the stuck machine before gradually meeting up with the original tunnel alignment. The machine was required to be used in EPB mode as it encountered water pressures up to 26 bars, alluvium, flowing materials, and clay. Water pressure was lowered by draining the ground water through the rear shield probe drill ports, which were equipped with normally-closed ball valves. Probe drilling became routine after advancing 50 meters (164 feet) past the section that buried the original Double Shield TBM. During its bore the TBM encountered a total of 48 fault zones. Despite the constraints of the difficult geological conditions and the time it took to reach the TBM within the tunnel, crews achieved a best day of 29.4 m (29.4 m (96.5 ft), best week of 134.6 m (441.6 ft) and a best month of 484 m (1,588 ft).
Breakthrough
Excavation of Turkey’s longest water tunnel came to an end on December 18, 2018. With tunneling complete, the pipeline opened in March 2019. The tunnel will convey water from the Gerede River to Çamlıdere Dam, which provides potable water for the Ankara city water system.
Túnel Emisor Poniente (TEP) II
Project Overview
A Robbins Crossover (XRE) TBM was chosen to bore a 5.8 km (3.6 mi) tunnel as part of Mexico City’s wastewater management efforts, making it the first Crossover machine to bore in North America. The 8.7 m (28.5 ft) diameter machine includes features of both a hard rock single shield and an EPB in order to “cross over” into vastly different types of ground. Once complete, the tunnel will prevent flooding in urban areas and will convey sewage to the area’s first wastewater treatment plant, affecting the lives of 2.1 million people.
Geology
The tunnel path travels through a mountain with cover as high as 170 m (560 ft), through fault zones and in a section with cover as low as 8.0 m (26.2 ft) above the tunnel crown. Much of the tunnel consists of andesite rock with bands of tuff, and softer material in fault zones as well as an 874 m (2,870 ft) long section in soft ground at the end of the tunnel.
Machine Design
The Robbins XRE TBM features components like a convertible cutterhead that can be changed from a Hard Rock to EPB design, a removable belt conveyor and screw conveyor, and multi-speed gearboxes to increase torque for tunneling through difficult ground. Breakout torque is one way that the shielded TBM can propel itself through fracture zones without becoming stuck—multi-speed gear boxes can be activated to achieve high torque at a low speed, similar to how an EPB operates. With multi-speed gear boxes, the cutterhead can be freed in bad ground where it might otherwise become stuck. In hard rock, the TBM can operate in a standard low torque, high RPM mode.
The Crossover XRE has other strategies in its arsenal to deal with difficult ground. The unique TBM was designed to bore below several valleys with expected water inflows. In the event of a high water inflow, a guillotine gate located on the muck chute is able to seal off the mixing chamber from the rest of the machine. In this way the TBM can passively hold high water pressures while the crew takes measures to dewater and consolidate ground.
The machine is equipped with continuous probe drilling, with a wide drilling range to investigate ground ahead of the machine. In addition to the standard probe drill, a canopy drill provides another ring for grout drilling or forepoling close to the cutterhead and in the top 120 degrees of the tunnel, while a second probe/grout drill is located further back on the machine, allowing two different patterns of holes.
Excavation
The Crossover machine was launched in August 2015 in a hard rock configuration and mounted with 20-inch diameter disc cutters—a risky move given that the first sections of tunnel were in softer soils before the TBM hit more solid rock. The machine’s advance rates picked up quickly, with project records set in December, and again in January after the machine achieved a best day of 42.8 m (140 ft) and a best week of 185.1 m (607 ft).
Early in 2016 the TBM hit the first of several contact zones, a 30 m (98.4 ft) wide fault of fractured and blocky rock. While the excavation through the contact zone was slow going, progress picked up again in the more competent andesite rock. After an intermediate breakthrough in March 2016 into an 80 m (262.5 ft) deep shaft followed by inspection and maintenance, the TBM continued on.
By June 2016, the TBM was boring in fairly competent rock and had achieved two national records for TBM advance—one for excavating 57 m (187 ft) in one day and another for boring 702.2 m (2,303.8 ft) in one month.
While boring in fractured andesite rock in autumn 2016, the TBM encountered a naturally occurring cavern believed to be the result of either a rock fall in a transition zone, or an old, underground lake body that had eroded the rock away. The cavern was approximately 90 cubic meters in size, including about 57 cubic meters of unstable floor area. The TBM was stopped and immediate measures were taken to fill the cavern.
