Category: Redefining the Industry
Let’s Be Clear: Transparency is a Boon, not a Bust, for the Tunneling Industry
The idea of transparency is one that we most often hear touted in politics and policies. But transparency is a concept that applies to our underground industry as well. Widespread knowledge sharing can and should be the policy in our industry, but all too often jobsite politics, confidentiality agreements, and fear of poor public opinion limit what is ultimately divulged. I argue that transparency in tunneling is a help, not a hindrance, and we can make steps today towards clearer communication.
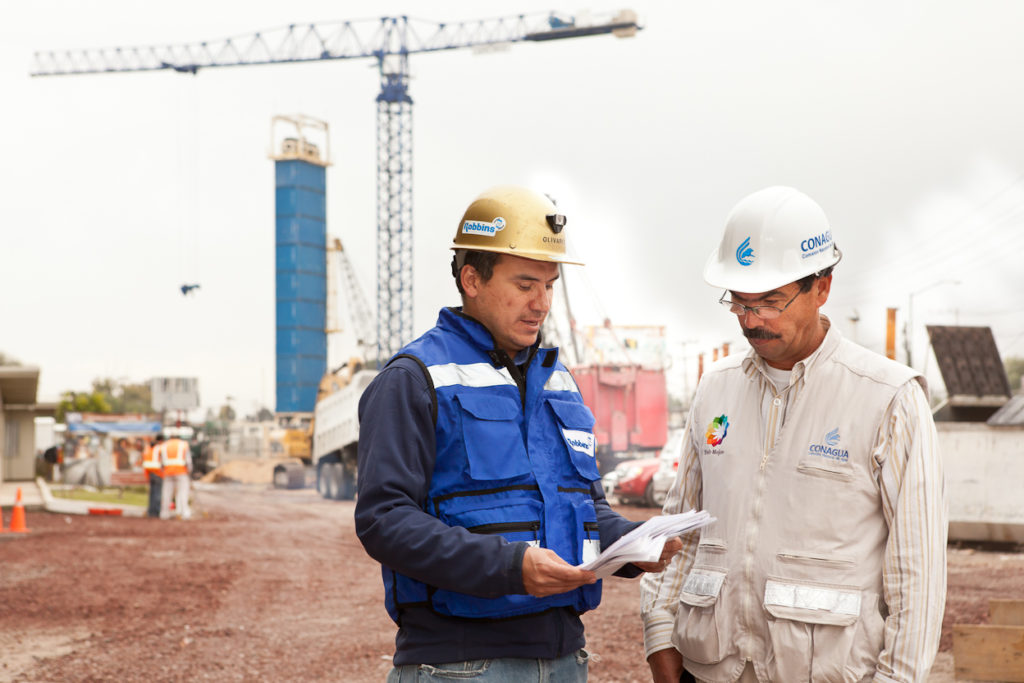
Transparency, achieved through better communication among all stakeholders, is the key to continued success in our industry.
Why It’s Needed
- Learn from Experiences in the Field: Tunneling professionals deserve full access to the successes and the problems that have been encountered in the field. If we were to employ universal knowledge sharing, tunneling operations themselves could become safer and more efficient and overall project costs could be reduced.
- Improve Tunneling Technology: Knowledge of advance rates, performance in specific ground conditions, wear rates for cutters and other surfaces in contact with the cutting face, performance of ground conditioners and foams, and many other types of info are imperative to improving technology. Tunnel boring could be made faster, safer, and more cost effective with such knowledge. It could also improve willingness to try new and emerging technologies in the industry, which benefits all stakeholders. With a good knowledge of TBM performances in specific ground conditions, TBM specifications could also be written to greater accuracy and result in using the most cost effective solutions.
- Improve Risk Sharing: Risk is often apportioned unfairly on today’s tunneling projects. In many cases the TBM supplier is required to shoulder a larger part of that burden than their potential returns. With a better understanding of the risks through knowledge of past projects, as well as knowledge of past risk sharing strategies, this problem can be resolved.
- Ensure Fair Financial Practices: With transparency in terms of contractual pricing and project spending, payments for work performed, etc. and other unsavory practices can be lessened.
- Reduce Litigiousness: Claims in tunneling projects are on the rise worldwide. Recent projects have resulted in separate and duplicate claims against different parties, such as the equipment manufacturer and the owner, for the same issues and without their mutual knowledge. Such claims are unfair, and through transparency and equal access by all parties to a Dispute Review Board, the frequency and extent of lawsuits in our industry could be reduced.
From the Equipment Supplier Perspective
As equipment suppliers, we strive to share the information that is available to us. We’ve opened up about stuck TBMs, challenging drives, and how we’ve overcome those issues. We’ve also tried to share whenever possible why we think fast advance rates and good efficiency were achieved on various projects.
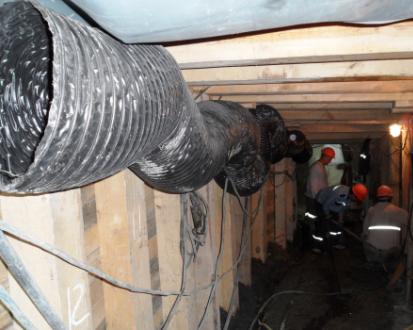
A bypass tunnel at Turkey’s ultimately successful Kargi project, where we shared information on seven such tunnels built in the first 2 km of tunneling.
Unfortunately knowledge is sometimes not shared even within parties on the same project, such as the contractor, project owner, owner’s representative, and equipment supplier. Time and again we see that communication between all parties is key to overcoming challenging conditions. The road to transparency starts here: with clear communication between all coordinating parties on a given project.
Not Without Precedent
Transparency is not an untested idea in our industry. A great recent example is that of the U.K.’s Crossrail project. The project follows governmental codes of practice for data transparency and the country’s Freedom of Information Act. Details such as project and equipment costs, spending budgets and records, safety records, and more are available for download on their website, and special requests can be made for additional data. Multiple reports have also been up front about TBM performance, advance rates, and other experiences on the project. The Crossrail project was highly successful and, arguably, transparency played a large part in that. Crossrail is also just one example of transparency at work in the U.K.—governmental programs such as Transport for London’s Transparency Strategy aim to give clear and consistent information to the public about all road and public transit spending.
A Call for Clarity
Transparency is possible in the tunneling industry, but it may require things like international regulations, or at the very least certifications that could be provided by an international organization like the ITA. Such a certificate would be highly beneficial to all stakeholders: It could certify corruption-free practices, and guarantee knowledge sharing. Transparency is not an easy thing to achieve, and there are certainly barriers to the process in various areas of the world. But we can start with transparency requirements within projects, and then move outward. To be clear: knowledge sharing is something that can only benefit our industry. It is our recommendation we start today.
Are You in Tough Ground? Learn from our Trials and Tribulations in some of the Tunneling World’s Most Difficult Projects
Squeezing Ground, Fault Zones, Water Inflows, and More
True story: In a mountain range, crews worked on a shielded TBM more than 500 m below the surface. The TBM had excavated several kilometers in worsening conditions. The crew encountered karstic aquifers filled with mud and water. Personnel were pumping polyurethane through the cutting face to staunch the water inflows.
Suddenly, water inrushes climbed to a rate of 1,500 liters/second, creating a knee-deep underground river and causing the machine to become stuck. Thankfully, the crew was able to exit the tunnel, unharmed. The massive inrush created a damming effect with enough pressure to crush the TBM shields and send cylinders catapulting into the back-up.
As quickly as it had started, the machine ground to a halt, deep underground.
What happens when you encounter an unforeseen condition? A severe water inflow, fault zone, or squeezing ground? A geological feature that seems like it might stall your tunneling operation altogether? Some of our most difficult challenges—spanning from New York to Peru to the Republic of Georgia—are detailed below. These case studies are meant to pass on our knowledge and experiences to help you overcome obstacles, unforeseen or otherwise.
How to Overcome an Epic Flood: New York’s Harbor Siphons project
Sometimes an unforeseen condition requires a rescue effort to overcome. In October 2012, a storm was coming to New York City’s Harbor Siphons Project on the shores of Staten Island. The undersea tunnel and its 3.6 m CAT EPB ground to a halt when hit by Superstorm Sandy. The monstrous hurricane battered the eastern seaboard of the U.S. with winds of 145 kph.
