Author: Desiree Willis
World Tunnel Congress 2024
Event Name: ITA-AITES World Tunnel Congress
Dates: April 19-25, 2024
Location: Shenzhen, China
Venue: Shenzhen World Exhibition & Convention Center
Stand: F04
Come join us April 19-25 in Shenzhen, China for the ITA-AITES World Tunnel Congress, the premiere event for tunneling and underground construction. More than 2,000 professionals are set to take part in the world’s top-attended tunneling conference, where hundreds of technical papers will be presented on the latest topics of interest. Stop by our stand F04 to converse with our expert international team, and find out the latest about our products, projects, and talks at the conference.
Technical Presentation:
Monday April 22
Tech Session 7.1: Guidelines, Reviews & Prospects of Mechanized Tunneling
2:20 – 2:40 PM
CC207, Hall 18
Evaluating TBM Design and Performance, 30 Years Apart: The Lesotho Highlands Water Tunnel, Phase 1 and Phase 2
Presented by Brad Grothen VP Engineering
Most Momentous: 2021 Global Project Updates
From China’s largest Crossover TBM launch to an epic 13.77 m diameter XRE that began boring recently in Esme, Turkey, we’ve compiled the year’s most momentous events thus far. Read on to find out about Robbins machines embarking on tunnels large and larger.
Twin Crossover TBMs for Chongqing
Two 6.91 m (22.6 ft) diameter XRE machines are currently boring sections of the Chongqing Metro Phase 2 in ground conditions ranging from weathered mixed granite to weathered pegmatite and adamellite. The twin machines are the first of their kind in China, and are part of a trend towards more geologically challenging tunnels in China. To date, the machines have achieved up to 365 m (1,197 ft) advance in one month, with rates expected to ramp up as the machines progress.
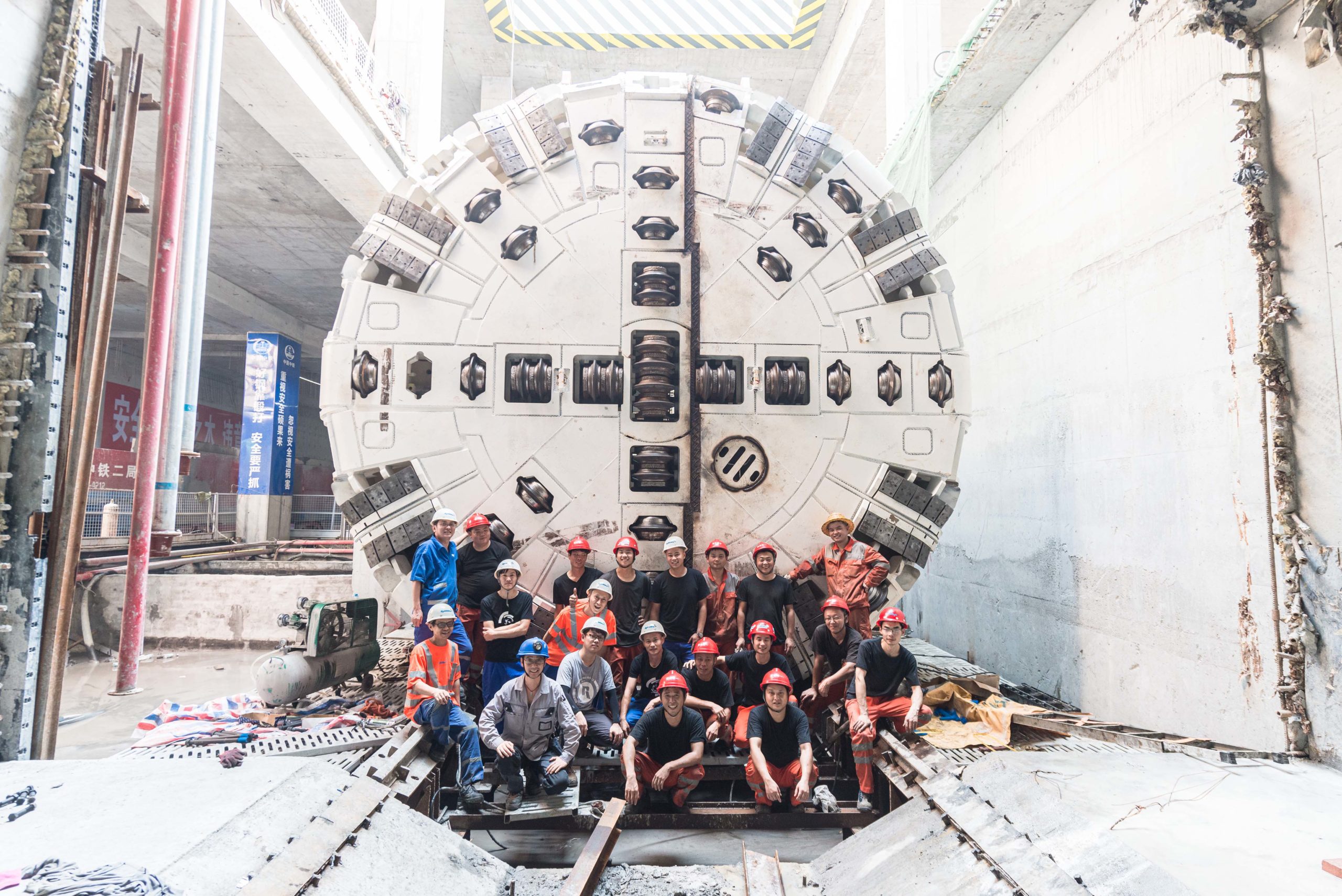
The team takes a moment to mark the assembly of one of two Robbins Crossover machines in Chongqing, China.
An Epic XRE Launch in Esme
In Esme, Turkey, a massive 13.77 m (45.2 ft) diameter Crossover XRE TBM began its bore for contractor Kolin Construction. Launched in late March 2021, the unique TBM is designed to tackle mixed ground conditions including sandstone, gravelstone, claystone and siltstone along the 3.05 km (1.9 mi) Esme-Salihli Railway Tunnel. The XRE can swiftly convert between hard rock mode using a belt conveyor and EPB mode using a screw conveyor, as both remain in place inside the machine.
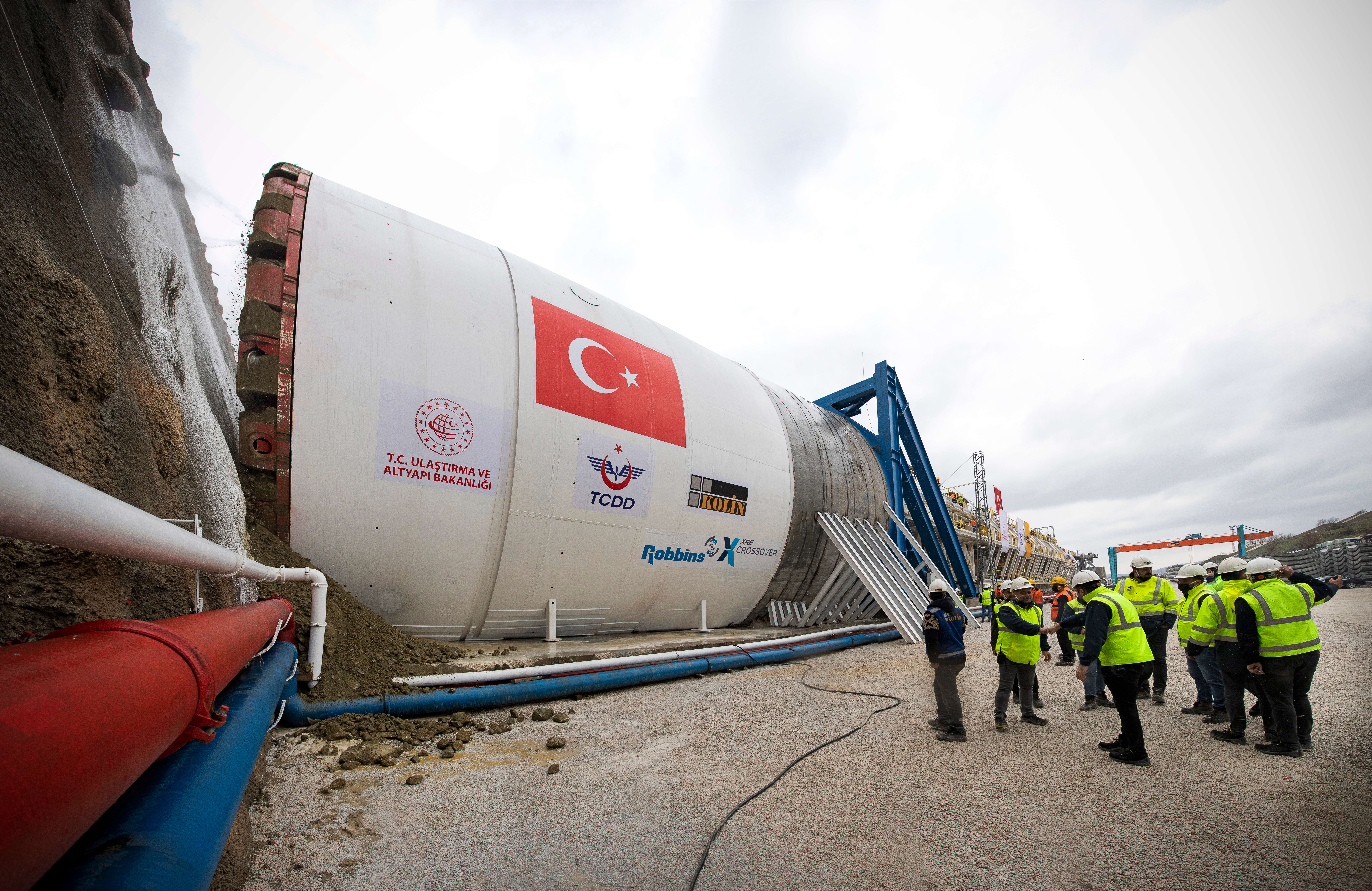
Launch of the 13.77 m diameter Robbins XRE TBM for Turkey’s Esme-Salihli Rail Tunnel.