Changing Modes
By the end of October 2016, the TBM had reached the final section of soft ground. In this final zone of low cover, the distance from the top of the tunnel to the surface is less than 1.5 times the machine diameter, and the ground has the consistency of reconsolidated soil. The residential area meant that subsidence had to be kept to a minimum, and the decision was taken to convert the Crossover machine to EPB mode.
Conversion of the TBM to EPB mode required multiple steps. The conversion process started with the modifications of the cutterhead, adding the piping for the new foam lines, changing the hard rock bucket lips into the EPB soft ground scrapers, and removing the muck buckets characteristic of a hard rock TBM. The removable plates on the cutterhead were changed to alter the opening ratio from Hard Rock optimized to EPB optimized (from 7.9% to 18.95%). Other steps include installing mixing bars into the bulkhead, switching out the TBM belt conveyor to a screw conveyor, altering the fluid system for EPB additives, and installing tails seals and articulation seals for pressurized boring.
The machine was completely converted and ready to bore at the start of 2017. The machine started its latest section with about 18 m (59 ft) of cover, which was reduced due to the ground slope to just 12 to 14 m (39 to 46 ft). By March 2017, the TBM had performed well, with just 517 rings (about 775 m, 2.543 ft) left to bore. The TBM’s best day of production in soft ground was 13 rings (19.5 m, 64 ft) in only one 12-hour shift—impressive results despite the limited boring hours due to the residential area above. Final breakthrough occurred in late May 2017.
Jaipur Metro
Twin EPBs Excavate Under Historic Structure
Project Overview
The city of Jaipur, India is encircled by a wall six meters high and three meters thick, with seven gated openings. It is below these delicate and iconic structures that Jaipur’s first Metro, Line 1, travels. For this project, Contractor Continental Engineering Corporation (CEC) decided to refurbish their two 6.52 m (21.3 ft) diameter Robbins EPBs. The machines bored twin tunnels 2.3 km (1.4 mi) in length, directly beneath the historic Chandpole Gate.
Geology
In this particular project, the geology was not anticipated as a main concern. The bores consist mainly of silty sands, with a minor amount of clay and gravels. However, the geological conditions coupled with the extremely low overburden in the area of the launch shaft, especially the section passing beneath Chandpole gate, was cause for major concern.
The Machines
The contractor opted to refurbish its two 6.52 m (21.3 ft) diameter Robbins EPBs originally used for the New Delhi Metro Project. The Robbins EPBs were refurbished in India, and customized for the Jaipur project. The original machines for New Delhi bored a straight tunnel and did not require active articulation, but a 430 m (1,410 ft) radius curve in Jaipur necessitated that the machines be articulated. The shields were essentially cut in half and another section put in to form articulation joints in the contractor’s casting yard. In addition, new a+b grouting systems were installed as well as sophisticated tunnel guidance systems to monitor each machine’s position.
Boring Below the Historic Chandpole Gate
Chandpole gate, one of the seven, is directly above the bore path for the Line 1 extension, and serves as a historical landmark. The construction materials of the walls and gate consist of irregularly-sized pieces of stone cemented together with lime mortar and faced with a sand and lime mortar render that provide little to no resistance to tunneling-induced settlement. Contractually the allowable limit for surface settlement was set at 4 mm (.16 in). Yet, there was also an Indian archeological law in place that made the stakes a bit higher. It states, “Whoever destroys, injures, mutilates, defaces, alters, removes, disperses, misuses, imperils or allows to fall into decay a protected monument, or removes from a protected monument any sculpture, carving image, bas-relief, inscription or other like object, shall be punishable with imprisonment for a term which may extend to six months with a fine which may extend to five thousand rupees or with both.”
The key to boring beneath the gate without any adverse effects relied on refining the TBM operating parameters before the TBM reached the zone of influence. As this had been achieved, these parameters were maintained after the restart and similar results were achieved up until ring No. 75, where surface heave increased slightly. Due to the increase in heave the EPB pressure was reduced to 1.2 bar and cutterhead speed to 1.1 RPM. These changes reduced the heave to within tolerance. Although vibrations levels were minimal, as the TBM approached the gate the cutterhead speed was further reduced to 1.0 RPM to reduce the risk of damage by vibration. The machine passed beneath the gate and through the zone of influence without incident using these parameters. The maximum recorded settlement in the vicinity of the gate was 2 mm (.08 in) and absolutely no adverse effects were sustained to the gate. The lessons learned on the first drive were applied to the second drive and TBM II also passed beneath the gate with minimal settlement and no damage to the gate.
