Year: 2023
Use of a Tunnel Boring Machine on Nepal’s First and Second TBM-Driven Tunnels
Nepal’s mountainous terrain has historically been a challenge to tunnel through. That very terrain also holds great promise for hydropower – a resource that the country is now beginning to tap into. Launched in October 2022, a 6.4 m Double Shield TBM is making Nepal’s hydropower plans into a reality as it bores the 13.1 km headrace tunnel for the Sunkoshi Marin Diversion Multipurpose Project (SMDMP). The tunnel is connected to a 28.6 MW surface powerhouse on the Marin River.
The SMDMP is the machine’s second tunnel: on its 12.2km first tunnel (the Bheri Babai Diversion Multipurpose Project/BBDMP), the TBM finished nearly one year early and achieved 1,202 m advance in one month. It was the first instance of TBM use in the country.
In this paper, we examine the successes and lessons learned in Nepal’s mountainous conditions during excavation of both the SMDMP and BBDMP.
Robbins Double Shield Sets Record in Nepal
In the southern Himalayan mountains of Nepal, a Robbins Double Shield TBM has crossed into new territory. At the end of June 2023, the machine turned in an impressive advance rate of 1,224.13 m in one month – a record for Himalayan geology and believed to be a TBM record within the Indian Subcontinent. Launched in October 2022, the 6.4 m diameter machine has been boring the 13.3 km headrace tunnel for the Sunkoshi Marin Diversion Multipurpose Project (SMDMP).
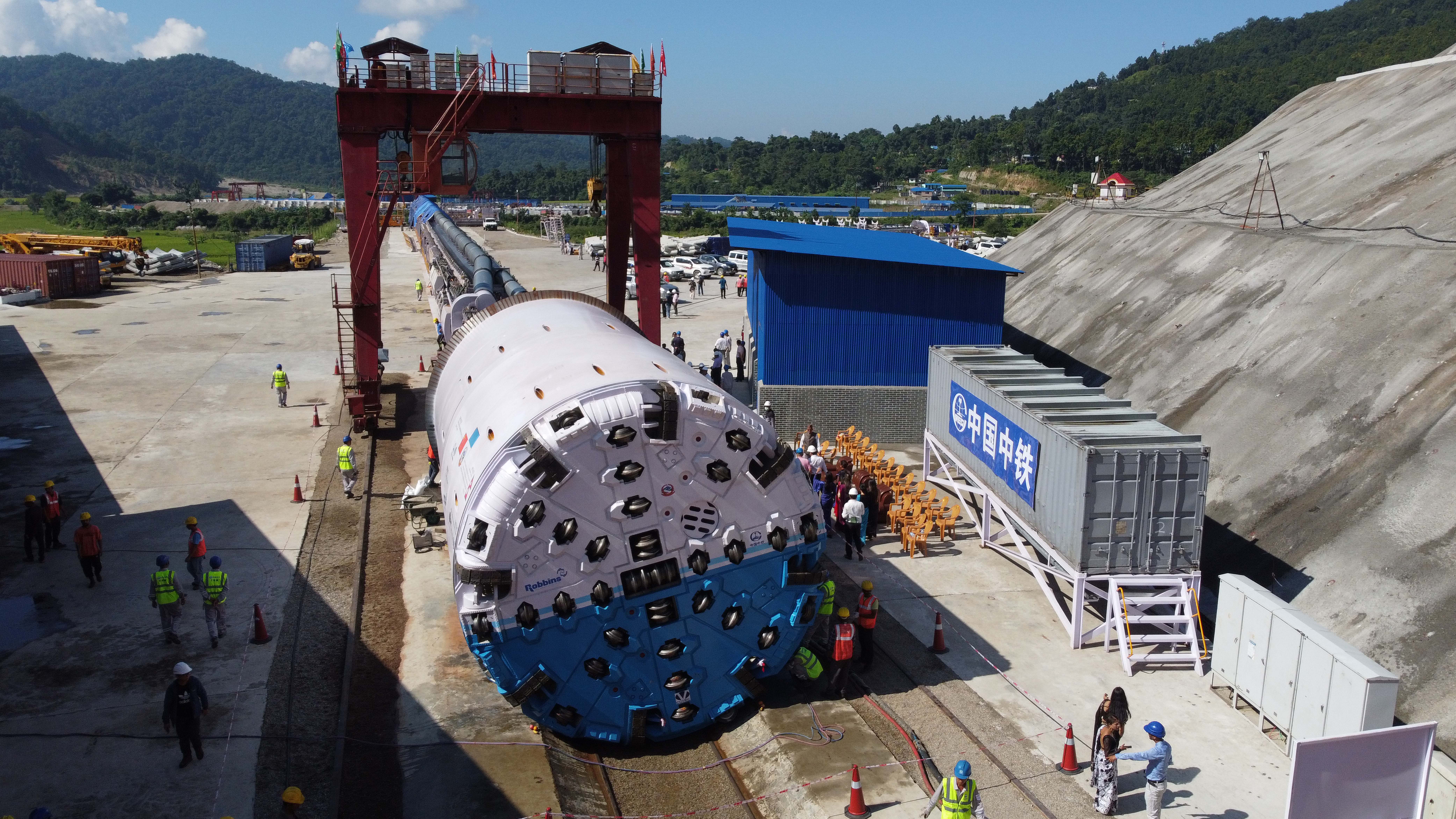
At the end of June 2023, a 6.4 m diameter Robbins Double Shield TBM achieved an impressive advance rate of 1,224.13 m in one month.
Multiple factors played into the successful result. “Proper TBM selection for the existing subsurface is the key reason for success. The Double Shield is the most logical TBM type and has played a major role in this successful journey. Operation, maintenance, and an experienced, dedicated team are additional factors,” said Mitra Baral, Project Director of SMDMP under the Department of Water Resources and Irrigation, part of Nepal’s Ministry of Energy, Water Resources & Irrigation.
Contractor Covec/B-2 echoed those sentiments: “The designed adaptation of the TBM & backup provided by Robbins is verified to be scientific and good under the geology, which are Siwalik stratum and the lower Himalayan zone–both quite complex and variable. The performance of the equipment is generally stable,” said Covec/B-2’s Project Manager, Mr. Liu Feng Fan.
Contractor B-2/COVEC (China Overseas Engineering Group Co. Ltd and China Railway No. 2 Engineering Group Co Ltd) have navigated the Robbins TBM through two major fault zones with challenging and varied conditions ranging from highly jointed mudstone, sandstone and conglomerate to quartzite, granite, and more.
The record result is all the more impressive considering the adversity the machine has overcome to date. Approximately 2,156 m into the excavation the machine became stuck in jointed sedimentary rock, requiring nine days of intensive work and a bypass tunnel to free it. As the machine progressed to more than 4 km in, the geology changed to dolomite, slate, schist, quartzite and phyllite. The machine became stuck a second time 4,669 m in due to collapsing and squeezing ground, requiring a further 27 days of work to release it.
Despite the challenges early on, the machine and its experienced crew have persevered. Currently the TBM is more than 8.3 km into the tunnel and boring in high strength granite, having passed through the two major fault zones predicted on the tunnel alignment. “Timely support from Robbins has made for a good relationship and teamwork. It has been quite important for the success of our project,” said Mr. Liu.
Prajwal Man Shrestha, General Manager of Robbins Nepal, emphasized that the successful results thus far are a milestone for the use of TBM tunneling in the country: “There are now private sector hydropower developers considering the use of a TBM for their project instead of the conventional D&B method. Very soon we may see that most tunnels longer than 6 or 7 km will be exploring the possibility of using TBMs on their project.”
As for the future of tunneling in Nepal, Mr. Baral is positive it will continue to grow and evolve: “Many TBM projects could be planned for many different areas. Taking into consideration that Nepal is a mountainous country with complex geology, tunnels are indispensable not only for irrigation and hydropower but also roads, railways, water supply, and even metro lines in the cities.”
Final Breakthrough at Bahçe-Nurdaği Railway
In June 2023, a resilient 8.0 m diameter Robbins Single Shield TBM completed its second tunnel at Turkey’s Bahçe-Nurdaği Railway. The machine completed 9.6 km of tunneling, adding on to the 9.2 km it completed in its initial railway tunnel in 2020 – for a total of more than 18 km bored.