Tunneling below Lake Ontario
A Robbins 7.95 m (26.1 ft) diameter Single Shield TBM launched recently on March 26th from an 85 m (280 ft) deep, 14 m (46 ft) diameter shaft. The machine, for the Ashbridges Bay Outfall with contractor Southland Holdings LLC in Toronto, ON, Canada has the task of boring a 3.5 km (2.2 mi) long tunnel below Lake Ontario. The completed tunnel will connect up to 50 in-lake risers to enable efficient dispersion of treated effluent over a wide area of the lake.
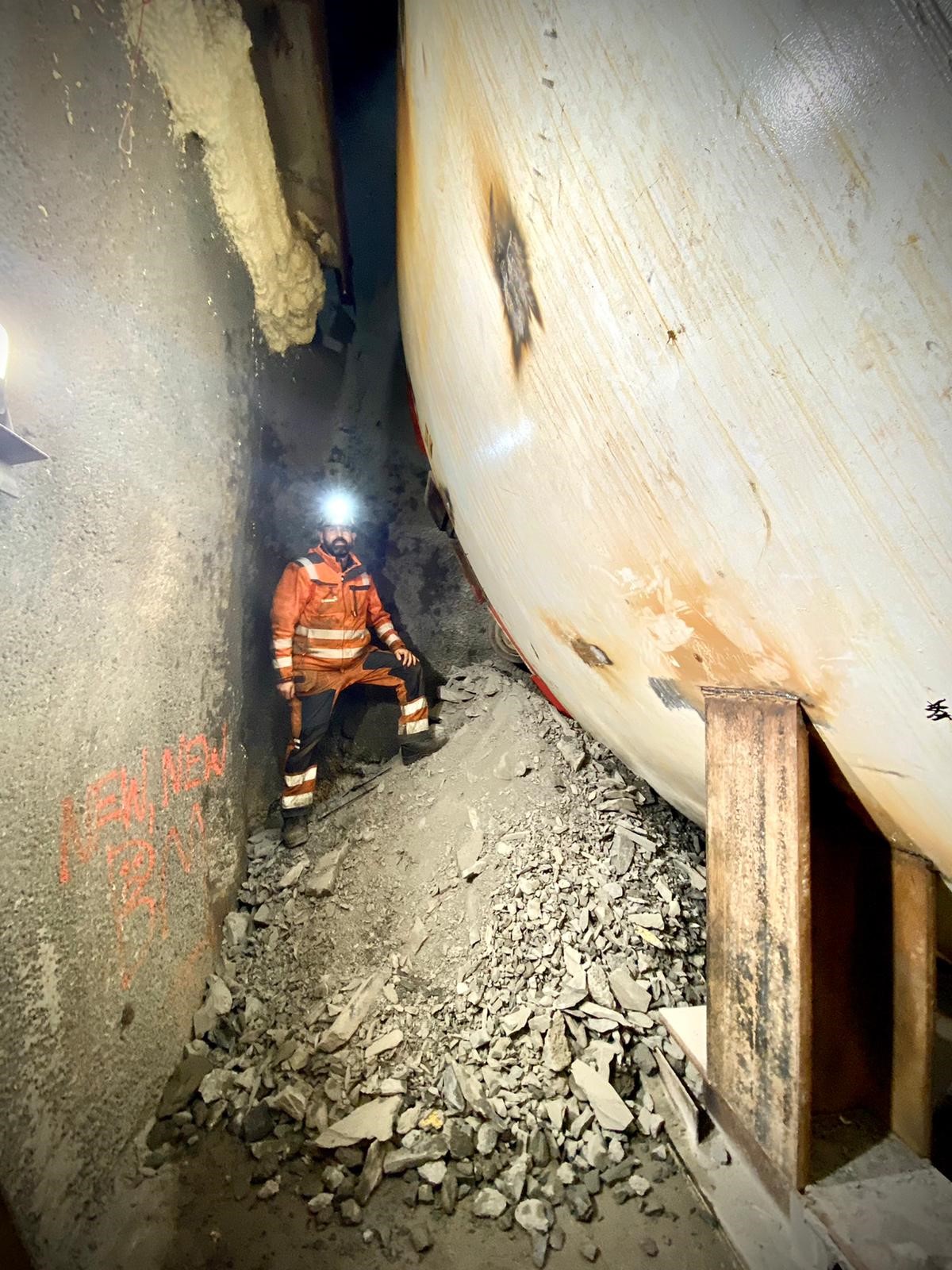
The Robbins Single Shield TBM for the Ashbridges Bay Outfall Tunnel launched on March 26, 2021. Photo: Alfredo Garrido
China’s Largest Crossover TBM
The largest ever Crossover (XRE) TBM in China launched in late March 2021 in Guangzhou for contractors Sichuan Jinshi Heavy Equipment Leasing Co., Ltd and CREC Bureau 2. Onsite First Time Assembly (OFTA) was utilized to build the 9.16 m (30 ft) diameter Robbins TBM, taking just four months from contract signing to machine launch. The hybrid machine is boring the 2.5 km (1.6 mi) long Pazhou Line Lot PZH-1 of the Pearl River Delta Intercity Railway Project, which will offer better commutes for Guangzhou residents traveling to and from University City.
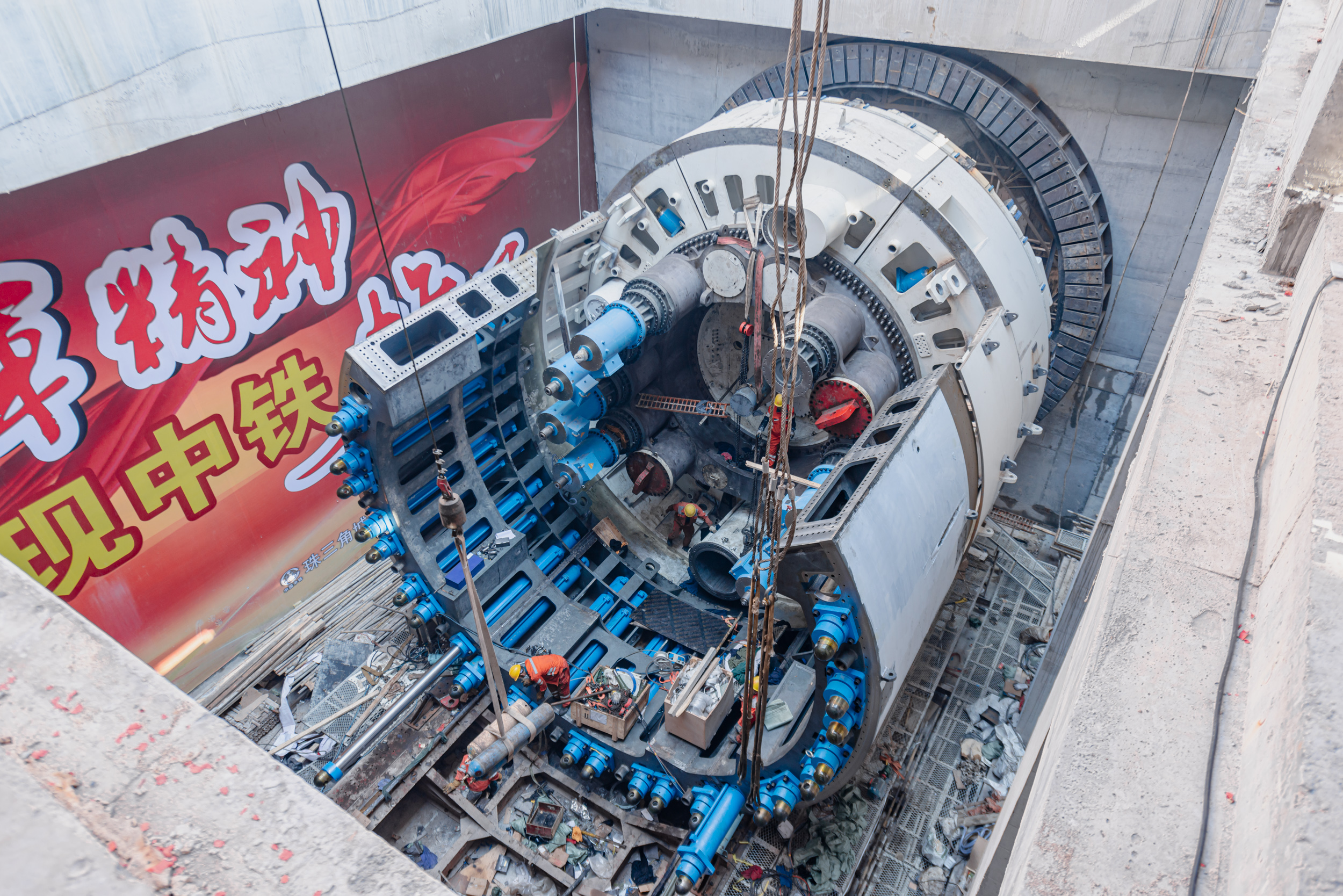
The Robbins Crossover XRE TBM at the Pearl River Delta site was assembled using Onsite First Time Assembly in just four months from contract signing.
The Next Push: Robbins TBMs on the Move Around the Globe
Robbins machines continue to advance in 2020, with essential projects ongoing and starting up the world over. From a proven Main Beam starting its fifth tunnel in Switzerland to a triumphant small diameter breakthrough in Norway to continued Crossover success in India, we’ve got all the tunneling highlights below.