Kargi Hydroelectric Project
Robbins Double Shield TBM Overcomes Challenging Conditions and Spurs the Design of Crossover TBMs
Project Overview
Driven through a mountainside with 600 m (1,968 ft) of cover in Central Turkey, the Kargi Kizilirmak Hydroelectric Project is one of the most challenging tunneling projects ever completed in the region. A 10-m (32.8 ft) diameter Double Shield TBM was supplied to contractor Gülermak to bore the headrace tunnel that would divert water from the dam to the powerhouse. The entire tunnel, with both TBM and drill and blast portions, is 11.8 km (7.3 mi) in length. The project generates 470 GWh of power annually for project owner Statkraft, an amount sufficient enough to supply approximately 150,000 homes. The extremely challenging ground conditions of this project made it necessary for the machine to be modified in-tunnel. The results of which largely contributed to the creation of the Crossover machines used today.
Geology
The expected geology along the tunnel alignment consisted of Kirazbasi complex Kargi ophiolites (including sandstone, siltstone and marl) for the initial 2,300 meters (7,545 ft), followed by 1,000 meters (3,280 ft) of Kundaz metamorphites (including marble, metalava and metapelite), and the remaining 8,500 meters (27,887 ft) consisted of Beynamaz Volcanites (including basalt, agglomerates and andesite). The anticipated strength of the rock was up to 140 MPa. Multiple fault zones and transition zones added to the complexity of the geological conditions.
Launch
Almost immediately after launch in early 2010, the machine encountered geology that was substantially more problematic that was described in the geological report. The geology consisted of blocky rock, sand, and clays. 80 meters (262 ft) into the bore the TBM became stuck in a section of collapsed ground. As a countermeasure that was immediately put into place to avoid the cutterhead becoming stuck in the blocky material, crews began boring half strokes and half resets. Despite these measures, the machine encountered a section of extremely loose running ground with high clay content. Another collapse occurred in front of the cutterhead and the weight of the material trapped the cutterhead.
After assessing all the available options, it was decided that a bypass tunnel would be required. Robbins Field Service assisted Gülermak with bypass tunnel design and work procedures to free the cutterhead and stabilize the disturbed ground. Blasting techniques were ruled out due to concern over further collapses caused by blast induced vibration; hence, the excavation was undertaken using pneumatic hand-held breakers. Hopes that the section of bad ground would be an isolated occurrence were quickly proved wrong, and the actual complexity of the geology became apparent. Six more tunnels were needed within the first 2 km (1.2 mi) of tunneling.
Both the contractor and manufacturer worked together to develop and improve bypass tunneling and hand tunneling techniques, resulting in an average bypass tunnel construction time of just 14 days. All tunnels were completed safely and in a timely manner, though there were of course significant delays associated with the downtime. Despite the setbacks of these multiple events, the TBM did succeed in crossing numerous faulted sections that would have trapped a machine with less power. Bypass tunneling was successfully completed and at that point the section of bad ground was believed to be an isolated one.
The Beginnings of the Crossover TBM
In order to improve progress in the difficult conditions, the contractor, owner, consultants, and Robbins engineers worked together to generate solutions. The contractor, with the assistance of the field service team, installed a Robbins custom-built canopy drill and positioner to allow pipe tube support installation through the forward shield. Drilled to a distance of up to 10 m (33 ft) ahead of the cutterhead, 90 mm (9 cm) diameter pipe tubes provided extra support across the top 120 to 140 degrees at the tunnel crown. Injection of resins and grout protected against collapse at the crown while excavating through soft ground. As a result of successful use of the probe drilling techniques, Gülermak was able to measure and back-fill cavity heights above the cutterhead in some fault zones to over 30 m (98 ft) and, in addition, was able to help detect loose soil seams and fractured rock ahead of the face.