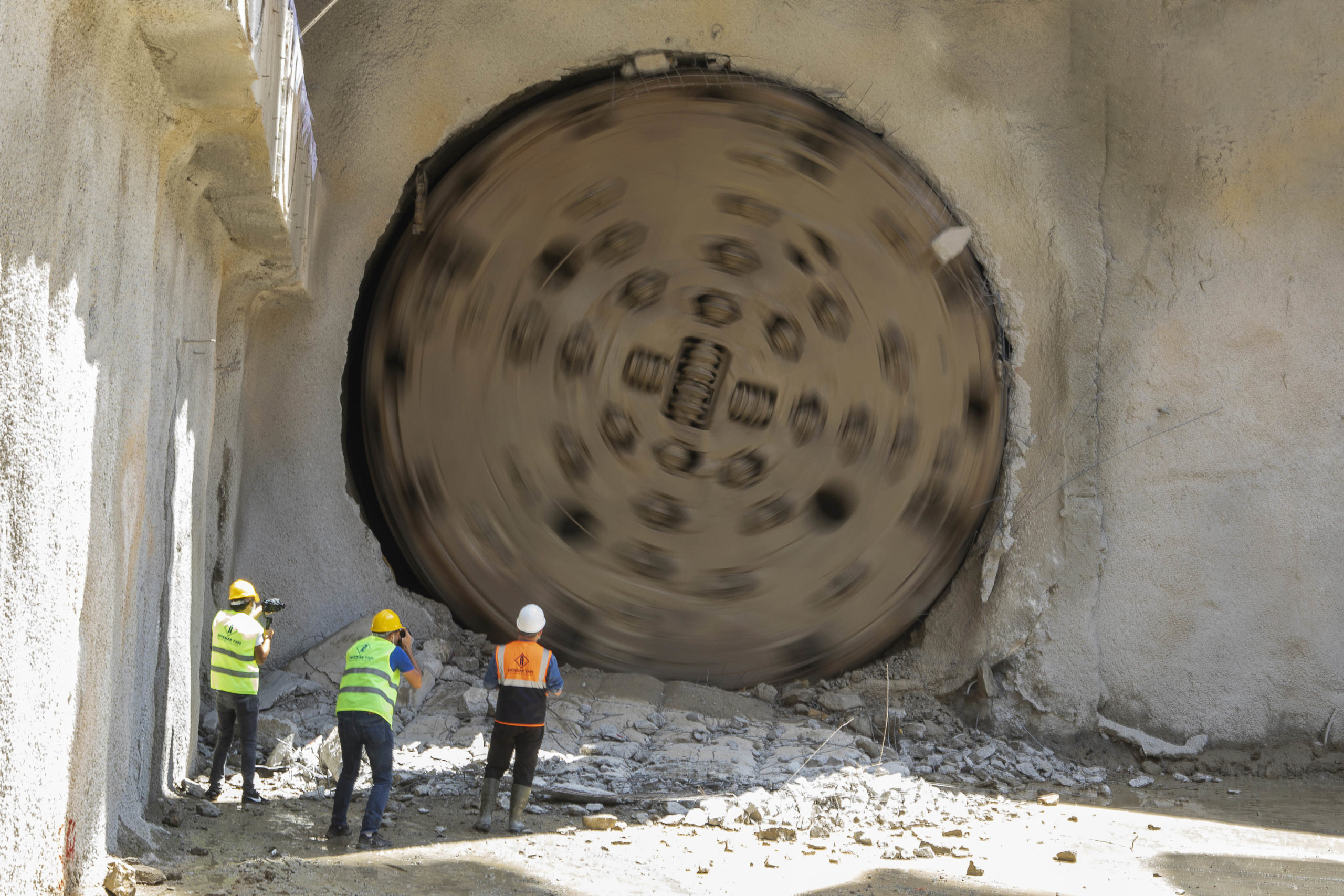
The Robbins TBM completed 9.6 km of tunneling, adding on to the 9.2 km it completed in its initial railway tunnel in 2020 (pictured) – for a total of more than 18 km bored.
“We are very proud to complete this tunnel in difficult rock formations with our excellent team by utilizing an extremely powerful and strong Robbins Single Shield TBM,” said Deniz Şahin, TBM Chief for contractor İntekar Yapı Turizm Elektrik İnşaat San. ve Tic. Ltd. Şti.
Geology in the second tunnel was comparable to the first, including incredibly hard and abrasive metasandstone with quartz, with an average of 220 MPa (31,900 psi) UCS and a Cerchar abrasion value of 3.87. The rock has some of the most extreme hardness and abrasiveness ever measured in Turkey.
After its first bore in the difficult ground, the machine required some inspection and repairs. “Robbins Field Service was always available when we requested,” said Şahin. “The biggest repairs we undertook with Robbins Field Service technicians were the main bearing seal change and checking and repairing of the TBM before launching it on the twin tunnel after the completion of the first tunnel. Both operations were completed in a short time due to good planning with Robbins technicians.”
The machine began its second bore in February 2021, achieving a best monthly advance rate of 411 m. “During tunneling we performed a normal maintenance program as given in the TBM manual, and the machine had minimum downtime, which shows the durability of Robbins TBM in very hard and abrasive rock,” said Şahin.
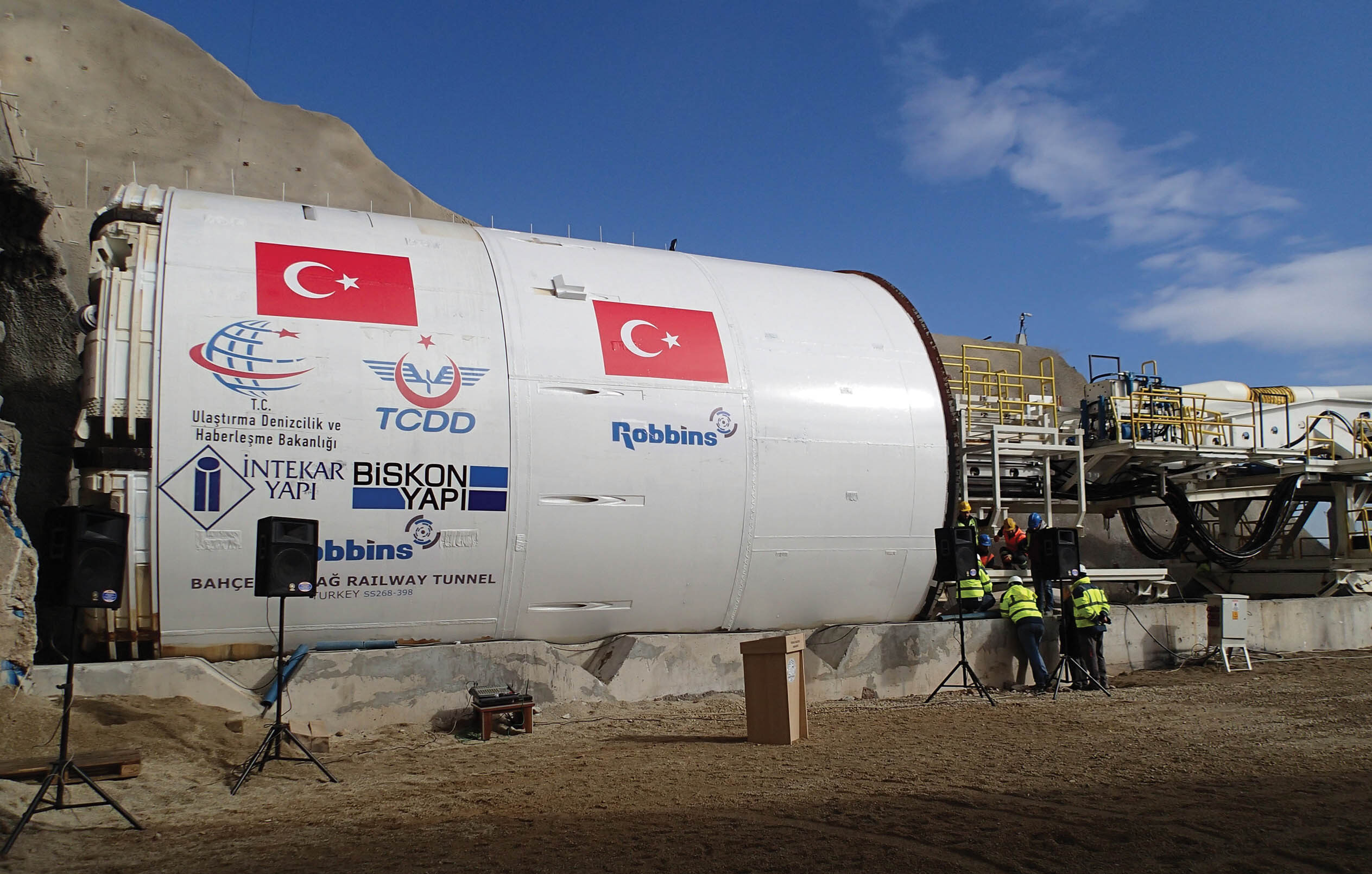
The Robbins Single Shield TBM was designed to bore in incredibly hard and abrasive geology including metasandstone with quartz – some of the hardest rock ever encountered by a TBM in Turkey.
“The Robbins TBM has performed extremely well in this project with minimal downtime and good advance rates to complete the longest twin tube railway tunnels in Turkey,” said Yunus Alpagut, Robbins representative in Turkey.
The twin rail tunnels, for owner Turkish State Railways Directorate (TCDD), will provide an economic boost to a region recovering from two consecutively devastating earthquakes with magnitudes of 7.8 and 7.6 that occurred in February 2023. The project site is located very close to the intersection of two large active fault zones, the East Anatolian Fault (EAF) and Dead Sea Fault (DSF). The tunnels were inspected after the event and were found to have sustained only minor cracking in a few segments. The new rail line will provide service between the towns of Bahçe and Nurdağı, and is part of the TCDD’s plan to overhaul the railway connection in southeastern Turkey by providing a shorter, faster route in one of the country’s busiest railway corridors.