ASSEMBLY UNDERWAY IN TORONTO
Assembly is underway on a Single Shield TBM for the Ashbridges Bay Treatment Outfall in Toronto, ON, Canada. The 7.95 m (26.0 ft) diameter machine and Robbins continuous conveyor will bore a tunnel to replace a 70 yr old existing outfall. The video below shows the machine acceptance in Mexico before being shipped to Canada. Due to coronavirus protocol, this was the first all-remote machine acceptance that Robbins has conducted.
SMALL DIAMETER TRIUMPH IN NORWAY
On June 16, 2020, crews wrapped up tunneling at the Salvasskardelva Hydroelectric Power Project (HEPP), located far above the Arctic Circle at 68.7 degrees north latitude near Bardufoss, Norway. The site may well be the world’s northernmost TBM-driven tunnel. The 2.8 m (9.2 ft) diameter specialized Main Beam TBM known as “Snøhvit”, or “Snow White”, was provided to contractor Norsk Grønnkraft for use on several of their hydroelectric tunnels. A continuous conveyor was also provided. The small hydro tunnels featured moderate to steep positive gradients up to 25 percent. The TBM was able to achieve rates of up to 44 m (144 ft) in 24 hours.

A small diameter Robbins Main Beam TBM broke through in June 2020 in Northern Norway.
PROVEN MACHINE RAMPS UP FOR 5TH BORE
In Oberwalden, Switzerland a 6.50 m (21.3 ft) diameter Robbins Main Beam TBM, originally built in 1993, is ramping up to begin boring in December 2020. The machine, rebuilt by Swiss contractor Marti, will bore the 6.4 km (4.0 mi) long Sarnen Stormwater Relief Tunnel through hard rock. As the bore proceeds, wire mesh, shotcrete, and invert segments will be installed.
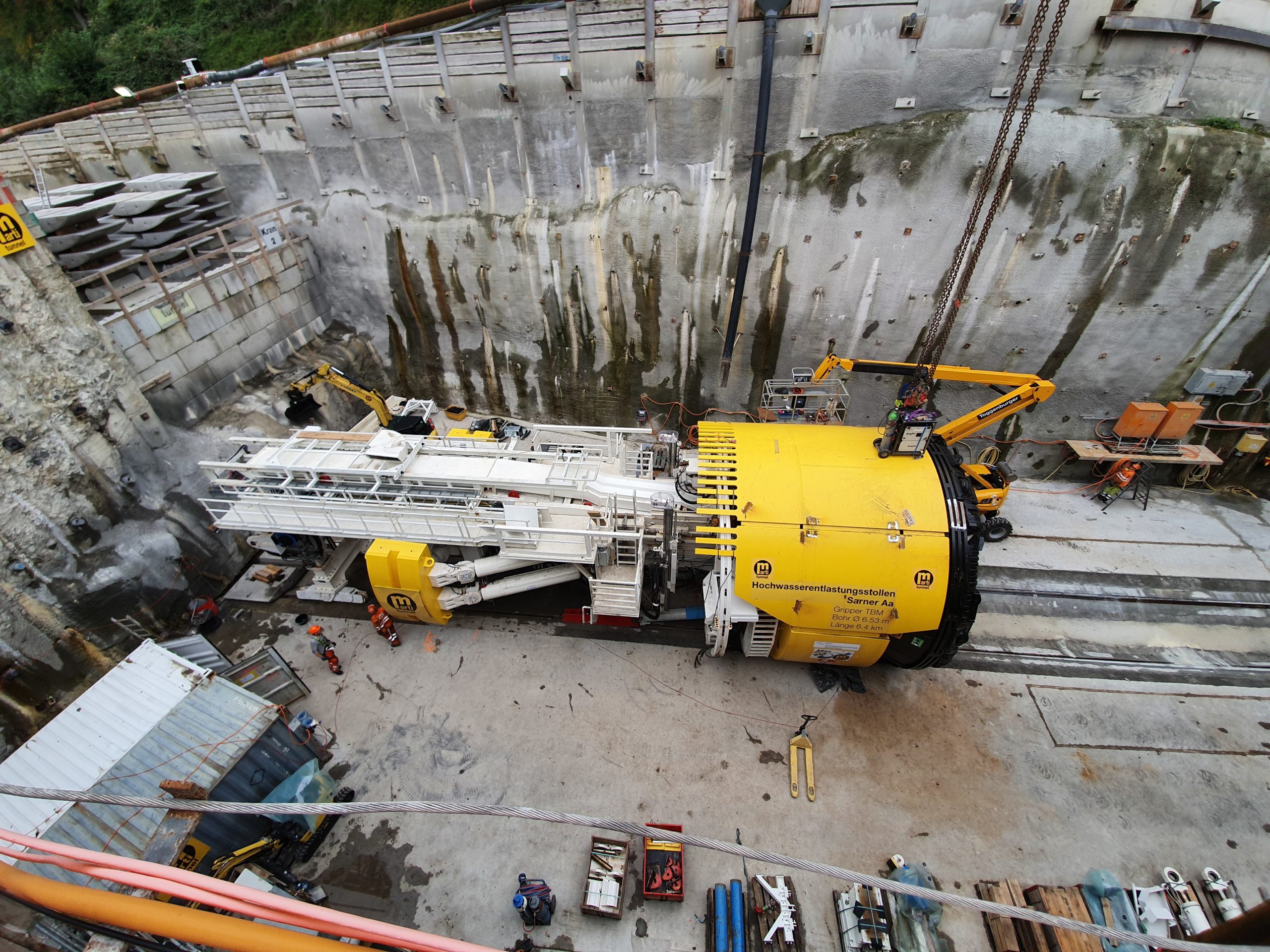
The 6.50 m Robbins Main Beam TBM will begin boring in December 2020 in Oberwalden, Switzerland.
UNIQUE CONVEYOR SYSTEM FOR NEUTRINO FACILITY
In Lead, South Dakota, a unique Robbins conveyor system is gearing up to begin hauling muck. The conveyor system will be used to build the Long Baseline Neutrino Facility (LBNF) for Fermilab. Contractor Kiewit will renovate a disused gold mine into a world-class neutrino research facility. Two caverns will be excavated by drill & blast and roadheader deep below the surface. Rock will be transported by cable hoist up a 1.5 km (0.9 mi) deep mine shaft to a rock crusher at the surface using much of the original but refurbished mining equipment, and from there will be transported via conveyors. The Robbins conveyor systems are designed for the unique application, and include the longest overland conveyor Robbins has ever provided (550 m/1,800 ft), which travels over a main road and city park and near a residential area.
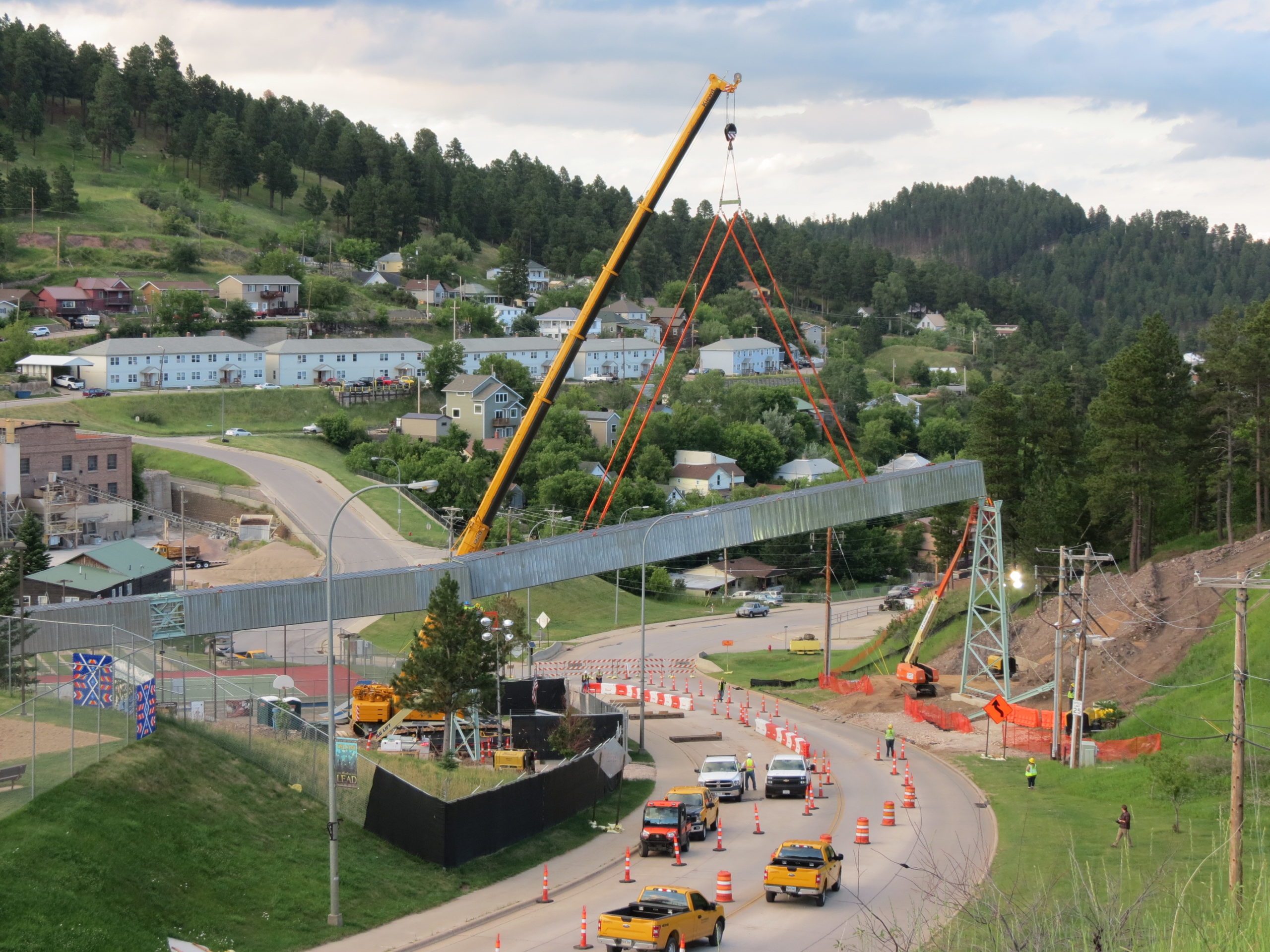
Crews install the completely enclosed box truss for the overland conveyor, which will traverse a roadway and other features.
