Category: 新闻简讯
Robbins Main Beam Ramps Up at the Mid-Halton Outfall Tunnel
The News in Brief:
- A 3.5 m (11.5 ft) Robbins Main Beam is a hard rock veteran, with a career spanning 32 years.
- With the 6.3 km (4.0 mi) Mid-Halton Outfall Tunnel under its belt, the Robbins Main Beam will have bored nearly 30 km (18.6 mi) of tunnels.
- The refurbished TBM was beefed up with modern VFDs, electronics, and a modified cutterhead for high-capacity tunneling in hard rock.
- Contractor STRABAG is in charge of tunnel construction in Ontario, Canada, as well as the construction of two deep shafts.
Full Story:
On July 22, 2015, a 3.5 m (11.5 ft) Robbins Main Beam TBM began a new chapter in its storied 32-year career. Originally built for the Terror Lake project in Alaska, the veteran machine has been used all over the world, most recently in Hong Kong. Including its new 6.3 km (4.0 mi) long tunnel for the Mid-Halton Outfall in Ontario, Canada, the machine will have bored nearly 30 km (18.6 mi) of tunnels since 1983.
The machine’s latest endeavor will not be without challenges. The rebuilt TBM has been beefed up for high-capacity tunneling in hard rock. Geology is expected to consist of laminated shale with interbedded limestone and siltstone layers and a maximum rock strength of 120 MPa UCS. “We have kept this a simple, streamlined Main Beam machine, but we modified the cutterhead with larger muck buckets, so material can be moved through it faster,” explained Robbins Project Manager Lynne Stanziale. In addition the TBM was outfitted with fully modernized VFDs, electronics, and high-capacity gearing and motors. The back-up system was also modified to make it more mobile through two 130 m (427 ft) radius curves that the TBM will have to navigate, one in each direction.
“The concept of using refurbished TBMs bears great opportunities for value-for-money constructors,” said Christian Zoller, Commercial Project Manager for contractor STRABAG. “Our TBM “˜Peggie’ is evidence of that–when well-maintained and professionally refurbished, the lifespan of these machines is extensive. We’re pleased to see that our client Halton Region has the forward-oriented mindset that allows STRABAG to provide its renowned high level of skill and quality, paired with the good value for money that a refurbished TBM yields.”
Contractor STRABAG, who has had several projects in Canada including the epic Niagara Tunnel project, is in charge of the works. In addition to the tunnel, STRABAG had to construct two deep shafts for the launch and exit of the TBM. The scheme involves two sections of tunnel designed to carry treated effluent water from a treatment plant in Oakville into Lake Ontario. The completed system will upgrade water treatment capacity in the Halton Region of Ontario.
The TBM was launched from a 12 m (39 ft) diameter, 62 m (203 ft) deep shaft and is ramping up production, having excavated over 300 m by early September 2015. “An ongoing challenge associated with the tunneling on this project is the requirement to drive the TBM downhill for the first 4 km (2.5 mi) of the tunnel. Keeping the water that infiltrates the tunnel from flowing directly to the cutterhead requires significant effort,” said Terry McNulty, Technical Project Manager for STRABAG.
Management of water inflows is not the only challenge. A portion of the drive will curve to run directly under Lake Ontario for 2.1 km (1.3 mi), though the tunnel is deep enough that it will remain in bedrock. Once the machine has completed its final bore under Lake Ontario, it will be backed out of the blind heading and removed from an 8.0 m (26 ft) diameter shaft in a local park.
“We can already see the potential performance that this TBM will have, once fully assembled and tested. We look forward to the continued support and cooperation with our partner Robbins on this endeavor,” said Zoller. Though the TBM has only recently started up, crews are moving forward with a plan to line the tunnel with mesh panels and ring beams if necessary. A cast-in-place liner will follow on after tunneling is completed in August 2017.
"Rock Girl" Revs Up
The News In Brief:
- A Robbins 3.96 m (13.0 ft) Main Beam TBM launched in spring 2015 to bore Hawaii’s longest tunnel.
