Author: Barrie Willis
Rescuing and Refurbishing TBMs: Experiences at Bangalore’s Namma Metro
In this blog, Robbins and guest blogger Barrie Willis, Manager Tunneling & Civil for iPS, share their experiences rebuilding and relaunching TBMs in the field.
TBM maintenance: it’s one of the most important factors predicting project success, but it is often glossed over. Experience shows, however, that maintenance plays just as much a part in the excavation rates as the proper TBM design. Regular maintenance can keep future rebuild costs low and keep equipment efficiency high while maximizing advance rates.
Conversely, a lack of maintenance, improper operation, and/or severe ground conditions can result in undue wear and slow advance rates. In a worst case scenario, it can even require rescuing and refurbishing a TBM. Such a case occurred at Bangalore, India’s Namma Metro, where several TBMs required recovery and refurbishment after operating in abrasive ground. Teams from both Robbins and iPS were called in to evaluate and rescue TBMs on separate sections of the tunnel.
The Robbins Experience
Two European-manufactured EPB TBMs “Krishna” and “Kaveri” were launched from the South Ramp station at the Namma Metro project in October and November of 2012, and were slated to bore three sections of metro tunnel each, totaling 1,550 m. While the first 400 m long drive from South Ramp to City Market station went well, the TBMs encountered severe ground conditions on the second, 432 m long drive from City Market to Chickpet Station.
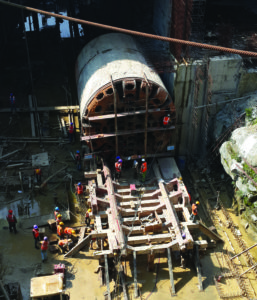
Robbins refurbished the two EPBs but did not change any of the machine design features.
Difficult Conditions
The drives took 12 and 22 months, respectively, and were hampered by a mixed face comprising hard granite and soil with high groundwater levels. Tunneling took place near fragile, historic building foundations in some cases hundreds of years old. The TBMs in this section encountered large boulders as well as reinforced blocks of concrete that seriously damaged the TBM cutterheads. These challenges required regular cutterhead interventions but at the same time there was an inability to grout unstable areas from the surface due to congested residential areas.
It was at this point that the contractor, along with owner Bangalore Metro Rail Corporation Ltd. (BMRCL), approached Robbins and asked them to take over the operations of the TBMs—the critical path tunnels needed to be brought back up to speed. The last 750 m drive between Chickpet and Majestic stations was all that stood in the way of opening a substantial section of Namma Metro’s Phase 1.
Robbins Signs On
After obtaining agreement from the project owner and the contractor, Robbins took over the responsibility for all aspects of the underground operations. A team of over 60 staff including TBM operators, TBM technicians, ring builders, a grouting team, and others began work. Robbins was also responsible for running surface installations and equipment such as the grout batching plant, gantry cranes and power supply. The contractor provided a team of people including surveyors, QC engineers, and loco operators who reported directly to the Robbins site management team.
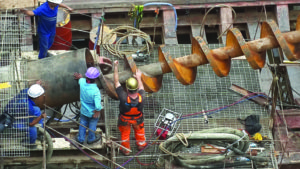
Robbins Field Service guided the refurbishment and assembly of the two competitor-manufactured EPBs.
The Robbins crew carried out refurbishment of the two TBMs, keeping the designs of the machines in tact while installing Robbins cutting tools in both cutterheads. In particular TBM “Krishna” underwent 112 days of repairs and testing. The refurbishment, and subsequent assembly and launch of the two machines, was carried out even as the Chickpet station was being constructed in order to mitigate any further delays. The two TBMs were re-launched in 2015 on their last drive—in March for TBM “Kaveri” and in December for TBM “Krishna”.
Challenging Ground Continues
Difficult conditions were encountered during the bore: the initial 160 meters of the drive was found to consist of residual soil, gradually transitioning into a mixed face of soil and highly weathered granite over the following 100 m. The mixed face conditions then gave way to a full face of fresh granite in the last 50 meters of boring.
The zones of transition were particularly difficult, with soil occasionally falling in due to the vibrations during tunneling. The conditions also made it impossible to maintain hyperbaric air pressure during cutterhead interventions. This problem was overcome by pumping a weak-mix grout solution into the ground surrounding the TBM. The solution permeated into existing voids and effectively prevented air from percolating through to the surface. A period of approximately 36 hours was initially required for curing of the grout solution. However, on-site trials with various additives enabled the standing time to be reduced to 12 hours.