The launch shaft was inundated with seawater despite contractor Tully/OHL’s best efforts. Flood water entered the tunnel and stopped the TBM just 460 m into its 2.9 km long drive. A 2013 post-storm survey of the tunnel showed a damaged machine extensively corroded by saltwater. All electrical components needed to be replaced.
Contractor OHL turned to Robbins for help. During the downtime, the original TBM manufacturer had exited the tunneling industry. Robbins worked with the contractor to come up with a multi-pronged approach to bring the TBM back to life.
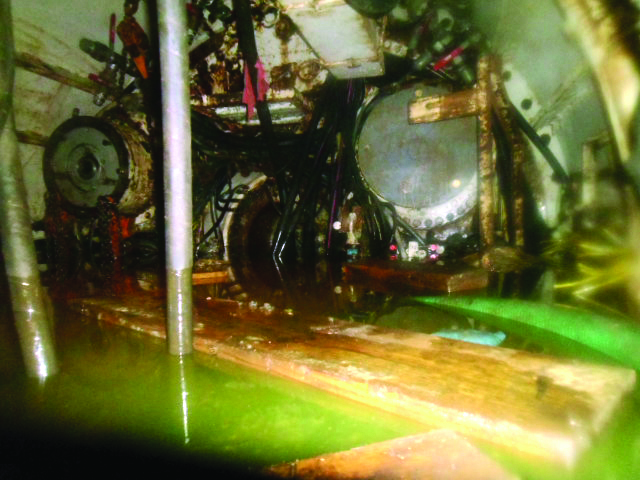
Flooded TBM: A view of the initial inspection after the flood, looking at the machine’s drive motors submerged in seawater.
Hiring a Dedicated Team
Per the scope of work, defined jointly by OHL and Robbins, crews temporarily excluded the cutterhead and main bearing of the TBM for refurbishment, as they were under earth pressure and not accessible. The Robbins team would need to complete the refurbishment taking into account unknowns, such as the condition of the cutterhead. The segmented concrete tunnel lining would not permit the removal of many of the larger TBM components, so these would have to be refurbished onsite.
The Robbins crew was contracted to guide onsite personnel in replacing corroded hydraulic components and installing all new electrical components. Variable Frequency Drives, PLCs, and wiring were replaced inside the small tunnel under atmospheric pressure of 3 bar. Crews constantly monitored earth pressure during the refurbishment. The machine had been stopped with its thrust cylinders in, and thus the crew could not replace or evaluate certain components before the machine started up.
Reverse-Engineering Electrical Components
By mid-December 2013, Robbins PLC technicians were reverse engineering the TBM’s control system. The team understood early on that the previous control programming would be unusable given the PLC change. The technicians had only limited assembly drawings from the CAT manual, so much of the refurbishment, including the PLC system, had to be built from the ground up. The team at site understood how the machine should work and therefore were able to build the correct PLC system.
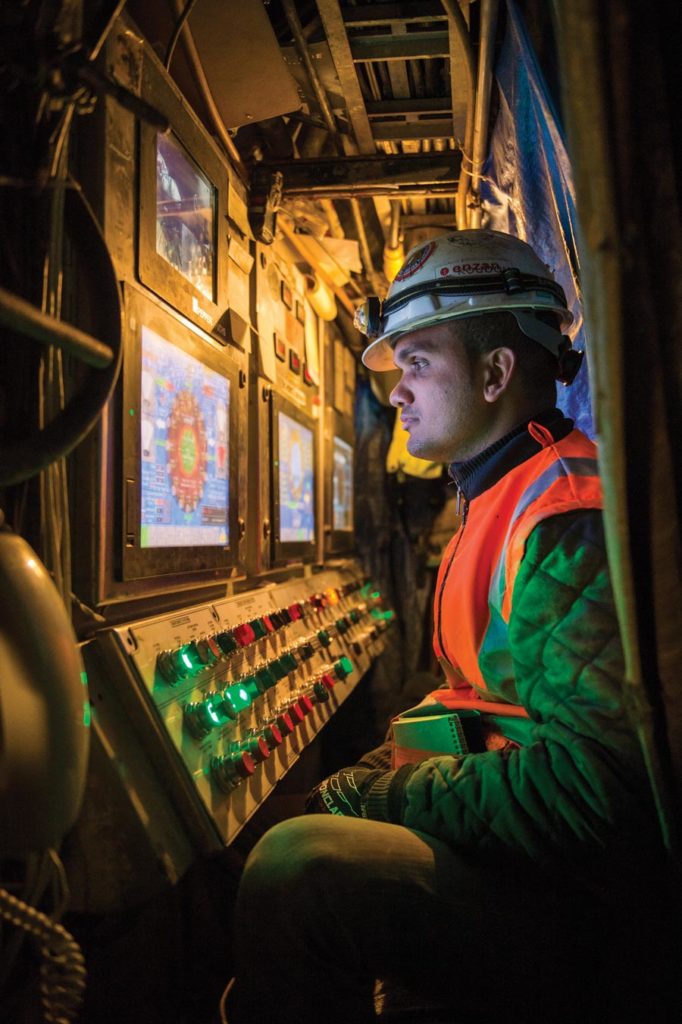
Reworked Electronics: The Harbor Siphons TBM required all new electronic systems.
Coordinating Success
Despite all of the challenges, the refurbishment project was a success. Crews had gone from a shipwrecked TBM—rusted, corroded, and abandoned in the tunnel—to a successful tunneling operation. It was a monumental task, scheduled to be completed in four months, and finished on schedule.
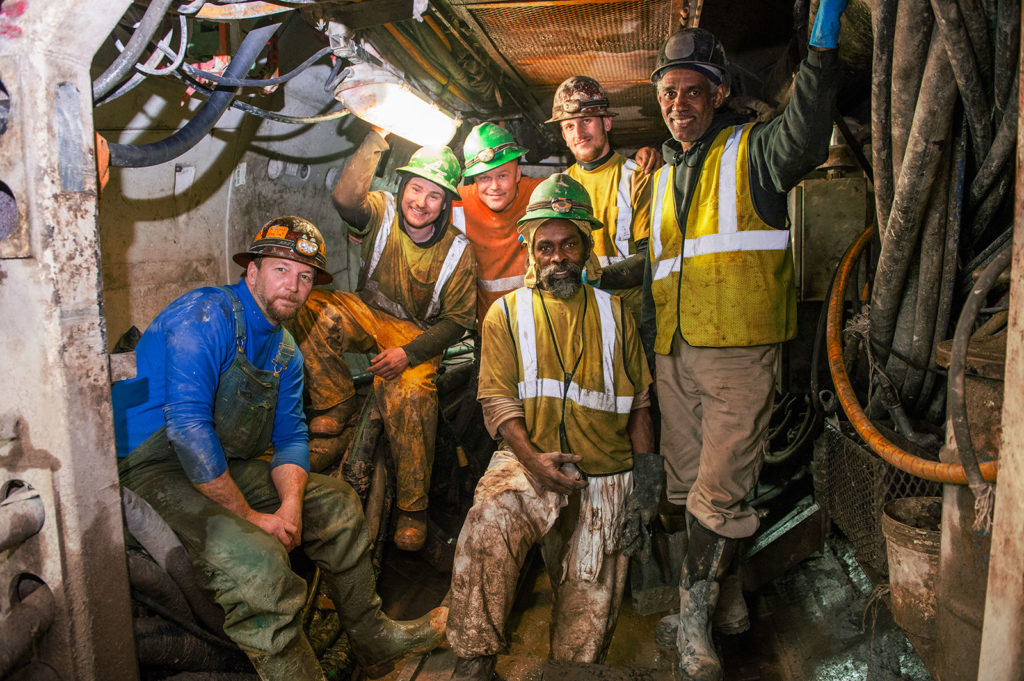
A Good Result: The happy crew during TBM boring, after the full refurbishment.
In the final phase of the refurbishment, a Robbins PLC technician was able to complete the commissioning of the TBM and on April 14, 2014 the machine officially returned to mining. The machine successfully completed its tunnel in February 2015.
