Author: Roland Herr
The Brenner Base Tunnel: A European Core Project
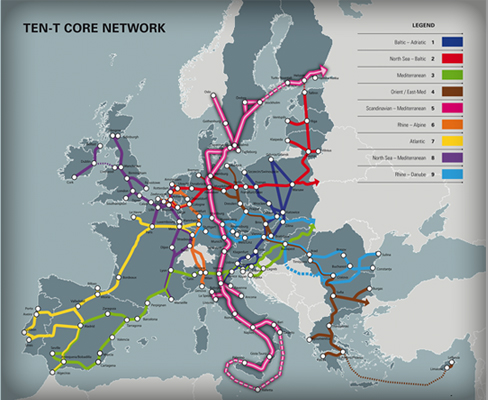
Figure 1. The Trans-European Network for Transport (TEN-T) aims to connect all European member nations from West to East and and North to South.
Tunneling is a worldwide business with often-changing markets. At the moment, everybody is watching the markets in Asia and in particular various huge projects in China and India, as well as the Middle East. With these busy hot spots, it’s easy to overlook projects elsewhere.
In this blog, I want to refocus and take a look at Europe, where there are some very interesting and challenging mega-projects underway for the Trans-European Network for Transport (TEN-T) of the European Union. The TEN-T connects all economies in the European Member Countries from West to East and North to South (Figure 1). This master plan for connectivity in Europe includes nine core network corridors with several projects crossing the borders of multiple European countries. The cross-border project implementation is complicated because of the different technical, financial and statutory requirements.
TEN-T core network projects
The core projects of the TEN-T master plan all serve as missing links that would connect the European Member Countries, like the Koralm and Semmering Railway Tunnels (both in Austria), Lyon-Turin Railway Project (connecting France and Italy), Fehmarn Belt Crossing (connecting Denmark and Germany), Brenner Base Tunnel (connecting Austria and Italy), Ceneri Base Tunnel (connecting Switzerland and Italy) and also some completed projects like the Oresund Bridge, Tunnel Road and Rail Fixed Link (connecting Sweden and Denmark), Milano-Roma-Napoli Railway (Italy), Gotthard and Lötschberg Base Tunnels (Switzerland), Betuwelijn Railroad (connecting the Netherlands and Germany) and the Channel Tunnel (connecting United Kingdom and France).
Financial support from the European Union in an amount estimated at 500 billion euro is required to complete this Trans-European Network and to widen some of the bottlenecks within it. The Brenner Base Tunnel is one of the most interesting cross-border projects and a core project of the TEN-T master plan (Figure 2).
Brenner Tunnel Conversations
The Brenner Base Tunnel (BBT) is a big challenge for all involved parties. In 2015, I had the great opportunity to interview Prof. Konrad Bergmeister, who has been the CEO of the BBT SE since August 2006 (Figure 3). Bergmeister was previously the technical director and head engineer of the company managing the Brenner Highway and was responsible for the planning and construction of new infrastructure and for maintenance of the existing structures. For the past 22 years, he has taught construction engineering at the University of Natural Resources and Applied Life Sciences in Vienna (Austria). He has been the President of the Free University in Bolzano (Italy) since 2010.
Interview with Prof. Bergmeister
Could you give me a brief overview of the Brenner Base Tunnel?
The Brenner Base Tunnel is a ground-breaking engineering project for the 21st century. This underground structure has a total length of 64 km and consists of three tubes: the exploratory tunnel and two main tubes with four lateral access tunnels connecting them together (Figure 4). The tunnel itself will become the longest railway tunnel in the world once complete.
The history of the tunnel is a long one: 160 years ago, an Italian engineer came up with the idea to go beneath the Brenner Pass. After World War Two, the project was reassessed but never proceeded. Finally, between 1987 and 1989 a feasibility study was carried out. The preliminary project was approved in 2002, and between 2005 and 2008 project details were worked out. In 2009 the environmental and technical approvals were obtained in Austria and in Italy. So we started with the first exploration of the whole rock situation in 2006, drilling vertical bore holes that totalled more than 28 km when we sum it all up. And this preliminary information was used in order to study the final layout of the tunnel in order to do the definitive design.