Record-Setting Large Diameter Mixed Ground Tunneling in Turkey: The Eşme-Salihli Railway Tunnel
Large diameter tunneling has historically been seen as a challenge. Add into the equation mixed ground conditions, and it becomes a task that may seem insurmountable. How-ever, a recently completed tunnel in Turkey is a flagbearer for changing the mindset towards these challenging tunneling scenarios that are becoming more frequent. A 13.77 m diameter mixed ground Rock/EPB TBM bored the Eşme-Salihli Railway Tunnel at rates of up to 721.8 m in one month, making it the fastest TBM ever recorded over 13 m in diameter. The machine began its bore in altered gneiss, then passed through mélange consisting of gneiss, sandstone, claystone, mudstone, quartz, and silt. By the end of the bore the machine was excavating in mainly mudstone. Core drillings were taken every 200 m prior to boring.
In this paper, we detail the project as well as analyze factors contributing to the fast advance rates. The factors include TBM choice and system design, ground conditions, TBM utilization rates and downtimes, as well as maintenance practices, crew expertise and technical support, all of which have a part to play in the overall advance rates and successful outcome. Recommendations are made as to best practices in order to achieve good advance rates on similar large diameter, mixed ground tunnels.
Lessons Learned During Excavation of the Incredibly Challenging Yin Han Ji Wei Water Diversion Tunnel
The 2022 breakthrough of an 8 m diameter Main Beam TBM at China’s Yin Han Ji Wei project was a triumph of technology and perseverance – crews at the 17.5 km long tunnel encountered over 14,000 rock bursts, some with energy as high as 4,080 kJ. The rock, consisting of mainly quartzite and granite, was estimated to have a rock hardness of between 107 and 309 MPa UCS, with high abrasivity and a maximum quartz content of 92.6%. The incredibly challenging tunnel also experienced at times severe water inflows, with one particular event exceeding 20,000 m3 of water in one day from a single point. In-tunnel ambient temperatures peaked at 40 degrees Celsius and 90% humidity. Throughout the challenges, the crew and support teams found ways to persevere – whether through unique ground support, or increased monitoring and analysis. In this paper, we will examine the successes and lessons learned in the incredibly challenging ground conditions, determining what worked best to confront each condition as it came up. Recommendations will be made towards what could be used successfully on future projects that en-counter these geological features.
Record-Setting Tunnel Boring Below Lake Ontario at the Ashbridges Bay Outfall Tunnel
The 3.5 km long Ashbridges Bay Outfall in Toronto, Ontario, Canada was a challenging drive set below Lake Ontario. After a remote machine acceptance due to the global pandemic, an 8 m diameter Single Shield machine launched in March 2021 from an 85 m deep shaft and began its bore in shale with limestone, siltstone and sandstone. During excavation, the TBM and its crew bored a city-wide record of 30 rings in one day, or 47 m of advance. This paper will cover the unique project, from TBM acceptance through to launch, tunneling in difficult conditions, and completion in 2022.
Enhanced Probe Drilling & Pre-Grouting on Hard Rock TBMs
While probe drills are not strictly necessary for all projects, the incorporation and use of probe drills and pre-grouting adds capability and insurance to boring operations. Water ingress and unstable ground can be resolved before becoming a problem and resulting in costly delays through the use of enhanced, 360-degree probe drilling setups. To do this, proper design of the array of drill ports in the shield, matched to the possible ground conditions, is critical. For ground with exceptional water and instabilities expected, additional probing locations are low-cost additions that can lower risk and increase efficiency. In this paper we will look at recent and ongoing projects including the Lower Meramec Tunnel and Jefferson Barracks Phase 2. We will detail the design of those probe drill arrangements, and our overall recommendations for probing/grouting systems that best suit challenging ground conditions and keep projects running smoothly.
Tunneling in Turkey: The Esme Salihli Railway
Large diameter tunneling in mixed ground has historically been seen as a challenge, but a recently completed tunnel in Turkey has changed the conversation. A 13.77 m diameter Crossover XRE TBM bored the Esme Salihli Railway Tunnel at world-record-setting rates of up to 721.8 m in one month, making it the fastest TBM over 13 m in diameter. What allowed the project to achieve such high advance rates?
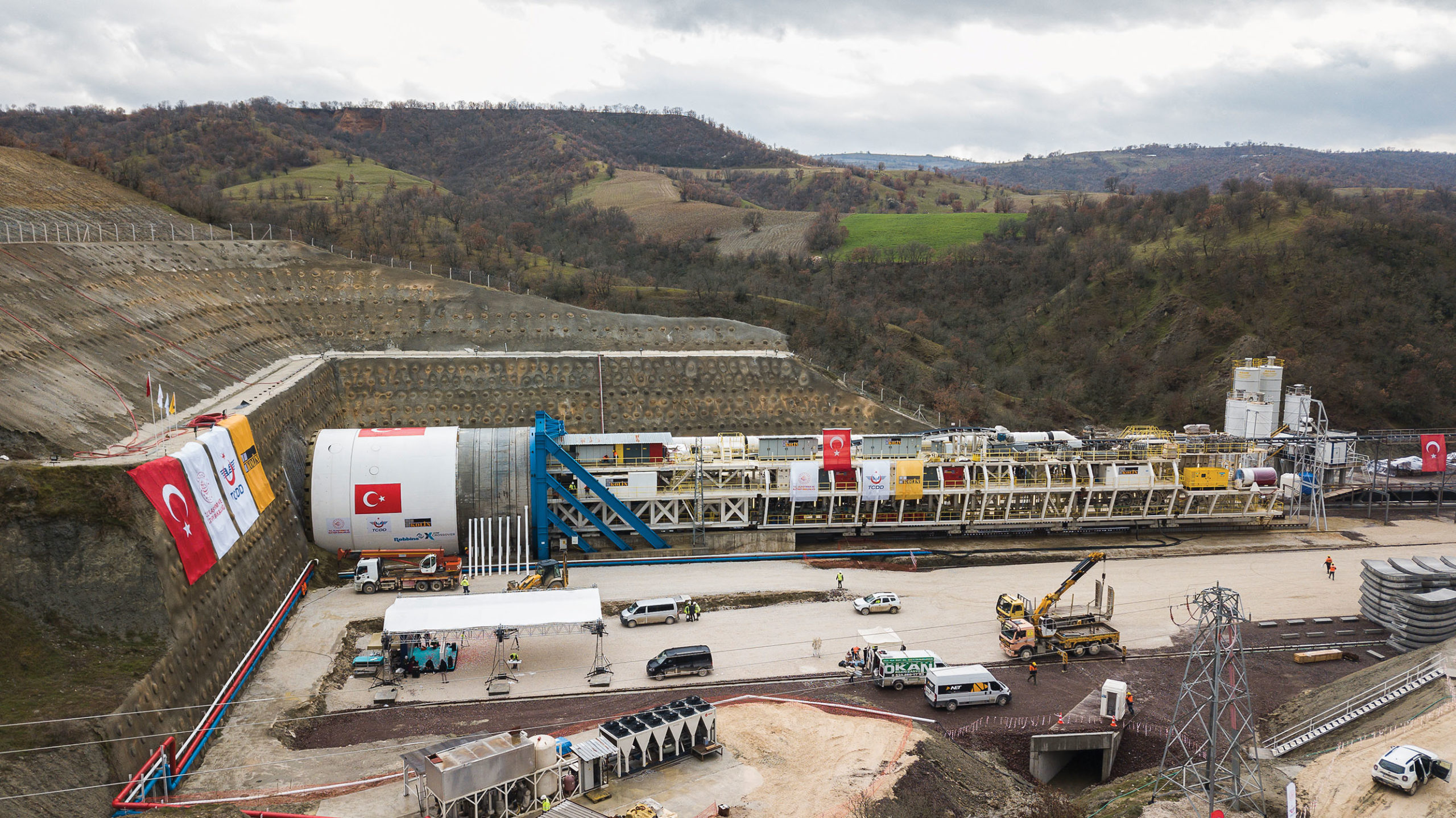
A Robbins Crossover machine that bored Turkey’s 3.05 km (1.90 mi) Eşme-Salihli Railway Tunnel through mixed conditions including sandstone, gravelstone, claystone, and siltstone for contractor Kolin Construction.
Machine Design for Variable Geology
The Eşme-Salihli Railway Tunnel is a short section of high-speed railway, measuring 3.05 km (1.90 mi) through mixed conditions. Contractor Kolin Construction conducted 15 core drillings at 200 m intervals prior to the start of construction, with results predicting occasional groundwater and weak rock between 5 to 9 MPa (720 to 1,300 psi) UCS, with the potential for a gassy environment. Rock and soil types included sections of gneiss, sandstone, claystone, mudstone, quartzite, and silt.
A dual mode rock/EPB TBM design was created for the project, in which no design elements were sacrificed in the engineering: The machine was fully capable of operating in 100% EPB mode or 100% Hard Rock Single Shield Mode. The TBM was designed for sections of hard rock and mixed ground, in highly variable conditions. For details on the design, check out this technical paper.