Read more in the white paper here.
Make Rock Bursting Conditions Safe for Your Crew: The Olmos Trans-Andean Tunnel
If 16,000 recorded rock bursting events in the world’s second deepest tunnel weren’t enough, the crew at Peru’s Olmos Trans-Andean Tunnel had another problem. As the machine progressed and the cover grew higher—up to 2,000 m at the highest point—the rock bursts became more violent. Crews experienced large over-breaks and cathedralling in fractured and unstable ground. Teams of personnel had to inject concrete into large cavities that had formed during stress-relieving activities and stabilize these cavities with spiling. Then, several kilometers into the tunnel, a major rock bursting event occurred that twisted ring beams and caused damage in 45 m of lined tunnel. Damage was extensive to the TBM gripper, which was ballooned and blown off its mountings. Damage also occurred to other hydraulic cylinders. Thankfully crew members were not harmed, but downtime for repairs would be substantial.
A Century-Long Effort
The Olmos tunnel is a 12.5 km long water transfer tunnel that was bored through the Andes Mountains to bring irrigation to drought-ridden areas on the pacific coast. The project was more than 100 years in the making, with several attempts being made and thwarted by incredibly difficult geology as recently as the 1950s.
In 2007, with Odebrecht as the main contractor, the tunnel was finally completed using a 5.3 m diameter Robbins Main Beam TBM after other attempts with conventional methods failed. The route is the world’s second deepest civil works tunnel with overburden of up to 2,000 m. The tunnel alignment traverses complex geology consisting of quartz porphyry, andesite, and tuff with rock strengths ranging from 60 to 225 MPa UCS. The machine crossed over 400 fault lines including two major faults of approximately 50 m wide.
A Rocky Start
The machine was launched in March 2007, in ground conditions that immediately became more complex than anticipated. As the height of the overburden increased, long stretches of extremely loose, blocky ground were encountered. TBM utilization was as low as 18.7% of working time because rock support installation was requiring a very high 43.5% of the working time.
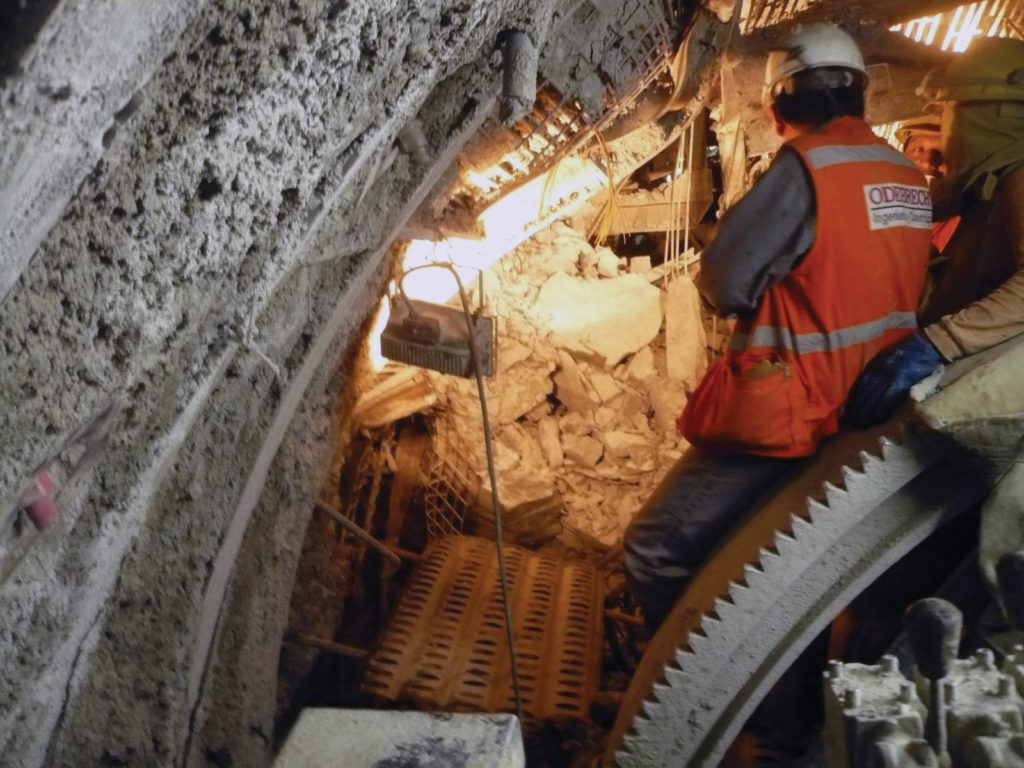
A rocky start: Rock bursting conditions at Olmos prompted a major overhaul of the TBM in the tunnel.
One of the main problems faced was ground deterioration and the resulting falls of blocky ground. The majority of these events occurred during the time taken for the newly excavated bore to pass behind the rear fingers of the roof shield, where ring beams and mesh were installed.
Modifying the Machine in the Tunnel
During consultations between Robbins and Odebrecht, a decision was made to modify the machine in the tunnel. The TBM would be reworked to use the McNally roof support system, which allows support to be installed directly behind the main roof shield. Crews removed the roof shield fingers and installed a series of rectangular pockets in their place. The pockets ran from the rear side of the cutterhead to the trailing edge of the roof support. These pockets were designed to be used with rebar, which is part of the McNally Roof Support System. At a later stage when the ground conditions worsened these pockets were extended to cover the sides of the TBM as well.
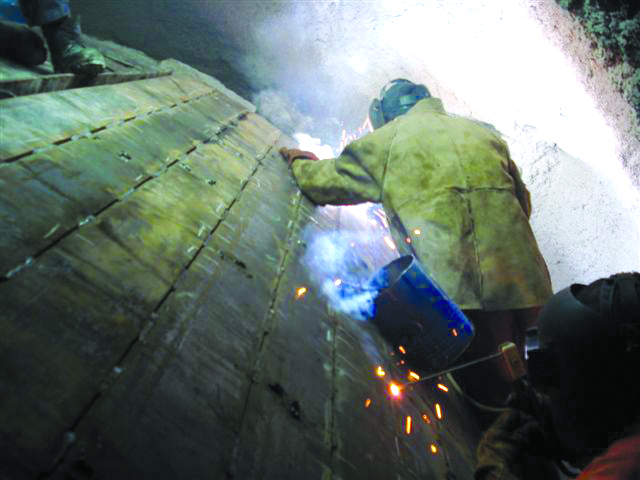
TBM Modifications: The crew add McNally pockets to the TBM roof shield in the tunnel.
The McNally Support System
One big advantage of the McNally support system is that it is possible to install ground support closer to the face than other ground support methods used on TBMs. It holds loose rock in place, which in turn helps to activate the strength of the rock mass and maintain the inherent strength of the tunnel arch. When used correctly the system can significantly reduce the time taken to provide adequate support. It can also offer reductions in the level of support required, and contain rock bursts and collapsing ground. The greatest benefit of the system, by far, is its ability to provide a much safer work area.
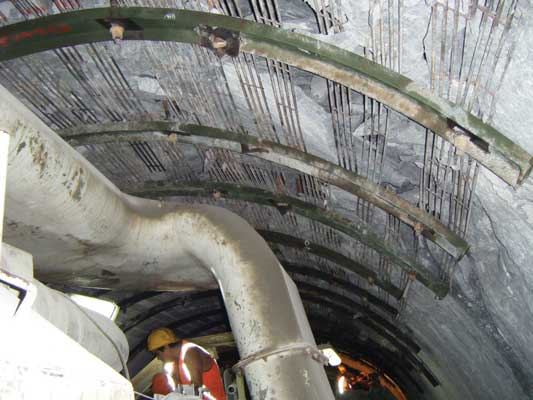
Crown Control: McNally slat installation at the Olmos Trans-Andean Tunnel.
Incorporation of the McNally support system and various other modifications to the TBM resulted in a steady increase in production rates in spite of continuous rock bursting events. The machine broke though in December 2011 having achieved production rates in excess of 670 m a month.
Read more about the McNally Support System here.
