Author: Lok Home
Notice of Retraction and Apology
To all Visitors of our Site: I declare that our website contained information that was inaccurate, and in retrospect, was offensive and disrespectful to our longtime Customer and highly qualified construction Client, Obayashi Corporation of Japan, along with their Joint Venture (JV) Partners, Taisei Corporation and Kosei Corporation. The referenced Project Site name is Hiroshima Expressway 5 Shield Tunnel Project and the Robbins Technical Article titled https://www.robbinstbm.com/grout-or-not/, which states as if the JV selected the wrong type of TBM for the Hiroshima Project.
We retract the statements made in our article such as, “Contractors who are used to tunneling in soft ground may not realize that when using a Slurry TBM in rock, inspections must be frequent due to increased cutter consumption. We have seen this borne out on recent projects such as the Hiroshima Expressway Line 5 in Japan” because these statements were not based on facts and were incorrect. This statement reads as if the contractor did not review other optional TBM types, when in fact, the JV did indeed study all TBM types and methods to excavate this Express Tunnel.
There were additional incorrect statements made in the Article as follows:
- The same paragraph of the Article continues,”…, and they (contractor) were expecting up to 13 bar water pressure. This high pressure water zone was only in a small section of the overall tunnel length, about 5 percent.“
- The Article further states, “The contractor in Hiroshima had grouted off from the surface a planned safe zone in which to inspect the cutterhead without requiring a hyperbaric intervention, but this strategy did not go according to plan. The abrasive rock damaged the cutters and cutterhead before they could reach the safe zone, resulting in unplanned delays“.
- The same paragraph of the Article continues, “…grout off from the surface a planned safe zone…“.
The reason for choosing a Slurry type TBM was not solely based on the high water pressure but was also a result of the JV’s extensive review of all aspects of the tunnel requirements.
There was no plan to grout a “safe zone/safe haven” from the surface as other plans for cutter changes were in place and such plans have proven to be effective over numerous cutter change events.
Robbins commits to have more peer review and where a Client is involved, to have the Client review prior to presenting such data on our website.
The Light at the End of the Tunnel: The Positive Side of Seattle’s SR99 Project
Seattle is the founding city of The Robbins Company, and a place where I lived for nearly 15 years and commuted on SR99 while working at Robbins early in my career. As such, the new SR99 Viaduct Replacement Tunnel Project is of great interest to me.
The industry is all too familiar with Seattle’s SR99 Tunnel and its TBM, known as “Big Bertha”. More specifically, much has been written with regards to the TBM needing repairs after about 300 m of boring. The TBM is the world’s current largest at 17.5 m in diameter, and is excavating a 2.7 km long drive.
TBM Tendering
Robbins was a relatively new entry into the EPB/soft ground tunneling business when tenders were called for the latest SR99 project in 2011, and we made a concerted effort to get the order for this particular TBM. We teamed up with Japanese TBM manufacturer Mitsubishi Heavy Industries (MHI) to get the order. Robbins has had an association with MHI for more than 20 years, with jointly-designed machines operating around the world on projects in India, China, the U.S., and more. MHI has built over 1,000 EPB machines and in my opinion, the Japanese TBM manufacturers are further advanced in EPB technology than their European and American counterparts.
Through the process of trying to receive this order, we learned a lot about the geology, as well as the contractors’ and TBM’s specification requirements. The contractor Dragados, one of the JV partners and very well-experienced in soft ground tunneling technology, developed a high-level specification for the TBM suppliers. All of the prospective TBM suppliers were required to quote and if successful, supply to this standard. We eventually stepped out of the tendering process to supply this TBM, as the lower prices and greater assumption of contract risk offered by our competitors made the TBM supply an impractical business option for us.
Tough Tunneling
The current situation at the SR99 project is more positive than media tend to paint it. The project design consultant did a commendable job on laying out the tunnel route and building in a contingency plan. Boring through glacial till, even with modern TBMs, is never an easy task as previous projects like the Brightwater Conveyance Tunnels have taught the city of Seattle. This is doubly so along the Seattle waterfront, which includes manmade fill, utilities, and buried refuse. In such ground, TBMs can encounter rapidly changing geology; pockets of groundwater; abrasive soil; and manmade objects such as unmapped disused pipes; foundation piles; etc.
Aware of the problems that can develop while using an EPB TBM in glacial till under a city with a lot of backfill, the SR99 designer wisely developed a contingency plan. The strategy, in addition to pre-planned safe havens, involved a “shake down” stretch of tunnel, which ran under no buildings. If problems did occur repairs to the TBM could be made by sinking a surface access shaft at this location. Unfortunately the need for that repair event occurred shortly after the machine commenced excavation.
Why there were failures of the cutterhead seals, and potentially the cutterhead main bearing, is yet to be determined. I doubt there will be any signs of failure of the main bearing when the crews get to inspect it. However, all parties involved are wisely taking precautions and installing a new main bearing in addition to the seals.
