Category: 罗宾斯博客
Tunneling in Turkey: The Esme Salihli Railway
Large diameter tunneling in mixed ground has historically been seen as a challenge, but a recently completed tunnel in Turkey has changed the conversation. A 13.77 m diameter Crossover XRE TBM bored the Esme Salihli Railway Tunnel at world-record-setting rates of up to 721.8 m in one month, making it the fastest TBM over 13 m in diameter. What allowed the project to achieve such high advance rates?
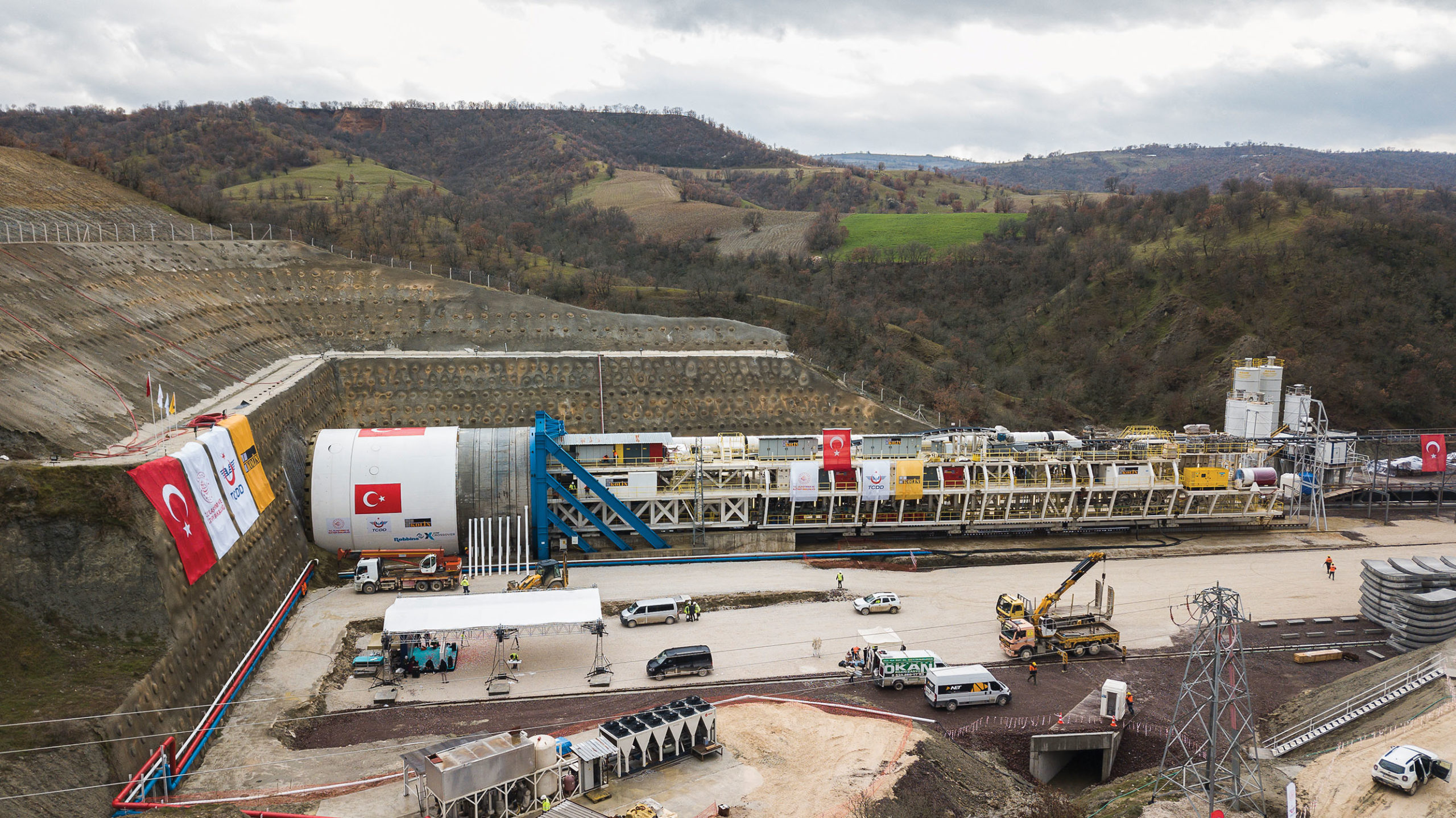
A Robbins Crossover machine that bored Turkey’s 3.05 km (1.90 mi) Eşme-Salihli Railway Tunnel through mixed conditions including sandstone, gravelstone, claystone, and siltstone for contractor Kolin Construction.
Machine Design for Variable Geology
The Eşme-Salihli Railway Tunnel is a short section of high-speed railway, measuring 3.05 km (1.90 mi) through mixed conditions. Contractor Kolin Construction conducted 15 core drillings at 200 m intervals prior to the start of construction, with results predicting occasional groundwater and weak rock between 5 to 9 MPa (720 to 1,300 psi) UCS, with the potential for a gassy environment. Rock and soil types included sections of gneiss, sandstone, claystone, mudstone, quartzite, and silt.
A dual mode rock/EPB TBM design was created for the project, in which no design elements were sacrificed in the engineering: The machine was fully capable of operating in 100% EPB mode or 100% Hard Rock Single Shield Mode. The TBM was designed for sections of hard rock and mixed ground, in highly variable conditions. For details on the design, check out this technical paper.
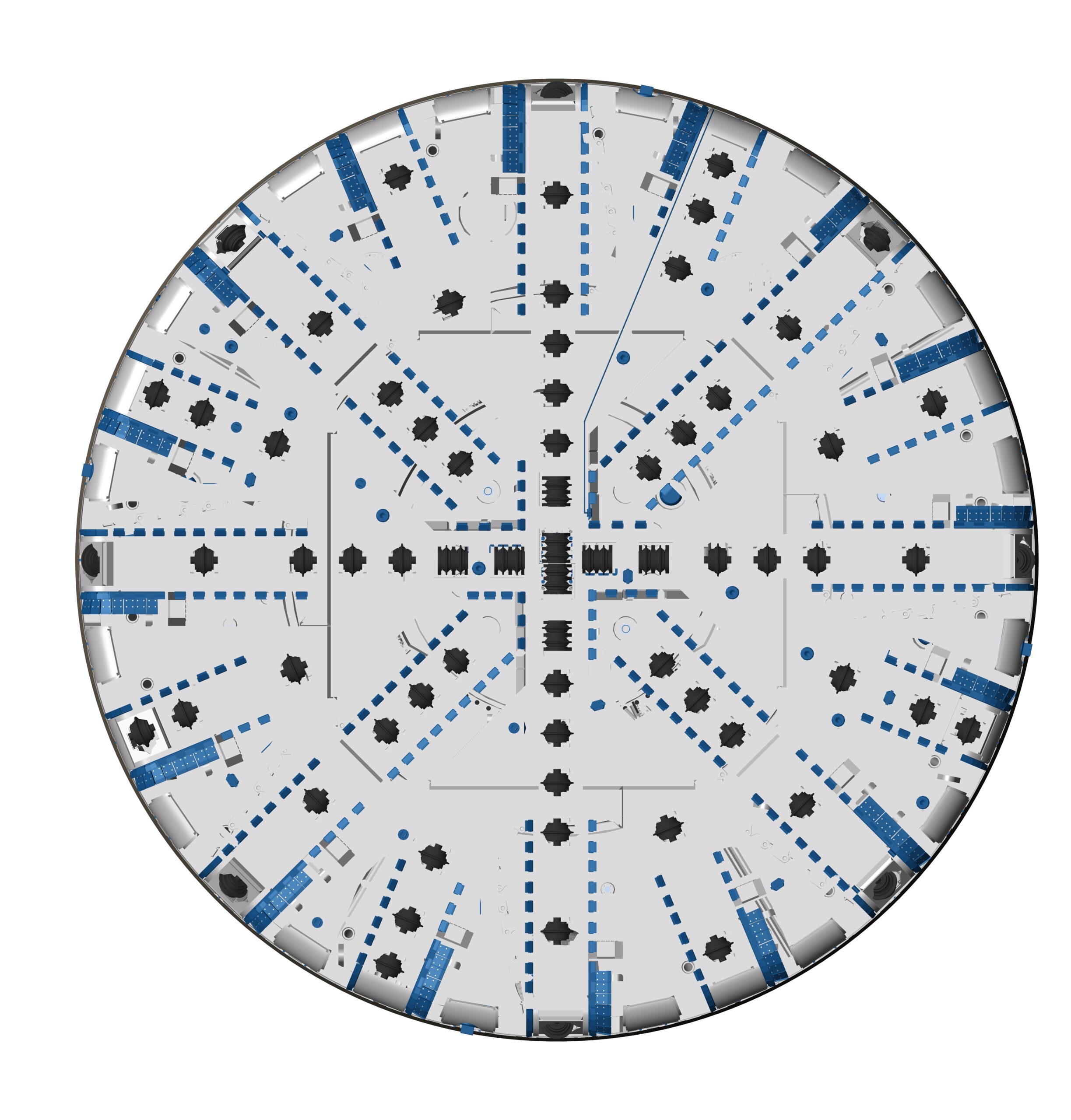
The cutterhead in hard rock mode.
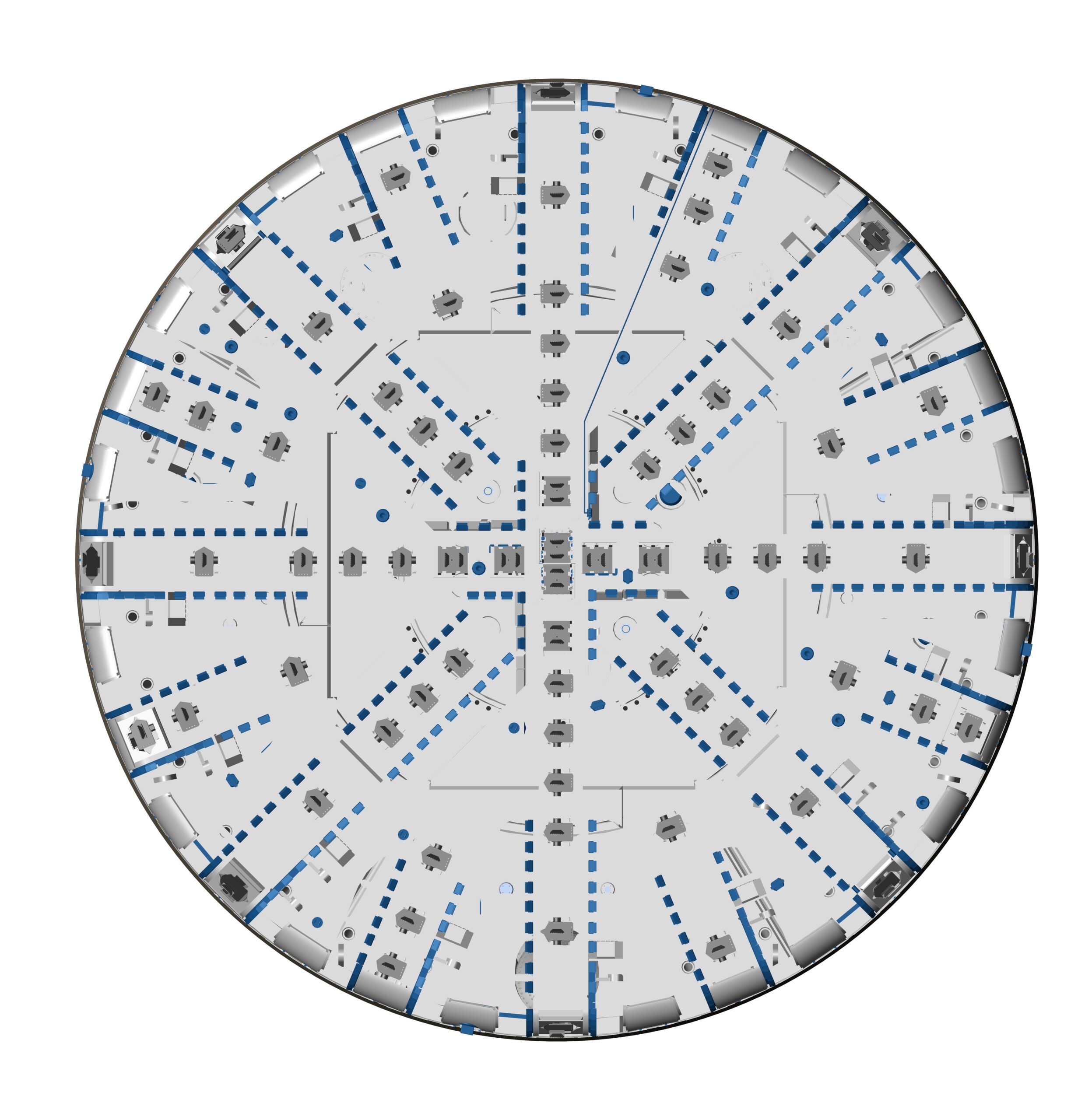
The cutterhead in EPB mode.
Epic Results
The 13.77 m Crossover XRE machine launched on its 3.05 km (1.90 mi) bore at the end of March 2021. While some of the crossover features proved beneficial the TBM was able to utilize the screw conveyor for mucking for the complete tunnel drive, which was a further benefit for the project’s overall schedule.
What allowed the machine to perform at high rates of advance? Utilization charts reveal that 38% of the total time was spent on excavation, 27% on ring assembly, 21% on planned downtime such as maintenance, and 14% on unplanned downtime.
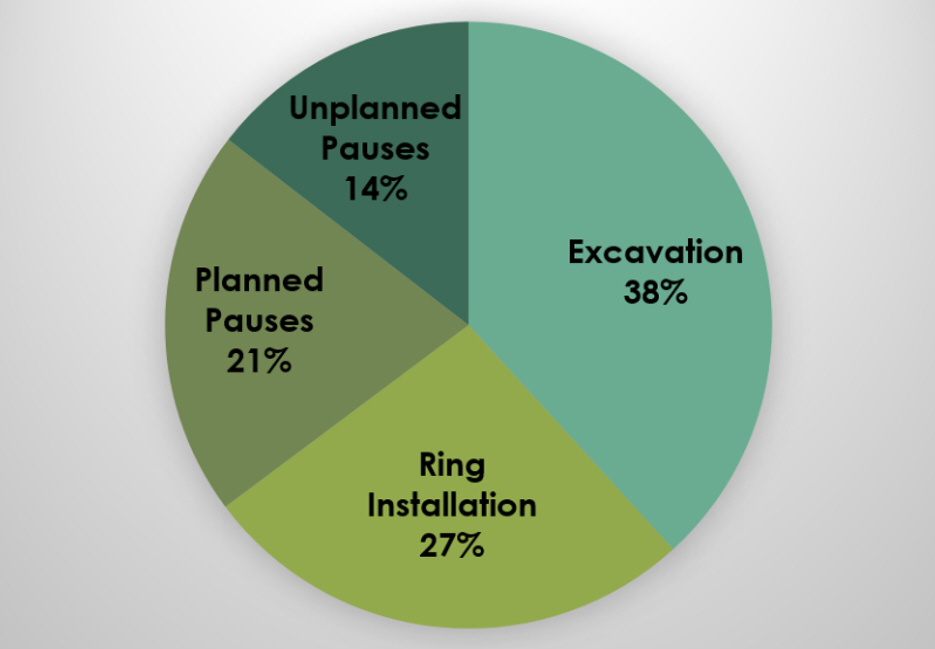
Productivity pie chart.
When looking at planned downtime, the most time was spent on cutterhead maintenance at 28%, followed by crew breaks at 22%. An average machine push took 60 minutes, while ring builds averaged 42 minutes.
Delays caused by mechanical, hydraulic or electrical failures were very low. The contractor cited the main reasons for minimal downtime, and thus high advance rates, as regular planned maintenance, cleaning, an experienced team, and an adequate supply of spare parts. Ultimately the tunnel was completed in just 6.5 months.