- The 4.8 km (3.0 mi) Kaneohe-Kailua Wastewater Conveyance Tunnel is being built for the City and Council of Honolulu to stem overflows of wastewater after rain events.
- Southland/Mole JV is constructing the tunnel””the first of its scope to be built in the Hawaiian Islands.
- As of June 2015, the Robbins TBM had excavated more than 300 m (1,000 ft), and was boring at a rate of 12 to 15 m (40 to 50 ft) per day in basalt rock.
In the spring of 2015 by the idyllic shores of Oahu, a Robbins 3.96 m (13.0 ft) diameter Main Beam TBM began its long journey. The TBM started its excavation on a 4.6 km (2.8 mi) drive for a new sewer tunnel in Kaneohe, Honolulu, Hawaii, USA. The machine, nicknamed Pohakulani, meaning “Rock Girl” in Hawaiian, launched from a 23 m (74 ft) deep starter tunnel on a mission to bore through almost 4.8 km (3.0 mi) of basalt bedrock. Contractor Southland/Mole JV is building the Kaneohe-Kailua Wastewater Conveyance Tunnel for the City and Council of Honolulu, which will improve wastewater infrastructure by eliminating overflows during rain events.
The deep tunnel option was not the first design considered for the project: preliminary plans called for a smaller tunnel traveling under the bay. As Kaneohe Bay is an environmentally-sensitive area, a deep tunnel remained an attractive option. Richard Harada, of project consultant Wilson Okamoto Corporation, explains the ultimate decision: “A number of factors were considered in making the decision to build a deep tunnel including reliability, construction costs, life cycle costs, environmental impacts, constructability and qualified contractor availability.”
During the tunnel design phase, it was decided that the tunnel route should travel inland and deeper underground in order to bypass one of the few residential areas along the alignment. Designers introduced an isolated curve in the tunnel alignment of 150 m (500 ft) radius, requiring the TBM to be designed with a unique back-up system. There will also be operational procedures when crews navigate the tunnel curve, requiring the machine to be operated using half strokes rather than a full TBM stroke.
The curve is not the only unusual aspect of the tunnel; in fact, a tunnel on this scale has not been built in the Hawaiian Islands before. Everything from the logistics of the tunnel operation to pre-grouting sections ahead of the TBM for groundwater control are new to the Aloha State. Director of Southland, Tim Winn, elaborates: “There has not been a Tunnel Boring Machine of this size in the Hawaiian Islands or a tunnel of this length. The tunnel is being driven from an active Water Treatment Plant (WTP), and space is at a premium. There are also simultaneous contracts being performed there outside the scope of our work.” He adds that although there have been challenges, teamwork has been key: “Robbins Field Service has been extremely valuable during assembly and commissioning of the TBM.” As of June 2015, the TBM has excavated more than 300 m (1,000 ft), and is boring at a rate of 12 to 15 m (40 to 50 ft) per day in basalt rock. Rock bolts, steel arches, wire mesh, and ring beams are being installed as necessary.
Upon completion, the deep tunnel will enhance water treatment capabilities and further aid in ceasing non-compliant, uncontrolled or moderately treated wastewater discharges. The Main Beam TBM is estimated to end its journey in eight to ten months at the Kaneohe Wastewater Pre-Treatment Facility.
Remotely Controlled SBU set to Revolutionize the Industry
The News In Brief:
- The Robbins Remote Controlled Small Boring Unit (SBU-RC) is a new type of boring machine capable of excavating small diameter hard rock tunnels at long distances, on line and grade.
- The SBU-RC is currently manufactured in the 36-inch (900 mm) diameter range, but could be designed as small as 30 inches (750 mm) in diameter.
- The SBU-RC features a smart guidance system for pinpoint steering accuracy and is controlled from an operator’s station on the surface.
- Muck removal is accomplished through a vacuum system, making the Robbins SBU-RC more cost effective than MTBMs requiring slurry and cleaning plants onsite.