Make short work of an unforeseen cavern: The MKTVARI project
The Republic of Georgia’s Mktvari Hydropower Plant Construction project, along the river of the same name, was a challenge from the outset. The initial contractor used drill and blast for the 9.5 km long headrace tunnel through hard rock, but after 1.5 years they had only advanced about 200 m. The new contractor took over a previously-ordered non-Robbins hard rock machine but enlisted Robbins to help with the TBM assembly. They also wanted Robbins to be available if problems occurred. The machine did well at the outset, boring up to 900 m per month. But then, the machine hit bad ground.
Cavernous Conditions
Crews hit an unforeseen cavern above the TBM and were unsure of how to proceed through mixed layers of breccia, andesite, and bands of clay with light water inflows. A Robbins Field Service Manager was sent to the site, where he determined that the cavern was part of a fault zone consisting of unstable material that fell onto the cutterhead. At the time of his arrival, the TBM had passed through most of the fault zone but huge voids were left behind the segments.
Using pea gravel pumped through holes drilled in the segments, combined with cementitious grout, the crew was able to stabilize the existing segments and safely advance through the cavern in about 10 additional segments. There was also a probe drill onsite that had not been used; the Robbins manager persuaded the crew to install the probe drill and conduct systematic probing ahead of the machine, in case a larger section of clay was encountered.
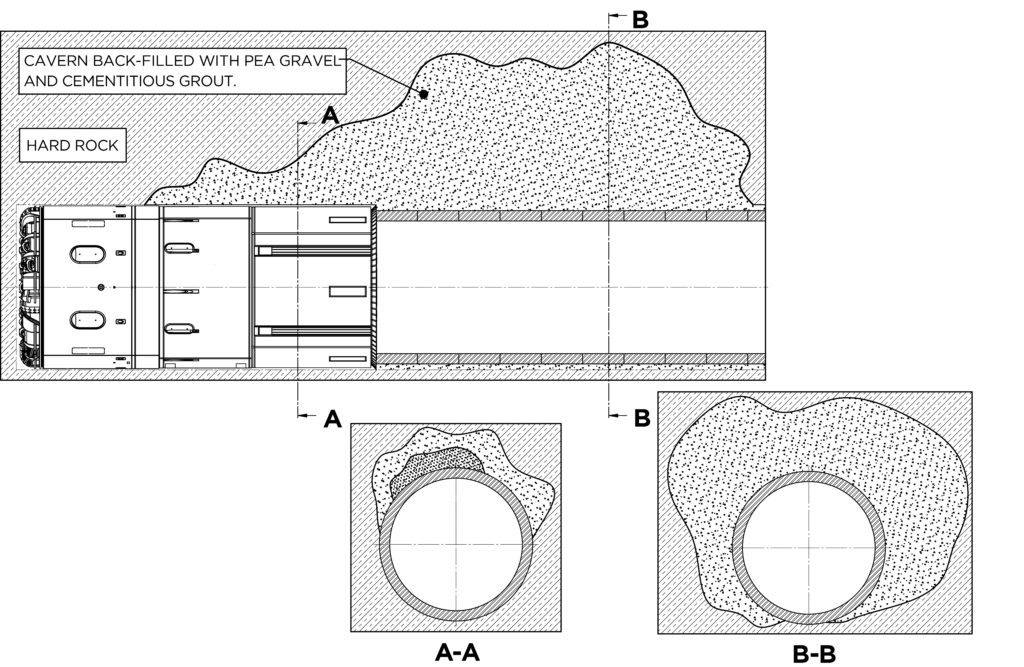
Crossing the Void: Robbins worked with the contractor to backfill the cavern, enabling the crew to advance out of the void in 10 additional segment rings.
Key Takeaways
As can be seen in these examples, planning is key. But, even the best-laid plans can go awry. When conditions go from bad to worse, having an expert team of personnel on your side is by far the most valuable tool and the most positive predictor of a project’s ultimate success. That true story I started off with certainly wasn’t the first such incident in the tunneling world, and it won’t be the last. Be prepared by arming yourself with knowledge, and with a knowledgeable team.
Information at your Fingertips
Learn more about our vast experience in difficult ground conditions. Our selection of white papers covers some of the world’s most challenging projects, while our Project Solutions section offers many examples of past successes.
What’s in a Name? Mixshield, Crossover, Hybrid and More
For underground construction professionals and manufacturers, there is some confusion about the current TBM designations and what they really mean, and for what applications they are to be considered. This is especially noted when it comes to soft and mixed ground type shield machines and if they are to operate in “open” mode, “closed” mode or “semi-open/closed” mode conditions.
The term “open mode” defines defines a mode of TBM operation where no pressure is required to stabilize the boring face; the geology is self-standing and ground settlement will not occur.
The term “closed mode” defines tha mode of TBM operation where face pressure needs to be constantly applied in order to maintain face support. Should the face pressure not be maintained as determined by the geology, under-pressurization will cause ground settlement, over-pressurization can cause surface heaving.
The term “semi-open/closed mode” defines a mode of TBM operation in varying geology where the TBM has the ability to control the face.
The various machine types in question are Mixshield, Hybrid and the Robbins “Crossover”. Are they the same? If not, what is the difference? This blog seeks to clarify and explore those definitions.
Mixshield
Mixshield is a terminology introduced by German manufacturer Herrenknecht for what is essentially a Slurry TBM that uses an air bubble to control and support pressure at the face. The air bubble acts like an accumulator with the belief that this offers better pressure control. This type of machine operates only in “closed mode”. Mixshields are not meant to go from high pressure soft ground to significant rocky conditions with great efficiency, hence the name “Mixshield” is somewhat of a misnomer. They can excavate mixed face conditions, but the machine configuration is not changed so it is a different thing entirely than to excavate significant sections of differing geology. In order to change the configuration to allow more efficient operation in different sections of geology, a Hybrid machine is needed.
Hybrid, etc.
“Hybrid”, “Dual Mode”, and “Multi-Mode” are names developed by the industry to try and define machines that feature components of two different machine types. The most common types is a multi-mode between EPB with a screw conveyor (for operation in “closed mode” or “semi-closed mode”) and conversion to Rock Mode with the installation of a belt conveyor (for use in “open mode” operation). Typically, the only changes made to the machine are components such as cutting tools and muck removal method that can be switched out in the tunnel depending on ground conditions. The machines are used for large sections of vastly different geology in one tunnel, such as a section of clay followed by as significant section of rock. However these types of machines are typically designed as EPB machines and then converted, making them not very efficient for use in rock geology.
Robbins Crossover
The “Crossover Series” of TBMs was developed by Robbins in March 2015 using innovative design concepts to effectively excavate between different geologies. The Crossover Series is Robbins’ version of a Hybrid TBM but with many additional features to allow the TBM to effectively cross between different geology types. Operation of the machine can allow the machine to quickly change from “open mode” to “semi open/closed mode” and “closed mode.” The main types of Crossover TBM include the XRE (Crossover between Hard Rock and EPB), XSE (Crossover between Slurry and EPB) and XRS (Crossover between Hard Rock and Slurry). The features include interchangeable cutting tools; single direction and bi-directional cutterhead muck pick-up; multi-speed, multi-torque cutterhead drive systems; durable, abrasion resistant components on the cutterhead and screw conveyor; emergency thrust; tapered shields to reduce shield entrapment in squeezing ground; integrated probe/grout drill system for ground consolidation; and heavy steel construction with components designed for +12,000 hours of life, just to name a few.
The Crossover Series is suitable for tunnel projects that require the ability to excavate different types of geology efficiently with one machine, based on ground conditions. The TBM design is flexible enough to switch from one mode to another. Ultimately, Crossover Series machines are cost efficient in the long run, since the TBMs require less repair costs than a non-customized machine, and they can be used on multiple projects.
Based on the ground situation (whether it’s self-supporting ground, self-supporting ground with water pressure, or unstable ground), the Crossover is optimized towards “open” mode (as in hard rock shielded TBMs) or “closed” mode (as in compressed air, slurry, and EPB TBMs).
Reliable geological information is therefore critical to the TBM design. An accurate geological report is needed to decide when and where to convert the machine as well. During excavation, adequate probe drilling is further essential to determine the ground conditions ahead of the Crossover TBM.
Below are the features specific to each type of Crossover machine.