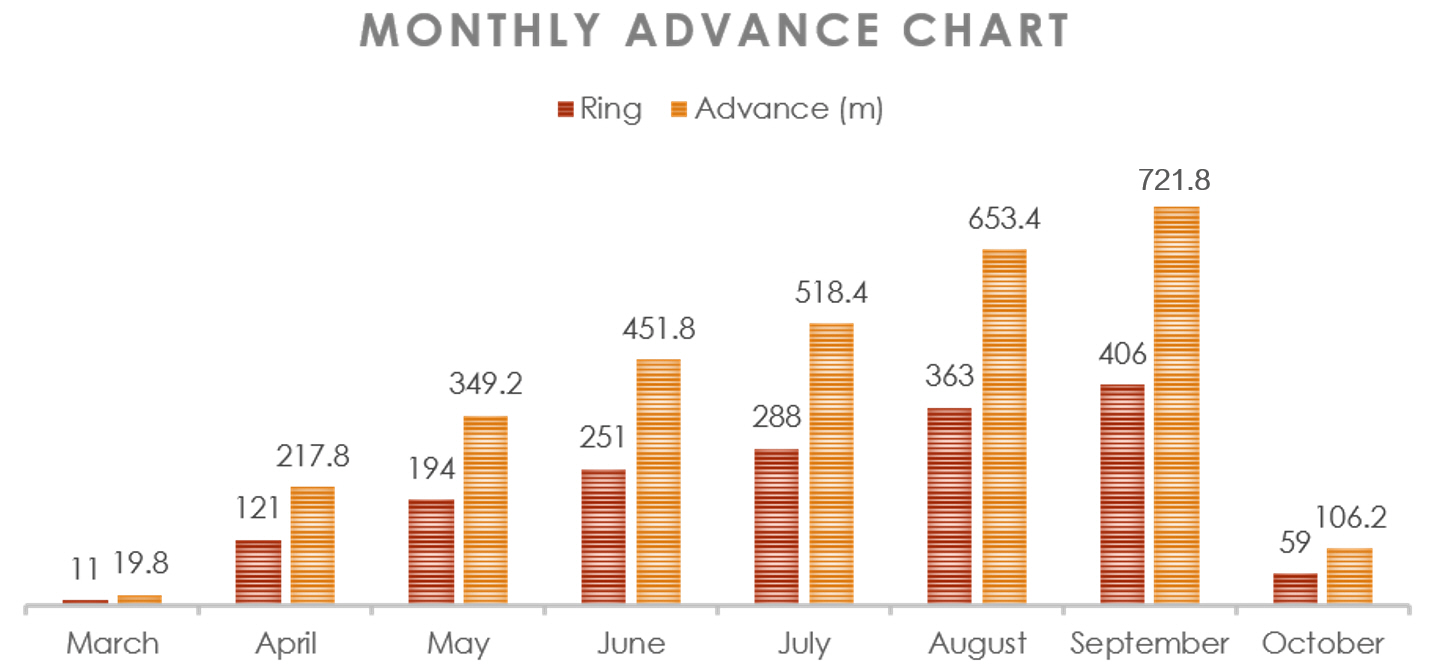
Monthly advance rate chart in meters bored and rings built.
In Conclusion
Large diameter, dual mode rock/EPB machines can and will excavate mixed ground conditions efficiently – even at world record rates. While similar projects in Turkish geology have met with challenges, the Esme-Salihli tunnel shows that with proper maintenance and a knowledgeable crew, equipment downtime can be kept to a minimum and advance rates can remain high.
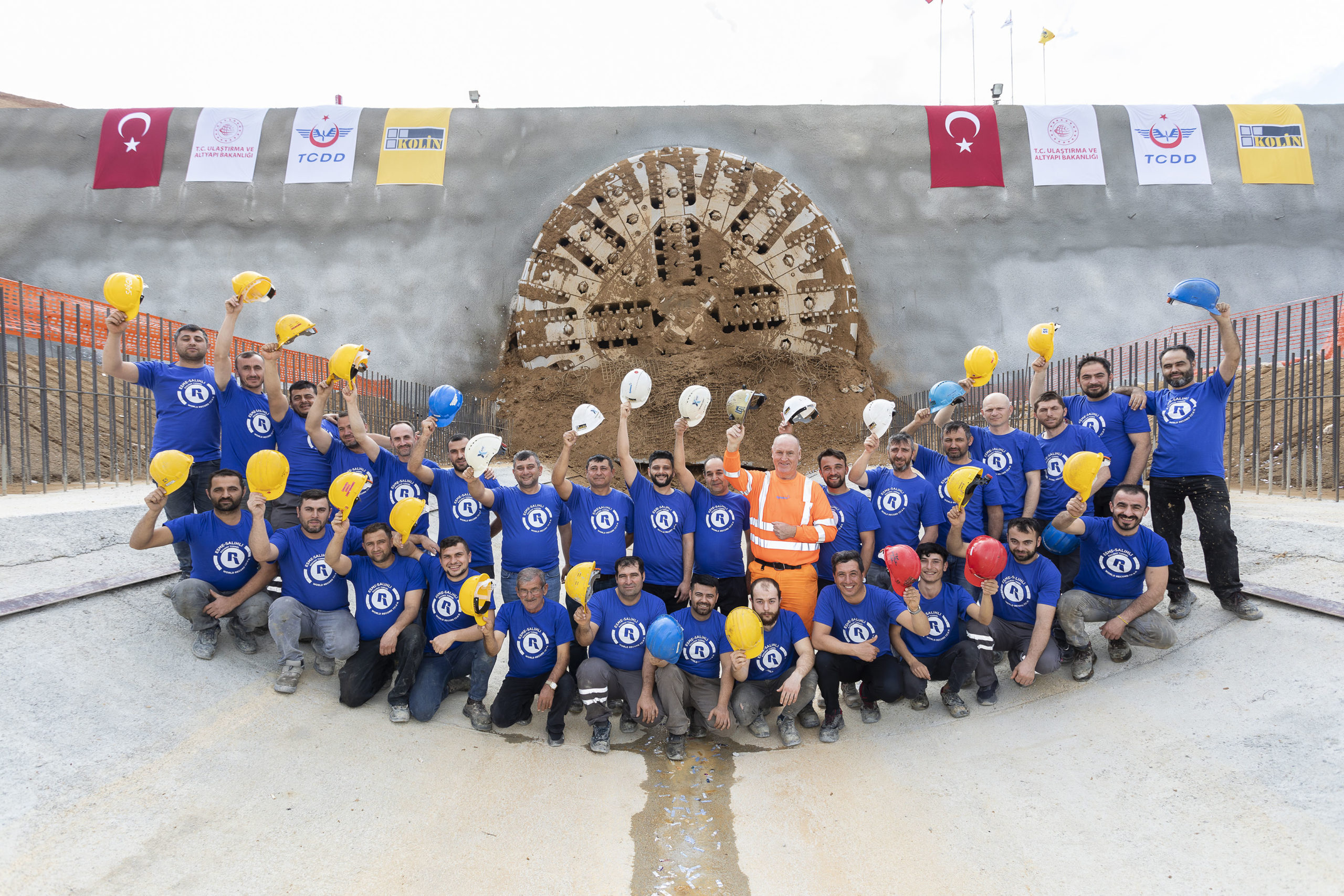
Personnel from contractor Kolin Construction and Robbins celebrate the breakthrough of a Crossover (XRE) TBM after it completed Turkey’s Esme Salihli Railway Tunnel.
Incredible India: Machines on the Move in Agra and Delhi
India’s metro network has undergone extensive growth in recent years, and is showing no signs of slowing. Multiple Robbins machines are part of tunneling work in cities across India, including Agra and Delhi.
Agra Metro: From First Site Acceptance…
On February 16, 2023 the Robbins crew and contractor SAM India celebrated the site acceptance test for the first of two 6.65 m diameter EPB TBMs at Agra Metro. The machine began boring a 1.3 km long tunnel in soft soils, for Uttar Pradesh Metro Rail Corporation Ltd.
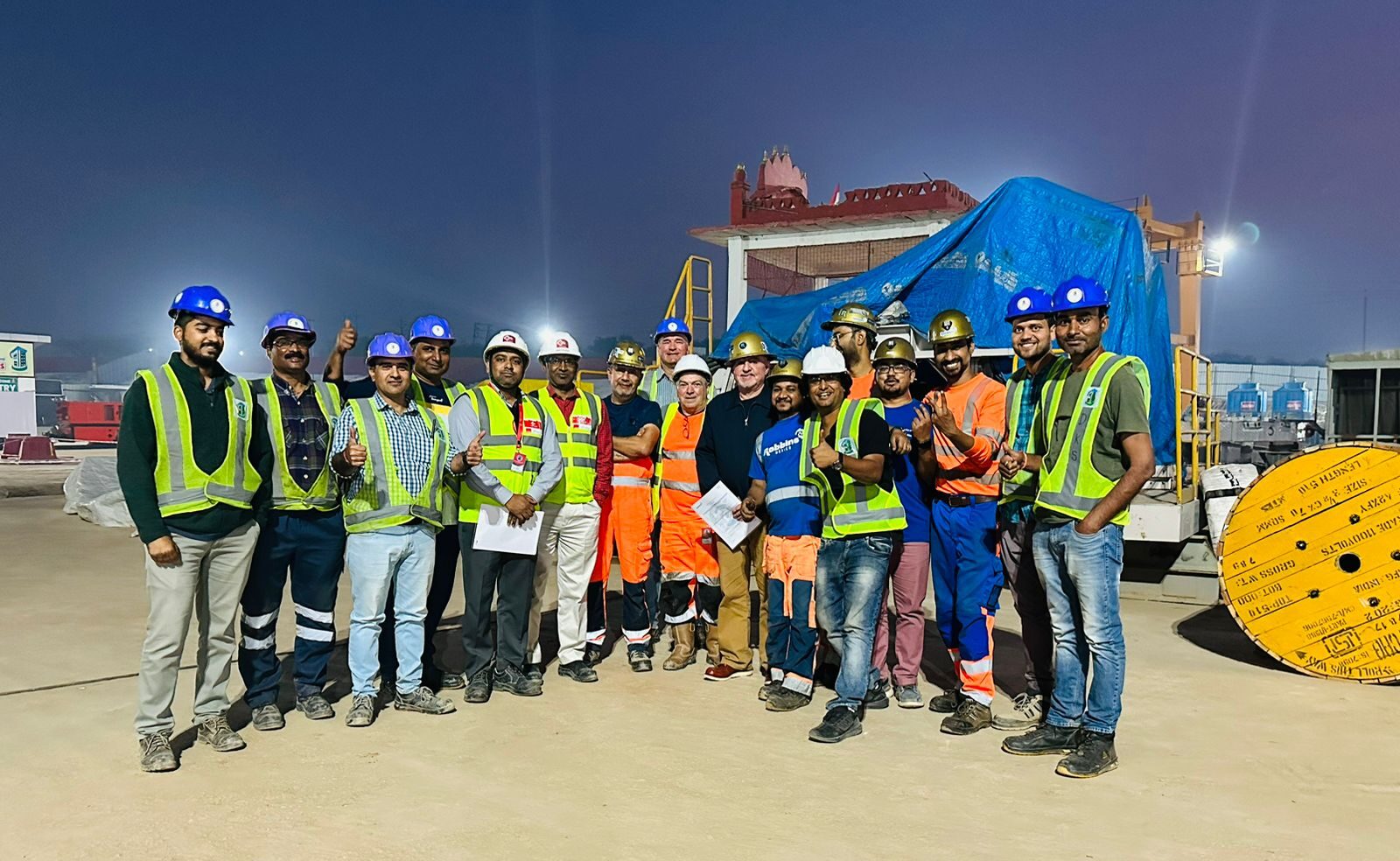
The Robbins team celebrates a successful site acceptance test for the first of two Robbins EPBs at Agra Metro.
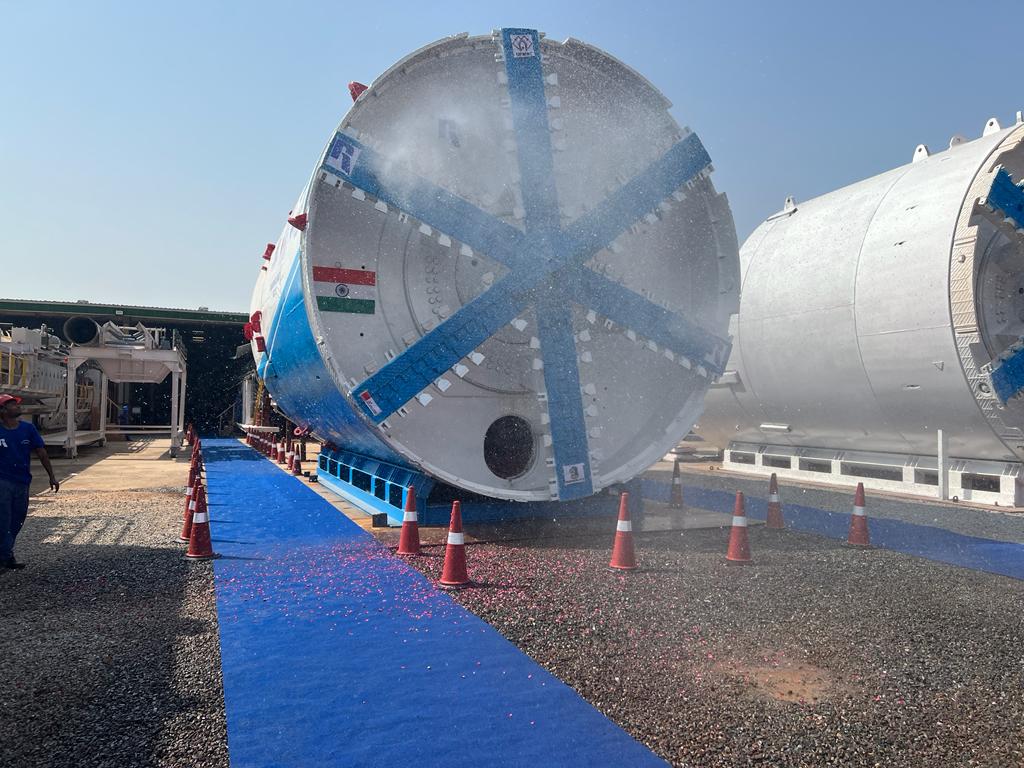
The Robbins EPBs, seen during their Factory Acceptance, are designed for soft soils.
To Second Site Acceptance…
With the first TBM well into tunneling, a second 6.65 m Robbins EPB underwent site acceptance on April 13, 2023 to bore a parallel 1.3 km long tunnel in soft soils. The crew gathered for a ceremony before sending the TBM on its way.
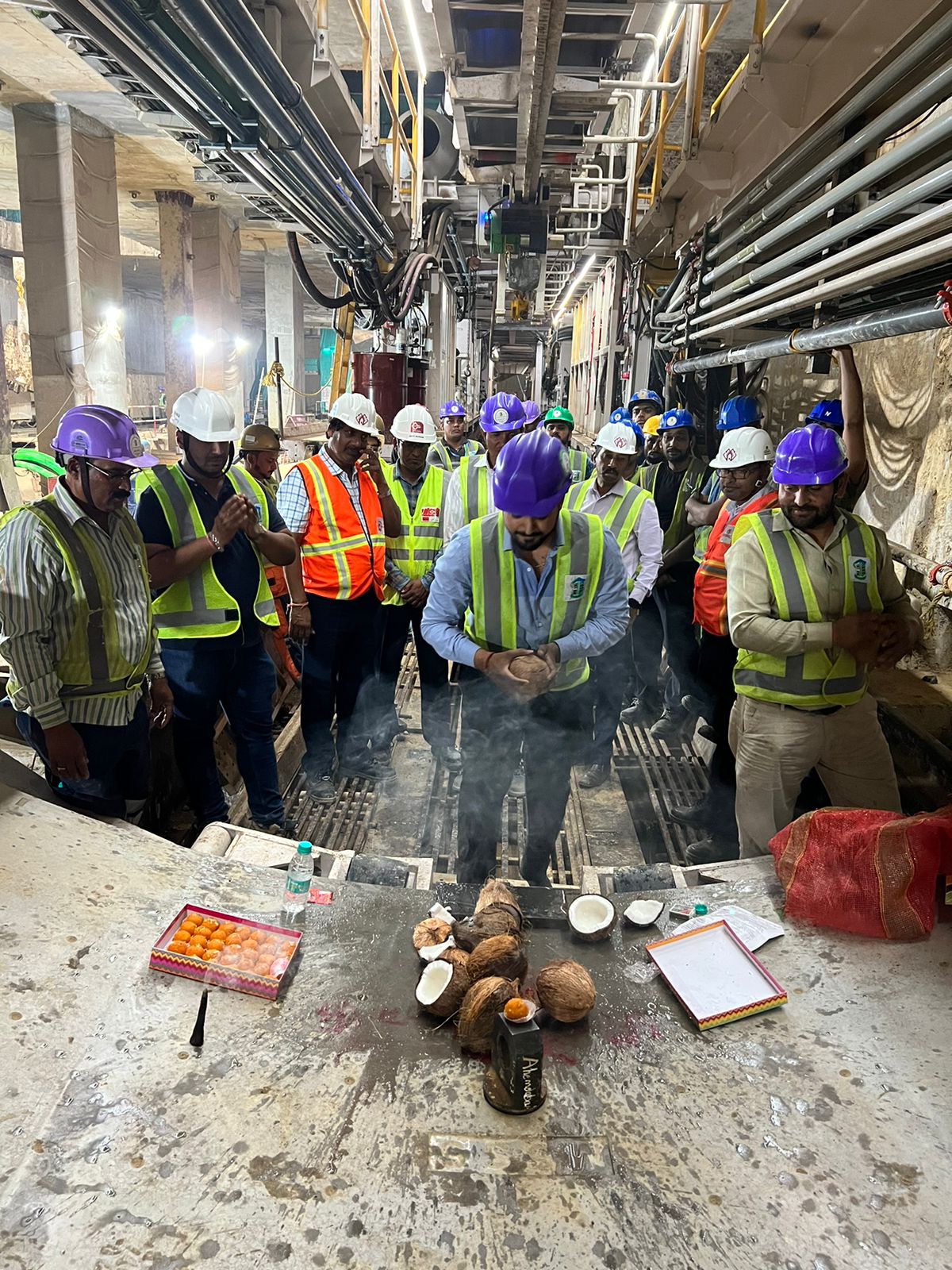
The crew gathers for the site acceptance ceremony of the second Agra metro EPB.