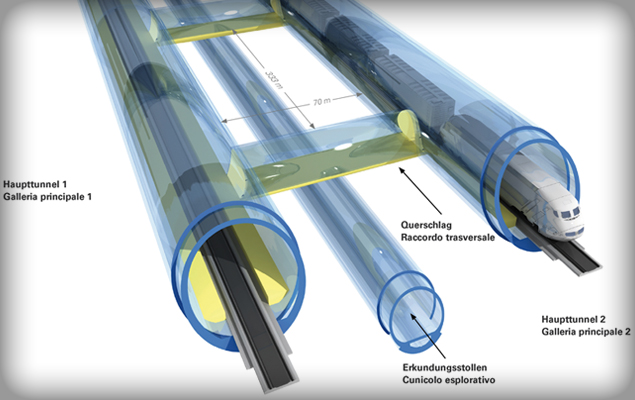
Figure 4. The 64 km long Brenner Base Tunnel consists of three tubes: An exploratory bore and two main tubes connected by access tunnels.
What, for an engineer, is the most challenging aspect of the Brenner Base Tunnel?
The most challenging issues for me are the following:
First of all we developed the so-called design guide in order to have the right basis to execute the design in both countries. This design guide was based on some new design ideas taking into account all the safety issues that have been proposed with the Eurocodes on a European level.
Second we developed internally a so-called chance and risk analysis, which should allow us to monitor the development of the project in terms of possible chances and risks. How we are doing that? Well we are trying to evaluate and double check the actual ongoing construction with our project managers and external experts and we are trying to identify all the possible risks and chances that might occur as tunneling proceeds. This analysis is part of a database that will be actualized on a yearly basis so we have additional information in terms of possible risks, additional costs, cost savings and scheduling.
The third issue is something that deals with some novel forecast technologies. We are using digital mapping and photogrammetric mapping as forecasting methods, particularly for the ongoing drill and blast operations. This is called the Tunnel Control System and is able to predict complex excavation shapes by using statistics regression analysis. It is based on 3D point clouds of the rock surfaces captured after each excavation, and the precision of previous excavated profiles is also analysed. The previous blasting data and the corresponding geological information are used for the prediction of the upcoming upper and lower blast profiles. For the forecast a certain number (minimum five previous blasts) is taken into account for a linear or nonlinear regression analysis. Through this optimization procedure up to 65% reduction in over-break has been achieved.
And the last issue is actually that we have been trying to develop ideas for the reuse of excavation material. The concrete mixture must be sustainable for the next 200 years since this is the lifetime of the tunnel. We have been studying the material of the exploratory tunnel (Figure 6), especially the schists, in the central zone of the project and we were able to modify the preparation methodology and optimize the concrete mixture to re-utilize 100% of the excavation material. Five years ago, all of the geologists and specialists during the approval phase told us that the excavation material must be disposed of. So this is actually a real step forward into optimizing the project excavation.
What is your opinion about the on-site TBM assembly of Robbins compared with the re-assembly of factory-built machines on jobsites?
From an engineering point of view we are only interested that the machine works very well on site. So we are interested to see, when the machine really starts, the performance in a certain excavation length. We are interested in the results and not so much on the specific assembly situation. There are different trade-offs: On the one hand, if you pre-assemble the machine in the production facility, this can guarantee you certain tolerances and probably certain pre-operation errors can be adjusted and finally avoided. But, the major problem is that you have to transport the semi-assembled machine on site and you have to re-assemble the machine on site again and then you have to start excavation. However, with Robbins for example, they can bring all the individual pieces on site and very often they are adjusting the machine itself directly under site conditions. It is easier, I think, to do the adjustment on site directly for specific logistics reasons. We can say that you might have more flexibility if you assemble directly on site compared with doing the assembly at the production facility.
Beyond Boring: A Journalist's Fascination with Tunnelling
About the Guest Author: Roland Herr has a background in civil engineering and is an international freelancing journalist. He has over 20 years of experience on engineering and construction projects all over the world, and is especially interested in tunneling.
Those working in tunnelling understand that this is an industry more fascinating than any other. What is it about tunnelling that makes it so exciting to those in the field?
Curious to know more, I discussed this question with some very experienced European tunnelling specialists: Frode Nilsen (Norway), Managing Director of LNS, and Dr.-techn. Klaus Rieker (Germany), Managing Director Tunnelling Division of Wayss & Freytag Ingenieurbau AG. Both conversations took place at different places and times, but with strikingly similar results.