CROSSOVERS CONTINUE BELOW MUMBAI
Tunneling continues on the Mumbai Metro Line 3, where two 6.65 m (21.8 ft) diameter Crossover XRE TBMs are on their third drives for the L&T/STEC JV. TBM 1 has bored 2,178 m (7,146 ft) with another 765 m (2,500 ft) left to bore. TBM 2 has bored 2,352 m (7,716 ft) with another 592 m (1,942 ft) left to bore, and is scheduled to bore fourth drive later this year. Two 6.65 m (21.8 ft) Robbins Slurry TBMs are also boring for the Dogus-Soma JV with one machine starting its second drive after boring 2,181 m (7,155 ft), and the other being reading for its second drive after boring 2,100 m (6,890 ft).
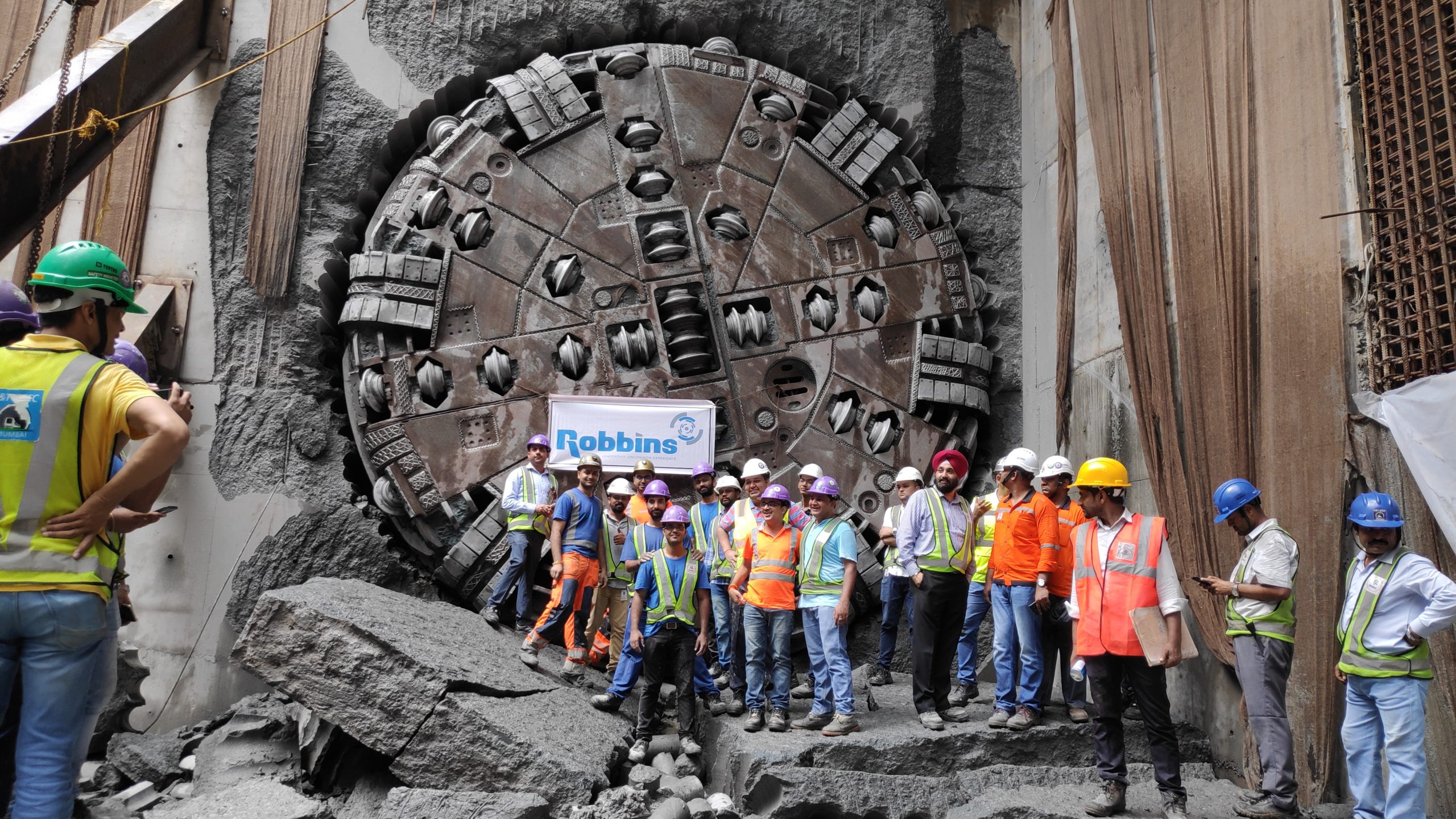
One of two 6.65 m (21.8 ft) Robbins Crossover XRE TBMs at India’s Mumbai Metro during a recent breakthrough.
On the Move: Robbins TBMs Around the World
At any given time Robbins TBMs are operating in dozens of countries around the world at all project stages. Thus far, 2020 has been no exception to the rule: From an icy visit to the world’s northernmost TBM to breakthroughs across the U.S. to a vast hydropower project on the verge of completion in China, we’ve got the latest updates from Robbins tunnels around the globe.
TBM Tunneling Above the Arctic Circle
Robbins engineers paid a visit to what is likely the northernmost TBM ever to operate in the world, at the Salvasskardelva HEPP near Bardufoss, Norway, 68.7 degrees north latitude. Robbins personnel and the contractor, Norsk Grønnkraft , have been braving frigid winter temperatures, ice and snow to excavate the 2.8 km long tunnel with a Main Beam machine at an upward gradient of 5.8 percent. As of the first quarter of 2020 they are nearly two thirds complete. Once breakthrough occurs the machine will be moved to bore a second tunnel 1.3 km long.
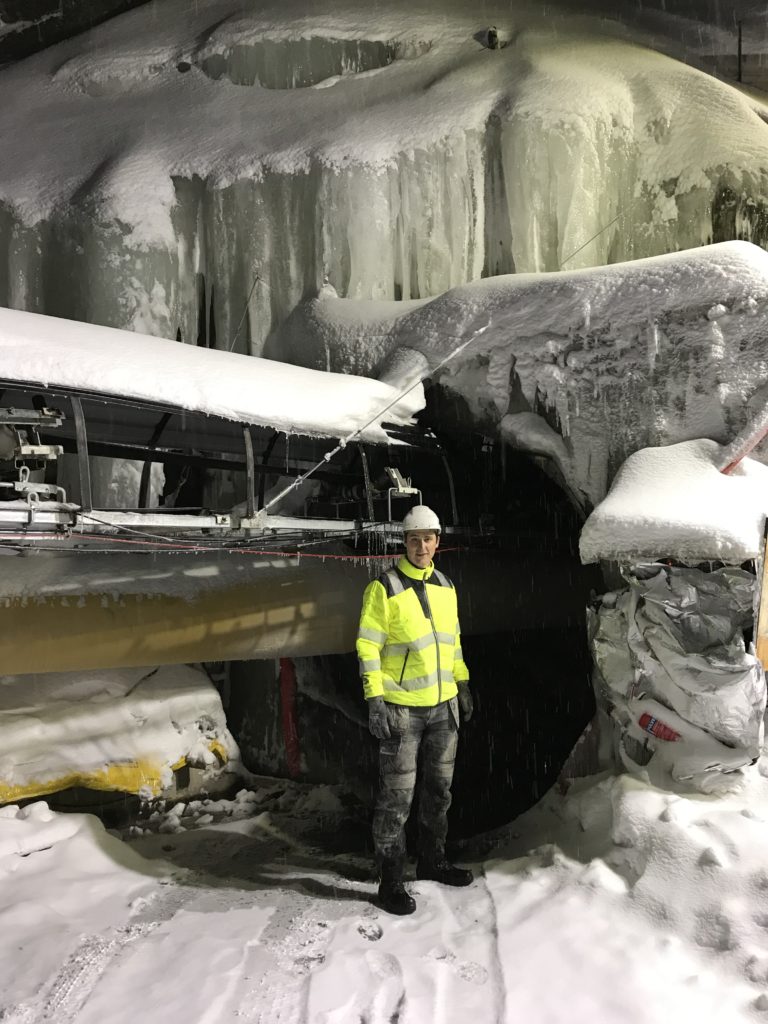
Sindre Log of Robbins Norway visits the wintry jobsite at Salvasskardelva HEPP, possibly the northernmost TBM operation ever.
A Trio of U.S. Tunneling Breakthroughs
Meanwhile in the U.S. multiple machines ranging from 2.2 to 6.5 m in diameter broke through. First up is the Deer Creek Interceptor using a 6.5 m Main Beam TBM and continuous conveyor. The machine holed through on January 29, completing a 6.3 km long tunnel below St. Louis, MO for contractor SAK. Watch this great video from the owner, MSD Project Clear, below.
Also in January, the Turkey Creek Interceptor finished up: a project using a 3.0 m diameter Robbins Double Shield TBM to bore three short drives below Kansas City, MO. Contractor Radmacher Brothers bored a total of 220 m with the machine. Check out the video of the final breakthrough, and image of its first breakthrough several months earlier.