To First Breakthrough!
Just a few days later on April 26, 2023 the first machine made an intermediate breakthrough into a station site, completing the Jama Masjid to Agra Fort stretch of the metro. The machine bored a total of 345 m in sand and clay, and broke through to a celebration by the crew and project teams.
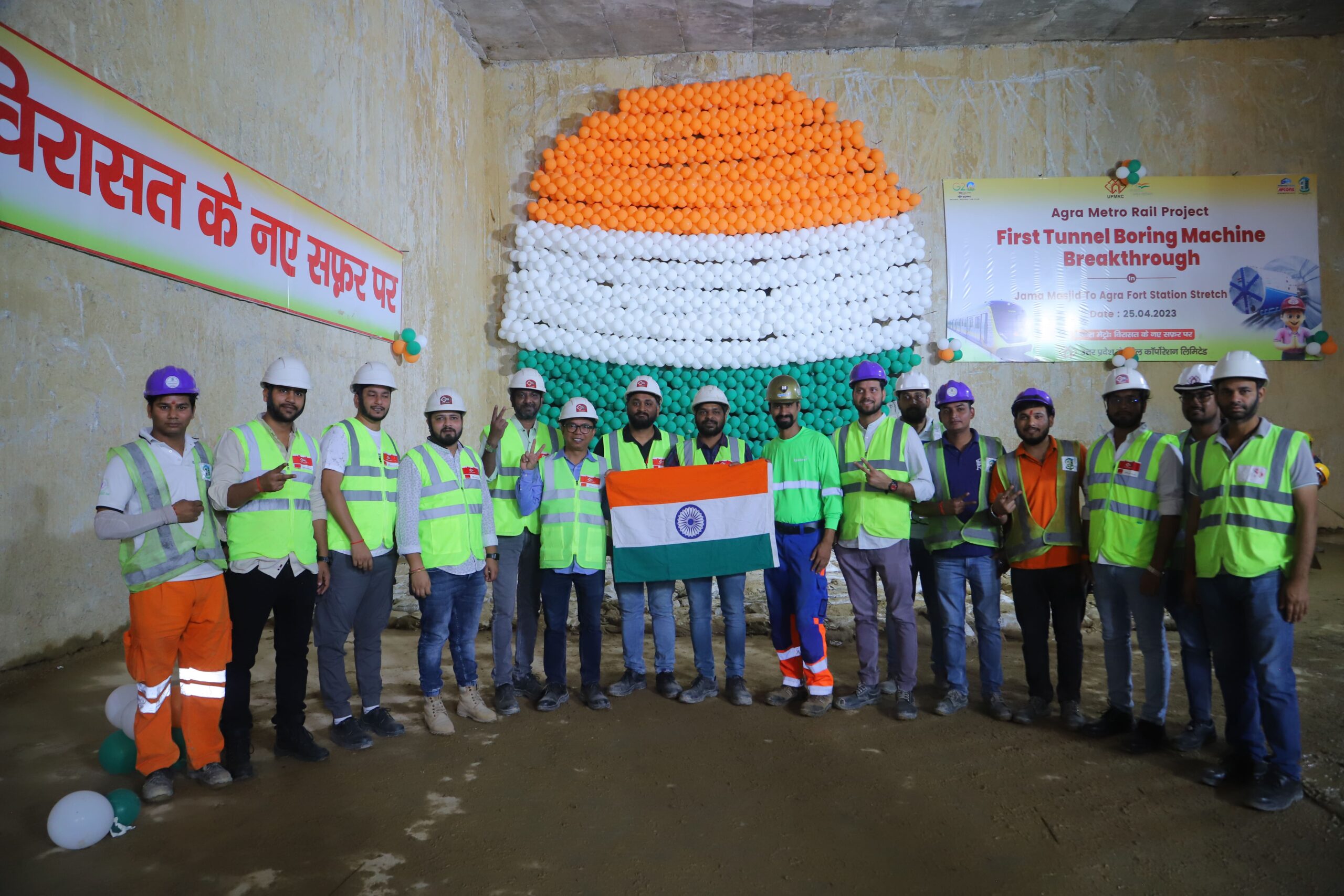
The crew anticipate the first breakthrough of the Robbins EPB at Agra Metro.
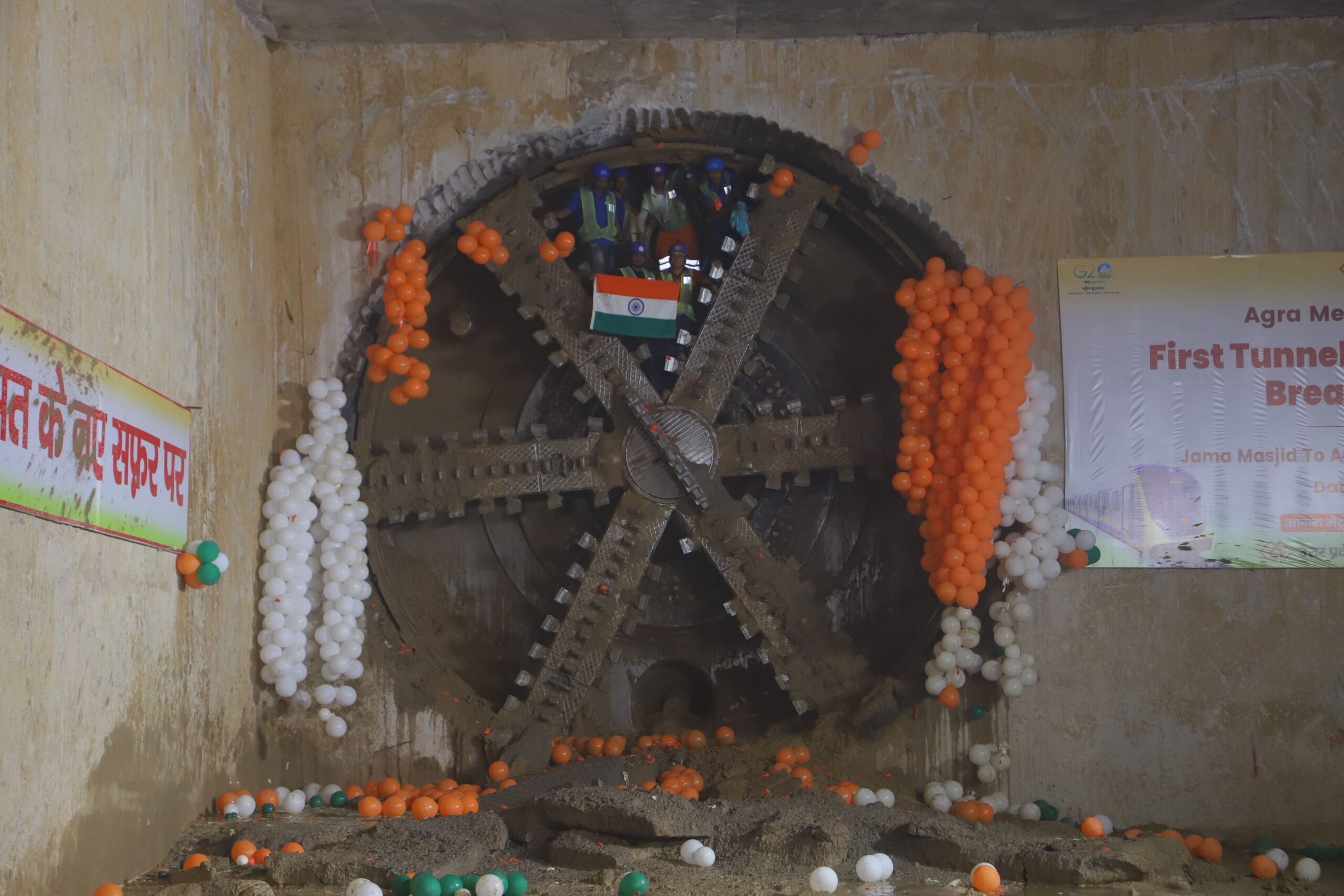
The Robbins EPB breaks through to much fanfare at Agra Metro.
New Delhi Metro: Machines Ramping Up
On February 27, 2023 the first of two 6.65 m diameter EPBs for the Delhi Metro (owner is Delhi Metro Rail Corporation) was completed in the Robbins Gurgaon, India facility. The mixed ground machine will bore a 3 km long tunnel through rock with some gravel, sand, silt and clay for contractor Afcons Infrastructure Ltd.
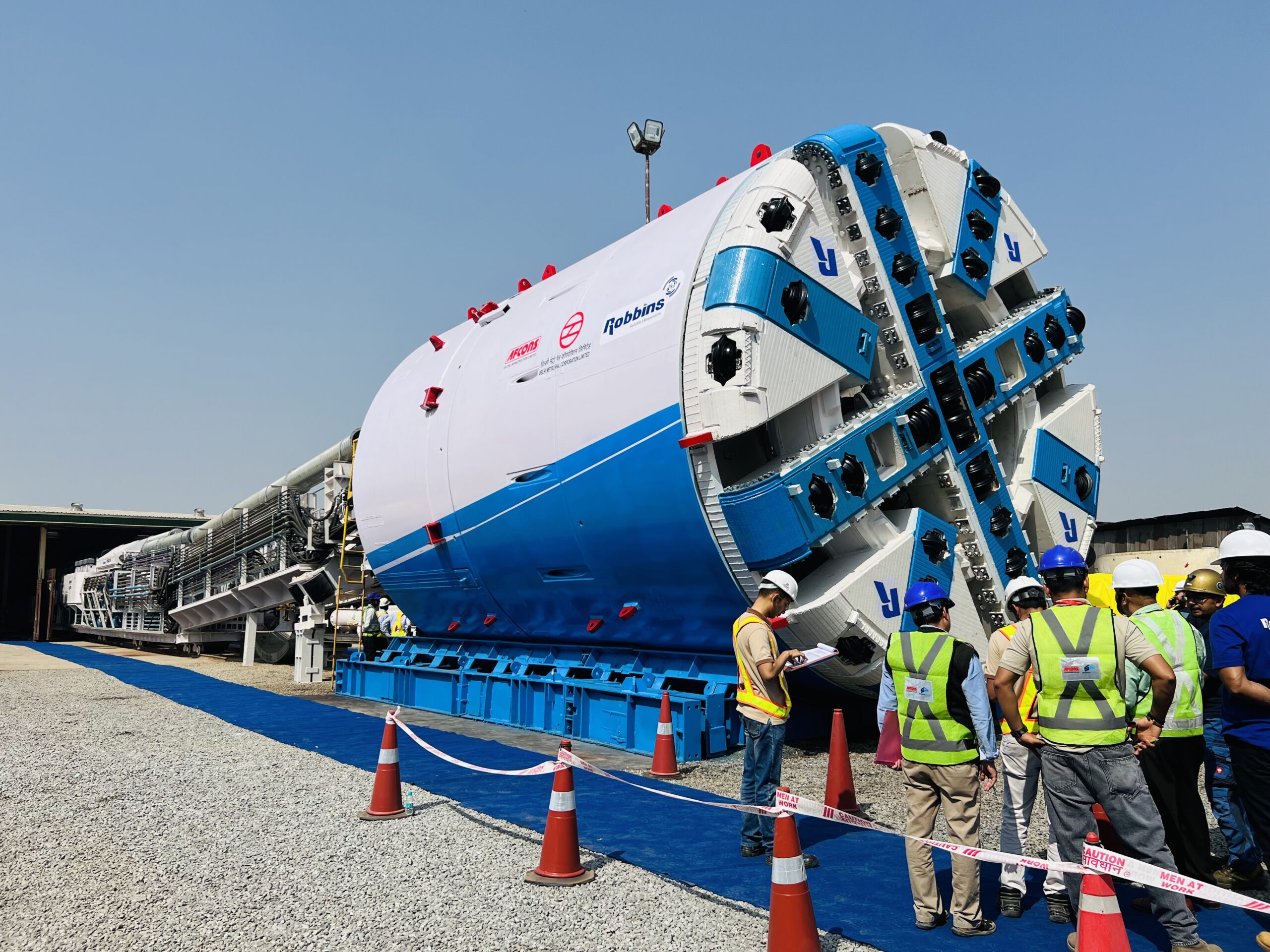
The first of two TBMs set to bore in mixed ground at Delhi Metro, during the factory acceptance in February 2023.
A second machine factory acceptance followed in April 2023. Both machines are scheduled to launch on parallel tunnels this summer.
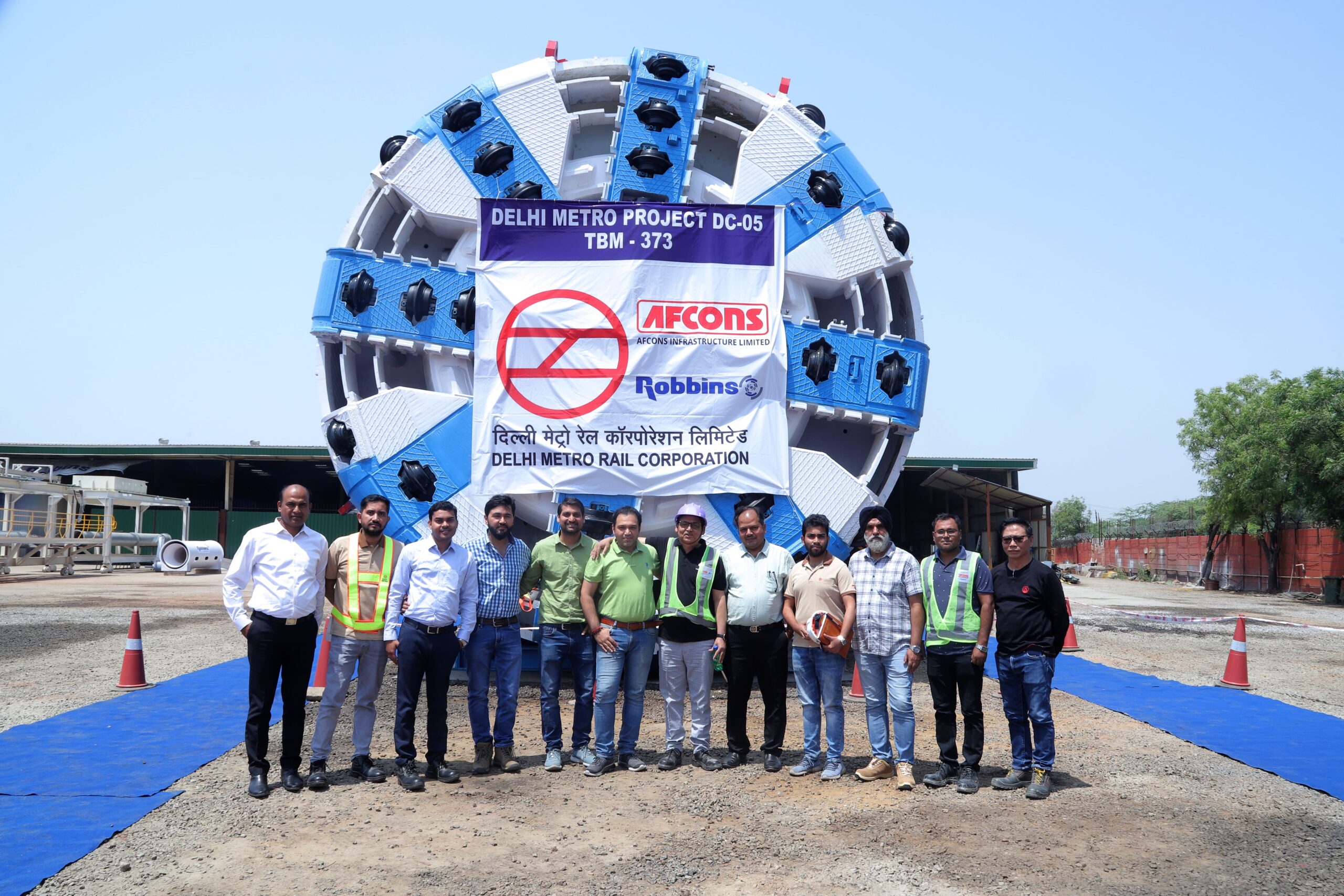
The second Delhi Metro EPB, designed to bore in mixed ground conditions.