- A Robbins 36-inch (900 mm) SBU-RC completed a critical hard rock crossing below railroad tracks two weeks early in Bend, Oregon, USA, breaking through on May 5, 2015.
- The SBU-RC holed through on line and grade after achieving up to 50 ft (15 m) of advance per day in abrasive basalt rock up to 7,000 psi (48 MPa) UCS
In Bend, Oregon, USA, local contractor Stadeli Boring & Tunneling had a unique set of circumstances for a new gravity sewer interceptor. “We had a contract with general contractor Taylor NW to furnish and install 323 ft (98 m) of 36-inch (900 mm) steel casing under railroad tracks. Line and grade were very crucial, and the tolerances were very close. We had to be right on,” said Larry Stadeli, president and owner of Stadeli Boring & Tunneling. In addition to those parameters, the job was also in solid rock.
Fortunately, there was a solution available to help them. The contractor turned to The Robbins Company, a business that they had worked with many times over the years for their Small Boring Units (SBUs). Stadeli first contacted Robbins 10 years ago to rent a 30-inch standard Small Boring Unit (SBU-A), and has since rented dozens more. The company currently owns two SBU-As, but their Bend, Oregon job required precision guidance systems that their SBU-As lacked. “We met with Robbins in Ohio and told them what our needs were. They felt like their 36-inch (900 mm) prototype machine, which they had tested at one other job in Oman, would be a good fit. They listened to what we were wanting and needing to have done,” said Stadeli.
At Robbins, Kenny Clever, SBU Sales Manager, and a group of engineers were honing the prototype machine that fit the bill. Known as the SBU-RC, for Remote Controlled Small Boring Unit, the machine was equipped with a smart guidance system by TACS. The guidance system could show an operator projections of the future bore path so steering corrections could be made before the machine was ever out of line and grade. The feature was critical for the crossing below the railroad tracks, which could not be shut down if problems occurred.
The SBU-RC is currently manufactured in the 36-inch (900 mm) diameter range, but could be designed as small as 30 inches (750 mm). The machine operates much like a Motorized SBU (SBU-M) with a circular cutterhead and cutting tools that can excavate hard rock or mixed ground conditions. An in-shield drive motor provides torque to the cutterhead, while a pipe jacking system or Auger Boring Machine (ABM) provides thrust. Clever explains the biggest differences: “There is no manned entry. It eliminates the human element, so it is safer and there is no need for ventilation and other things required when you have a worker in the tunnel. With its guidance system, it also eliminates much of the risk on line-and-grade-critical bores.” Muck removal is accomplished via a vacuum system connected to a vacuum truck. The machine is capable of excavating hard rock and mixed ground crossings up to 500 ft (150 m) long, depending on conditions.
While microtunneling machines have been used on jobs such as these, Clever cites key advantages for the SBU-RC: “There is no slurry to mix or contend with. With MTBMs the slurry must be cleaned, pumped, and treated. With the SBU-RC there is a clean and dry pit, with no spoils to remove. The way the SBU-RC operates is much more cost effective. The SBU-RC is also available for lease; MTBMs are often not cost effective to lease for contractors trying to stay competitive.
The SBU-RC was delivered on April 14, 2015, and was lowered into a launch pit 26 ft (8 m) deep. There were several early tweaks to the setup including a larger vacuum truck that improved suction, and some modifications to the cutterhead including grill bars. These modifications were expected and will be incorporated into later versions of the machine.
The machine began boring in volcanic basalt rock that was full of fissures, fractures, and rubble pockets between 5,000 and 7,000 psi (34 to 48 MPa) UCS. While the start-up was rough going, crews quickly began getting rates of 20 ft (6 m) per day. “As we got used to the machine we went up to 40 ft (12 m), and one day we even got 50 ft (15 m). We were able to cut off a couple weeks of our schedule time. Taylor NW was very pleased about it. When you look down the pipe now after it’s finished, it looks like a rifle barrel. There is no sag, it’s all in one straight line,” said Stadeli.