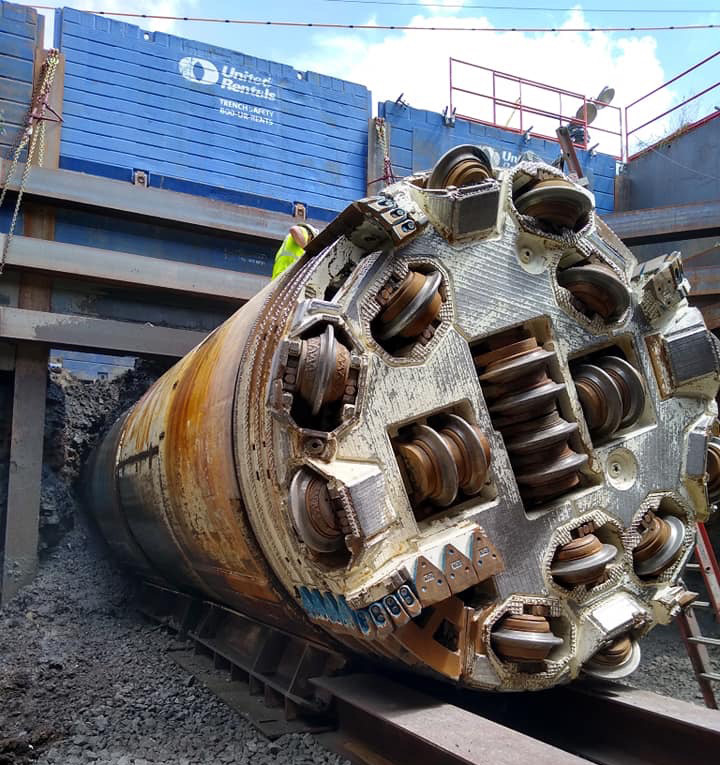
The Turkey Creek TBM, a Robbins Double Shield, during its first breakthrough in Kansas City, MO, USA.
Lastly, in San Antonio, TX a 2.2 m diameter Robbins Double Shield TBM achieved a breakthrough at the SAWS Central Water Integration Pipeline, Segment 5-1. The tunnel, for owner San Antonio Water System, was excavated by contractor Atkinson.
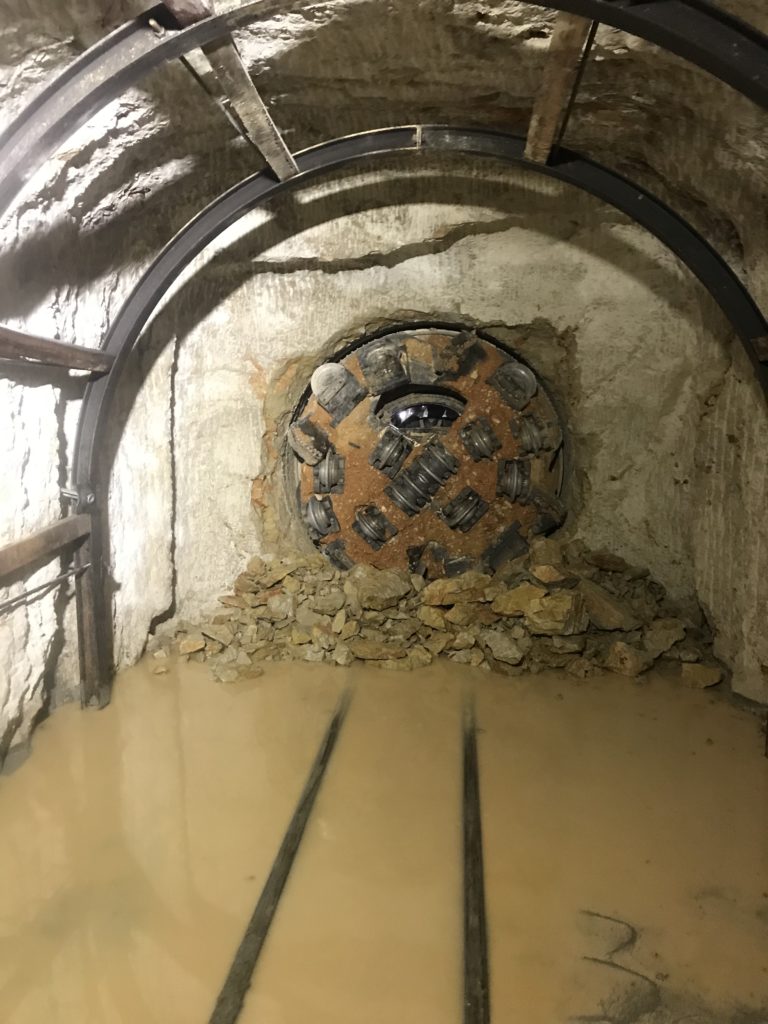
The 2.2 m Robbins Double Shield TBM for the SAWS Central Water Integration Pipeline in Texas.
A Massive Project Nears Completion in China
Two of three long-running Double Shield TBMs have completed their epic drives at China’s Great Hydro Network in Shanxi Province in recent months. The Great Hydro Network sprawls thousands of kilometers and is a feat of engineering. The Robbins machines at Tunnel 2 and Tunnel 4 bored from 15 to 23+ km in length. The machines overcame fault zones, water inflows and karst cavities to forge fast advance rates up to 865 m in one month.
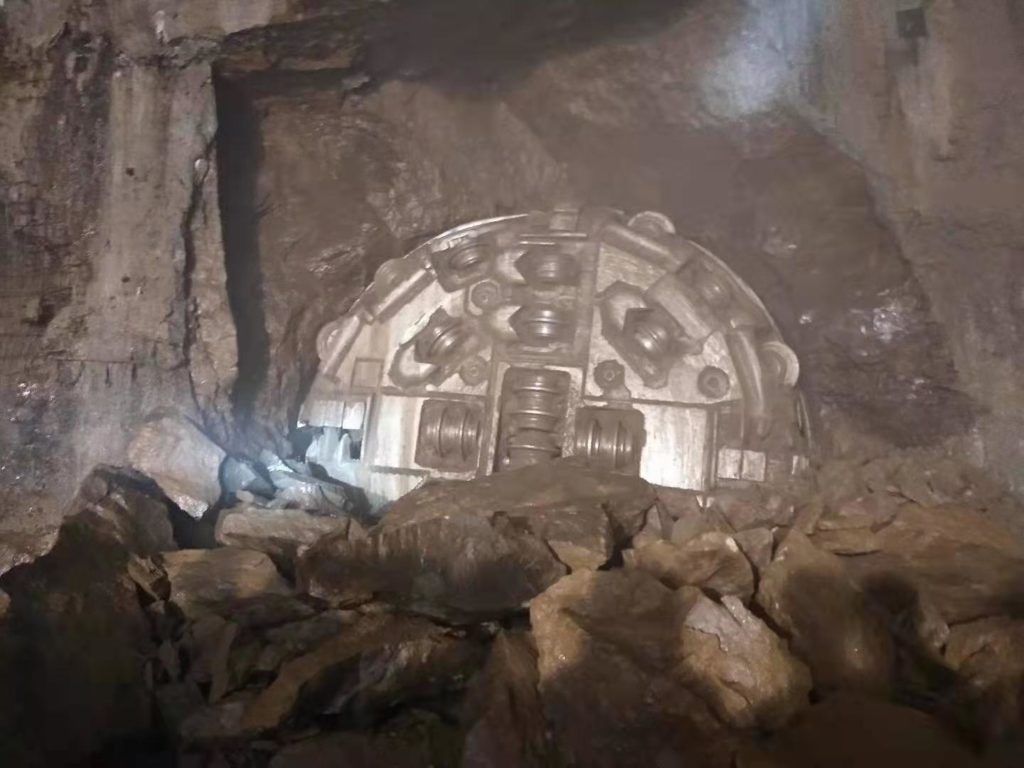
The Robbins Double Shield TBM at Tunnel 4 of the Great Hydro Network.
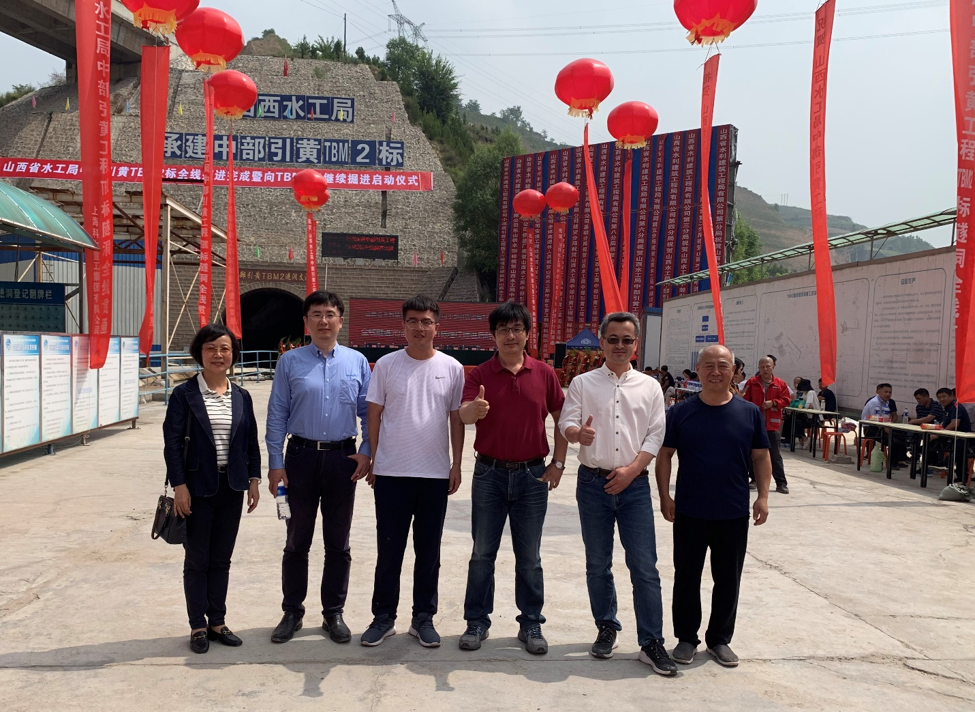
Officials celebrate the breakthrough of the Robbins Double Shield TBM at Tunnel 2 of the Great Hydro Network.