Notice of Retraction and Apology
To all Visitors of our Site: I declare that our website contained information that was inaccurate, and in retrospect, was offensive and disrespectful to our longtime Customer and highly qualified construction Client, Obayashi Corporation of Japan, along with their Joint Venture (JV) Partners, Taisei Corporation and Kosei Corporation. The referenced Project Site name is Hiroshima Expressway 5 Shield Tunnel Project and the Robbins Technical Article titled https://www.robbinstbm.com/grout-or-not/, which states as if the JV selected the wrong type of TBM for the Hiroshima Project.
We retract the statements made in our article such as, “Contractors who are used to tunneling in soft ground may not realize that when using a Slurry TBM in rock, inspections must be frequent due to increased cutter consumption. We have seen this borne out on recent projects such as the Hiroshima Expressway Line 5 in Japan” because these statements were not based on facts and were incorrect. This statement reads as if the contractor did not review other optional TBM types, when in fact, the JV did indeed study all TBM types and methods to excavate this Express Tunnel.
There were additional incorrect statements made in the Article as follows:
- The same paragraph of the Article continues,”…, and they (contractor) were expecting up to 13 bar water pressure. This high pressure water zone was only in a small section of the overall tunnel length, about 5 percent.“
- The Article further states, “The contractor in Hiroshima had grouted off from the surface a planned safe zone in which to inspect the cutterhead without requiring a hyperbaric intervention, but this strategy did not go according to plan. The abrasive rock damaged the cutters and cutterhead before they could reach the safe zone, resulting in unplanned delays“.
- The same paragraph of the Article continues, “…grout off from the surface a planned safe zone…“.
The reason for choosing a Slurry type TBM was not solely based on the high water pressure but was also a result of the JV’s extensive review of all aspects of the tunnel requirements.
There was no plan to grout a “safe zone/safe haven” from the surface as other plans for cutter changes were in place and such plans have proven to be effective over numerous cutter change events.
Robbins commits to have more peer review and where a Client is involved, to have the Client review prior to presenting such data on our website.
超前钻探和预注浆需要知道的四件事
This blog is the first in a series called “Insights in Brief” that aims to boil down complex concepts into bite-sized facts and key points.
While probe drilling and pre-grouting have a long and successful history in drill and blast applications, their adoption for TBM technology has been more tenuous. Continuous probe drilling and pre-grouting was first pioneered in Norwegian hard rock D&B tunnels, where they have since been used with great success to detect ground conditions and consolidate weak rock ahead of the excavation face. If these methods have great potential to allow TBMs to excavate in difficult conditions, then there must be a knowledge gap. Here, we highlight four key things to know in order to get the most out of probe drilling and pre-grouting.
Number 1: There are always Pros and Cons
Much of the reluctance to adopt probing and grouting is based on a belief that the overall impact on the project schedule and TBM advance does not usually make up for the benefits provided. However, the benefits can be dramatic when compared to alternatives such as stuck TBMs, bypass tunnels, and other costly delays to the project schedule. The ability of a grout curtain to cut off or reduce water ingress and stabilize weak zones is unique to the method. This result has also been proven on hundreds of D&B projects over decades. When tunnel projects such as India’s Tapovan-Vishnugad Hydroelectric Project are considered, where a Double Shield TBM was brought to a halt following a massive influx of mud and water, the benefits seem clear.
There are other barriers towards industry acceptance besides time, however, and that is the perception of cost (both of course being related). In particular, in mountainous conditions or when tunneling downhill, probing may be the only practical approach towards risk mitigation, and pre-grouting may be the best possible option to control water inflows. When the cost of a stuck TBM is considered as the alternative, continuous probe drilling is looking pretty good.
Number 2: The Right Program and Machine Design can make all the Difference
Though the industry view of probing and pre-grouting tends toward the conservative, there are multiple ways to reduce impact to time and budgets while maximizing the benefits:
Plan and optimize the downtime for maintenance and cutter changes to minimize the downtime caused by probing and grouting
Proper scheduling may be one of the easiest ways to reduce downtime compared with current industry standards. To efficiently perform probe drilling and potentially pre-grouting in a TBM process, it is essential to plan the interventions and remove them from the critical path of the TBM process. Detailed planning should be done to coordinate the maintenance and cutter changing stops to the probing intervals. As an example a daily maintenance shift could be sufficient time to complete a grouting umbrella, with the correct TBM set up.
Analyze the drilling performance in detail
To get the most out of probe drilling and pre-grouting, detailed measurements of the advance rates of the probe drilling and the grouting pressure should be done. These measurements enable proper prediction of the ground ahead of the TBM. The drilling could be measured manually or automatically with Measurement While Drilling (MWD) systems, which are commonly used in D&B applications. The MWD system is used to analyze the rock in detail (hardness, water content, rock mass properties, etc.) and can be used to generate 3D-models of the rock mass in order to decide on the rock support or for documentation purposes.
Choose the right TBM Design
Ultimately, choosing the right TBM type can significantly cut time and cost. A customized machine, whether shielded or open-type, can be designed for accurate and continuous probe drilling. While it might seem that a shield machine would have limited drilling trajectories, machines like the Single Shield TBM for New York’s Delaware Aqueduct Repair offer 360-degree probe drilling paths using multiple drills, as well as probe drilling under pressure using down-the-hole hammers through ports sealed with ball joints. No matter what is needed, planning during the TBM design phase will most certainly cut downtime and costs later on.
Number 3: It has been Successful on Difficult TBM Projects
Though probe drilling and pre-grouting have not yet been used extensively on TBM projects, successful examples can be found worldwide. At Canada’s Seymour Capilano Water Filtration Tunnels, using two Robbins Main Beam TBMs, 100% probe drilling (with minimum overlap) and pre-excavation grouting were specified as part of the twin down drives of the Seymour Capilano tunnel project. This was due to the down gradient of the tunnel under high cover where there was a moderate risk of encountering significant inflows. Fortunately the actual groundwater inflows were much less than originally anticipated and so very limited pre-excavation grouting was required. Probe drilling was continuously carried out during TBM excavation, and while it had an impact on progress in the early days, once the crews became familiar with the equipment and procedures the work activity became efficient, and was successfully implemented with minimum impact to progress. Success stories like this are common in deep rock tunnels around the world.
Number 4: Knowledge Level is Key to Success
As with many developments in the tunneling industry, probe drilling and pre-grouting are seen from the view of risk sharing. Risk sharing could entail clearly defined specifications and payment provisions that allow for fair compensation to the contractor so they will not be reluctant to accept the approach, for example. Clear design and environmental criteria need to be established, so the execution of probe drilling and pre-excavation grouting involve the opinion of the contractor, the design engineer, and equipment supplier. In some cases, for example, the contractor may choose to accept moderate inflows that are manageable and do not impact excavation progress.
Training in the operations of probe drilling and pre-grouting will also necessarily lead to greater acceptance. While there is some training available at colleges that offer mining and tunneling degree programs, much of the training for such operations is necessarily hands-on and experience based. With an experienced workforce, the negatives of probe drilling and pre-grouting are greatly reduced. Such hands-on training is currently being provided by Robbins on several projects using a combination of classroom instruction and jobsite operation for crews who are not familiar with the methods.
Ultimately, the adoption of probe drilling and pre-grouting on TBMs is something that must be recognized as an overall benefit to the industry in difficult ground conditions. The technology is well developed in D&B tunneling, and it has been field-tested for decades. It is, in our opinion, the best method of accurately detecting and treating poor ground conditions in front of the TBM.
The Latest Updates: Records in Toronto, the News from Nepal, and More
Much like the face of a TBM, tunneling’s wheels of progress are always turning. Join us as we check in on projects across the globe—including a breakthrough in Japan, record setting progress in Canada, and a new project ramping up in Nepal.
Setting Citywide Records in Toronto
Exciting progress is being made deep below Lake Ontario. The 7.95 m (26.1 ft) Single Shield Robbins TBM boring the 3.5 km (2.2 mi) long Ashbridges Bay Outfall tunnel is seeing record setting progress for the City of Toronto, ON, Canada. The machine, operated by contractor Southland Holdings, has recently completed 30 rings in a single day, at 1.5 m (5 ft) per ring, equating to 45 m (148 ft). With this accomplishment, the machine and crew surpassed a previous best day of 21 rings at a project with similar specifications. The Ashbridges Bay Outfall is anticipated to be the largest wastewater outfall in Canada and will improve the city’s shoreline, beaches, and Lake Ontario’s water quality.
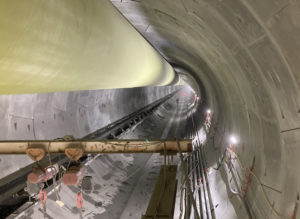
The record-setting machine at Ashbridges Bay Outfall placed 30 rings in one day.
A Third Set of Records in Esme, Turkey
If two sets of records weren’t enough, the 13.77 m (45.18 ft) diameter Robbins Crossover (XRE) TBM boring Turkey’s Esme-Salihli Railway Tunnel has just set another precedent. In July and August 2021, the speedy machine outdid its previous records in the size class of 13 to 14 m (43 to 46 ft), boring 167.4 m (549.2 ft) in one week and 651.6 m (2,138 ft) in one month. The rates are the fastest ever recorded for any TBM over 13 m (43 ft) in diameter! They even surpass those set over a decade ago at the Niagara Tunnel Project by a Robbins 14.4 m (47.5 ft) diameter Main Beam TBM. Check out the records here.
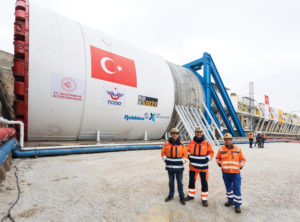
The Crossover TBM at the Esme-Salihli Railway Tunnel is now the world’s fastest TBM over 13 m (43 ft) in diameter.
Breakthrough at Tamagawa
In June, JV contractors Obayashi & Kumagai celebrated their final breakthrough at the Tamagawa HPP #2, Lot 2 project in Yamagata Prefecture, Japan. During the bore, the crew faced unpredictable soft ground conditions and other challenges. To surmount these issues, an airborne electromagnetic survey was conducted for predicting soft ground conditions ahead of the tunnel surface and tunnel face stability was improved by using forepiling. The project, completed with the use of a Robbins 4.5 m (14.7 ft) Main Beam TBM, will supply 14,600 kw of renewable power to the region.
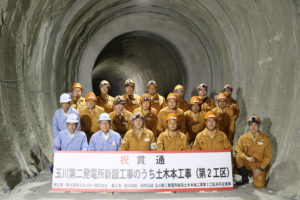
The Obayashi & Kumagai JV celebrate their final breakthrough at Tamagawa.
Double Shield to Bore Second Nepalese Tunnel
A record-setting 5.09 m (16.7 ft) Robbins Double Shield TBM is currently being rebuilt to tackle its second project for Nepal. The machine, which set multiple records and finished a year early at the Bheri Babai Diversion Multipurpose Project, has been chosen to bore the 13.3 km (8.2 mi) long Sunkoshi Marin Diversion Tunnel. Upon completion, the structure will divert part of the flow of the Sunkoshi River into the Bagmati river to irrigate farmland in the Tarai district. The project has been awarded to contractor China Overseas Engineering Co (COVEC), who will be bringing their expertise and experience from the Bheri Babai tunnel to this new endeavor.
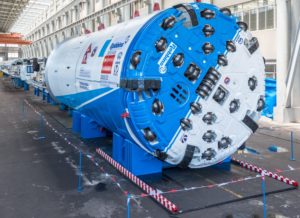
The veteran Robbins Double Shield will now be rebuilt to bore a second tunnel for Nepal.
Most Momentous: 2021 Global Project Updates
From China’s largest Crossover TBM launch to an epic 13.77 m diameter XRE that began boring recently in Esme, Turkey, we’ve compiled the year’s most momentous events thus far. Read on to find out about Robbins machines embarking on tunnels large and larger.
Twin Crossover TBMs for Chongqing
Two 6.91 m (22.6 ft) diameter XRE machines are currently boring sections of the Chongqing Metro Phase 2 in ground conditions ranging from weathered mixed granite to weathered pegmatite and adamellite. The twin machines are the first of their kind in China, and are part of a trend towards more geologically challenging tunnels in China. To date, the machines have achieved up to 365 m (1,197 ft) advance in one month, with rates expected to ramp up as the machines progress.
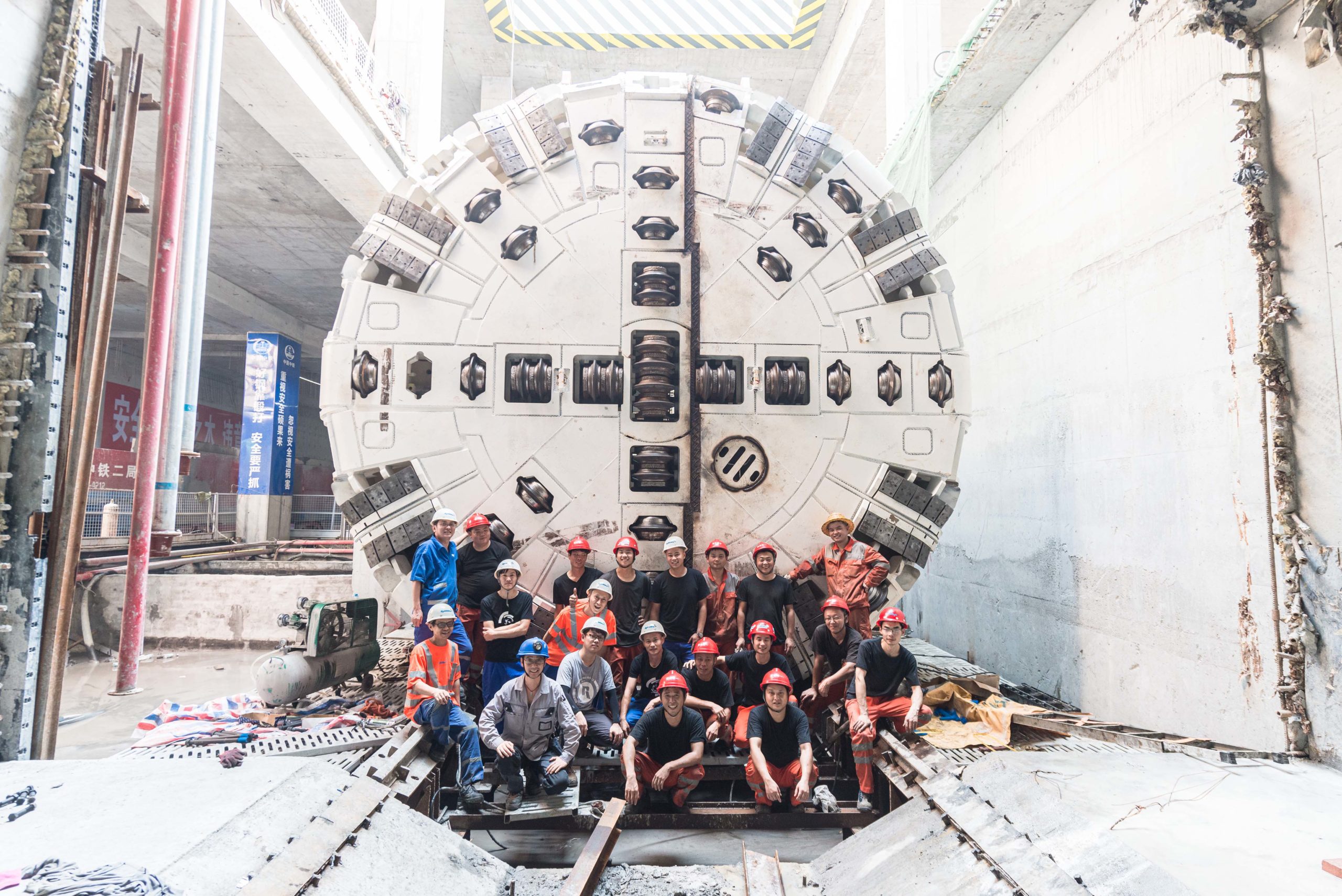
The team takes a moment to mark the assembly of one of two Robbins Crossover machines in Chongqing, China.