Crossover XRE
- Mixed ground cutterhead: with disc cutters & soft ground tools or a combination of tools (interchangeable).
- Two-speed gearboxes: provide high torque at low RPM under soft ground conditions and high RPM under hard rock conditions.
- Cutterhead rotation: Single direction is more efficient in hard ground conditions and bi-directional is more efficient in soft ground to prevent roll.
Crossover XSE
- Equipped with both screw conveyor and slurry system for muck removal.
- Ground conditions: soft ground containing water under pressure (particularly for water pressures > 5 bar).
- The most universal of the Crossover machines, the XSE can bore in most types of ground.
Crossover XRS
- Highly adaptable to variable ground conditions; suitable for rock tunnels with water pressure > 5 bar.
- Hard rock machine with a rock cutterhead and slurry system in place.
- Capable of mining rock through high water pressure without grouting off water flows.
Rebuilt, Refurbished, Remanufactured: Designing a TBM to Live for Generations
With the increase in large TBM projects over the last few decades and a global awareness of their environmental impacts, there has been a greater focus on the origin of TBMs and their parts. The focus has been further highlighted by the ITAtech; a technology-focused committee for the International Tunneling Association (ITA-AITES) that produced guidelines on rebuilds of machinery for mechanized tunnel excavation were released in 2015. While the guidelines are relatively new, Robbins has a long history of delivering robust machines, many of which are rebuilt (many are also 100% new). In this post, I’d like to explore just what a “rebuilt” TBM is, and what that means to Robbins as a TBM manufacturer.
History and Terminology
Throughout Robbins’ history (over 65 years), our TBMs and design philosophies have been based on the understanding that TBMs require a substantial initial investment, and designing machines for single tunnels is neither economical nor sustainable. This realization has resulted in robust, sturdy designs of high quality that–even before the pencil is put to paper–are meant to last for multiple projects. This is clearly shown when you look at the number of Robbins TBMs around the world that are excavating their second, third, fourth or even their eighth or ninth tunnel. There are even Robbins TBMs manufactured in the 1960s that are still in operation!
For Robbins, the term “rebuilt” describes any manner of creating a custom TBM from already existing components. It is the term we use most and continue to use. The ITAtech guidelines introduce different terminologies depending on the extent to which a TBM is rebuilt. They are, very shortly, described here:
- Remanufacturing – Remanufacturing is a process with the aim to start a new life cycle of the product using its current or modified configuration.
- Refurbishment– Refurbishment can be considered a full maintenance, where defect parts are replaced to extend the life of the product in its original configuration or with small modifications.
The guidelines describe the requirements of each process in order to designate a TBM “refurbished” or a “remanufactured”, but in reality the majority of “rebuilt” TBMs may be somewhere in between these qualifications.
The Robbins Philosophy
Over the years Robbins has built a quality assurance system that ensures when we deliver a rebuilt machine, either to the original configuration or a modified one, we still adhere to a design life of 10,000 hours. This standard also includes checks to make sure that all the components are in a functional condition of ‘as new’ or ‘new’. Due to our long experience in rebuilding TBMs, we can offer in principal the same warranty on a rebuilt machine as a new machine.
The Robbins philosophy on this is that, in order to offer the same design life and same warranties on a rebuilt machine, the initial design of the TBM will need to consider that the TBM will be used on several projects. This means that the major structures will need to be strong enough to survive even the toughest conditions and that worn parts can easily be replaced. If the machine is not properly designed for multiple projects, there will be a need to do major work to get the TBM in a working condition either in its original or modified configuration. Robbins strongly believes that considering the total life cycle of a machine, even in its first design stages, is the most economical and sustainable option.
One can argue that project owners typically only have one project and that the condition of the TBM and the suitability of its rebuild is therefore not essential. This is something that is also reflected in many of today’s tunneling projects, where the commercial consideration is often given far more attention than the technical one. We would argue, however, that an initially sturdy and robust design of the TBM will give the project more uptime, higher production rates and better flexibility if unexpected conditions are encountered, making it a good and effective kind of insurance for the project. This effect has been clearly identified in the field, where Robbins has more than 90% of world production records in hard rock.
What’s Missing
In terms of the international guidelines, they are certainly necessary and welcomed. However, the strictness of the guidelines makes them hard to adopt worldwide and perhaps not realistic for the majority of TBM rebuilds, which are customized based on project needs. The ITAtech guideline is also missing something else: the definition of what makes a TBM “new”. While opinions from different suppliers vary, Robbins is perfectly clear on this topic: If you are buying a new TBM, then it is a 100% new TBM with only 100% new components. We strongly believe the whole industry should commit to this definition of what makes a TBM “new”, and this definition should be added to the guidelines.
Robbins has throughout the years built up a vast experience in providing the right machine for the right project, whether that means a new or rebuilt machine. As a part of this experience, we are convinced that the life cycle of TBMs should be considered at the earliest stages of the design process. Designing machines with ease of rebuilding in mind ensures that we do not have to start from scratch every time a machine needs work. It also results in time, cost, and energy savings when the time does come to rebuild a machine for a new project. For the industry, this type of perspective is the only economical and sustainable option going forward.
By Sindre Log, Civil Engineer and General Manager for Robbins Norway
The Brenner Base Tunnel: A European Core Project
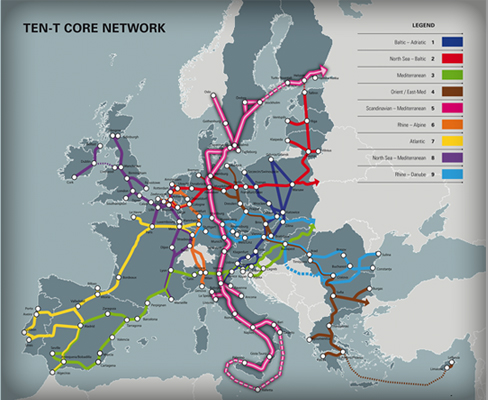
Figure 1. The Trans-European Network for Transport (TEN-T) aims to connect all European member nations from West to East and and North to South.
Tunneling is a worldwide business with often-changing markets. At the moment, everybody is watching the markets in Asia and in particular various huge projects in China and India, as well as the Middle East. With these busy hot spots, it’s easy to overlook projects elsewhere.
In this blog, I want to refocus and take a look at Europe, where there are some very interesting and challenging mega-projects underway for the Trans-European Network for Transport (TEN-T) of the European Union. The TEN-T connects all economies in the European Member Countries from West to East and North to South (Figure 1). This master plan for connectivity in Europe includes nine core network corridors with several projects crossing the borders of multiple European countries. The cross-border project implementation is complicated because of the different technical, financial and statutory requirements.
TEN-T core network projects
The core projects of the TEN-T master plan all serve as missing links that would connect the European Member Countries, like the Koralm and Semmering Railway Tunnels (both in Austria), Lyon-Turin Railway Project (connecting France and Italy), Fehmarn Belt Crossing (connecting Denmark and Germany), Brenner Base Tunnel (connecting Austria and Italy), Ceneri Base Tunnel (connecting Switzerland and Italy) and also some completed projects like the Oresund Bridge, Tunnel Road and Rail Fixed Link (connecting Sweden and Denmark), Milano-Roma-Napoli Railway (Italy), Gotthard and Lötschberg Base Tunnels (Switzerland), Betuwelijn Railroad (connecting the Netherlands and Germany) and the Channel Tunnel (connecting United Kingdom and France).
Financial support from the European Union in an amount estimated at 500 billion euro is required to complete this Trans-European Network and to widen some of the bottlenecks within it. The Brenner Base Tunnel is one of the most interesting cross-border projects and a core project of the TEN-T master plan (Figure 2).
Brenner Tunnel Conversations
The Brenner Base Tunnel (BBT) is a big challenge for all involved parties. In 2015, I had the great opportunity to interview Prof. Konrad Bergmeister, who has been the CEO of the BBT SE since August 2006 (Figure 3). Bergmeister was previously the technical director and head engineer of the company managing the Brenner Highway and was responsible for the planning and construction of new infrastructure and for maintenance of the existing structures. For the past 22 years, he has taught construction engineering at the University of Natural Resources and Applied Life Sciences in Vienna (Austria). He has been the President of the Free University in Bolzano (Italy) since 2010.