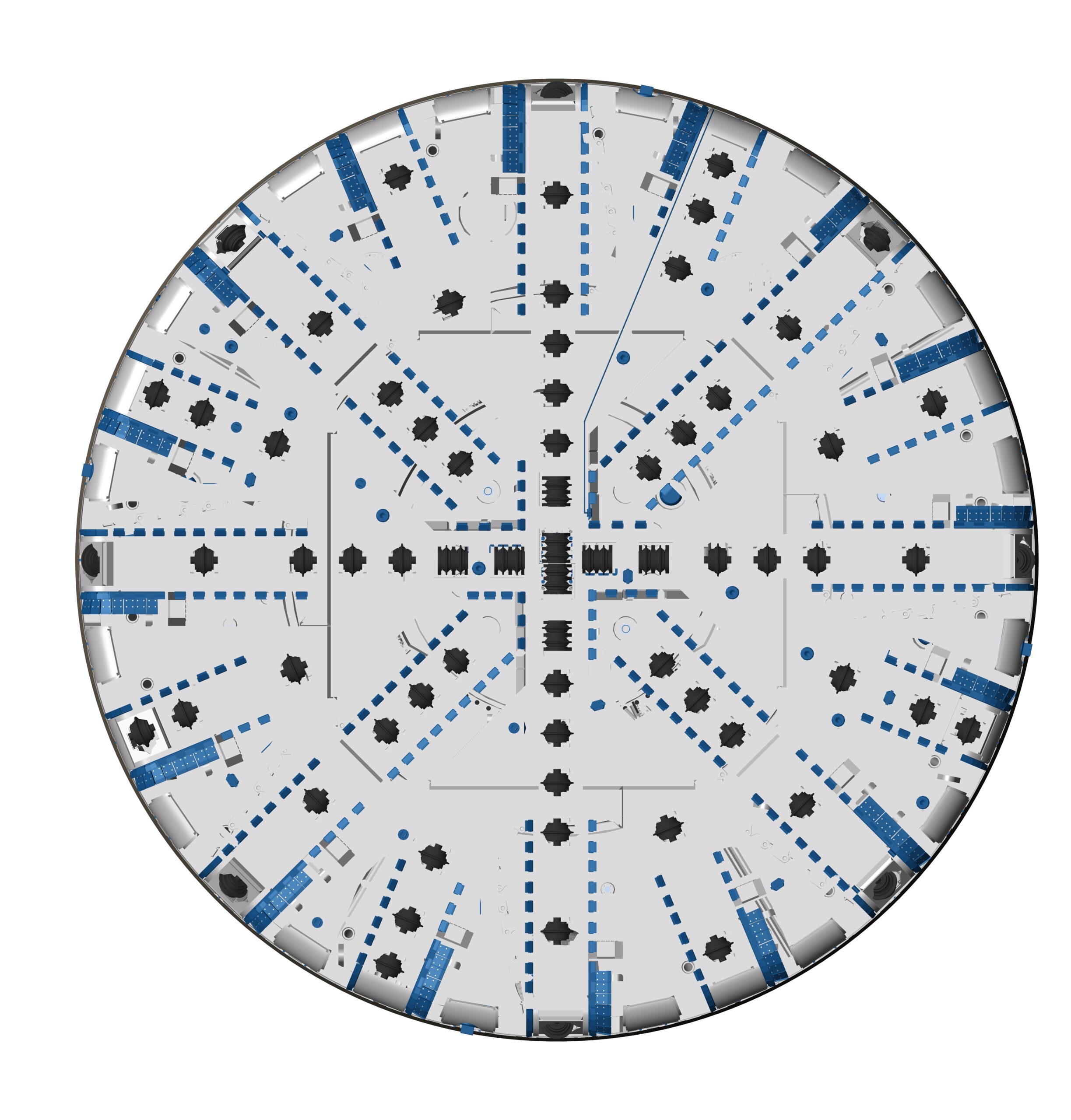
The cutterhead in hard rock mode.
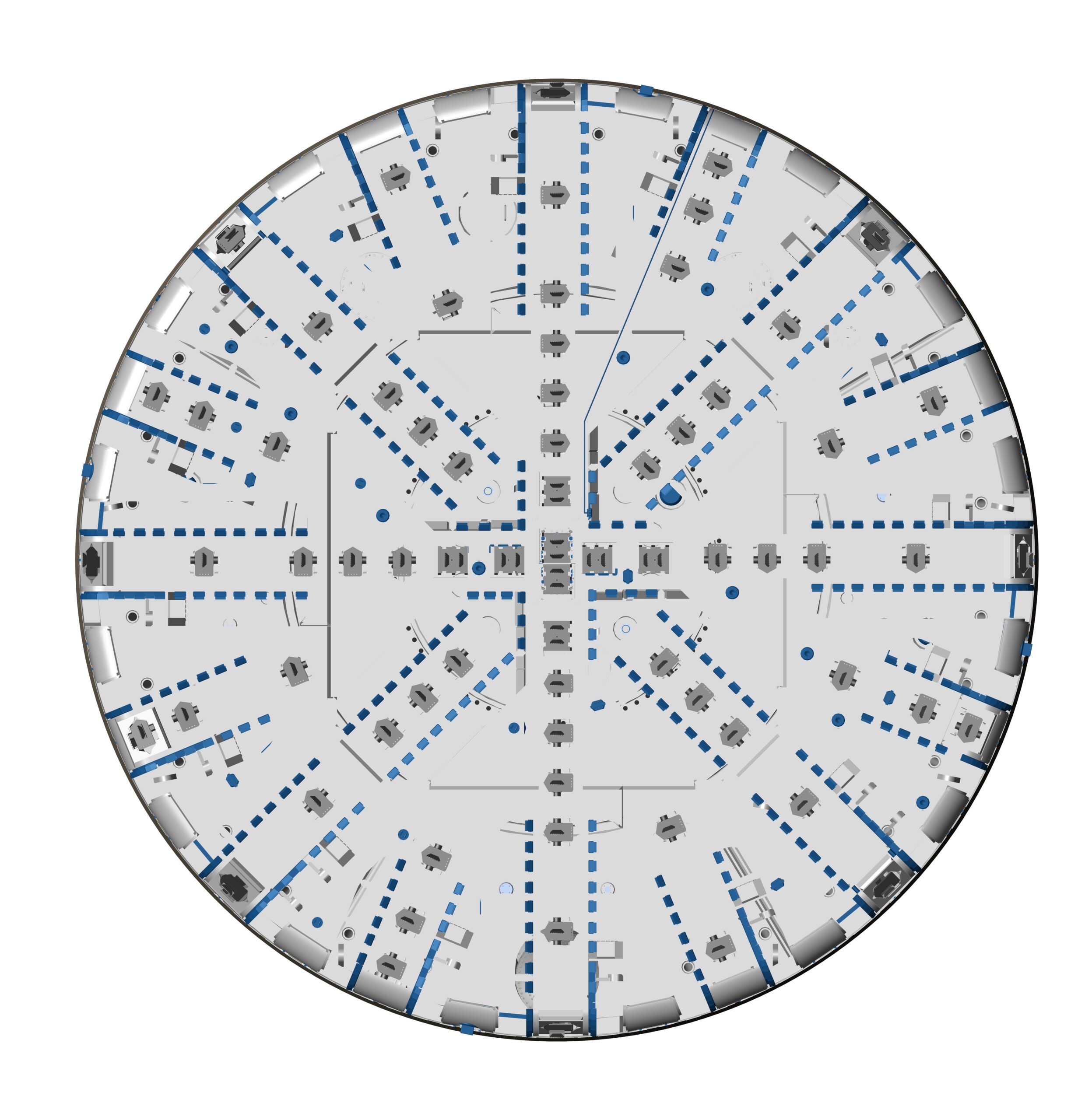
The cutterhead in EPB mode.
Epic Results
The 13.77 m Crossover XRE machine launched on its 3.05 km (1.90 mi) bore at the end of March 2021. While some of the crossover features proved beneficial the TBM was able to utilize the screw conveyor for mucking for the complete tunnel drive, which was a further benefit for the project’s overall schedule.
What allowed the machine to perform at high rates of advance? Utilization charts reveal that 38% of the total time was spent on excavation, 27% on ring assembly, 21% on planned downtime such as maintenance, and 14% on unplanned downtime.
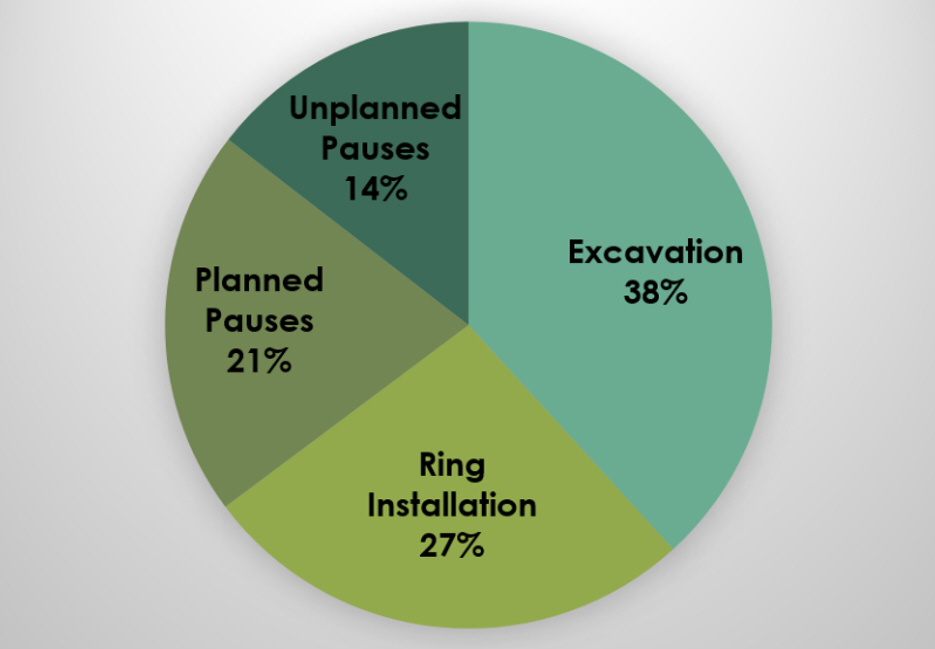
Productivity pie chart.