An Epic XRE Launch in Esme
In Esme, Turkey, a massive 13.77 m (45.2 ft) diameter Crossover XRE TBM began its bore for contractor Kolin Construction. Launched in late March 2021, the unique TBM is designed to tackle mixed ground conditions including sandstone, gravelstone, claystone and siltstone along the 3.05 km (1.9 mi) Esme-Salihli Railway Tunnel. The XRE can swiftly convert between hard rock mode using a belt conveyor and EPB mode using a screw conveyor, as both remain in place inside the machine.
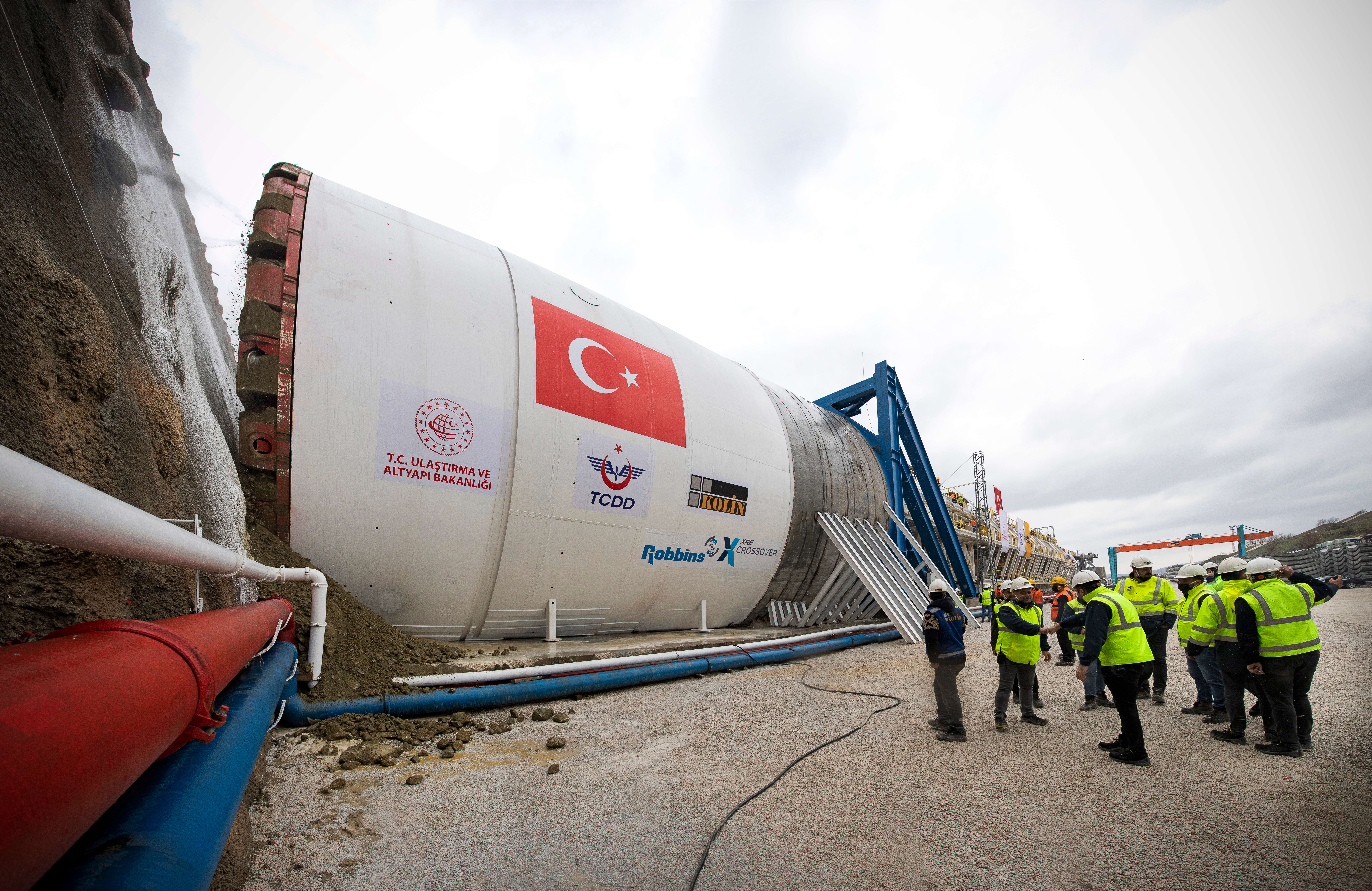
Launch of the 13.77 m diameter Robbins XRE TBM for Turkey’s Esme-Salihli Rail Tunnel.
Tunneling below Lake Ontario
A Robbins 7.95 m (26.1 ft) diameter Single Shield TBM launched recently on March 26th from an 85 m (280 ft) deep, 14 m (46 ft) diameter shaft. The machine, for the Ashbridges Bay Outfall with contractor Southland Holdings LLC in Toronto, ON, Canada has the task of boring a 3.5 km (2.2 mi) long tunnel below Lake Ontario. The completed tunnel will connect up to 50 in-lake risers to enable efficient dispersion of treated effluent over a wide area of the lake.
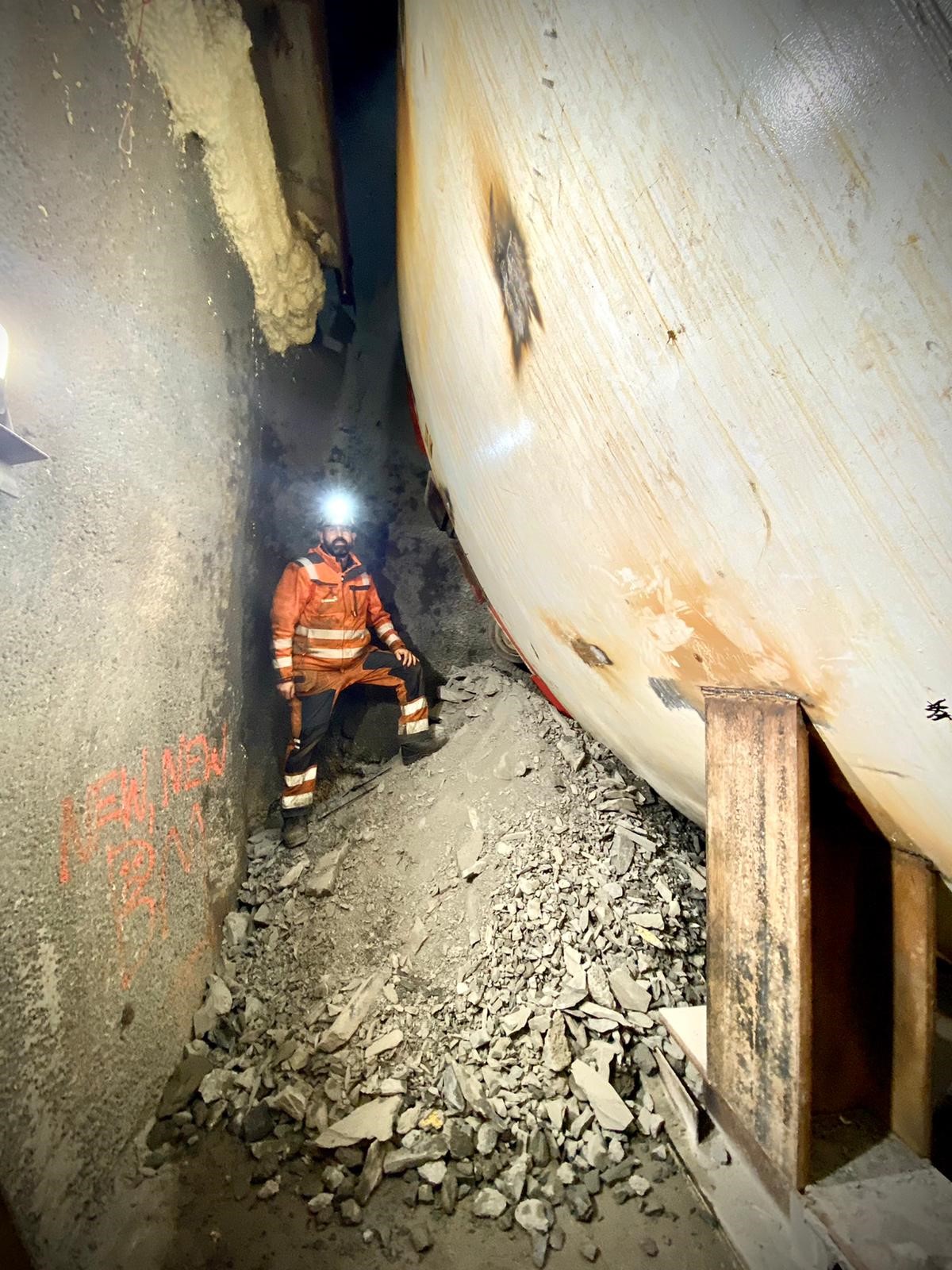
The Robbins Single Shield TBM for the Ashbridges Bay Outfall Tunnel launched on March 26, 2021. Photo: Alfredo Garrido
China’s Largest Crossover TBM
The largest ever Crossover (XRE) TBM in China launched in late March 2021 in Guangzhou for contractors Sichuan Jinshi Heavy Equipment Leasing Co., Ltd and CREC Bureau 2. Onsite First Time Assembly (OFTA) was utilized to build the 9.16 m (30 ft) diameter Robbins TBM, taking just four months from contract signing to machine launch. The hybrid machine is boring the 2.5 km (1.6 mi) long Pazhou Line Lot PZH-1 of the Pearl River Delta Intercity Railway Project, which will offer better commutes for Guangzhou residents traveling to and from University City.
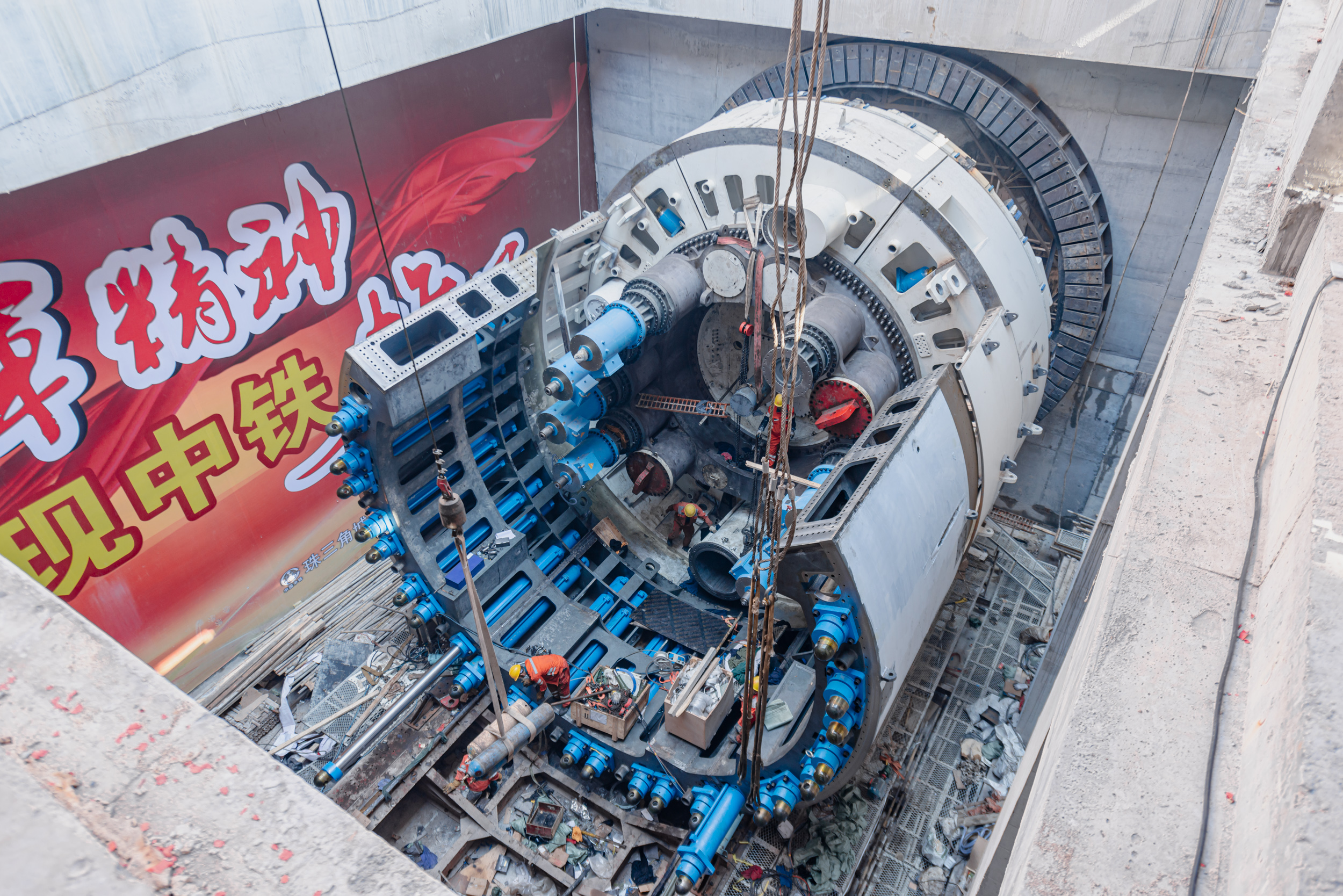
The Robbins Crossover XRE TBM at the Pearl River Delta site was assembled using Onsite First Time Assembly in just four months from contract signing.
Tunneling in Karst: Your Questions Answered
On November 18, 2020 we held a webinar on a unique recent project, France’s Galerie des Janots. Crews utilized a 3.5 m diameter Robbins Main Beam TBM to bore a 2.8 km long tunnel through limestone with karstic features, with some surprises: Two uncharted caverns up to 8,000 cubic meters per size in the bore path of the TBM. To find out how the crew overcame the challenges, watch the video here:
We held a question and answer session during our event that was not recorded and wanted to share some selected Q & A with you below.
Question and Answer Session
Q: What type of karst was predominant along the alignment?
A: The karst was a kind of weak limestone formation. Very soft with a tendency to get pasty – like chalk in water.
Q: Could another type of TBM have been used in the geological conditions (limestone with karst)?
A: It was a rather small diameter tunnel and the less structure you have with the machine, the better. A shielded machine with segments at this diameter can work – but when in bad rock and you need to do something, the shield can become an obstacle to access the rock. We think the Main Beam machine was the best option and provided full access to the tunnel walls and strata.
Q: Do you think an EPB or Slurry machine could have been used in this tunnel?
A: I do not think so. When in rock, you will struggle with EPB or Slurry TBMs–producing conditioned muck or building up a filter cake and pressurizing the chamber will be very difficult to make happen in these conditions. However, our Crossover type machines do provide for operation in various modes and can run from rock into soft material.
Q: One of the typical challenges faced with karst is high water ingress. Can an open face machine deal with that?
A: Here we did not have water ingress, and did not have karstic aquifers either, so it was sufficient to employ normal water pumping. An open machine provides full access to the tunnel walls and the face. So, you can inject and fight the water ingress better compared to a shielded machine.
Q: In the Middle East, we had a project that, during pilot tunnel drilling in front of the cutterhead, resulted in sudden inrush of water ,which led to flooding inside the TBM. What types of mitigations measures do you recommend to overcome flooding risk?
A: A TBM can be furnished with doors and chutes at the relevant points to stop water ingress. A very appropriate tool is a so-called Guillotine Door, which is assembled to the muck chute above the TBM conveyor and allows for quick closing. Also, TBM conveyors can be furnished with a water-tight plug door, which can seal the machine when pulling back the conveyor. For sure, submersible pumps are needed, and to stop the water ingress, injection grouting should be used.