The early completion by the SBU-RC delighted the City of Bend and all those involved. “I think the SBU-RC is an exciting piece of equipment that has been compressed into a 36-inch size. To make it all work it is very compact. It’s impressive that the components have been sized down and it still works so efficiently,” said Stadeli.
With the clear success in Oregon, Robbins is looking to lease the machine on more projects and expand their offerings. As Clever put it: “Finally our industry has provided a small diameter, on-line-and-grade machine that will drill in solid rock at distance. This is a game changer, it will be the most innovative piece of equipment in our industry for a long time.”
Rugged Robbins TBM and Conveyors go for Gold in Indianapolis
The News In Brief:
- The Robbins 6.2 m (20.2ft) diameter Main Beam TBM completed the Eagle Creek extension tunnel on March 5, 2015.
- The world-record-setting jobsite includes a number of unique aspects, the conveyor system being one of them. The Robbins continuous conveyor consists of 82,000 ft of belt and travels through two unprecedented 90-degree curves.
- The project was put in place to reduce the amount of raw sewage overflows in the city’s neighborhoods and clean up tributaries along the White River.
On March 5, 2015, a Robbins 6.2 m (20.2 ft) diameter Main Beam TBM finished boring a 2.8 km (9,175 ft) long extension tunnel, known as the Eagle Creek Tunnel, for the Indianapolis Deep Tunnel System in Indiana, USA. The contractor, Shea/Kiewit (S-K) JV, had much to celebrate: “I’m proud of our world records, and most of all our men and the hard work they have done as a team, working together to accomplish a project of this size,” explained Stuart Lipofsky, Project Manager, for S-K JV. “We finished the first 12.5 km (41,000 ft) [of the main tunnel] almost a year ahead of schedule. The extension added time but what is remarkable is that we were still able to finish within the original contractual dates,” continued Lipofsky. The completion of the first leg of a much larger tunnel system targets three critical CSOs that flow into the nearby White River, and will go online in 2017. The completed tunnels bring the city one step closer to achieving its consent decree with the U.S. Environmental Protection Agency (EPA), set to be achieved by 2025, to eliminate overflows into the city’s rivers.
The rebuilt Robbins hard rock TBM was first used on the 12.5 km (7.8 mi) long main tunnel, called the Deep Rock Tunnel Connector (DRTC). The new cutterhead arrived onsite in November 2012, and the machine was launched from a 76 m (250 ft) deep shaft to bore through limestone and dolomite. The TBM achieved world records in its size class of 6 to 7 m (20 to 23 ft), including “Most Feet Mined in One Day” (124.9 m/409.8 ft); “Most Feet Mined in One Week” (515.1 m/1,690 ft); and “Most Feet Mined in One Month” (1,754 m/5,755 ft). According to Tim Shutters, Construction Supervisor for project owner Citizens Energy Group, there were two main factors for the TBM’s high performance: “The first one is the very nice cutterhead provided by Robbins. It has performed very well. [Second], rock conditions are favorable for mining operations and optimal for fast production.”
Another important element that helped the speedy machine achieve a fast advance was, as Lipofsky put it, “one of the most complex continuous conveyor systems in North American tunneling construction.” The custom-built Robbins system, consisting of 25 km (82,000 ft) of belt, included horizontal and vertical conveyors for efficient muck removal. The system was the first built by Robbins to go through such sharp curves: “The belt is going through two 90-degree curves in opposite directions and S-curves in other places. It’s very unusual and amazing to see a belt system perform as well as this one did,” said Lipofsky.
Once complete, the deep tunnel project will reduce the amount of raw sewage overflows and clean up tributaries along the White River. Tim Shutters describes the environmental benefits the project will provide the Indianapolis community: “I’ve lived in Indy all of my life, and the White River has never been a focal point for the city as there is a lot of pollution. I really think that once it has been cleaned up, people will want to visit, they will swim and fish, and property values along that body of water will go up. Being able to finally utilize the river is key for us.”