Interview with Prof. Bergmeister
Could you give me a brief overview of the Brenner Base Tunnel?
The Brenner Base Tunnel is a ground-breaking engineering project for the 21st century. This underground structure has a total length of 64 km and consists of three tubes: the exploratory tunnel and two main tubes with four lateral access tunnels connecting them together (Figure 4). The tunnel itself will become the longest railway tunnel in the world once complete.
The history of the tunnel is a long one: 160 years ago, an Italian engineer came up with the idea to go beneath the Brenner Pass. After World War Two, the project was reassessed but never proceeded. Finally, between 1987 and 1989 a feasibility study was carried out. The preliminary project was approved in 2002, and between 2005 and 2008 project details were worked out. In 2009 the environmental and technical approvals were obtained in Austria and in Italy. So we started with the first exploration of the whole rock situation in 2006, drilling vertical bore holes that totalled more than 28 km when we sum it all up. And this preliminary information was used in order to study the final layout of the tunnel in order to do the definitive design.
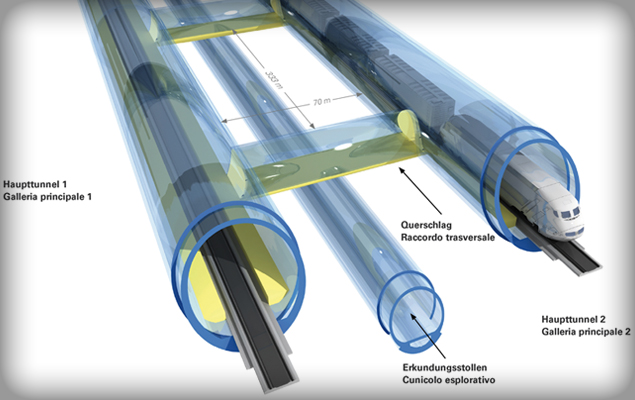
Figure 4. The 64 km long Brenner Base Tunnel consists of three tubes: An exploratory bore and two main tubes connected by access tunnels.
What, for an engineer, is the most challenging aspect of the Brenner Base Tunnel?
The most challenging issues for me are the following:
First of all we developed the so-called design guide in order to have the right basis to execute the design in both countries. This design guide was based on some new design ideas taking into account all the safety issues that have been proposed with the Eurocodes on a European level.
Second we developed internally a so-called chance and risk analysis, which should allow us to monitor the development of the project in terms of possible chances and risks. How we are doing that? Well we are trying to evaluate and double check the actual ongoing construction with our project managers and external experts and we are trying to identify all the possible risks and chances that might occur as tunneling proceeds. This analysis is part of a database that will be actualized on a yearly basis so we have additional information in terms of possible risks, additional costs, cost savings and scheduling.
The third issue is something that deals with some novel forecast technologies. We are using digital mapping and photogrammetric mapping as forecasting methods, particularly for the ongoing drill and blast operations. This is called the Tunnel Control System and is able to predict complex excavation shapes by using statistics regression analysis. It is based on 3D point clouds of the rock surfaces captured after each excavation, and the precision of previous excavated profiles is also analysed. The previous blasting data and the corresponding geological information are used for the prediction of the upcoming upper and lower blast profiles. For the forecast a certain number (minimum five previous blasts) is taken into account for a linear or nonlinear regression analysis. Through this optimization procedure up to 65% reduction in over-break has been achieved.
And the last issue is actually that we have been trying to develop ideas for the reuse of excavation material. The concrete mixture must be sustainable for the next 200 years since this is the lifetime of the tunnel. We have been studying the material of the exploratory tunnel (Figure 6), especially the schists, in the central zone of the project and we were able to modify the preparation methodology and optimize the concrete mixture to re-utilize 100% of the excavation material. Five years ago, all of the geologists and specialists during the approval phase told us that the excavation material must be disposed of. So this is actually a real step forward into optimizing the project excavation.
What is your opinion about the on-site TBM assembly of Robbins compared with the re-assembly of factory-built machines on jobsites?
From an engineering point of view we are only interested that the machine works very well on site. So we are interested to see, when the machine really starts, the performance in a certain excavation length. We are interested in the results and not so much on the specific assembly situation. There are different trade-offs: On the one hand, if you pre-assemble the machine in the production facility, this can guarantee you certain tolerances and probably certain pre-operation errors can be adjusted and finally avoided. But, the major problem is that you have to transport the semi-assembled machine on site and you have to re-assemble the machine on site again and then you have to start excavation. However, with Robbins for example, they can bring all the individual pieces on site and very often they are adjusting the machine itself directly under site conditions. It is easier, I think, to do the adjustment on site directly for specific logistics reasons. We can say that you might have more flexibility if you assemble directly on site compared with doing the assembly at the production facility.
Beyond Boring: A Journalist's Fascination with Tunnelling
About the Guest Author: Roland Herr has a background in civil engineering and is an international freelancing journalist. He has over 20 years of experience on engineering and construction projects all over the world, and is especially interested in tunneling.
Those working in tunnelling understand that this is an industry more fascinating than any other. What is it about tunnelling that makes it so exciting to those in the field?
Curious to know more, I discussed this question with some very experienced European tunnelling specialists: Frode Nilsen (Norway), Managing Director of LNS, and Dr.-techn. Klaus Rieker (Germany), Managing Director Tunnelling Division of Wayss & Freytag Ingenieurbau AG. Both conversations took place at different places and times, but with strikingly similar results.
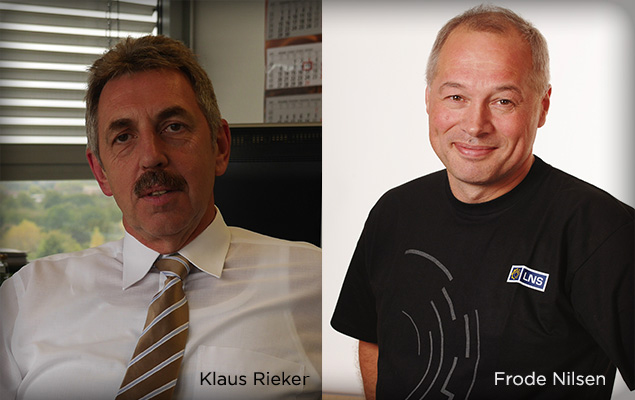
Dr.-techn. Klaus Rieker and Frode Nilsen took time to share their experiences in the tunnelling industry.
Frode and Klaus both have extensive backgrounds in the underground industry. Frode has been working with tunnels since he left university, the Norwegian Institute of Technology, in 1988, and Klaus has been building tunnels for 25 years. Comparatively, I am a “youngster” with 14 years of experience with tunnels and the tunnelling industry, but no less enthusiastic.
Read on for the results of my Q&A sessions with Frode and Klaus:
One characteristic shared by most tunnellers is that they work internationally, on many different projects with varying levels of responsibility. Tell me about your international experience.
Klaus: [At Wayss & Freytag] I was assigned to different projects in Singapore, Malaysia and Taiwan. As a young engineer working in Asia, it was very hard to gain acceptance, particularly because in the Asian culture, older people are typically responsible for project management. It was difficult to convince the contractor that I could handle it, but step-by-step I proved myself with my performance and knowledge. I remember with pleasure my time on a metro project in Singapore; altogether we had about 30 nations involved on the project. It was really amazing!
Frode: Our most impressive project [at LNS] was SILA for the Iron Ore company LKAB. We blasted 12 silos out of the rock and built a 600 m long unloading hall and a 2.8 km tunnel for iron transport from the silos to the harbour. Our most famous project was the Svalbard Global Seed Vault in Spitsbergen for the UN, where we built tunnels and 3 rock caverns in the permafrost with an even temperature of -18° Celsius to store samples of the world’s seeds.
For Frode, the timeline and longevity of underground projects is also an amazing feat worthy of note—tunnels can be built in difficult ground conditions over a period of years, but the hard work pays off in that many tunnels have a design life of 100 years or more.
Working in tunnelling also provides a unique perspective on emerging markets. Which countries or markets are currently experiencing rapid development when it comes to tunnel construction?