When looking at planned downtime, the most time was spent on cutterhead maintenance at 28%, followed by crew breaks at 22%. An average machine push took 60 minutes, while ring builds averaged 42 minutes.
Delays caused by mechanical, hydraulic or electrical failures were very low. The contractor cited the main reasons for minimal downtime, and thus high advance rates, as regular planned maintenance, cleaning, an experienced team, and an adequate supply of spare parts. Ultimately the tunnel was completed in just 6.5 months.
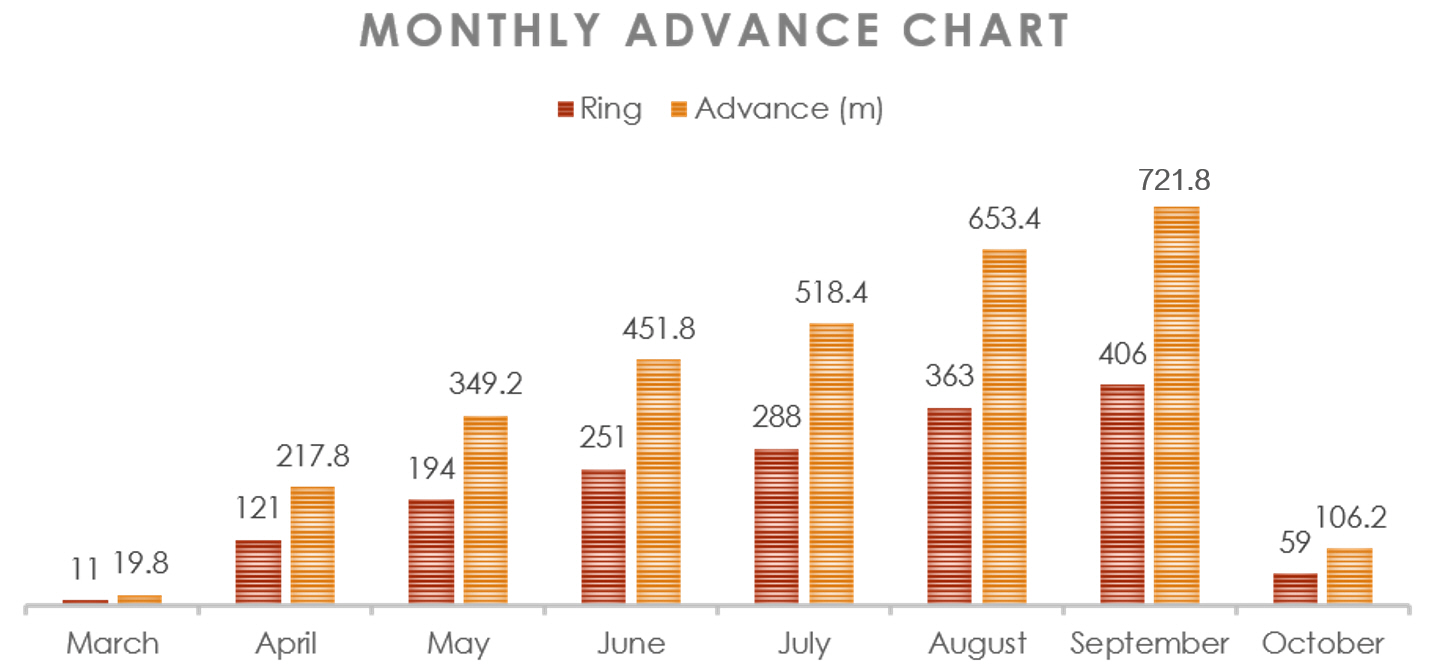
Monthly advance rate chart in meters bored and rings built.
In Conclusion
Large diameter, dual mode rock/EPB machines can and will excavate mixed ground conditions efficiently – even at world record rates. While similar projects in Turkish geology have met with challenges, the Esme-Salihli tunnel shows that with proper maintenance and a knowledgeable crew, equipment downtime can be kept to a minimum and advance rates can remain high.
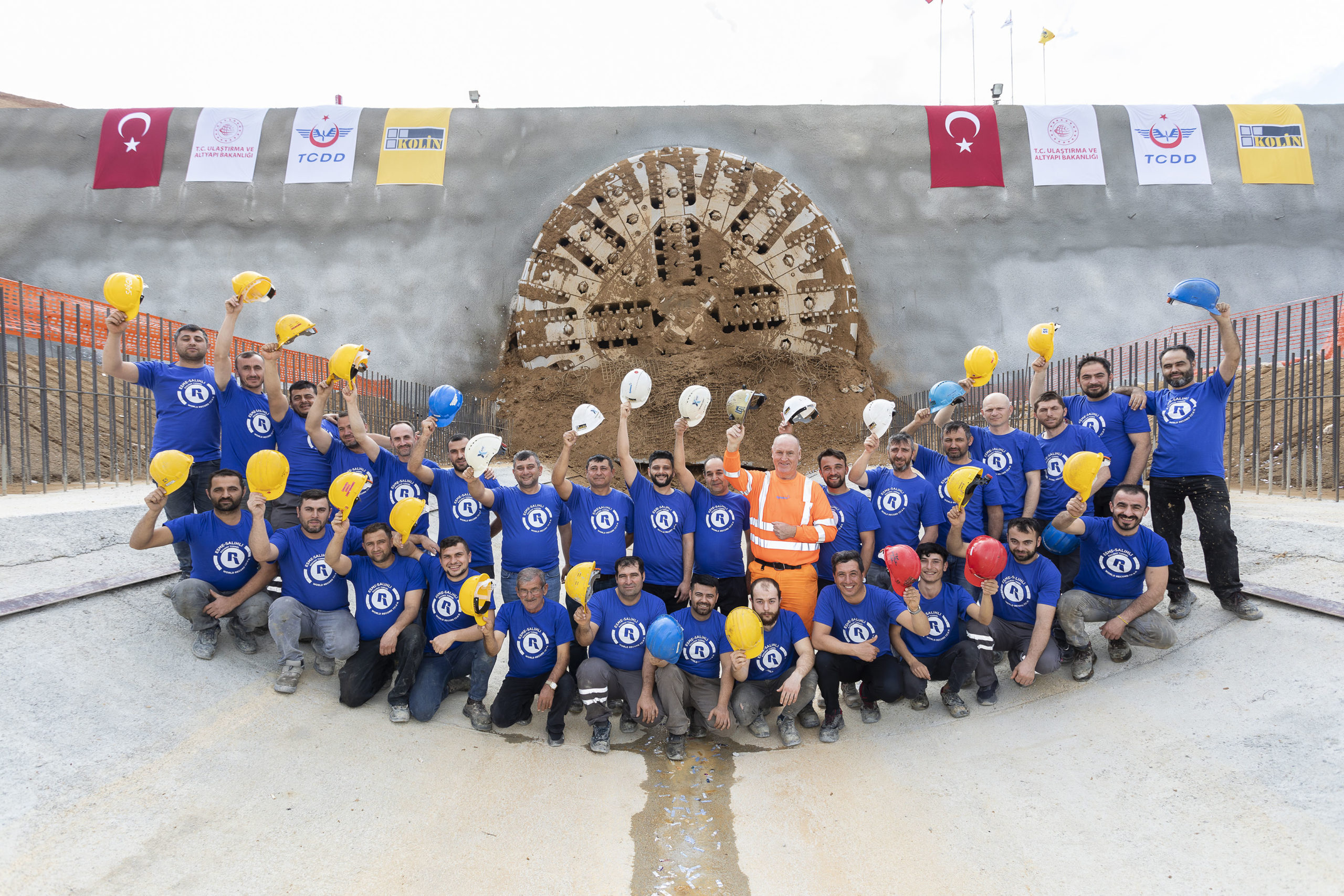
Personnel from contractor Kolin Construction and Robbins celebrate the breakthrough of a Crossover (XRE) TBM after it completed Turkey’s Esme Salihli Railway Tunnel.
Incredible India: Machines on the Move in Agra and Delhi
India’s metro network has undergone extensive growth in recent years, and is showing no signs of slowing. Multiple Robbins machines are part of tunneling work in cities across India, including Agra and Delhi.
Agra Metro: From First Site Acceptance…
On February 16, 2023 the Robbins crew and contractor SAM India celebrated the site acceptance test for the first of two 6.65 m diameter EPB TBMs at Agra Metro. The machine began boring a 1.3 km long tunnel in soft soils, for Uttar Pradesh Metro Rail Corporation Ltd.