Q: What is BEAM Technology and was it able to successfully predict any real detected cavities before the TBM excavation?
A: BEAM Technology stands for Bore-tunneling Electrical Ahead Monitoring. BEAM is a ground prediction technique using focused electricity-induced polarization to detect anomalies ahead of the TBM. Yes, they were able to predict a cavity using BEAM on this TBM, see drawing below courtesy of Geo Exploration Technologies. The red spot spot in the colored band clearly indicates the location of the cavity, and the picture verifies that it was found at that location.
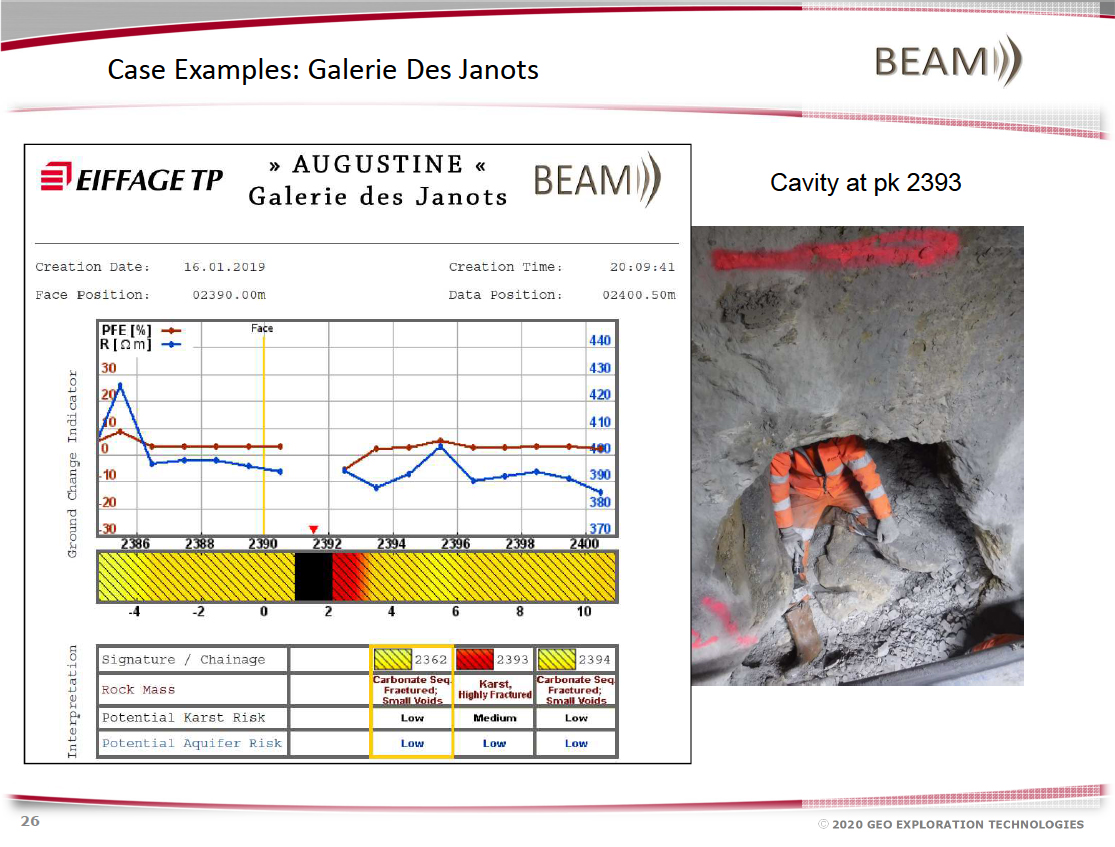
Detection of a cavity using BEAM at Galerie des Janots.
Q: What type of material did you use to fill the cavities?
A: It was mainly concrete reinforced with steel mesh and wood structures.
Q: How did they move past the first cavern and did ground support change during tunneling?
A: To cross the cavern space, crews erected a 4 m high wall of concrete so the TBM would have something to grip against (see picture below). The TBM was started up and was able to successfully navigate out of the cavern in eight strokes without significant downtime to the operation. Shotcrete was also employed – as long as necessary. Rock conditions changed often in this tunnel.
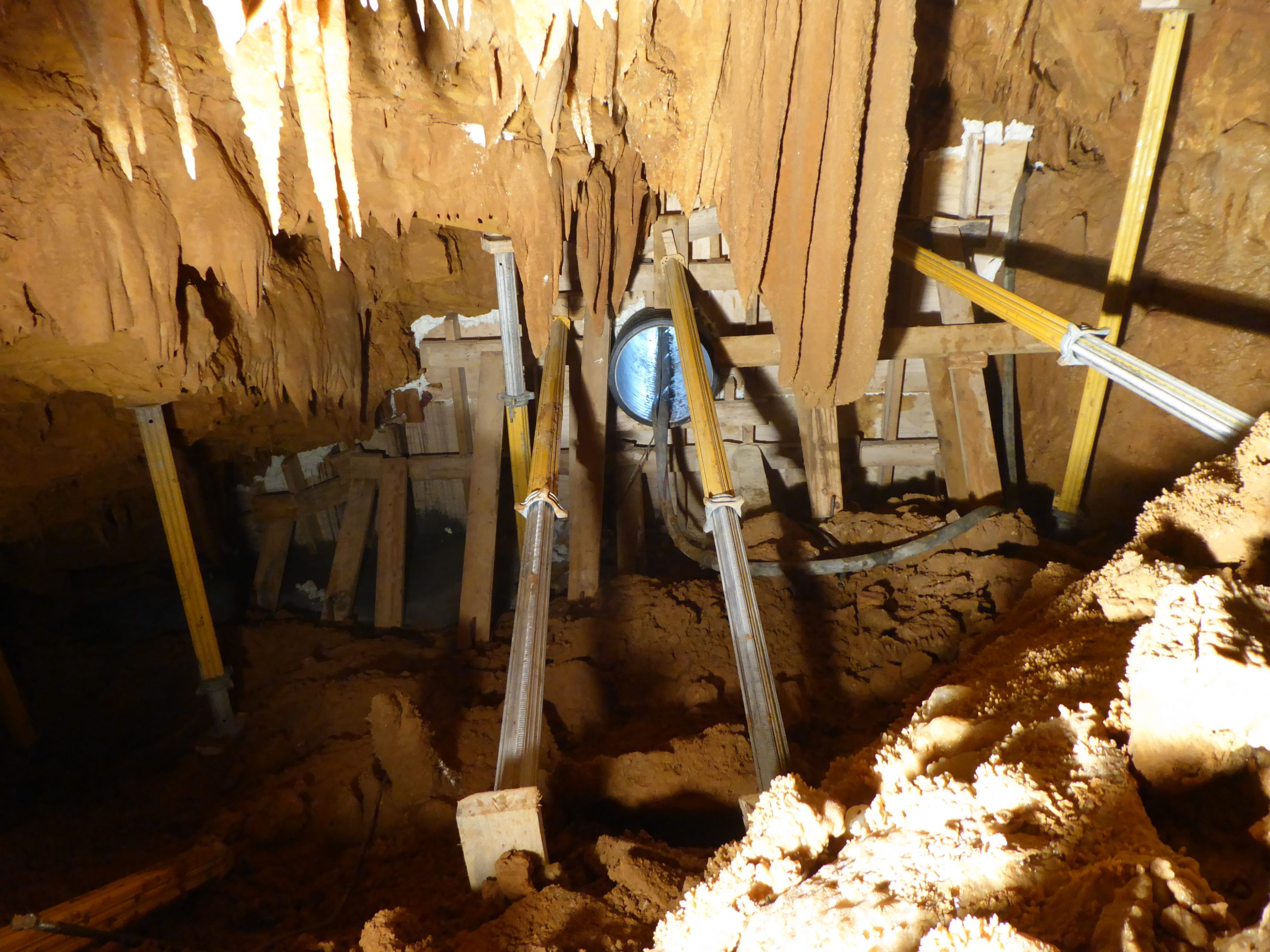
Reinforcement of the first cavern at Galerie des Janots.
The Next Push: Robbins TBMs on the Move Around the Globe
Robbins machines continue to advance in 2020, with essential projects ongoing and starting up the world over. From a proven Main Beam starting its fifth tunnel in Switzerland to a triumphant small diameter breakthrough in Norway to continued Crossover success in India, we’ve got all the tunneling highlights below.
ASSEMBLY UNDERWAY IN TORONTO
Assembly is underway on a Single Shield TBM for the Ashbridges Bay Treatment Outfall in Toronto, ON, Canada. The 7.95 m (26.0 ft) diameter machine and Robbins continuous conveyor will bore a tunnel to replace a 70 yr old existing outfall. The video below shows the machine acceptance in Mexico before being shipped to Canada. Due to coronavirus protocol, this was the first all-remote machine acceptance that Robbins has conducted.
SMALL DIAMETER TRIUMPH IN NORWAY
On June 16, 2020, crews wrapped up tunneling at the Salvasskardelva Hydroelectric Power Project (HEPP), located far above the Arctic Circle at 68.7 degrees north latitude near Bardufoss, Norway. The site may well be the world’s northernmost TBM-driven tunnel. The 2.8 m (9.2 ft) diameter specialized Main Beam TBM known as “Snøhvit”, or “Snow White”, was provided to contractor Norsk Grønnkraft for use on several of their hydroelectric tunnels. A continuous conveyor was also provided. The small hydro tunnels featured moderate to steep positive gradients up to 25 percent. The TBM was able to achieve rates of up to 44 m (144 ft) in 24 hours.

A small diameter Robbins Main Beam TBM broke through in June 2020 in Northern Norway.
PROVEN MACHINE RAMPS UP FOR 5TH BORE
In Oberwalden, Switzerland a 6.50 m (21.3 ft) diameter Robbins Main Beam TBM, originally built in 1993, is ramping up to begin boring in December 2020. The machine, rebuilt by Swiss contractor Marti, will bore the 6.4 km (4.0 mi) long Sarnen Stormwater Relief Tunnel through hard rock. As the bore proceeds, wire mesh, shotcrete, and invert segments will be installed.
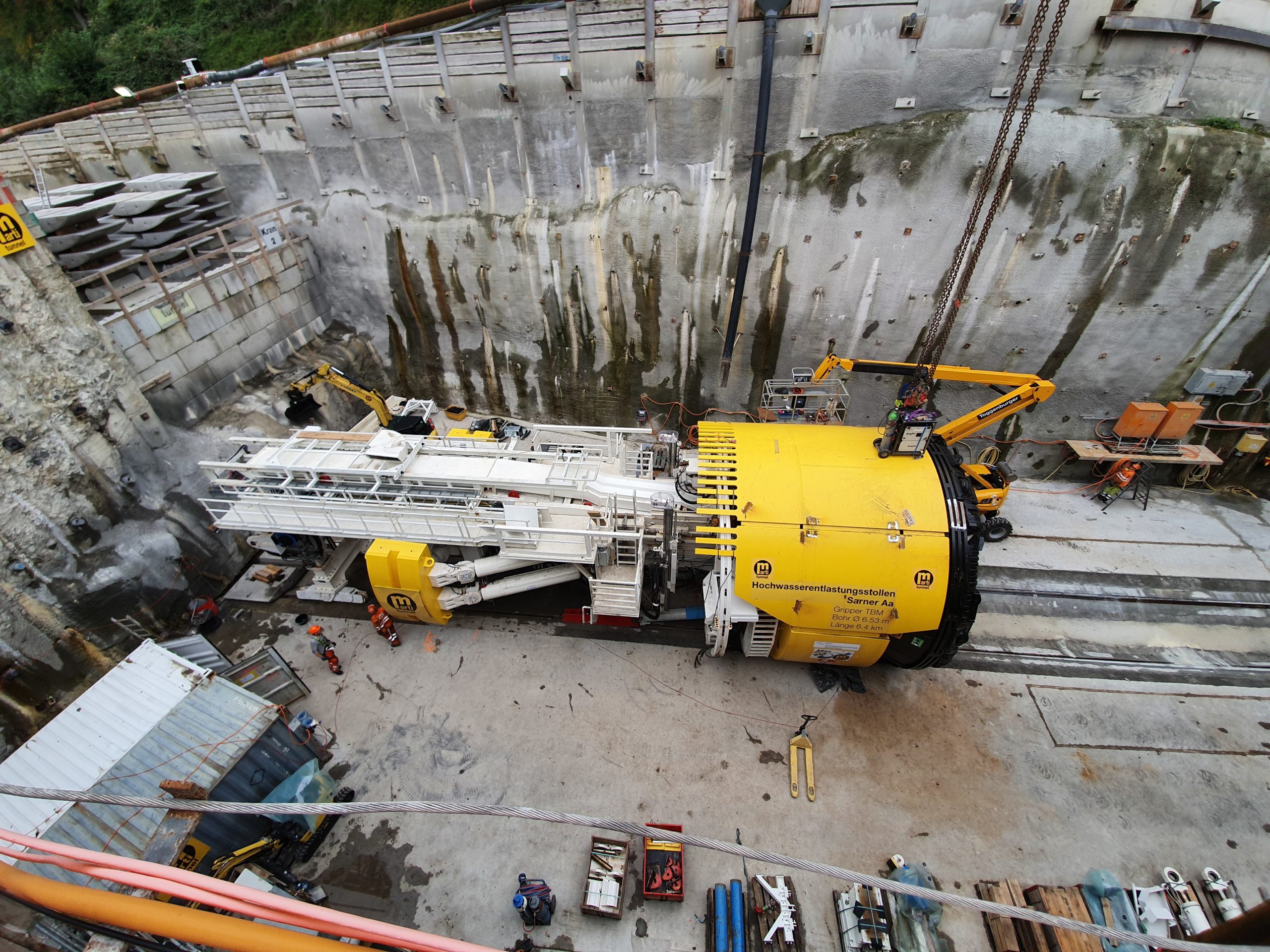
The 6.50 m Robbins Main Beam TBM will begin boring in December 2020 in Oberwalden, Switzerland.
UNIQUE CONVEYOR SYSTEM FOR NEUTRINO FACILITY
In Lead, South Dakota, a unique Robbins conveyor system is gearing up to begin hauling muck. The conveyor system will be used to build the Long Baseline Neutrino Facility (LBNF) for Fermilab. Contractor Kiewit will renovate a disused gold mine into a world-class neutrino research facility. Two caverns will be excavated by drill & blast and roadheader deep below the surface. Rock will be transported by cable hoist up a 1.5 km (0.9 mi) deep mine shaft to a rock crusher at the surface using much of the original but refurbished mining equipment, and from there will be transported via conveyors. The Robbins conveyor systems are designed for the unique application, and include the longest overland conveyor Robbins has ever provided (550 m/1,800 ft), which travels over a main road and city park and near a residential area.