Frode: In Europe, Norway is one of the most interesting nations, especially for drill & blast, with hard competition and low prices. In Asia, China is on top, and South America is also growing, in particular with the mining industry in Chile. Much of the future of tunnelling lies in mining: studies show that in 2034 around 60% of mining will be done in underground mines. That means tunnels for access, ore haulage, and more.
Klaus: Germany is now no longer really a market for tunnelling, and in Central Europe tunnel construction is declining. Meanwhile, Asia is the growing market. In Singapore for example, 10 to 20 machines are running annually for the metro system extension. China and India are also huge markets right now. I find North America to also be an interesting market with many current and upcoming projects.
Every industry has its own set of challenges. What do you find most challenging about working in the tunnelling industry specifically?
Klaus: A defining characteristic of tunnellers is that we love a challenge. We thrive on new, very difficult situations that demand utilization of all our knowledge and problem-solving skills, in order to find the best technical solution.
Frode: Client demands can be challenging, and are often accompanied by environmental and technical limitations as well as financial constraints.I am happiest when projects are profitable and everybody involved is satisfied.
Frode and Klaus’ comments on their experiences led me to one overarching conclusion: engineers working in tunnelling are some of the world’s brightest and most experienced, with shared passions for overcoming difficult situations and ever-expanding their world views. For adaptable and driven engineers, the tunnelling industry offers a challenging yet rewarding career with job security, as projects and new markets continue to emerge globally.
The Light at the End of the Tunnel: The Positive Side of Seattle’s SR99 Project
Seattle is the founding city of The Robbins Company, and a place where I lived for nearly 15 years and commuted on SR99 while working at Robbins early in my career. As such, the new SR99 Viaduct Replacement Tunnel Project is of great interest to me.
The industry is all too familiar with Seattle’s SR99 Tunnel and its TBM, known as “Big Bertha”. More specifically, much has been written with regards to the TBM needing repairs after about 300 m of boring. The TBM is the world’s current largest at 17.5 m in diameter, and is excavating a 2.7 km long drive.
TBM Tendering
Robbins was a relatively new entry into the EPB/soft ground tunneling business when tenders were called for the latest SR99 project in 2011, and we made a concerted effort to get the order for this particular TBM. We teamed up with Japanese TBM manufacturer Mitsubishi Heavy Industries (MHI) to get the order. Robbins has had an association with MHI for more than 20 years, with jointly-designed machines operating around the world on projects in India, China, the U.S., and more. MHI has built over 1,000 EPB machines and in my opinion, the Japanese TBM manufacturers are further advanced in EPB technology than their European and American counterparts.
Through the process of trying to receive this order, we learned a lot about the geology, as well as the contractors’ and TBM’s specification requirements. The contractor Dragados, one of the JV partners and very well-experienced in soft ground tunneling technology, developed a high-level specification for the TBM suppliers. All of the prospective TBM suppliers were required to quote and if successful, supply to this standard. We eventually stepped out of the tendering process to supply this TBM, as the lower prices and greater assumption of contract risk offered by our competitors made the TBM supply an impractical business option for us.
Tough Tunneling
The current situation at the SR99 project is more positive than media tend to paint it. The project design consultant did a commendable job on laying out the tunnel route and building in a contingency plan. Boring through glacial till, even with modern TBMs, is never an easy task as previous projects like the Brightwater Conveyance Tunnels have taught the city of Seattle. This is doubly so along the Seattle waterfront, which includes manmade fill, utilities, and buried refuse. In such ground, TBMs can encounter rapidly changing geology; pockets of groundwater; abrasive soil; and manmade objects such as unmapped disused pipes; foundation piles; etc.
Aware of the problems that can develop while using an EPB TBM in glacial till under a city with a lot of backfill, the SR99 designer wisely developed a contingency plan. The strategy, in addition to pre-planned safe havens, involved a “shake down” stretch of tunnel, which ran under no buildings. If problems did occur repairs to the TBM could be made by sinking a surface access shaft at this location. Unfortunately the need for that repair event occurred shortly after the machine commenced excavation.
Why there were failures of the cutterhead seals, and potentially the cutterhead main bearing, is yet to be determined. I doubt there will be any signs of failure of the main bearing when the crews get to inspect it. However, all parties involved are wisely taking precautions and installing a new main bearing in addition to the seals.
Bertha’s Lessons
The Seattle Tunnel Partners and WSDOT have in place a panel of experts to advise them on the highly technical details of the TBM design. I personally know several of these experts and they are well qualified to recommend and supervise the necessary repairs and procedures to get the TBM into a condition where it is able to finish this tunnel.
Having been in the TBM supply business for quite a few years, I unfortunately have to admit having been in a similar (fortunately not as well published) situation as the TBM supplier on more than one occasion. This situation–significant TBM problems at the beginning of boring—can result from many different factors and is not unique to the SR99 project. In fact, Robbins recently had a similar situation (admittedly on a smaller scale in terms of both public and financial impact) on a project in Turkey known as the Kargi HEPP. Despite extensive pre-planning, unexpected ground was encountered, which resulted in several in-tunnel stops and machine modifications in the first few hundred meters of the tunnel. What happens in these situations is you pull in the best minds with the most experience and immediately analyze the problem. The ultimate fix often ends up as a multi-level solution. You must ensure you have the problem under control, plus take additional measures to monitor the vulnerable components and operating procedures. At Kargi, this process resulted in the remainder of the project being finished without significant TBM problems. Without a doubt a similar process is going on at SR99 with Hitachi Zosen engineers, the contractor’s specialists, and the city’s board of experts.
Being one who is keenly interested in this project, I believe that this TBM will soon be back to boring with a new completion date, which will be fulfilled. I am optimistic that this project will one day be seen as a positive in the tunneling industry, where many lessons were learned and advancements were made. Such advancements will be put to use in Seattle and in other cities that greatly benefit from the excavation of more underground infrastructure.
A Tradition of Innovation: The 2013 Muir Wood Lecture takes a cue from Robbins’ Long History
When asked about his most memorable tunneling project, Dick Robbins narrowed it down to two: The Channel Tunnel and the Paris RER Metro. The former company president and CEO from 1958 to 1993 has seen hundreds of tunneling projects in his career, and should know. The Channel Tunnel, with its hybrid machines capable of operating under 10 bar water pressure, was challenging to say the least. But the Paris RER Metro in 1964 resulted in a radically unique machine design: “We created the world’s first below-water, pressure bulkhead shielded machine using air pressure. All future slurry and EPB designs had their genesis in this machine,” said Robbins. A sealing system using steel fingers back-supported with foam kept the gap between the machine shield and segments airtight. Wire brush seals with grease were not developed until later projects (see below).
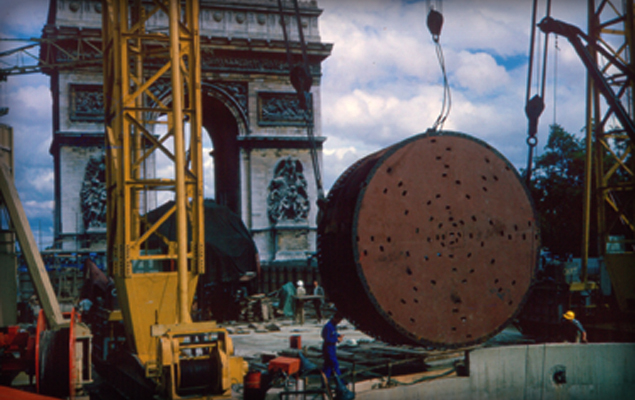
The central section of the Robbins machine at the Paris RER metro, with the Arc de Triomphe in the background.
These two projects are just a few of the highlights Dick Robbins is set to touch on during his 2013 Sir Alan Muir Wood Lecture, honoring the late tunneling statesman who initiated and served as the first president of the International Tunneling Association (ITA).
The talk, titled “A Tradition of Innovation: The Next Push for Machine Tunneling” will cover everything from the beginnings of mechanized tunneling to the era of modern tunneling when his father James S. Robbins came up with the idea of developing full-face TBMs (see picture below). Discussion will then move to modern-day marvels like the world’s largest TBM set to bore the Highway 99 Viaduct Replacement tunnel. Robbins will make the case that a culture of innovation is needed in greater force in order to push for new leaps in design that will accelerate the advancement of the industry.