Bertha’s Lessons
The Seattle Tunnel Partners and WSDOT have in place a panel of experts to advise them on the highly technical details of the TBM design. I personally know several of these experts and they are well qualified to recommend and supervise the necessary repairs and procedures to get the TBM into a condition where it is able to finish this tunnel.
Having been in the TBM supply business for quite a few years, I unfortunately have to admit having been in a similar (fortunately not as well published) situation as the TBM supplier on more than one occasion. This situation–significant TBM problems at the beginning of boring—can result from many different factors and is not unique to the SR99 project. In fact, Robbins recently had a similar situation (admittedly on a smaller scale in terms of both public and financial impact) on a project in Turkey known as the Kargi HEPP. Despite extensive pre-planning, unexpected ground was encountered, which resulted in several in-tunnel stops and machine modifications in the first few hundred meters of the tunnel. What happens in these situations is you pull in the best minds with the most experience and immediately analyze the problem. The ultimate fix often ends up as a multi-level solution. You must ensure you have the problem under control, plus take additional measures to monitor the vulnerable components and operating procedures. At Kargi, this process resulted in the remainder of the project being finished without significant TBM problems. Without a doubt a similar process is going on at SR99 with Hitachi Zosen engineers, the contractor’s specialists, and the city’s board of experts.
Being one who is keenly interested in this project, I believe that this TBM will soon be back to boring with a new completion date, which will be fulfilled. I am optimistic that this project will one day be seen as a positive in the tunneling industry, where many lessons were learned and advancements were made. Such advancements will be put to use in Seattle and in other cities that greatly benefit from the excavation of more underground infrastructure.
Research and Development: A Sneak Peek at the Next Generation of Disc Cutters
R & D is important in any industry, and it is no less true for the tunneling industry. Evolution, even if it is incremental, is where most research and development successes are made. Such improvement forms part of the competitiveness among manufacturers and thus begets further improvements. I also believe it is our obligation, as equipment manufacturers, to assist the market in driving down the costs of tunneling in general by improved product performance and product life.
Take, for example the research and development going on with our disc cutters: Robbins disc cutters have improved dramatically since the 1950s when they achieved their first success at 11 inches in diameter in crystalline limestone of 190 MPa (28,000 psi) UCS. Today’s disc cutters do reach 20 inches in diameter and cost-effectively excavate rock strengths of 400 MPa (60,000 psi) UCS, all while lasting much longer than their predecessors.
That being said, we believe there is always room for improvement. We are working hard right now to develop customized cutters for EPB tunneling in soft and mixed ground, and to optimize those designs so they can excavate under high pressure. In hard rock, we are researching and testing new steels, and developing monitoring systems to allow contractors to plan cutter changes.
Here’s a snapshot of what research and development is going on in the cutter department, both in the lab and in the field:
Improved Metallurgy
Working with the University of Trondheim and the Norwegian government, we are commencing a program of laboratory and field testing to improve the materials making up the disc ring itself. We are always testing new materials in order to find the most durable materials based on the ground conditions. An example of past cutter research in the lab can be seen below:
Pressure Compensated Disc Cutters
We are currently developing improved disc cutters specifically for use on EPB and Slurry TBMs at high pressures of plus 10 bars, using a testing module in our Kent, Washington facility. The module duplicates a pressurized operational environment so that we can analyze how the cutter seals perform under pressure—the design is in its 3rd or 4th generation with continuous improvements being made.
Remote Cutter Monitoring
Our remote cutter monitoring system is a breakthrough that we have been field testing for four years. The system is now undergoing full scale testing on three Main Beam TBMs at Malaysia’s Pahang Selangor Raw Water Tunnel. The setup allows crews to more closely monitor the actual working conditions and cutter wear. We project, through this system, to increase the TBM utilization of each machine by 3 to 4% and to reduce cutter cost by 10%.
We’re also working on expanding this wireless system to EPB and Slurry machines, so that monitoring of cutter wear and rotation can be used while those machines are in closed mode. This would be a highly beneficial development, because under pressure the detection of tool wear is difficult. Our goal here is to reduce or better plan interventions because of tool wear.
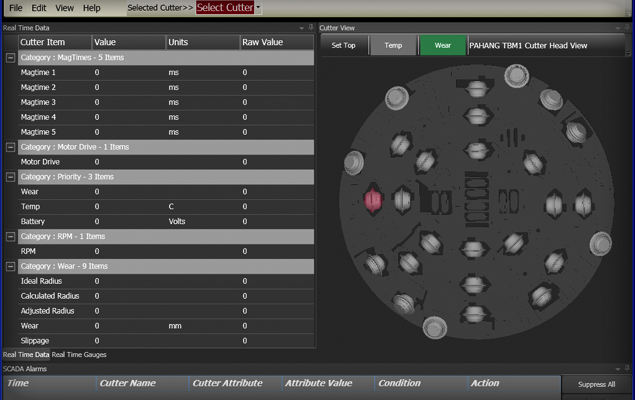
Sample screenshot of the Robbins remote cutter monitoring systems. Failed cutters are highlighted by a color on the screen.