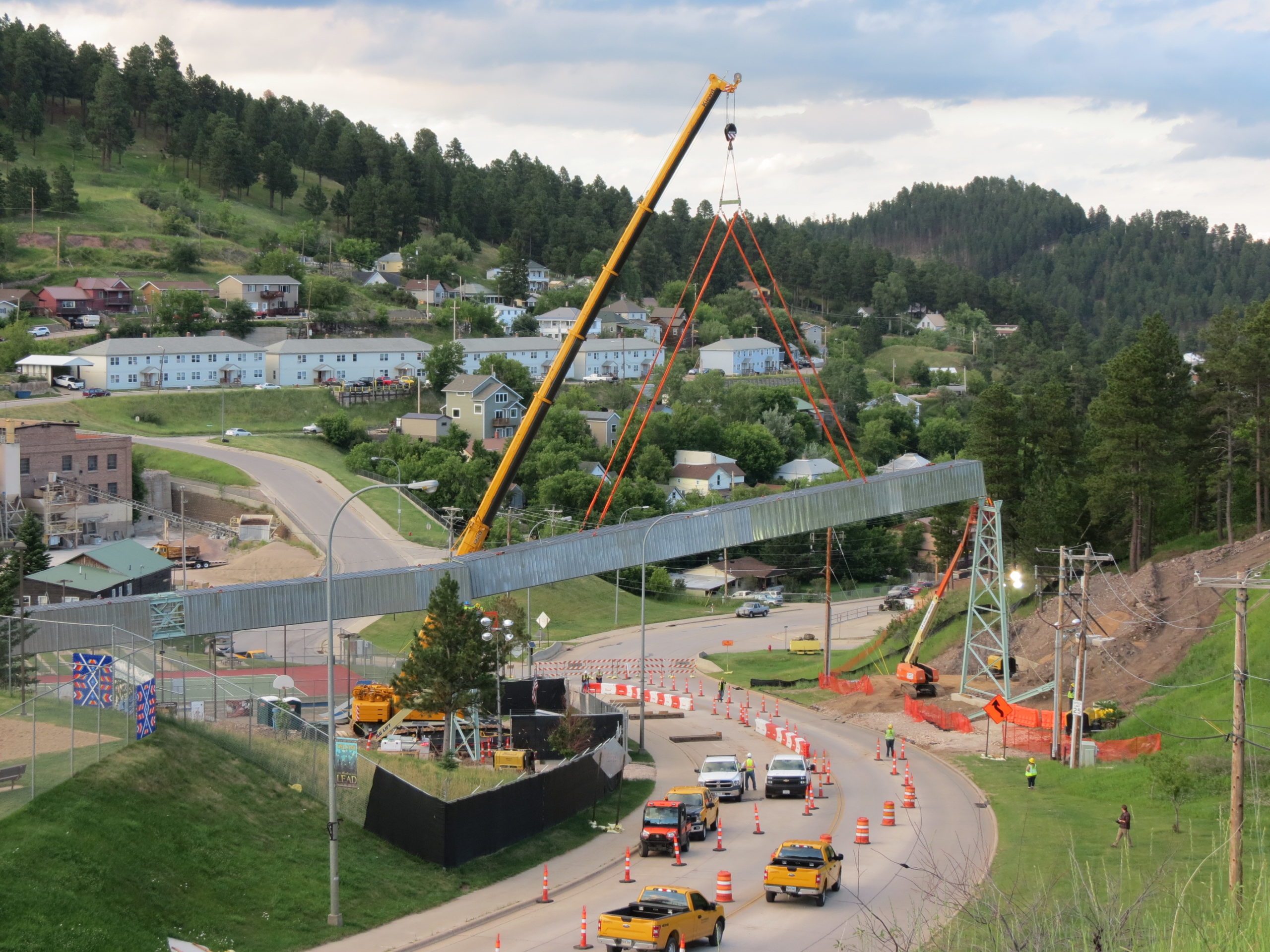
Crews install the completely enclosed box truss for the overland conveyor, which will traverse a roadway and other features.
CROSSOVERS CONTINUE BELOW MUMBAI
Tunneling continues on the Mumbai Metro Line 3, where two 6.65 m (21.8 ft) diameter Crossover XRE TBMs are on their third drives for the L&T/STEC JV. TBM 1 has bored 2,178 m (7,146 ft) with another 765 m (2,500 ft) left to bore. TBM 2 has bored 2,352 m (7,716 ft) with another 592 m (1,942 ft) left to bore, and is scheduled to bore fourth drive later this year. Two 6.65 m (21.8 ft) Robbins Slurry TBMs are also boring for the Dogus-Soma JV with one machine starting its second drive after boring 2,181 m (7,155 ft), and the other being reading for its second drive after boring 2,100 m (6,890 ft).
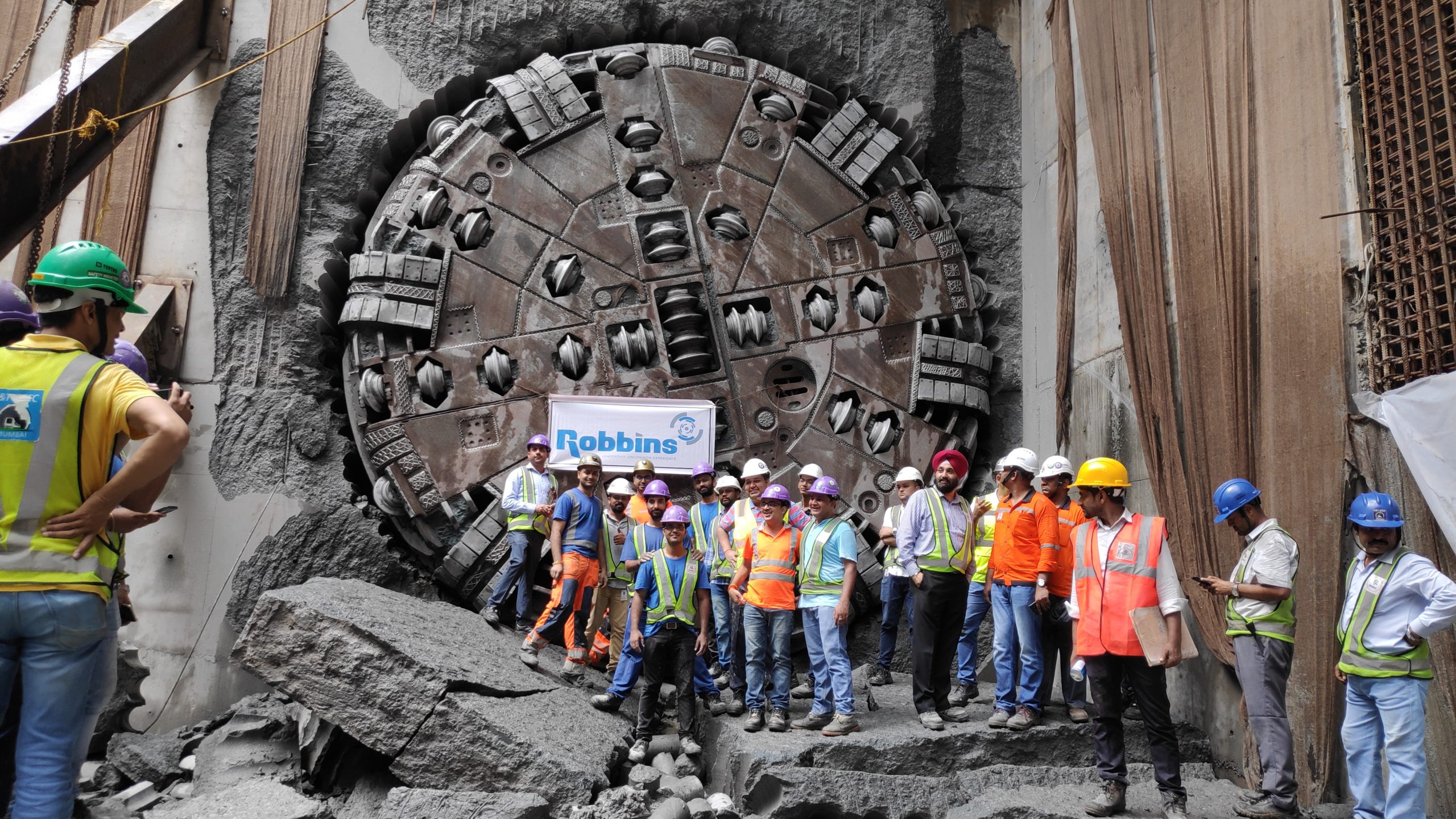
One of two 6.65 m (21.8 ft) Robbins Crossover XRE TBMs at India’s Mumbai Metro during a recent breakthrough.
On the Move: Robbins TBMs Around the World
At any given time Robbins TBMs are operating in dozens of countries around the world at all project stages. Thus far, 2020 has been no exception to the rule: From an icy visit to the world’s northernmost TBM to breakthroughs across the U.S. to a vast hydropower project on the verge of completion in China, we’ve got the latest updates from Robbins tunnels around the globe.
TBM Tunneling Above the Arctic Circle
Robbins engineers paid a visit to what is likely the northernmost TBM ever to operate in the world, at the Salvasskardelva HEPP near Bardufoss, Norway, 68.7 degrees north latitude. Robbins personnel and the contractor, Norsk Grønnkraft , have been braving frigid winter temperatures, ice and snow to excavate the 2.8 km long tunnel with a Main Beam machine at an upward gradient of 5.8 percent. As of the first quarter of 2020 they are nearly two thirds complete. Once breakthrough occurs the machine will be moved to bore a second tunnel 1.3 km long.
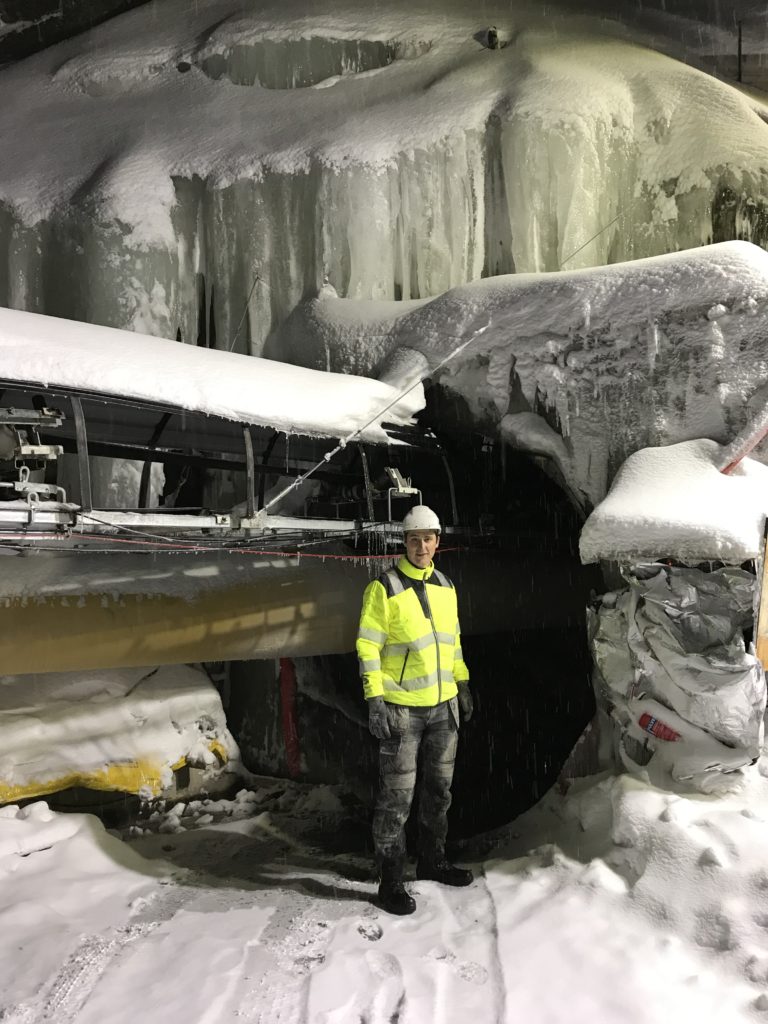
Sindre Log of Robbins Norway visits the wintry jobsite at Salvasskardelva HEPP, possibly the northernmost TBM operation ever.
A Trio of U.S. Tunneling Breakthroughs
Meanwhile in the U.S. multiple machines ranging from 2.2 to 6.5 m in diameter broke through. First up is the Deer Creek Interceptor using a 6.5 m Main Beam TBM and continuous conveyor. The machine holed through on January 29, completing a 6.3 km long tunnel below St. Louis, MO for contractor SAK. Watch this great video from the owner, MSD Project Clear, below.
Also in January, the Turkey Creek Interceptor finished up: a project using a 3.0 m diameter Robbins Double Shield TBM to bore three short drives below Kansas City, MO. Contractor Radmacher Brothers bored a total of 220 m with the machine. Check out the video of the final breakthrough, and image of its first breakthrough several months earlier.
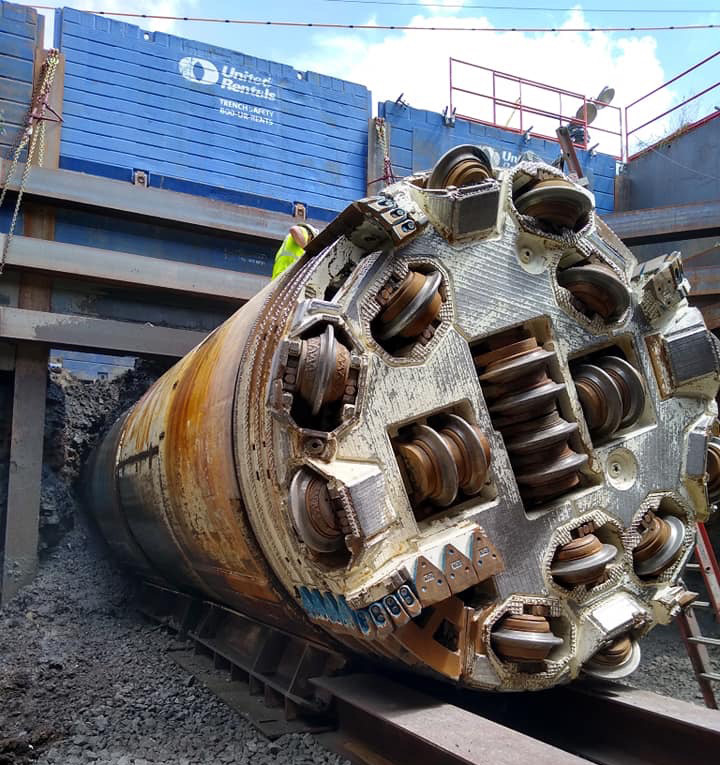
The Turkey Creek TBM, a Robbins Double Shield, during its first breakthrough in Kansas City, MO, USA.
Lastly, in San Antonio, TX a 2.2 m diameter Robbins Double Shield TBM achieved a breakthrough at the SAWS Central Water Integration Pipeline, Segment 5-1. The tunnel, for owner San Antonio Water System, was excavated by contractor Atkinson.
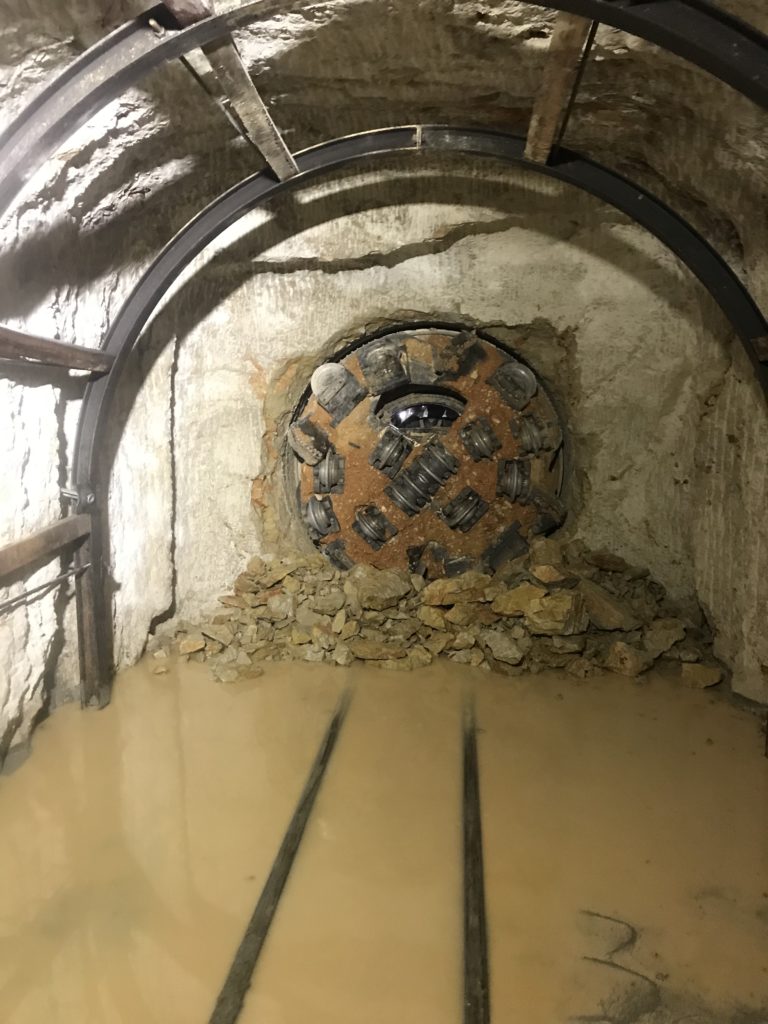
The 2.2 m Robbins Double Shield TBM for the SAWS Central Water Integration Pipeline in Texas.
A Massive Project Nears Completion in China
Two of three long-running Double Shield TBMs have completed their epic drives at China’s Great Hydro Network in Shanxi Province in recent months. The Great Hydro Network sprawls thousands of kilometers and is a feat of engineering. The Robbins machines at Tunnel 2 and Tunnel 4 bored from 15 to 23+ km in length. The machines overcame fault zones, water inflows and karst cavities to forge fast advance rates up to 865 m in one month.