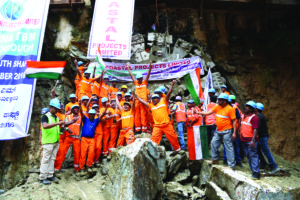
Robbins and crews celebrate the breakthrough of TBM “Kaveri”.
A Resounding Success
Despite the challenges, the TBMs were able to achieve advance rates of 50 mm per minute in highly weathered rock and 22 mm per minute in sections of competent hard rock. TBM “Kaveri” completed its final breakthrough in June 2016. The second TBM “Krishna” had the advantage of known geology and completed its excavation in about nine months on September 28, 2016.
The iPS Experience

When the TBM emerged from the rescue shaft most cutters and grill bars were worn away.
On another section of the recently completed Namma Metro, iPS rescued and refurbished a stuck TBM from another European manufacturer, and then operated it for owner Bangalore Metro Rail Corporation (BMRC) alongside the project’s original contractor.
Initial Inspection
iPS found severe wear—the cutterhead was essentially bare, and the cutters, disc boxes, cutter mountings and grill bars had been worn away. On inspection a serious crack in the screw conveyor was found and the flights had been severely worn. The TBM had been operating for 12 months and had bored 300 m of abrasive ground with insufficiently thorough maintenance. Geology consisted of weathered granite with a high quartz and feldspar content, 130 MPa UCS, and was often mixed with softer soils. It came to a standstill below the main railway lines at a major Bangalore metro station.
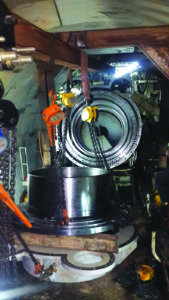
iPS crews had to rebuild the machine inside the tunnel.
Rebuild & Recovery Plan
iPS was able to build an intermediate shaft and refurbish the TBM to the point that it could advance into that shaft for further rebuild work including a replacement cutterhead. But the rebuild work itself was not easy—sourcing parts in India was a challenge, with smaller parts being brought in from Germany and other countries. A new cutterhead was shipped to the site by air freight. Crews dismantled the TBM to inspect and repair the screw conveyor, hydraulic system, PLC, and main drive. The TBM was relaunched in August 2015.
A Second Chance
Once the TBM had started up again, iPS then trained the crew on the importance of maintenance and inspections. They went over cutterhead interventions, what to look for, and how to prevent significant damage.
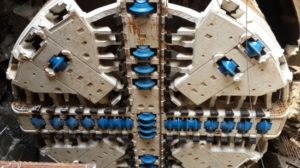
The cutterhead shown was shipped to the site by air freight, as sourcing parts was a challenge.
The training and TBM rebuild were a success—despite continued abrasive geology and mixed face conditions the machine completed the remaining 630 m of its drive in seven months. Frequent interventions were undertaken to maintain and inspect the machine. Breakthrough occurred on April 19, 2016.
Key Takeaways
Like any piece of machinery, it is essential to consider the total life cycle and to take steps to maximize the efficiency and life of the equipment through good operation and maintenance. Contractors should work with equipment suppliers to learn of the maintenance that is required—both scheduled and in response to changing geology.
When a project begins, err on the side of caution: do too many inspections, more than you think are necessary, to get a feel for how the machine reacts in different geologies. Geological surveys are extremely important, but they don’t always reveal every feature, so in the event the machine encounters unexpected geology, even more inspections will be necessary than normal. Above all, avoid complacency: just because a TBM is a large steel machine with a metal cutterhead and cutters doesn’t mean that nothing can damage it.
The proof is in the multitude of successful projects around the world: TBMs can and have shown their ability to excavate projects at world-class rates of advance even in very difficult conditions. With proper maintenance and operation, a TBM can last over many kilometers of tunnel and years of use.
Recent Posts
- Tunneling in Turkey: The Esme Salihli Railway
- Incredible India: Machines on the Move in Agra and Delhi
- Notice of Retraction and Apology
- Four Things You Need to Know about Probe Drilling and Pre-Grouting
- The Latest Updates: Records in Toronto, the News from Nepal, and More