罗宾斯泥水盾构机作业孟买地铁三号线
2017年9月4日,在新加坡的两台罗宾斯泥水盾构机中的第一台,直径6.65米(21.8英尺)的翻新泥水盾构机通过了车间验收。这台机器配备了罗宾斯刀盘和外护盾,它的目标是为孟买地铁三号线(简称DSJV)服务,并将于2017年底开始开挖。第二台直径6.65米(21.8英尺)直径的新泥水盾构机也将于2017年底进行作业。
第一部机器的准时交付仅仅是跨越数年合作的开始。“在国际舞台上,很少有像罗宾斯那样专业的公司。”自该项目成立以来,罗宾斯给与一直对DSJV非常达的帮助,(罗宾斯)将成为我们的合作伙伴,直到合同结束。罗宾斯在印度,包括现场服务人员,将对我们的未来有很大的帮助。” SOMA公司副总裁DV Raju先生说道
这两台机器将在位于孟买中心站和Worli站点之间的隧道中挖掘两条平行3.5公里(2.2英里)长的隧道,经过三个中间的明挖站。地质条件由新鲜至风化的玄武岩和角砾岩组成,抗压强度最高可达100 兆帕,水压最高可达3巴。
由于具有挑战性的地面条件,JV选择了泥水盾构机。“我曾在全球类似的地质学领域工作过。泥水盾构机具有真正的力量,将适合开挖我们孟买地铁三号线的坚硬岩石地质。水的表和变化的地质,尤其是更高硬度的玄武岩,可以很容易地用泥水盾构机来处理。”DSJV的项目经理Tamay Sayin先生说道。这些机器的刀盘配备了磨损保护,磨损检测刀,以及罗宾斯17英寸的滚刀。阻拦条板将限制进入设备的大卵石的尺寸到250毫米(9.8英寸)或以下。泥浆系统包括岩石破碎机以及高磨损区域的耐磨镀层。
这两台设备是罗宾斯为孟买地铁3号线提供的四个机器中的第一批。另外两台直径6.65米(21.8英尺)直径的跨模式XRE掘进机将于2018年开挖两条长2.8公里(1.7英里)的平行隧道。罗宾斯印度公司董事总经理Kapil Bhati说:“孟买地铁是全国最著名的地铁工程之一,罗宾斯参与提供合适的机器和相关服务是一项荣誉。
孟买地铁公司(MMRC)建造的孟买地铁三号线长达33.5公里(20.8英里),由26个地铁站和1个车站组成,这将减少班德拉和该市的教堂区之间的交通拥堵和铁路拥堵现象。总共有17台掘进机被采购来负责开挖隧道的各个部分,这些隧道将被挖掘到城市地下15到25米的平均深度。整个线路预计在2021年投入使用。
A Tradition of Innovation: The 2013 Muir Wood Lecture takes a cue from Robbins’ Long History
When asked about his most memorable tunneling project, Dick Robbins narrowed it down to two: The Channel Tunnel and the Paris RER Metro. The former company president and CEO from 1958 to 1993 has seen hundreds of tunneling projects in his career, and should know. The Channel Tunnel, with its hybrid machines capable of operating under 10 bar water pressure, was challenging to say the least. But the Paris RER Metro in 1964 resulted in a radically unique machine design: “We created the world’s first below-water, pressure bulkhead shielded machine using air pressure. All future slurry and EPB designs had their genesis in this machine,” said Robbins. A sealing system using steel fingers back-supported with foam kept the gap between the machine shield and segments airtight. Wire brush seals with grease were not developed until later projects (see below).
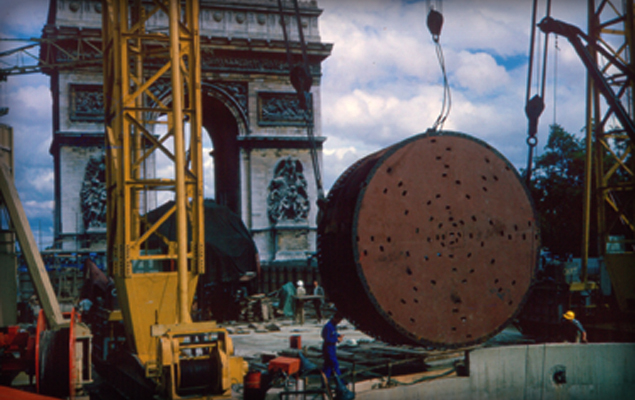
The central section of the Robbins machine at the Paris RER metro, with the Arc de Triomphe in the background.
These two projects are just a few of the highlights Dick Robbins is set to touch on during his 2013 Sir Alan Muir Wood Lecture, honoring the late tunneling statesman who initiated and served as the first president of the International Tunneling Association (ITA).
The talk, titled “A Tradition of Innovation: The Next Push for Machine Tunneling” will cover everything from the beginnings of mechanized tunneling to the era of modern tunneling when his father James S. Robbins came up with the idea of developing full-face TBMs (see picture below). Discussion will then move to modern-day marvels like the world’s largest TBM set to bore the Highway 99 Viaduct Replacement tunnel. Robbins will make the case that a culture of innovation is needed in greater force in order to push for new leaps in design that will accelerate the advancement of the industry.
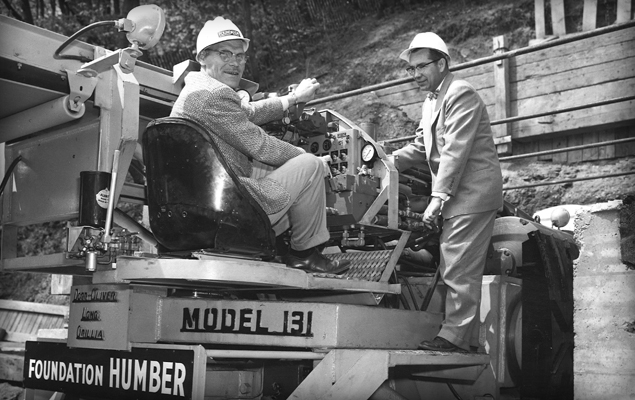
James S. Robbins (in driver’s seat), Robbins founder, at the launch of the Humber River Sewer TBM in 1956. The machine was the first ever to exclusively use rolling disc cutters.
See the Talk:
ITA-AITES World Tunnel Congress
Geneva, Switzerland
Opening Ceremony & Sir Alan Muir Wood Lecture
Monday June 3
9:00 AM to 10:30 AM
For more information on Robbins’ long history, check out the lecture Dick Robbins and colleagues made when he received the 2009 Benjamin Franklin Medal.
Salamanders, Pseudo Scorpions, and Quartz Crystals: How my Recent Site Visit proved that TBM Tunneling is the Greenest Way to Go
The Balcones Canyonlands just north of Austin, Texas, USA is a protected wildlife preserve, and it’s not open to the public. So when the city of Austin opted to build a 10.5 km (6.5 mi) long water line directly below it, there was understandably some concern—but not for humans. The inhabitants of the Canyonlands include some of the state’s most endangered species, from tiny, blind cave spiders to songbirds to the green-speckled Jollyville Plateau Salamander. And don’t forget the pseudo scorpions. The Jollyville Transmission Main, a pipeline planned to bring drinking water to the drought-ridden city, was designed deep below protected aquifers in chalk, up to 106 m (350 ft) down in limestone rock. This made tunneling the only option. But even so, how could the project avoid impacting such a sensitive environment?
When I visited the site in Autumn 2012, I got my answer. The contractor, Southland/Mole JV, is taking every precaution to mitigate impact, and they’ve been very successful thus far. An environmental consultant from the city is on the site daily, and routine inspections ensure that the minimally invasive tunnel is not encroaching on the habitat of the endangered animals.
Our guides for the visit, Kent Vest and John Arciszewski of Southland Contracting, took us to the 82 m (270 ft) deep Four Points Shaft first, which has been partially reinforced with liner plates. Kent and John explained that during excavation, water inflow from the aquifer had been high enough that the city opted to grout behind the liner plates to prevent further dewatering. Gravel in the annular space between the liner plates and shaft walls would keep any groundwater pathways intact.
As we descended into the unlined tunnel where a 3.25 m (10.7 ft) Robbins Main Beam TBM was averaging 55 m (180 ft) per day, we talked ground support—or the lack thereof. Three TBMs are being used to excavate portions of the tunnel in competent limestone. Southland is not permitted to do either pre-excavation drilling or grouting because of the possibility of karst cavities and groundwater pathways—areas where endangered aquatic species might live. While they plan to install wire mesh and rock bolts if it’s needed, the rock quality has so far been very good with little ground water. We took a few photos while in this tunnel (see below), and then moved on to the next site.
Our last site visit of the day was the deepest—the 106 m (350 ft) Jollyville shaft next to the similarly named Jollyville Reservoir in a much more urban location. Once we’d been lowered down the shaft, we found a small, unlined tunnel in competent limestone. A 3.0 m (9.8 ft), contractor-owned Double Shield TBM was tunneling this reach, after having been refurbished by Robbins in Solon, Ohio. Similarly, the machine was getting some fast advance rates of 46 m (150 ft) per day on average.
What I immediately noticed in this tunnel was the multitude of small, mostly dry karst cavities down the tunnel walls. These cavities could potentially be home to the blind cave spiders, though none had been found during tunneling and it was likely they wouldn’t live in such small voids. We noticed, during our ride on the muck train towards the machine, sparks of light emitting from these cavities. Once we stopped John reached into a cavity and pulled out a handful of quartz crystals. “These are all over, in all these cavities. You can take some with you,” he said. As I am part-pirate (my genealogy traces back to Sir Francis Drake on my mother’s side!), I decided to stuff my pockets with the sparkly crystals (i.e., treasure!). I had never seen anything like this before, but John explained that the minerals in the perched water in many of the pockets caused the crystals to grow. Since the pockets were small, they weren’t filled in or isolated and we could pluck quartz crystals to our heart’s content.