After the early completion of the Eagle Creek Tunnel, the project will be moving into its next two tunneling phases. The White River Deep Tunnel will continue 8.5 km (5.3 mi) north of the completed DRTC and pump station. The Lower Pogues Run Deep Tunnel will split off 2.7 km (1.7 mi) from the White River Deep Tunnel heading east. Two additional tunnels, including Fall Creek and Pleasant Run, are anticipated to be built in 2020, and the project (27 km/17mi of tunnels in total) is expected to be fully completed by the end of 2025.
Announcing the Crossover Series of Robbins Dual Mode TBMs
Robbins proudly announces its Crossover Series of TBMs, a line of field-tested, rugged Dual Mode-type machines. Crossover TBMs feature aspects of two TBM types, and are ideal for mixed ground conditions that might otherwise require multiple tunneling machines. The XRE (standing for Crossover Rock /EPB) is the most common type of hybrid machine, and features characteristics of Single Shield Hard Rock machines and EPBs for efficient excavation in mixed soils with rock.
An XRE TBM recently completed tunneling at Australia’s Grosvenor Decline Tunnel, where it excavated two mine access drives at rates fourteen times faster than a traditional roadheader. The latest drive was completed on February 9, 2015. “This was a big step forward for the mine to appropriately use civil tunneling technology for a mining application. I take my hat off to the management of owner Anglo American Coal to have the foresight and leadership ability to take this step. Using the Crossover technology [versus the traditionally-used roadheader method], the project was finished on schedule,” said Lok Home, Robbins President.
Additional types of Crossover machines include the XSE (Crossover between Slurry/EPB) and the XRS (Crossover between Rock/Slurry) TBMs. The Crossover series is quickly gaining in popularity, with Robbins Crossover TBMs currently being assembled in Mexico, Turkey, and Azerbaijan. An XRE TBM will begin excavation for Mexico’s Túnel Emisor Poniente II (TEP II) later this year, while an XSE is being readied for excavation at the Baku Metro.
The rebranding and Crossover terminology embodies the concept that the machines are able to cross over between modes, says Home. The unique machines are a top focus point for the company: “Robbins comes at this business with extensive rock experience so everything we design comes with the assumption that there will be tough conditions. When you have to “cross over” to another mode then already you are in difficult conditions, and contractors need robust machines to get through these challenges,” says Home.
Home foresees that machine sales will grow as more projects worldwide are planned in difficult and varying ground conditions. Survey results back up the trend, indicating an increased interest in Crossover-type machines worldwide. “This is a continuous evolution and we are consistently endeavoring to improve Crossover designs. We have three of the machines in production now and I see this number increasing year by year as the industry sees and accepts their value.”
Breakthrough Robbins "Crossover" Machine Breaks Through
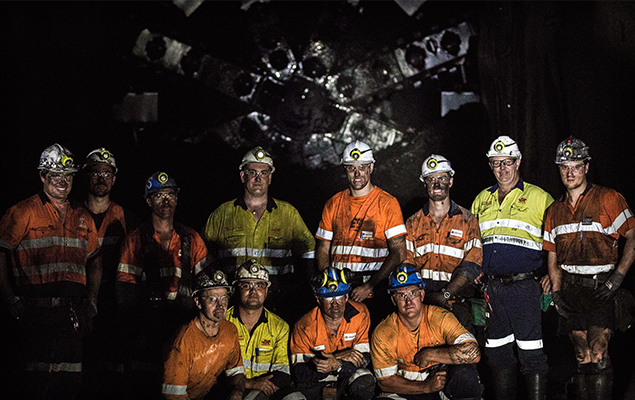
Workers from owner Anglo American celebrate the breakthrough of the Robbins Crossover Rock/EPB machine on February 9, 2015. Image courtesy of Anglo American.
The News in Brief:
- The Grosvenor Decline tunnel marks the first method of a TBM being used in a coal mine in Queensland.