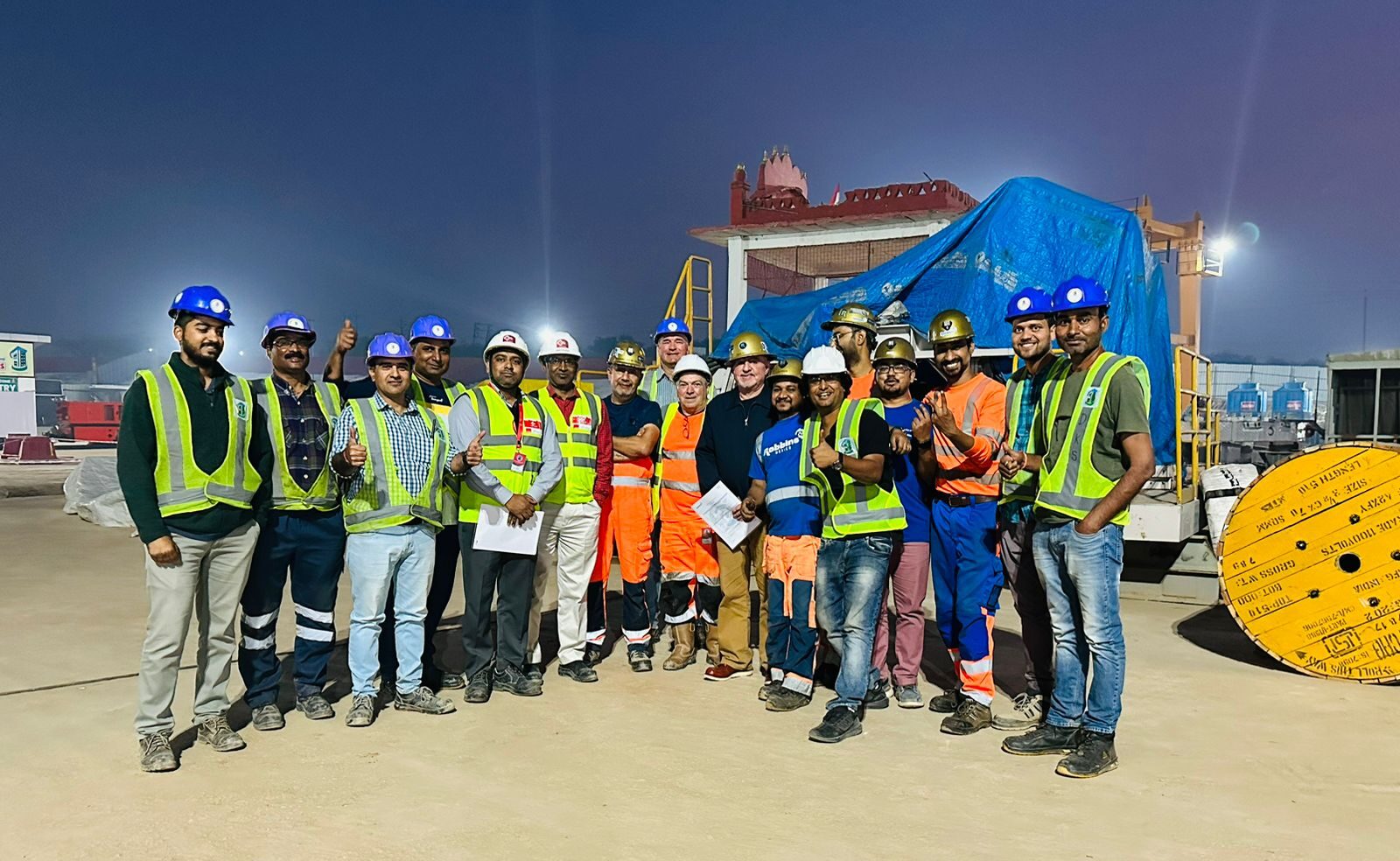
The Robbins team celebrates a successful site acceptance test for the first of two Robbins EPBs at Agra Metro.
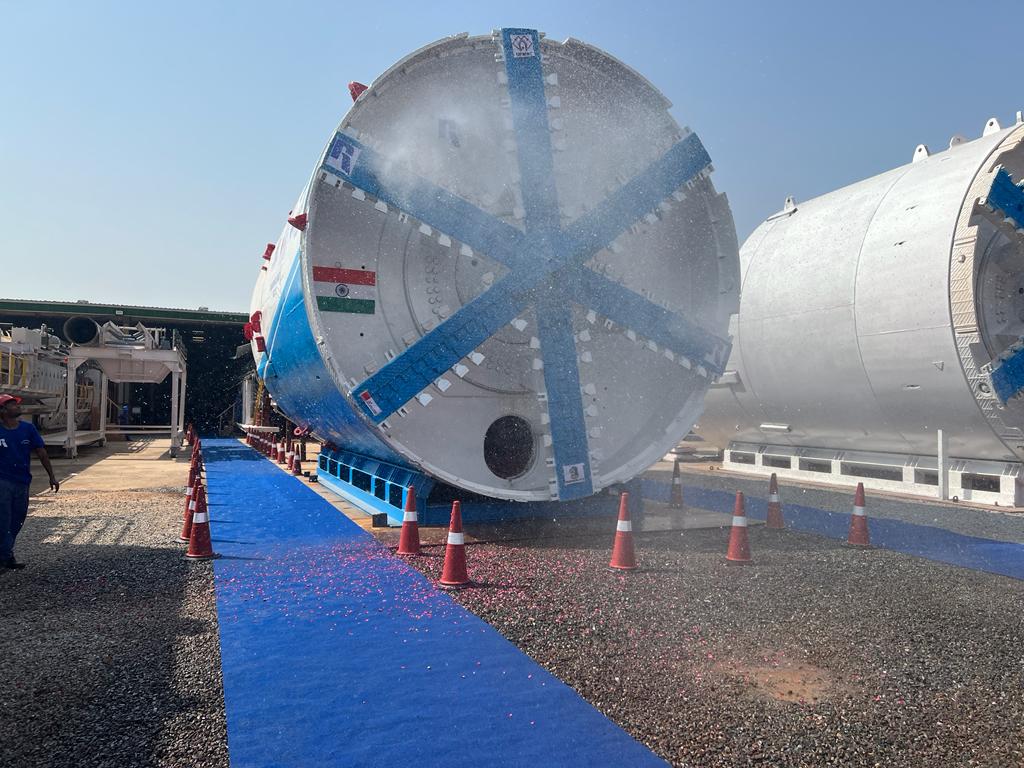
The Robbins EPBs, seen during their Factory Acceptance, are designed for soft soils.
To Second Site Acceptance…
With the first TBM well into tunneling, a second 6.65 m Robbins EPB underwent site acceptance on April 13, 2023 to bore a parallel 1.3 km long tunnel in soft soils. The crew gathered for a ceremony before sending the TBM on its way.
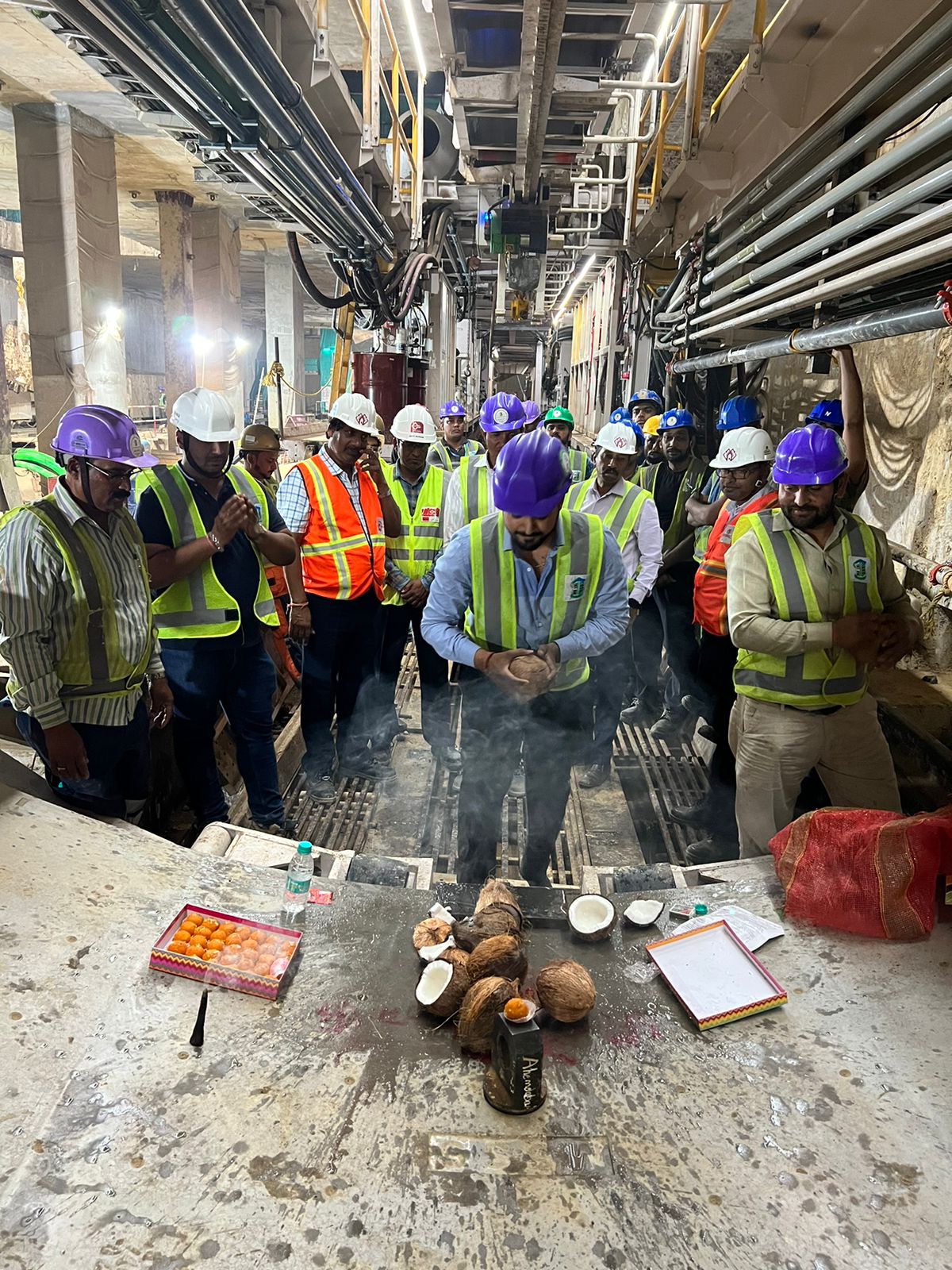
The crew gathers for the site acceptance ceremony of the second Agra metro EPB.