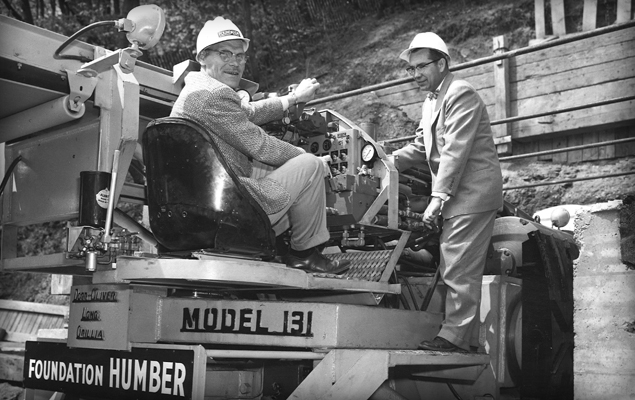
James S. Robbins (in driver’s seat), Robbins founder, at the launch of the Humber River Sewer TBM in 1956. The machine was the first ever to exclusively use rolling disc cutters.
See the Talk:
ITA-AITES World Tunnel Congress
Geneva, Switzerland
Opening Ceremony & Sir Alan Muir Wood Lecture
Monday June 3
9:00 AM to 10:30 AM
For more information on Robbins’ long history, check out the lecture Dick Robbins and colleagues made when he received the 2009 Benjamin Franklin Medal.
Salamanders, Pseudo Scorpions, and Quartz Crystals: How my Recent Site Visit proved that TBM Tunneling is the Greenest Way to Go
The Balcones Canyonlands just north of Austin, Texas, USA is a protected wildlife preserve, and it’s not open to the public. So when the city of Austin opted to build a 10.5 km (6.5 mi) long water line directly below it, there was understandably some concern—but not for humans. The inhabitants of the Canyonlands include some of the state’s most endangered species, from tiny, blind cave spiders to songbirds to the green-speckled Jollyville Plateau Salamander. And don’t forget the pseudo scorpions. The Jollyville Transmission Main, a pipeline planned to bring drinking water to the drought-ridden city, was designed deep below protected aquifers in chalk, up to 106 m (350 ft) down in limestone rock. This made tunneling the only option. But even so, how could the project avoid impacting such a sensitive environment?
When I visited the site in Autumn 2012, I got my answer. The contractor, Southland/Mole JV, is taking every precaution to mitigate impact, and they’ve been very successful thus far. An environmental consultant from the city is on the site daily, and routine inspections ensure that the minimally invasive tunnel is not encroaching on the habitat of the endangered animals.
Our guides for the visit, Kent Vest and John Arciszewski of Southland Contracting, took us to the 82 m (270 ft) deep Four Points Shaft first, which has been partially reinforced with liner plates. Kent and John explained that during excavation, water inflow from the aquifer had been high enough that the city opted to grout behind the liner plates to prevent further dewatering. Gravel in the annular space between the liner plates and shaft walls would keep any groundwater pathways intact.
As we descended into the unlined tunnel where a 3.25 m (10.7 ft) Robbins Main Beam TBM was averaging 55 m (180 ft) per day, we talked ground support—or the lack thereof. Three TBMs are being used to excavate portions of the tunnel in competent limestone. Southland is not permitted to do either pre-excavation drilling or grouting because of the possibility of karst cavities and groundwater pathways—areas where endangered aquatic species might live. While they plan to install wire mesh and rock bolts if it’s needed, the rock quality has so far been very good with little ground water. We took a few photos while in this tunnel (see below), and then moved on to the next site.
Our last site visit of the day was the deepest—the 106 m (350 ft) Jollyville shaft next to the similarly named Jollyville Reservoir in a much more urban location. Once we’d been lowered down the shaft, we found a small, unlined tunnel in competent limestone. A 3.0 m (9.8 ft), contractor-owned Double Shield TBM was tunneling this reach, after having been refurbished by Robbins in Solon, Ohio. Similarly, the machine was getting some fast advance rates of 46 m (150 ft) per day on average.
What I immediately noticed in this tunnel was the multitude of small, mostly dry karst cavities down the tunnel walls. These cavities could potentially be home to the blind cave spiders, though none had been found during tunneling and it was likely they wouldn’t live in such small voids. We noticed, during our ride on the muck train towards the machine, sparks of light emitting from these cavities. Once we stopped John reached into a cavity and pulled out a handful of quartz crystals. “These are all over, in all these cavities. You can take some with you,” he said. As I am part-pirate (my genealogy traces back to Sir Francis Drake on my mother’s side!), I decided to stuff my pockets with the sparkly crystals (i.e., treasure!). I had never seen anything like this before, but John explained that the minerals in the perched water in many of the pockets caused the crystals to grow. Since the pockets were small, they weren’t filled in or isolated and we could pluck quartz crystals to our heart’s content.
On a more serious note, Southland does have a plan of action if large cavities are found or if a groundwater pathway is very open and linked to the aquifer. In this case, large voids would be isolated and sealed off to protect the habitat within. If ground water inflows are severe they will install steel liner plates and grout behind them to stop the flow. But, says Southland, they don’t expect to encounter either of these since the tunnels are so far below the aquifer. In fact, one reach of the tunnel, already complete at the time of our visit, had encountered almost no groundwater in 1,300 m (4,400 ft) of tunneling.
Once back on the surface, it became clear to me that this well-designed project proved that tunneling, particularly TBM tunneling, could be used safely in even the most sensitive environments. The foresight, planning, and execution by the designers and contractors was impressive. The salamanders and pseudo scorpions thank you.
What is WIT, and Why Does it Matter?
“If going underground suits you, you are immediately hooked”; “Once I was exposed to the underground industry, I loved it”; “I fell in love with tunnel construction, and never left”. All of these statements came straight from women working in tunneling who were interviewed by TunnelTalk at NAT 2012. If tunneling is such a satisfying career path for women, why are so few females working in tunneling?
The lack of women may be attributed to lack of industry exposure and the male centricity of the field, Since its establishment, tunneling and underground construction has been primarily male-dominated. In recent years, the number of lady tunnelers has grown, and the need arose for a group to support this demographic. Women in Tunneling (WIT) was created by women for women with the purpose of providing networking opportunities to women from all corners of the tunneling world, and spreading the message of the exciting opportunities that accompany a career in the field.
The inaugural WIT networking event was hosted in conjunction with NAT 2012 in Indianapolis, IN, and took place at a popular Indy wine bar. Architects, consultants, editors, engineers, marketers, and writers were among the 27 attendees. Highlights of the two-hour event included a constructive roundtable discussion and a raffle with sponsor-supplied gifts.
All guests were excited about the future of the group, and eager to get additional women involved. The hope is to spread the word about WIT, and double the amount of attendees at the next event. Eventually, WIT would like to have events during all major North American trade shows. Interest internationally has been shown as well, and WIT looks forward to possibly expanding overseas.
WIT is not affiliated with any one company; it is an industry-supported group that aspires to grow the number of women in tunneling through networking and increased industry exposure. The group’s first event was hosted by The Robbins Company, and was entirely paid for by the generosity of sponsors Kiewit, Jacobs Associates, Arup and Bradshaw Construction Corporation.
As Natasha Taylor, one of the TunnelTalk interviewees and a civil engineer at Kiewit, said, “There are all the opportunities in the world [for women in the underground industry]”. Our market is thriving and there are countless possibilities for women who want a career in a challenging and dynamic business. We hope you’ll join us in supporting WIT, and the group’s goals of bringing women together and attracting additional women to the industry.
If you’d like to get involved with WIT and receive group updates, please join our LinkedIn group. To watch the videos referenced in this blog, visit the TunnelTalk YouTube channel.
Recent Posts
- Tunneling in Turkey: The Esme Salihli Railway
- Incredible India: Machines on the Move in Agra and Delhi
- Notice of Retraction and Apology
- Four Things You Need to Know about Probe Drilling and Pre-Grouting
- The Latest Updates: Records in Toronto, the News from Nepal, and More