On a more serious note, Southland does have a plan of action if large cavities are found or if a groundwater pathway is very open and linked to the aquifer. In this case, large voids would be isolated and sealed off to protect the habitat within. If ground water inflows are severe they will install steel liner plates and grout behind them to stop the flow. But, says Southland, they don’t expect to encounter either of these since the tunnels are so far below the aquifer. In fact, one reach of the tunnel, already complete at the time of our visit, had encountered almost no groundwater in 1,300 m (4,400 ft) of tunneling.
Once back on the surface, it became clear to me that this well-designed project proved that tunneling, particularly TBM tunneling, could be used safely in even the most sensitive environments. The foresight, planning, and execution by the designers and contractors was impressive. The salamanders and pseudo scorpions thank you.
There are Urgent Projects…and Then There’s Emisor Oriente
After visiting Mexico City’s Emisor Oriente Wastewater Tunnel, I realized something: there are urgent projects, and then there are URGENT PROJECTS. Túnel Emisor Oriente, often abbreviated to TEO by those involved, is the latter. We visited the site in 2011 to see the assembly of an EPB and learn about why the project is so important.
Day 1
On a good day with light traffic, the jobsite is about an hour’s drive away from the Distrito Federal, the downtown zone of Mexico’s capital city. Our first day, I noticed how the high rise buildings and restaurants slowly dissolved into ramshackle huts as we drove further from the city to an area known as Ecatepec. Approaching the site, we crossed a bridge in our SUV that spanned an extremely slow moving grayish brown river (more about this soon).
It was a warm day in June, Mexico’s rainy season, which is quite different from the rain in my home town of Seattle in the U.S. Each day during the rainy season, the morning dawns sunny and warm–but by 4:00 in the afternoon a torrential downpour begins. The water floods city streets throughout Mexico City, whose storm drains can’t handle the sudden inundation. Sometimes the rain only lasts a few minutes, and sometimes it goes for longer. The water eventually runs into rivers like the one we crossed by the jobsite, creating flooding risks.
We exited our SUV at the Lot 1 shaft and were greeted by several Robbins Field Service guys, including our Field Service Manager for the Americas, Jeremy Pinkham. I was excited to learn more about the TEO project, where we have three EPB machines among six TBMs that are excavating an epic 62 km (39 mi) long wastewater tunnel. The tunnel will feed into the country’s largest water treatment plant, which is currently being built.
As Jeremy and the group walked towards the shaft to be lowered down the elevator, I was struck by a smell—something akin to a vast field of poorly maintained port-a-potties. I asked Jeremy about the Robbins machine, which was originally intended for Lot 5 but had been fast tracked to bore part of the tunnel section at Lot 1. I was wondering why this particular section had been deemed top priority. “Did you see that river just a few meters away from our jobsite?” he asked. “Most rivers, when you throw a stone in, it splashes or skips and then sinks. This one, you throw a stone in and it just goes ‘plop’, then sits there.” It was only then that I realized that this “river” was El Gran Canal, Mexico City’s infamous open sewer originally commissioned in 1910 by President Porfirio Díaz.
The Robbins guys as well as engineers from the Lot 1 contractor Ingenieros Civiles Asociados (ICA) then explained to me that the canal in this section, lined with shacks, was prone to flooding during each rainy season due to a loss of its slope. The effects on the people and infrastructure were severe, so the National Water Commission (CONAGUA) had fast-tracked Lot 1. A pumping station would be put in and the first section of tunnel sealed off so that wastewater from this area could be pumped into a section of the canal downstream that still maintained its negative slope. I was beginning to realize the importance and urgency of this project!
The guys gave us a tour of the TBM being assembled at the bottom of the shaft, which was specially designed for high pressure conditions under the water table.
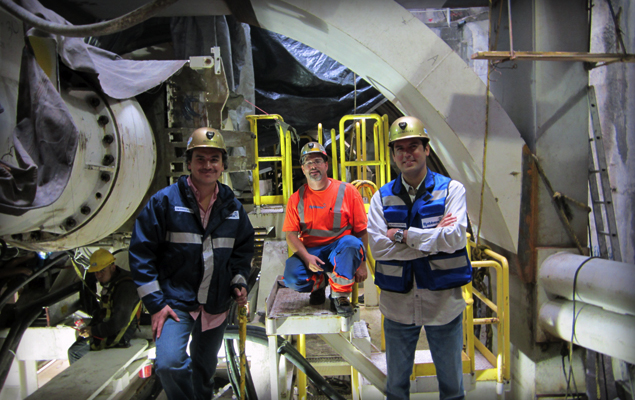
Robbins employees on the Lot 1 EPB. From left to right: Andrei Olivares, Robbins Project Engineer; Jeremy Pinkham, Field Service Manager – The Americas; Roberto Gonzalez, General Manager, Robbins Mexico
On the ride home that day we were hit by a particularly nasty rainstorm that went on for several hours. I learned via the local news later on that the very roads we had driven on to get to the jobsite were now flooded with wastewater and impassable—apparently a regular yet extremely concerning event.
Day 2
The next day we went to CONAGUA’s offices to speak with José Miguel Guevara, General Supply Coordinator for Potable Water and Sanitation. He spoke with us about the massive scope of Emisor Oriente—a project that could improve the lives of over 20 million people in the area by increasing wastewater capacity by 20% during each rainy season. The new pipeline will bolster current wastewater lines (both El Gran Canal and Emisor Central—a pipeline built in 1964) that have lost their slope due to Mexico City’s sinking lake clays.
While Guevara was optimistic, he admitted that health problems caused by El Gran Canal were numerous for the people living on its banks. When asked about future plans, he expressed grave concern that funds were not currently sufficient for a covered option to the open waterway. “At this moment,” said Guevara, “The Valley of Mexico is vulnerable. Our new treatment plant will treat 60% of the area’s water, but we need more alternatives as well. We are working on pieces to the problem, but the problem is not solved yet.”
With Emisor Oriente scheduled to be complete in 2014, I am hopeful that at least some of those problems will be alleviated. This is a great example of the magnitude that civil engineering works have on societies. I for one am proud that Robbins has a part in this monumental solution to an age old problem.After visiting Mexico City’s Emisor Oriente Wastewater Tunnel, I realized something: there are urgent projects, and then there are URGENT PROJECTS. Túnel Emisor Oriente, often abbreviated to TEO by those involved, is the latter.
Day 1
On a good day with light traffic, the jobsite is about an hour’s drive away from the Distrito Federal, the downtown zone of Mexico’s capital city. Our first day, I noticed how the high rise buildings and restaurants slowly dissolved into ramshackle huts as we drove further from the city to an area known as Ecatepec. Approaching the site, we crossed a bridge in our SUV that spanned an extremely slow moving grayish brown river (more about this soon).
It was a warm day in June, Mexico’s rainy season, which is quite different from the rain in my home town of Seattle in the U.S. Each day during the rainy season, the morning dawns sunny and warm–but by 4:00 in the afternoon a torrential downpour begins. The water floods city streets throughout Mexico City, whose storm drains can’t handle the sudden inundation. Sometimes the rain only lasts a few minutes, and sometimes it goes for longer. The water eventually runs into rivers like the one we crossed by the jobsite, creating flooding risks.
We exited our SUV at the Lot 1 shaft and were greeted by several Robbins Field Service guys, including our Field Service Manager for the Americas, Jeremy Pinkham. I was excited to learn more about the TEO project, where we have three EPB machines among six TBMs that are excavating an epic 62 km (39 mi) long wastewater tunnel. The tunnel will feed into the country’s largest water treatment plant, which is currently being built.
As Jeremy and the group walked towards the shaft to be lowered down the elevator, I was struck by a smell—something akin to a vast field of poorly maintained port-a-potties. I asked Jeremy about the Robbins machine, which was originally intended for Lot 5 but had been fast tracked to bore part of the tunnel section at Lot 1. I was wondering why this particular section had been deemed top priority. “Did you see that river just a few meters away from our jobsite?” he asked. “Most rivers, when you throw a stone in, it splashes or skips and then sinks. This one, you throw a stone in and it just goes ‘plop’, then sits there.” It was only then that I realized that this “river” was El Gran Canal, Mexico City’s infamous open sewer originally commissioned in 1910 by President Porfirio Díaz.
The Robbins guys as well as engineers from the Lot 1 contractor Ingenieros Civiles Asociados (ICA) then explained to me that the canal in this section, lined with shacks, was prone to flooding during each rainy season due to a loss of its slope. The effects on the people and infrastructure were severe, so the National Water Commission (CONAGUA) had fast-tracked Lot 1. A pumping station would be put in and the first section of tunnel sealed off so that wastewater from this area could be pumped into a section of the canal downstream that still maintained its negative slope. I was beginning to realize the importance and urgency of this project!
The guys gave us a tour of the TBM being assembled at the bottom of the shaft, which was specially designed for high pressure conditions under the water table.
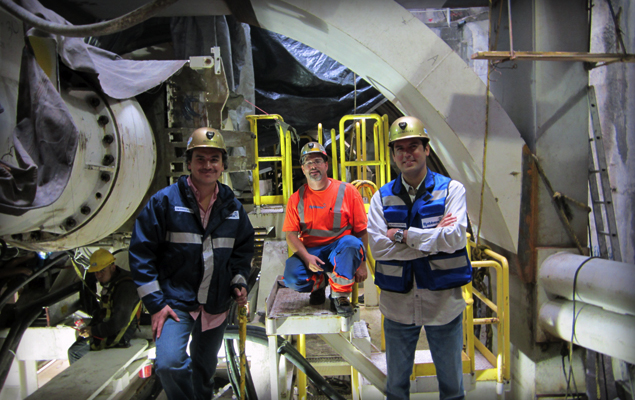
Robbins employees on the Lot 1 EPB. From left to right: Andrei Olivares, Robbins Project Engineer; Jeremy Pinkham, Field Service Manager – The Americas; Roberto Gonzalez, General Manager, Robbins Mexico
On the ride home that day we were hit by a particularly nasty rainstorm that went on for several hours. I learned via the local news later on that the very roads we had driven on to get to the jobsite were now flooded with wastewater and impassable—apparently a regular yet extremely concerning event.