To First Breakthrough!
Just a few days later on April 26, 2023 the first machine made an intermediate breakthrough into a station site, completing the Jama Masjid to Agra Fort stretch of the metro. The machine bored a total of 345 m in sand and clay, and broke through to a celebration by the crew and project teams.
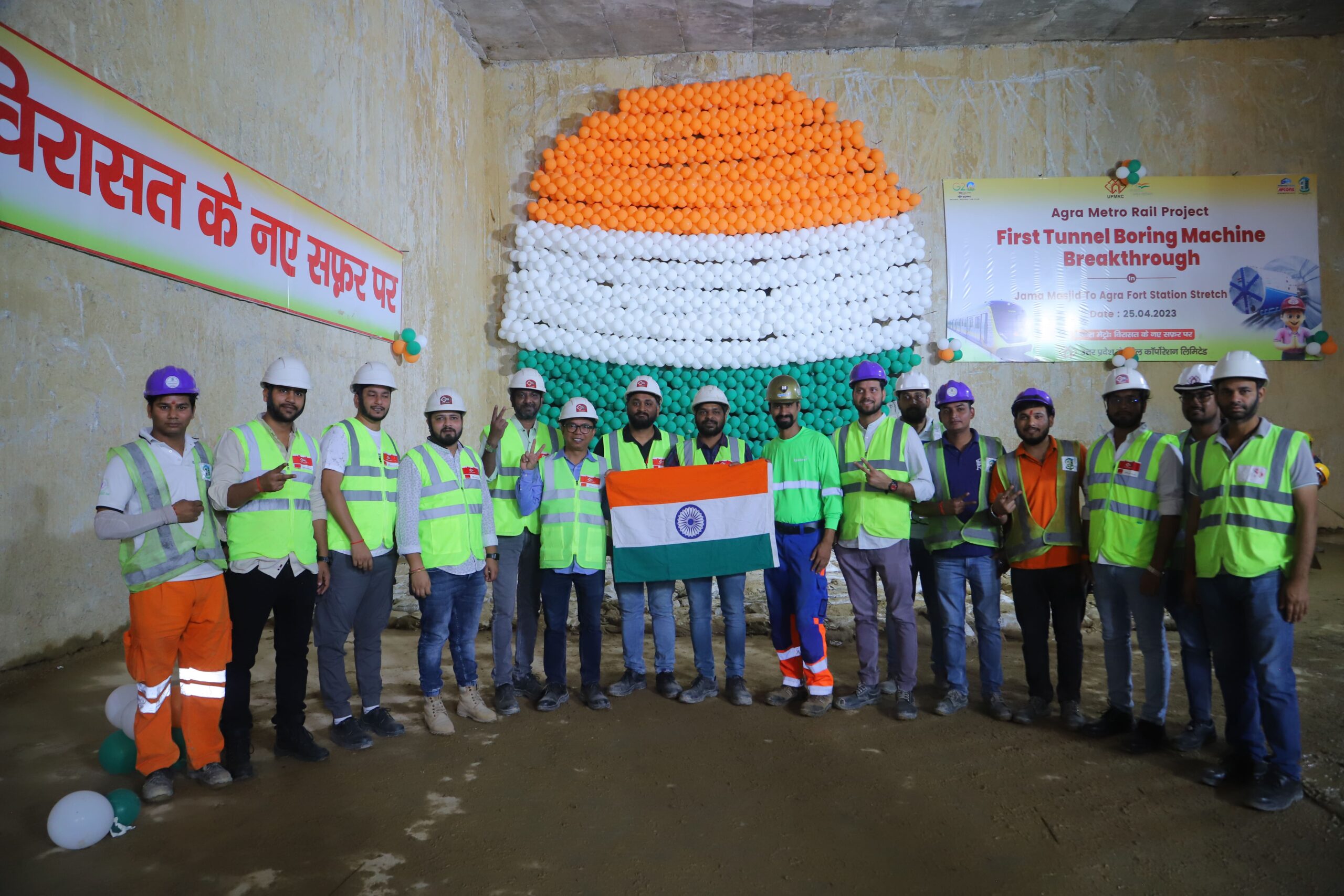
The crew anticipate the first breakthrough of the Robbins EPB at Agra Metro.
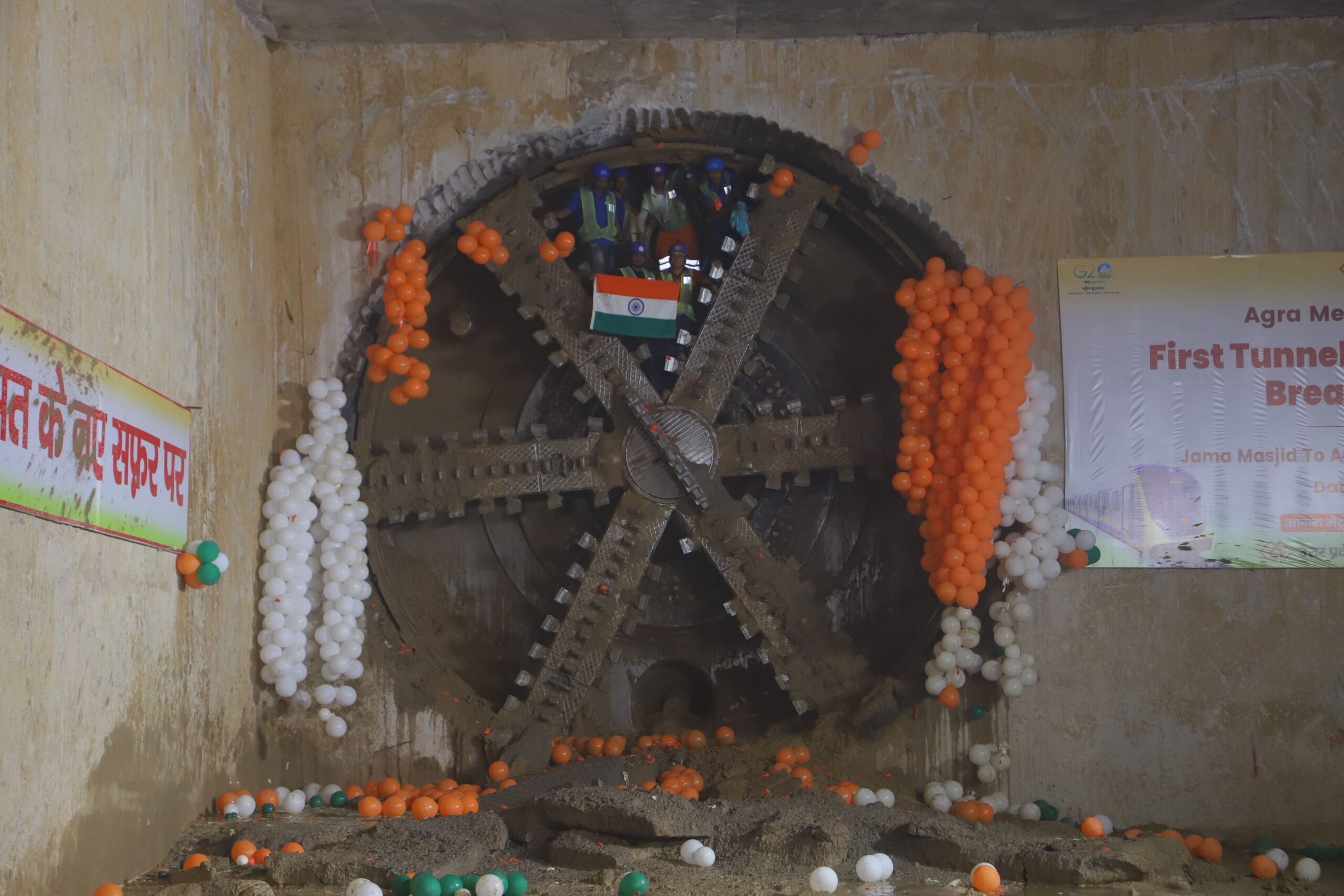
The Robbins EPB breaks through to much fanfare at Agra Metro.