Robbins Atmospheric Cutter Change System (RACCS)
Finally, we are developing a system to allow cutter changes at atmospheric pressure on large diameter EPBs. This atmospheric cutter change system is superior to other systems on the market because it allows muck to flow through. Other systems on the market are very prone to clogging. Each spoke of an EPB cutterhead will contain a chamber at atmospheric pressure. Cutters can be rotated from the pressure zone into the chamber to allow for efficient and relatively fast cutter changes.
The development is also significant because a huge cost of operating large diameter EPBs is associated with intervention for cutter inspection and change. We are currently building a large test fixture for this system, which will analyze how RACCS reacts in sand, gravel, boulders, clay, and mud conditions under pressure.
Conclusions
These research and development projects are all aimed at solving a particular problem or shortfall—with the objective to bore more meters per month. It is not the only area where we have research and development underway, as we have similar programs to investigate improvements of the probe drilling and lube systems on our TBMs. The process is usually rigorous, as designs need to be tested and re-tested in both the lab and the field.
I am not a big believer in “Big Step” research and development as was tried in earlier days at Robbins with the Mobile Miner and the Bore Pack. Such “Big Step” research and development usually leads to disappointment and heavy cost for the client and the company.
However, improvements like the 19” cutters and the cutter monitoring systems are and will be big wins for the contractors and for Robbins.
R & D is important in any industry, and it is no less true for the tunneling industry. Evolution, even if it is incremental, is where most research and development successes are made. Such improvement forms part of the competitiveness among manufacturers and thus begets further improvements. I also believe it is our obligation, as equipment manufacturers, to assist the market in driving down the costs of tunneling in general by improved product performance and product life.
Take, for example the research and development going on with our disc cutters: Robbins disc cutters have improved dramatically since the 1950s when they achieved their first success at 11 inches in diameter in crystalline limestone of 190 MPa (28,000 psi) UCS. Today’s disc cutters do reach 20 inches in diameter and cost-effectively excavate rock strengths of 400 MPa (60,000 psi) UCS, all while lasting much longer than their predecessors.
[Photo of a disc cutter]
That being said, we believe there is always room for improvement. We are working hard right now to develop customized cutters for EPB tunneling in soft and mixed ground, and to optimize those designs so they can excavate under high pressure. In hard rock, we are researching and testing new steels, and developing monitoring systems to allow contractors to plan cutter changes.
Here’s a snapshot of what research and development is going on in the cutter department, both in the lab and in the field:
Improved Metallurgy
Working with the University of Trondheim and the Norwegian government, we are commencing a program of laboratory and field testing to improve the materials making up the disc ring itself. We are always testing new materials in order to find the most durable materials based on the ground conditions. An example of past cutter research in the lab can be seen below:
Pressure Compensated Disc Cutters
We are currently developing improved disc cutters specifically for use on EPB and Slurry TBMs at high pressures of plus 10 bars, using a testing module in our Kent, Washington facility. The module duplicates a pressurized operational environment so that we can analyze how the cutter seals perform under pressure—the design is in its 3rd or 4th generation with continuous improvements being made. [Photo of testing facility?]
Remote Cutter Monitoring
Our remote cutter monitoring system is a breakthrough that we have been field testing for four years. The system is now undergoing full scale testing on three Main Beam TBMs at Malaysia’s Pahang Selangor Raw Water Tunnel. The setup allows crews to more closely monitor the actual working conditions and cutter wear. We project, through this system, to increase the TBM utilization of each machine by 3 to 4% and to reduce cutter cost by 10%.
We’re also working on expanding this wireless system to EPB and Slurry machines, so that monitoring of cutter wear and rotation can be used while those machines are in closed mode. This would be a highly beneficial development, because under pressure the detection of tool wear is difficult. Our goal here is to reduce or better plan interventions because of tool wear.
[Show screen shot of monitoring system]
Robbins Atmospheric Cutter Change System (RACCS)
Finally, we are developing a system to allow cutter changes at atmospheric pressure on large diameter EPBs. This atmospheric cutter change system is superior to other systems on the market because it allows muck to flow through. Other systems on the market are very prone to clogging. Each spoke of an EPB cutterhead will contain a chamber at atmospheric pressure. Cutters can be rotated from the pressure zone into the chamber to allow for efficient and relatively fast cutter changes.
The development is also significant because a huge cost of operating large diameter EPBs is associated with intervention for cutter inspection and change. We are currently building a large test fixture for this system, which will analyze how RACCS reacts in sand, gravel, boulders, clay, and mud conditions under pressure.
Conclusions
These research and development projects are all aimed at solving a particular problem or shortfall—with the objective to bore more meters per month. It is not the only area where we have research and development underway, as we have similar programs to investigate improvements of the probe drilling and lube systems on our TBMs. The process is usually rigorous, as designs need to be tested and re-tested in both the lab and the field.
I am not a big believer in “Big Step” research and development as was tried in earlier days at Robbins with the Mobile Miner and the Bore Pack. Such “Big Step” research and development usually leads to disappointment and heavy cost for the client and the company.
However, improvements like the 19” cutters and the cutter monitoring systems are and will be big wins for the contractors and for Robbins.