To further mitigate the effects of squeezing ground or collapses, custom-made gear reducers were ordered and retrofitted to the cutterhead motors. They were installed between the drive motor and the primary two-stage planetary gearboxes. During standard boring operations the gear reducers operate at a ratio of 1:1, offering no additional reduction and allowing the cutterhead RPM to reach design speeds for hard rock boring. When the machine encountered loose or squeezing ground the reducers were engaged, which resulted in a reduction in cutterhead speed but the available torque was increased by nearly double. The net effect of the modifications allowed the Double Shield TBM to operate much like an EPB in fault zones and squeezing ground with high torque and low RPM—these methods effectively kept the machine from getting stuck. In addition, short stroke thrust jacks were installed between the normal auxiliary thrust to double total thrust capabilities.
The TBM design changes gleaned from Kargi were not considered to be isolated, and immediately began to inform the design of Robbins’ new line of dual-mode type machines, termed Crossover TBMs. Crossover TBMs are also called hybrid or Dual Mode machines, and are able to “cross over” into distinct types of geology. Crossover TBMs feature aspects of two TBM types, and are ideal for mixed ground conditions that might otherwise require multiple tunneling machines.
Innovative Results
Despite the slow progress initially, the Robbins Double Shield TBM made some remarkable advances once modifications were in place, which essentially made it a Double Shield TBM with Crossover features. An advance rate of 600 m (1,986 ft) in one month was achieved in March 2013 and a project best of approximately 723 m (2,372 ft) was achieved in spring 2014, including a daily best of 39.6 m (130 ft) in April 2014. In so doing the TBM significantly outperformed a drill and blast heading progressing from the opposite end of the tunnel. Crews at that heading progressed in relatively good ground conditions for 4 km (2.5 mi), where they achieved advance rates of nearly 300 m (984 ft) per month. The TBM bored 7.8 km (4.8 mi) of the tunnel in total, making its final breakthrough in July 2014.
Grosvenor Decline Tunnel
First TBM to be used for Mining Tunnels in Queensland
Project Overview
The Grosvenor Mine, a greenfield coal operation, was the first to utilize TBM technology for mining tunnels in Queensland. Owner Anglo American opted for an 8 m (26 ft) diameter Robbins Dual Mode “Crossover” TBM and continuous conveyor system, which was assembled on location using Onsite First Time Assembly (OFTA) with onsite support from Robbins’ experienced Field Service team. The Crossover XRE TBM was picked over the traditionally-used roadheader method for several reasons, including excavation speed and tunnel maintenance. The machine bored two decline access tunnels at grades of 1:6 and 1:8, one for conveyors and another for people and equipment.
Geology
Ground conditions varied throughout each tunnel. Both drifts contained geology consisting of mixed soil and rock conditions, with the first 300 m (984 ft) or so of each tunnel containing the majority of the mixed ground such as soft clays and soils.
Machine Design
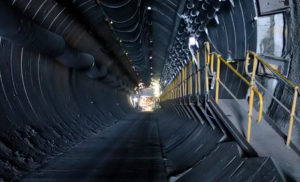
OLYMPUS DIGITAL CAMERA
The machine’s Crossover capabilities enabled it to operate in both hard rock and mixed ground. In addition, the TBM was required to operate in gaseous conditions. The unique TBM design included a cutterhead capable of interchanging hard rock and soft ground cutting tools, a two-stage center-mounted screw conveyor, a “quick removal” shield system, and flame-proof machine components due to the possibility of methane gas in the underground environment. A machine with EPB capabilities was chosen not only due to the presence of softer ground, but also to contain the methane gas where it could then be diluted or safely removed from the tunnel.
Excavation and Breakthrough
Construction on the Grosvenor project began in July 2012. The first of the decline tunnels, for conveyors, was excavated between the end of December 2013 and the beginning of May 2014, after achieving advance rates of up to 90 m (295 ft) per week. The Quick Removal System was a success, allowing the TBM inner core to be retracted back to the surface from a 160 m (525 ft) depth using specially designed transport dollies. In order to transport the machine to the next tunnel 2 km (1.2 mi) away, the TBM had to be split into two sections and required a large 600 metric ton lift.
The machine was re-commissioned for the men & materials tunnel with a new set of shields, and commenced boring in November 2014. Excavation was completed in 88 days at an average of 10.9 m (35.7 ft) per day, with a best day of 25.2 m (82.7 ft). The TBM averaged 70 m (229.7) a week, about 14 times faster than a roadheader. The bore itself was similar to the first, with few challenges encountered other than elevated methane gas levels that required several temporary stoppages in order to safely remove the gas from the tunnel. Final breakthrough was reached on February 9, 2015. Upon completion of the second tunnel, the machine shields were again left in place to provide continuous support.