New Delhi Metro: Machines Ramping Up
On February 27, 2023 the first of two 6.65 m diameter EPBs for the Delhi Metro (owner is Delhi Metro Rail Corporation) was completed in the Robbins Gurgaon, India facility. The mixed ground machine will bore a 3 km long tunnel through rock with some gravel, sand, silt and clay for contractor Afcons Infrastructure Ltd.
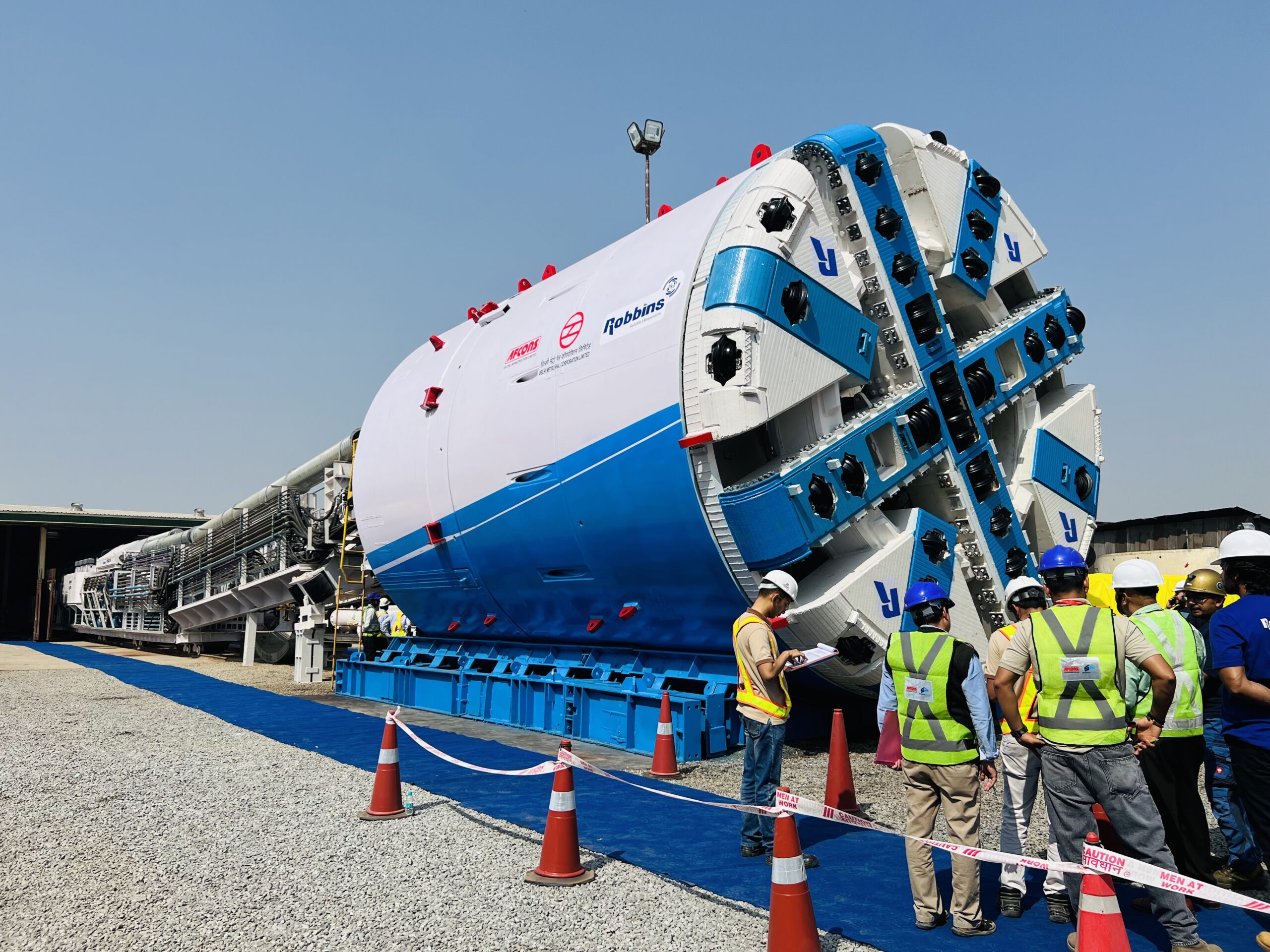
The first of two TBMs set to bore in mixed ground at Delhi Metro, during the factory acceptance in February 2023.
A second machine factory acceptance followed in April 2023. Both machines are scheduled to launch on parallel tunnels this summer.
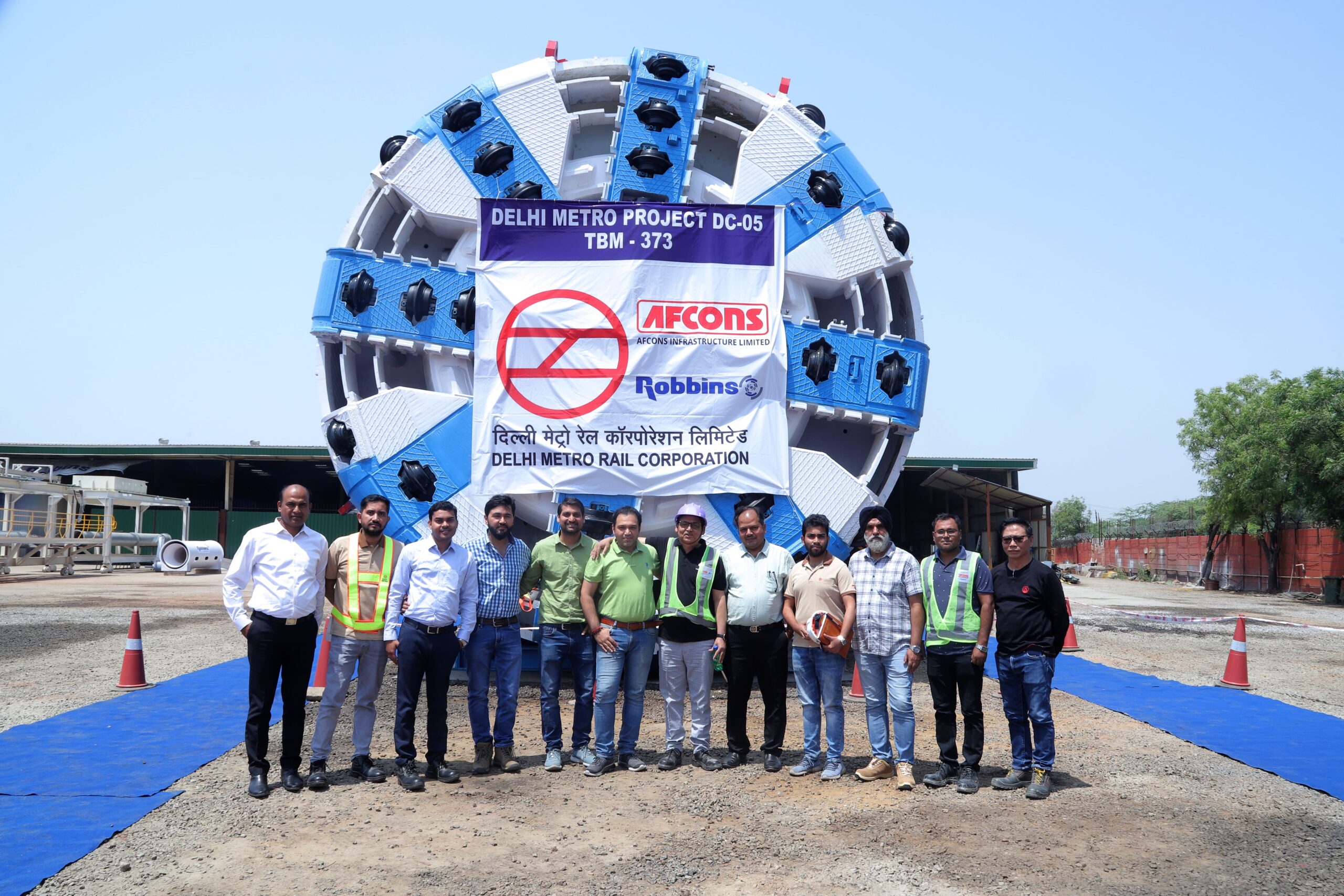
The second Delhi Metro EPB, designed to bore in mixed ground conditions.
RETC 2025
Event Name: RETC 2025
Dates: June 8-11
Location: Dallas, TX, USA
Venue: Sheraton Dallas Hotel
Booth No: 701
The Rapid Excavation and Tunneling Conference (RETC) is sponsored by the Society for Mining, Metallurgy & Exploration (SME). The show focuses on developments, technology, trends, and innovations that directly affect the tunneling and underground construction industry through a wide variety of technical presentations. Stop by the Robbins booth #701 to meet with our expert staff and find out the latest about our products and projects. Be sure to check out our technical presentation as well:
Monday June 9
Hard Rock TBMs Session
2:30 – 2:50 PM
The Resurgence of Pumped Power Storage & Small Hydropower: How TBMs and Shaft Boring Machines Can Increase Feasibility
Presented by Brad Grothen, Robbins VP Engineering