Day 2
The next day we went to CONAGUA’s offices to speak with José Miguel Guevara, General Supply Coordinator for Potable Water and Sanitation. He spoke with us about the massive scope of Emisor Oriente—a project that could improve the lives of over 20 million people in the area by increasing wastewater capacity by 20% during each rainy season. The new pipeline will bolster current wastewater lines (both El Gran Canal and Emisor Central—a pipeline built in 1964) that have lost their slope due to Mexico City’s sinking lake clays.
While Guevara was optimistic, he admitted that health problems caused by El Gran Canal were numerous for the people living on its banks. When asked about future plans, he expressed grave concern that funds were not currently sufficient for a covered option to the open waterway. “At this moment,” said Guevara, “The Valley of Mexico is vulnerable. Our new treatment plant will treat 60% of the area’s water, but we need more alternatives as well. We are working on pieces to the problem, but the problem is not solved yet.”
With Emisor Oriente scheduled to be complete in 2014, I am hopeful that at least some of those problems will be alleviated. This is a great example of the magnitude that civil engineering works have on societies. I for one am proud to have a part in discussing this monumental solution to an age old problem.
The Oldest Robbins TBM still in Action? We visit a jobsite in Canada that may be using the World’s Ultimate Workhorse TBM
It’s a long-standing question in the world of tunneling: Which TBM has been operating the longest? What makes it so durable?
In May 2011, I visited the site of the Centennial Parkway Sanitary Sewer Tunnel in Hamilton, Ontario, Canada to find some answers. The rock portion of the tunnel, located in the shale of the Niagara Escarpment, is being bored by a Robbins Main Beam TBM in operation since 1968. The 2.7 m (8.8 ft) diameter machine was first used for a Hydroelectric Tunnel in Tasmania, and is now owned by McNally Construction, who has used it on multiple sewer tunnels in Toronto and Ottawa since 1972.
I arrived at the Centennial Parkway site on a sunny Friday afternoon along with Tunnels & Tunnelling North America editor Nicole Robinson, where we were greeted by McNally Project Sponsor Dave Bax and Field Technician Kenny Baxter.
After giving us some safety instructions, we were handed full rubber suits and boots. “You’re going to need these,” said Kenny. “It’s muddy on the shaft floor, and the material is red. It gets everywhere.” A quick look around the jobsite confirmed his statement—red clay-like material caked nearly everything, from trailers to trucks to boots.
We climbed down a long ladder into the shaft, and were given a tour of the small diameter tunnel. Kenny explained that the ring beams and wooden lagging installed at the tunnel entrance were due to the softer clay material encountered at that point. The rest of the rock portion of tunnel was being supported with rock bolts and steel straps. “The shale material is being recycled to use as brick. The clay was used by a local gun club for berms on their grounds.”
Single track muck cars rolled out as we walked out of the tunnel, carrying more heaps of reddish shale, before they were lifted by a crane and dumped on the surface.
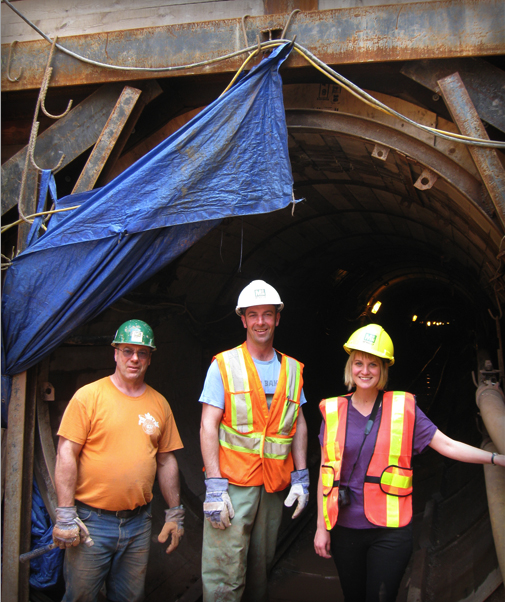
From left to right: Mark Walker, Laborer; Kenny Baxter, Field Technician; Nicole Robinson, T&T N. America, at the tunnel entrance.
Bax and Kenny mentioned that daily maintenance shifts have helped keep the veteran machine in good working order. Crews regularly check the 12-inch (304 mm) diameter disc cutters, and inspect the cutterhead and critical sub-systems. “We are not expecting a lot of wear. Our estimated completion for this tunnel is about two months,” said Bax. At the time of our Centennial visit, the TBM had advanced 200 m, at 1.8 to 2.1 m (6.0 to 7.0 ft) per hour, with no major issues.
The competent shale rock is certainly also a factor in limiting wear to the machine’s cutterhead and main bearing. Robust core components, including the main beam and gripper system, are key in keeping a TBM running for a long time (43 years, in this case).
Overall, the machine looked to be well equipped for its latest tunnel drive, and though it is impossible to know if it’s the world’s oldest working Robbins machine, it is certainly on the list. If you know of a Robbins machine that’s been operating longer, drop us a line in the comments section. We’d be interested to hear about it, and maybe even visit it!
Visiting Mexico City’s Newest Metro Tunnel: How the Country’s Capital is Upgrading its Aging Infrastructure
I was lucky enough to visit the jobsite of the Mexico City Metro Line 12 tunnel in October, along with Tunnels & Tunnelling International’s features editor Nicole Robinson. The country’s largest TBM, a 10.2 m (33.5 ft) diameter Robbins EPB, is excavating Mexico’s first new rail route in 10 years, below southern areas of the city. The 7.7 km (4.8 mi) long Mexico City Metro Line 12 is being excavated just 7 m (23 ft) below downtown areas in mixed ground including watery clay and boulders up to 800 mm (32 in) in diameter. The project is one of two major tunnels being constructed in Mexico City, the other being the 62 km (39 mi) long Emisor Oriente wastewater project, using six TBMs including three 8.93 m (29.3 ft) diameter Robbins EPBs.
During our visit to the site, the machine was between its first and second cut and cover station sites (it will hole through into seven such sites during the course of tunneling). We walked through the tunnel to view the machine, and later sat down with metro director Enrique Horcasitas of the Mexican Federal District for an interview on the current state of tunneling in Mexico.
Interview with Metro Director Enrique Horcasitas
Q: Were other methods besides tunneling with an EPB TBM considered for this tunnel?
A: Originally, the line was envisioned to be constructed using a technique of slurry walls cast in place. Most of Mexico City’s underground lines were built using this method. However, opening and closing city streets was not possible for a large portion of this route, while open cutting would interfere with existing municipal facilities and fragile archeological sites. In addition, cost estimates placed open cut excavation of the entire 24 km (15 mi) line at 19.5 billion pesos (USD $1.57 billion).
Our engineers needed a solution that would reduce risks and adverse impacts to traffic flow, as well as reduce project cost. For several weeks, methods were studied, and it was ultimately determined that a solution using multiple methods would work best. The 7.7 km (4.8 mi) long tunnel between Mexicaltzingo and Mixcoac would be excavated using a mixed ground EPB TBM, while the rest of the line between Atatonilco and Tláhuac, in much more difficult ground, would be constructed on the surface. Smaller portions of the tunnel would be constructed using cut and cover methods. The overall plan has a budget of 17.58 billion pesos (USD $1.41 billion).
Q: What does the city forecast for future ridership?
A: In the short term, it is expected this project will meet an average demand of 437,000 users per weekday. By 2030, this number is expected to grow to 600,000 users.
Q: How was the route of this line determined?
A: There is a long history associated with Mexico City’s metro plan. Engineers used to think it was impossible to excavate underground, given Mexico City’s highly complex geology. But in the 1950s and 60s, crews hand-mined the city’s main wastewater line, Emisor Central, about 100 m (330 ft) below ground. After the encouraging results, about 41 years ago, the project’s current contractor ICA (Ingenieros Civiles Asociados) began to make feasibility studies about metro lines running through the city. ICA was contracted to excavate the capital’s first metro lines, and 10 years later ICA gave the Federal District a gift: A master plan with over 300 km (185 mi) of rail that would serve as our template for decades to come.
The master plan is reviewed every 10 years, and it was most recently determined to build Line 12. The alignment is almost entirely true to the master plan, though it was made a bit longer after being reviewed by advisors, to match public demand for transportation.
Q: Are there any other metro expansions that the city is considering?
A: We are looking at doing an extension of the new Line 12, depending on the available budget. This extension would include 1,400 m (4,600 ft) of tunnels west of Mixcoac.
The next line we are considering in the master plan is Line 15, which would run directly below Insurgentes, the longest avenue in the world (18.8 km/11.7 mi), which goes straight through the city. A metro is absolutely needed on this route, as there are currently about 10,000 people per hour riding on just buses alone in each direction.
Q: Do you think current opinion about TBMs is changing in Mexico? What is the current climate towards TBMs?
A: I think the public can see the success of this tunnel—we arrived into the first station with precision, only 1 cm (0.4 in) to the side. We are monitoring settlement, and have detected only about 2 cm (0.8 in) at maximum—well within the limits and not enough to affect buildings. The public voted on where to excavate the next new line, they decided where to go, and so there is a consensus in society. I think that is why there has been a high degree of acceptance.
The operation of TBMs is seen as more favorable than hand mining or open cut, because there is less inconvenience at the surface, and building the tunnel itself is safer. For this reason, I think TBM tunneling will continue to increase in Mexico.
With the six TBMs currently excavating or being readied to excavate the new Emisor Oriente wastewater line, we now have seven TBMs operating in the country—this has never happened before. I think this is a tunneling boom!