- The unique Crossover Rock/EPB TBM features design aspects from both hard rock Single Shield and soft ground EPB TBMs to bore through a variety of ground.
- The “Crossover” designation is new for Robbins, and will going forward be the designation for all types of Dual Mode TBMs.
- The Crossover TBM for Grosvenor was uniquely designed for excavation in conditions that included the potential for methane gas. It was designed as Class 1, Division 2 Coal Mine Compliant.
- The TBM excavated at rates fourteen times that of a traditional roadheader operation (70 m per week on average vs. 5 m per week).
- The TBM broke through into an active section of the coal mine on February 9, 2015, completing excavation of two mine access tunnels.
Full Press Release:
A ground-breaking TBM brought a mining operation one step closer to first coal on February 9, 2015. The Robbins Dual Mode “Crossover” Rock/EPB TBM completed tunneling at Anglo American’s Grosvenor Project in Queensland, Australia. The “Crossover” designation is new for Robbins Dual Mode TBMs, and will be used for all such projects going forward. The efficient type of TBM used at Grosvenor is now known as an XRE, standing for Crossover between Rock/EPB. Other types of machines are designated the XSE (Crossover between Slurry/EPB) and the XRS (Crossover between Rock/Slurry).
The Grosvenor Mine, a Greenfield coal operation, was the first to utilize TBM technology for mining tunnels in Queensland. Mine owner Anglo American Coal chose the 8.0 m (26.2 ft) machine for two decline access tunnels at grades of 1:6 and 1:8, one for conveyors and another for people and equipment.
The XRE TBM was picked over the traditionally-used roadheader method for several reasons, including excavation speed and tunnel maintenance. The choice proved prescient with the machine excavating at a rate approximately ten to fourteen times faster than a roadheader™bout 70 m per week for the TBM vs. 5 m per week for a roadheader. In addition, the final tunnels have a smooth profile and are segment-lined, requiring minimal upkeep during the planned 40-year life of the mine. “In the coal mining community, and certainly in Queensland, companies are aware of the Grosvenor project and how it has set a benchmark for underground access drift construction,” said Glen Maynard, Robbins Field Service Site Supervisor at Grosvenor.
The machine’s Crossover capabilities enabled it to operate in both hard rock and mixed ground. In addition, the TBM was required to operate during gaseous conditions. The unique TBM design included a cutterhead capable of interchanging hard rock and soft ground cutting tools, a two-stage center-mounted screw conveyor, a “quick removal” shield system, and flame-proof machine components due to the possibility of methane gas in the underground environment.
The TBM was optimized for hard rock and mixed ground excavation in geology ranging from soft clay and soil to sandstone and basalt. The two-stage screw conveyor worked in both ground conditions to draw muck from the tunnel face. Two sets of shields were built for the TBM’s “Quick Removal” system, and were detached from the machine at the end of each blind tunnel to be left in the ground for constant support, a requirement in Australian tunnels. The inner core components of the TBM were then retracted out of the segment-lined tunnels on specially designed transport dollies.
The machine began boring the conveyor tunnel in December 2013, and after completion in May 2014 was successfully retracted and transported to the second tunnel site. The machine was then re-commissioned for the people and equipment tunnel in November 2014 with a new set of shields. Once excavation commenced, boring was completed in 88 days at an average of 10.9 m per day, with a best day of 25.2 m. The bore itself was similar to the first, with few challenges encountered other than elevated methane gas levels that required several temporary stoppages in order to safely remove the gas from the tunnel. “The machine performed very well and had high reliability. The cutting tools, in particular the knife edge bits, were exceptional. The bits were required for most of the drive and one complete set lasted 650 meters,” said Maynard.
The team is now preparing the machine for its final retraction and roll-out, and it will be on the surface in less than two months. The TBM will then be stored onsite for future Anglo American mining projects.
Once the longwall mine is operational in 2016, Grosvenor is expected to produce five million tonnes of coal per year over the next 26 years.