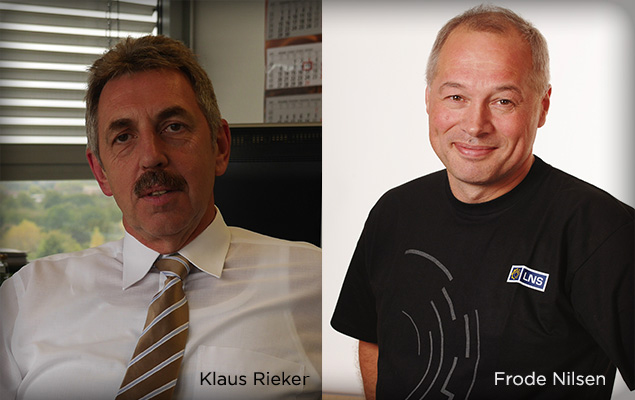
Dr.-techn. Klaus Rieker and Frode Nilsen took time to share their experiences in the tunnelling industry.
Frode and Klaus both have extensive backgrounds in the underground industry. Frode has been working with tunnels since he left university, the Norwegian Institute of Technology, in 1988, and Klaus has been building tunnels for 25 years. Comparatively, I am a “youngster” with 14 years of experience with tunnels and the tunnelling industry, but no less enthusiastic.
Read on for the results of my Q&A sessions with Frode and Klaus:
One characteristic shared by most tunnellers is that they work internationally, on many different projects with varying levels of responsibility. Tell me about your international experience.
Klaus: [At Wayss & Freytag] I was assigned to different projects in Singapore, Malaysia and Taiwan. As a young engineer working in Asia, it was very hard to gain acceptance, particularly because in the Asian culture, older people are typically responsible for project management. It was difficult to convince the contractor that I could handle it, but step-by-step I proved myself with my performance and knowledge. I remember with pleasure my time on a metro project in Singapore; altogether we had about 30 nations involved on the project. It was really amazing!
Frode: Our most impressive project [at LNS] was SILA for the Iron Ore company LKAB. We blasted 12 silos out of the rock and built a 600 m long unloading hall and a 2.8 km tunnel for iron transport from the silos to the harbour. Our most famous project was the Svalbard Global Seed Vault in Spitsbergen for the UN, where we built tunnels and 3 rock caverns in the permafrost with an even temperature of -18° Celsius to store samples of the world’s seeds.
For Frode, the timeline and longevity of underground projects is also an amazing feat worthy of note—tunnels can be built in difficult ground conditions over a period of years, but the hard work pays off in that many tunnels have a design life of 100 years or more.
Working in tunnelling also provides a unique perspective on emerging markets. Which countries or markets are currently experiencing rapid development when it comes to tunnel construction?
Frode: In Europe, Norway is one of the most interesting nations, especially for drill & blast, with hard competition and low prices. In Asia, China is on top, and South America is also growing, in particular with the mining industry in Chile. Much of the future of tunnelling lies in mining: studies show that in 2034 around 60% of mining will be done in underground mines. That means tunnels for access, ore haulage, and more.
Klaus: Germany is now no longer really a market for tunnelling, and in Central Europe tunnel construction is declining. Meanwhile, Asia is the growing market. In Singapore for example, 10 to 20 machines are running annually for the metro system extension. China and India are also huge markets right now. I find North America to also be an interesting market with many current and upcoming projects.
Every industry has its own set of challenges. What do you find most challenging about working in the tunnelling industry specifically?
Klaus: A defining characteristic of tunnellers is that we love a challenge. We thrive on new, very difficult situations that demand utilization of all our knowledge and problem-solving skills, in order to find the best technical solution.
Frode: Client demands can be challenging, and are often accompanied by environmental and technical limitations as well as financial constraints.I am happiest when projects are profitable and everybody involved is satisfied.
Frode and Klaus’ comments on their experiences led me to one overarching conclusion: engineers working in tunnelling are some of the world’s brightest and most experienced, with shared passions for overcoming difficult situations and ever-expanding their world views. For adaptable and driven engineers, the tunnelling industry offers a challenging yet rewarding career with job security, as projects and new markets continue to emerge globally.
Recent Posts
- Tunneling in Turkey: The Esme Salihli Railway
- Incredible India: Machines on the Move in Agra and Delhi
- Notice of Retraction and Apology
- Four Things You Need to Know about Probe Drilling and Pre-Grouting
- The Latest Updates: Records in Toronto, the News from Nepal, and More