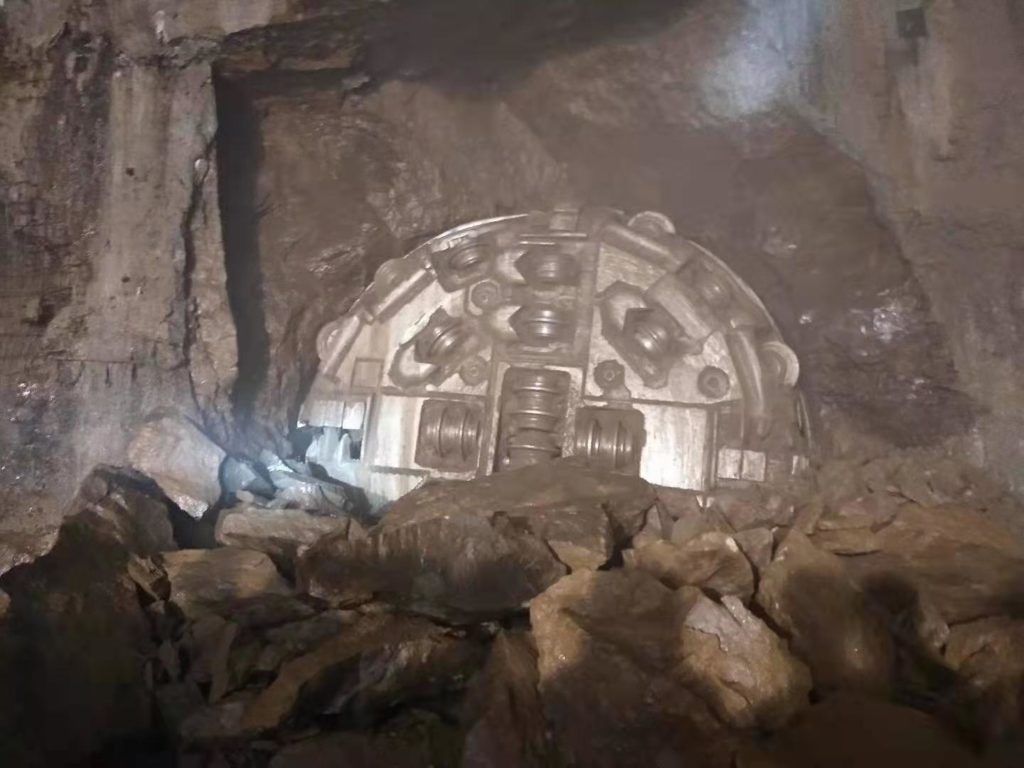
The Robbins Double Shield TBM at Tunnel 4 of the Great Hydro Network.
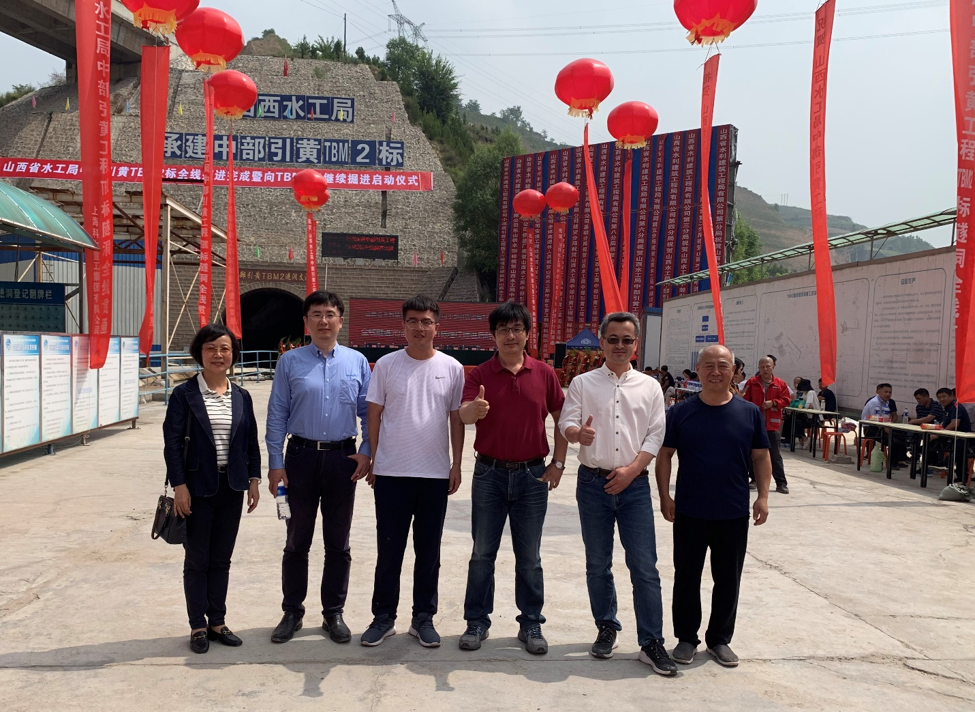
Officials celebrate the breakthrough of the Robbins Double Shield TBM at Tunnel 2 of the Great Hydro Network.
What it’s Like to Live at a Jobsite for a Year (or More): An Interview
Debbie Swival, Robbins Field Service Support, is no stranger to tunnel sites. Over her last 12 years at The Robbins Company she has worked on TBMs around the world, from the San Francisco Central Subway to the Moglicë Headrace Tunnel in a remote area of Albania to Turkey’s Bahce-Nurdag High Speed Railway and more. But her longest stay was in Newburgh, NY, USA for the Delaware Aqueduct Repair tunnel.
Swival remained on the jobsite from November 2017 until the TBM’s breakthrough in August 2019—a duration of 21 months. Her role in assisting the crew and troubleshooting issues was integral to the project’s success.
Boring Below the Hudson
The 6.8 m (22.3 ft) diameter Robbins Single Shield TBM for JV contractor Kiewit-Shea Constructors (KSC) bored a total of 3,794 m (12,448 ft) over 582 days with instantaneous penetration rates of 6 m (20 ft) per hour. The unique machine was designed to statically hold up to 20 bar pressure as it bored below the Hudson River to repair a section of the Delaware Aqueduct, the world’s longest continuous tunnel (137 km/85 mi long).
The New York City Department of Environmental Protection (NYCDEP), project owner, discovered that a section of the aqueduct below the Hudson River was leaking up to 75 million liters (20 million gallons) of water per day. On average the aqueduct—built in the 1930s and 1940s—supplies about 50 percent of the water consumed by 8.6 million residents of New York City and an additional 1 million residents in four counties north of the City. A swift repair of the tunnel section was essential.
The tunnel depth—ranging from nearly 270 m (900 ft) deep where the TBM was launched in Newburgh, New York to over 180 m (600 ft) deep at the exit shaft—the water volume, and pressure were all challenges. Probe drilling was mandatory ahead of the TBM and required the use of down-the-hole water hammers for accurate boring under pressure.
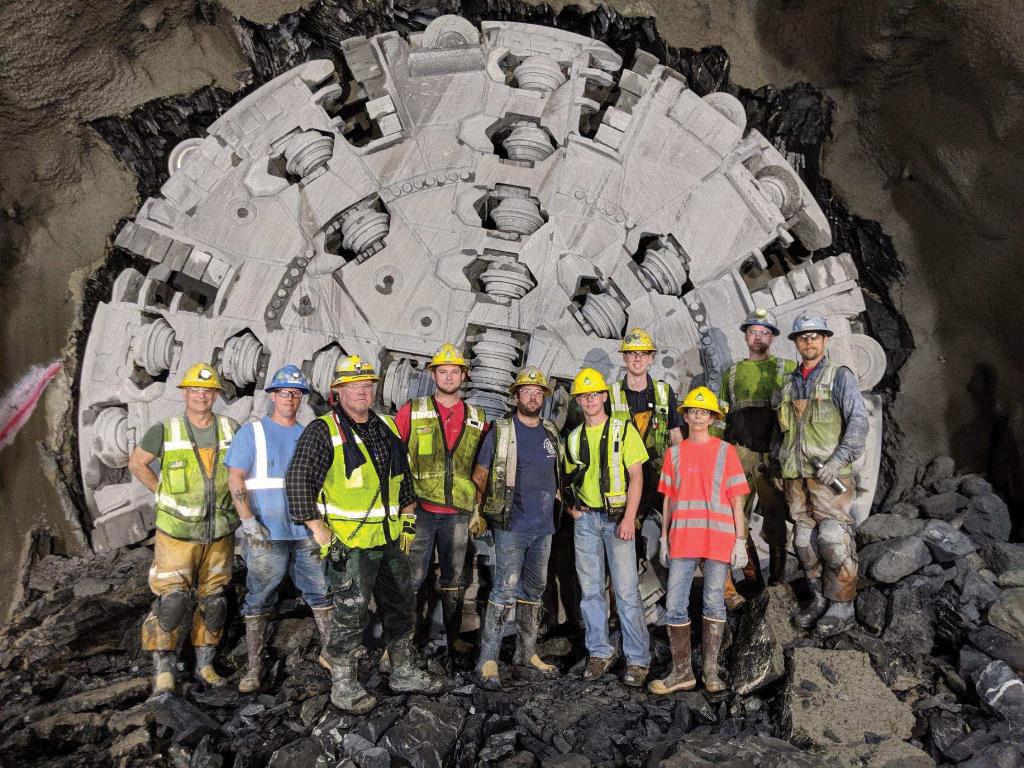
Debbie Swival, third from right, of Robbins Field Service, stayed on the Delaware Aqueduct Repair jobsite for a total of 21 months to keep the machine running smoothly.
What was it like to be at the jobsite for 21 months?
Swival: Being on site for that long was a fantastic experience. I typically stay on a jobsite for 6 to 8 weeks so I do not see the machine in full production. Staying for the boring of the length of tunnel allowed me to see the way that the machine is actually used, as opposed to the theoretical understanding of how different operations should be done. This has given me new insight for programming the machines to better meet the customer’s needs.
Being there for that long also gave the opportunity to create a strong working relationship with the customer. I was part of the team, with everyone working together to get the job done safely and successfully.
What were your main roles at the jobsite?
Swival: Initially I worked with the crew on the machine’s electrical systems and PLC (Programmable Logic Controller) programming changes. Other members of Robbins Field Service conducted training on hydraulics and machine operation. We had three operators at the jobsite who needed training, so I also spent time afterwards reinforcing that training they received. Much of it was on-the-job style training.
As the job continued my role shifted to supporting the machine for any issues that came up. I assisted with troubleshooting hydraulic and mechanical issues as well as continuing to work with the electricians for any problems that arose there. I worked with the customer to implement changes that they requested to the PLC program and to the HMI (Human Machine Interface) screens. I also assisted the customer with interfacing with Robbins engineering to obtain information that they needed.
What was a typical day at the jobsite like for you?
Swival: My typical day started with a 7:30 am meeting with the engineers and supervisors to go over the plan for the day and address any technical issues that had occurred since the previous day. At 8:00 am, a quick safety meeting with the crew, then head to the cage where we all got to be up close and personal during the 6-1/2 minute ride down the shaft. Once at the bottom we got on the mantrip to ride in to the machine. Near the end of the drive it took around 20 minutes to get to the TBM.
Once in the machine, it was time to tie in with the night shift for information on what had happened during the night and where they were in the mining process. At that point it was time to start troubleshooting any problems that had occurred. If all was well I went through and checked the machine for any signs of something getting ready to fail such as wear marks on hoses or cables, low tank levels, loose mounting on sensors and other things that could be fixed before they broke and caused an issue. I spoke with the mechanics and operators to see if there was anything they needed assistance with and also got feedback from them on what they liked as well as what could have been done differently to make their job more efficient.
Conditions in the tunnel were as you would expect – loud and dirty, although there were only a few times when dust was an issue and respirators needed to be worn. The crew often said it was hot in the tunnel, but I love the heat so I didn’t really notice it. We ate lunch on the machine. Since we did not leave the tunnel until the next shift came in, something that is normally overlooked is the need for the crew to relieve themselves. On this machine there was a really nice toilet that was kept cleaned, which made life there so much better! Around 4:30 pm “Mantrip coming in!” was announced over the mine phones as the next shift started their way in to relieve us. We got back to the surface a little after 5 pm and it was so nice to be back in the fresh air!
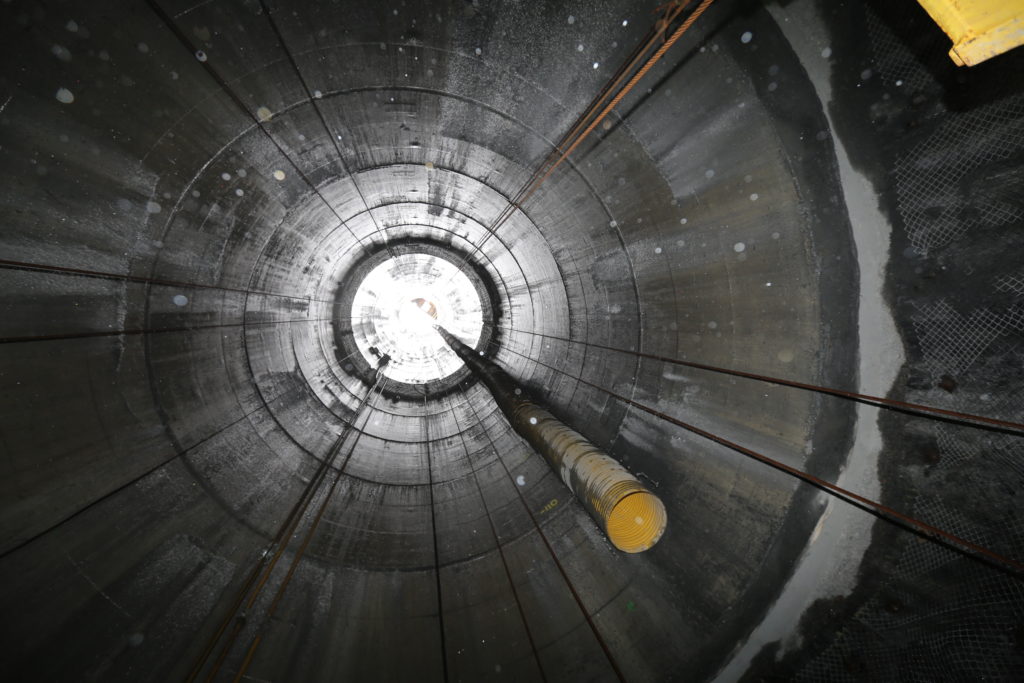
A view looking up from the bottom of the 270 m (900 ft) deep launch shaft in Newburgh. Photo: NYCDEP (www.nyc.gov/dep)
How important are knowledgeable field service personnel for the success of a project?
Swival: It’s absolutely imperative to have knowledgeable personnel. At the Delaware Aqueduct site they had me there because I knew the equipment well and could solve problems quickly. For example, it’s beneficial to have a PLC person on site because it’s a specialized piece of equipment. Although after commissioning there are not many problems with the PLC, when there is an issue it requires the code to be changed. Some PLC hardware failures or changes can also require that the program is modified. When an electrical or hydraulic issue occurs on the machine, I can use the program as a troubleshooting tool, find out what physical device isn’t working then describe the problem to the crew and educate them on how to fix it. This shortens downtime from 12 hours for a crew without PLC personnel on site, to around two hours.
What are some other examples of challenges that you were able to overcome at the site?
Swival: I helped to optimize the boring parameters, such as reducing thrust pressure, adjusting ring build procedures, and fine-tuning articulation cylinder pressure to avoid downtime and keep the machine moving. There was a section of the tunnel where the rock transitioned from shale to granite, and the difference in rock strength meant we had to set new limits for the thrust pressure to extend the life of the disc cutters.
There was an issue with the segment unloaders where the forward unloader was in the lowered position and the rear unloader was raised. The setup didn’t provide any clearance for when the train moved out. Typical sensors were not able to be mounted in the location. I worked with the mechanical team to find a solution for sensing the positions of the unloaders and prevent this from happening in the future. Lights were added to give a visual indication to the operator of the fully raised and lowered positions, and I changed the logic to incorporate the modifications. Those are just a few examples of what I helped with.
What is your favorite memory from the project?
Swival: It was amazing to be able to climb through the hole in the cutterhead and stand in front of the machine when it broke through. The support from everybody throughout the project was incredible. Everyone worked together, and the level of community on the job was exceptional. It was simply a great place to work.
Video courtesy of NYCDEP (www.nyc.gov/dep).
For more on the unique tunneling operation at the Delaware Aqueduct Repair, check out these resources:
White paper: https://www.robbinstbm.com/managing-high-water-inflows-2/
Press release: https://www.robbinstbm.com/delaware-aqueduct-repair-breakthrough/