Без категории
第一台掘进机的输送机
Modern Achievements
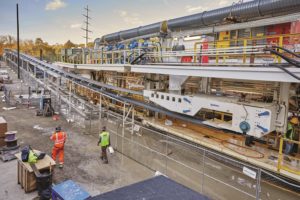
The 100th conveyor system has been refurbished and customized for the job in a process that Robbins has been perfecting for decades.
There are many elements that contribute to the success of a project: having an accurate report of ground conditions, choosing the proper equipment, having a well-trained team operating the tunnel boring machine—and behind it all—the utilization of a high-quality conveyor system. As tunneling machines evolve and bore at continuously faster rates, rapid muck removal becomes more important than ever. Robbins conveyor systems are capable of moving more than two thousand US tons of muck per hour—saving time and money on every project that uses the complete system.
In Akron, Ohio, a major milestone has been reached for Robbins conveyors. Running behind a Robbins 9.26 m (30.4 ft) diameter Crossover TBM is the 100th Robbins Continuous Conveyor System supplied for muck removal—more than any other TBM conveyor supplier has sold. The conveyor in Akron is just one landmark event in the long history of Robbins conveyors, the start of which can be traced back to the first ever documented use of a continuous conveyor system behind a TBM.
Pioneering Muck Removal
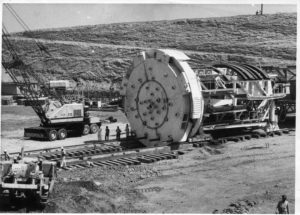
No roads were at the site in West Pakistan so goods were transported by rail car, requiring surveying of hundreds of bridges from the port city of Karachi.
The prototype for the conveyor systems we know today was developed by James S. Robbins in 1963 and was built using a Goodman coal-mine conveyor instead of muck cars which were more commonly used during that period. The conveyor ran behind what was, at the time, the largest TBM in the world. The 11.2 m (36.7 ft) diameter Robbins Main Beam was built for the Mangla Dam Project in what was then known as West Pakistan. The 4.3 km (2.7 mi) long tunnel was built to control water flow from the Jhelum River for use in agriculture and hydro-electric power.
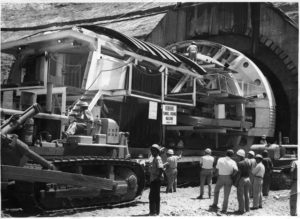
Temperatures at the jobsite climbed up to 53 degrees C (127 degrees F) in the shade.
The conveyor design had originally been used for coal and potash mines and was adapted for use behind the TBM. An extendable belt was side-mounted in the tunnel, leaving room for man-access and rail tracks to carry materials. Belt tension was maintained using a belt cassette. “They were able to operate continuously. It worked like a charm—and then the extensible conveyor was forgotten by the industry because it was perceived by contractors and owners as too much of an investment,” explained Dick Robbins, former President and CEO of The Robbins Company, in a 2013 article for World Tunnelling. It would be another 30 years after the successful completion of the Mangla Dam tunnel until conveyors became a standard means of muck removal in the tunneling industry.
Persistently Moving Forward
Conveyors have come a long way since their first use. Unlike the system used for the Mangla Dam project—which was limited to the use of a straight belt—conveyors can now wrap around curves and bring rock vertically up a shaft to the surface. “The control system, along with monitoring systems, has dramatically improved,” says Dean Workman, Robbins Director of Conveyors, Cutters, and SBUs. “The components have all been enhanced, giving a much longer life to the conveyor system. Contractors are using the same conveyors on multiple projects with minor refurbishments between projects.” While the basic function of a conveyor has stayed the same—muck hauling—the quality of conveyor systems has certainly changed.
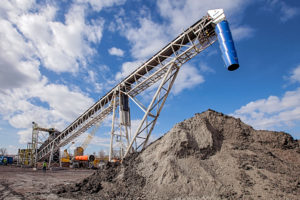
Did You Know: At least 75% of all world records achieved by TBMs were done with a continuous conveyor system for spoils removal rather than muck cars.
In a new design that is being used for the Los Angeles Purple Line Extension, continuous conveyors have gained another ability, they are now able to change direction. The unique system can be flipped to accommodate two machines boring parallel tunnels eastward before being re-launched to bore west. Due to the narrow launch shaft, modular components were designed to save space, and were built using a kit of secondhand parts, showcasing the long-life conveyor systems are capable of. “We are always looking to improve the design and function of the system,” says Workman, “modular components are a benefit to the contractor when installing, maintaining, and shipping the equipment.”
As progress continues and new technology provides advancements for the industry, The Robbins Company continues to uphold the pioneering spirit that James S. Robbins brought to tunneling with his trailblazing developments.
Read More:
Robbins Conveyor Systems
Conveyor Spec Sheet
100th Conveyor