Year: 2021
Turkish TBM Records, Twice Over
History has been made twice over at Turkey’s Eşme-Salihli Railway Tunnel where a 13.77 m (45.18 ft) diameter Robbins Crossover XRE TBM has set new world records for best day, week, and month in the 13 to 14 m (42.6 to 46 ft) diameter range. The machine broke all three records first in May with 25.3 m (83 ft) in one day, 117 m (383.8 ft) in one week, and 345.6 m (1,134 ft) in one month, then again in June with 28.5 m (93.5 ft), 133.2 m (437 ft), and 455.4 m (1,494 ft) respectively. The TBM, which sat in storage for seven years before being newly upgraded for this project, proves the robust durability of Robbins machines.
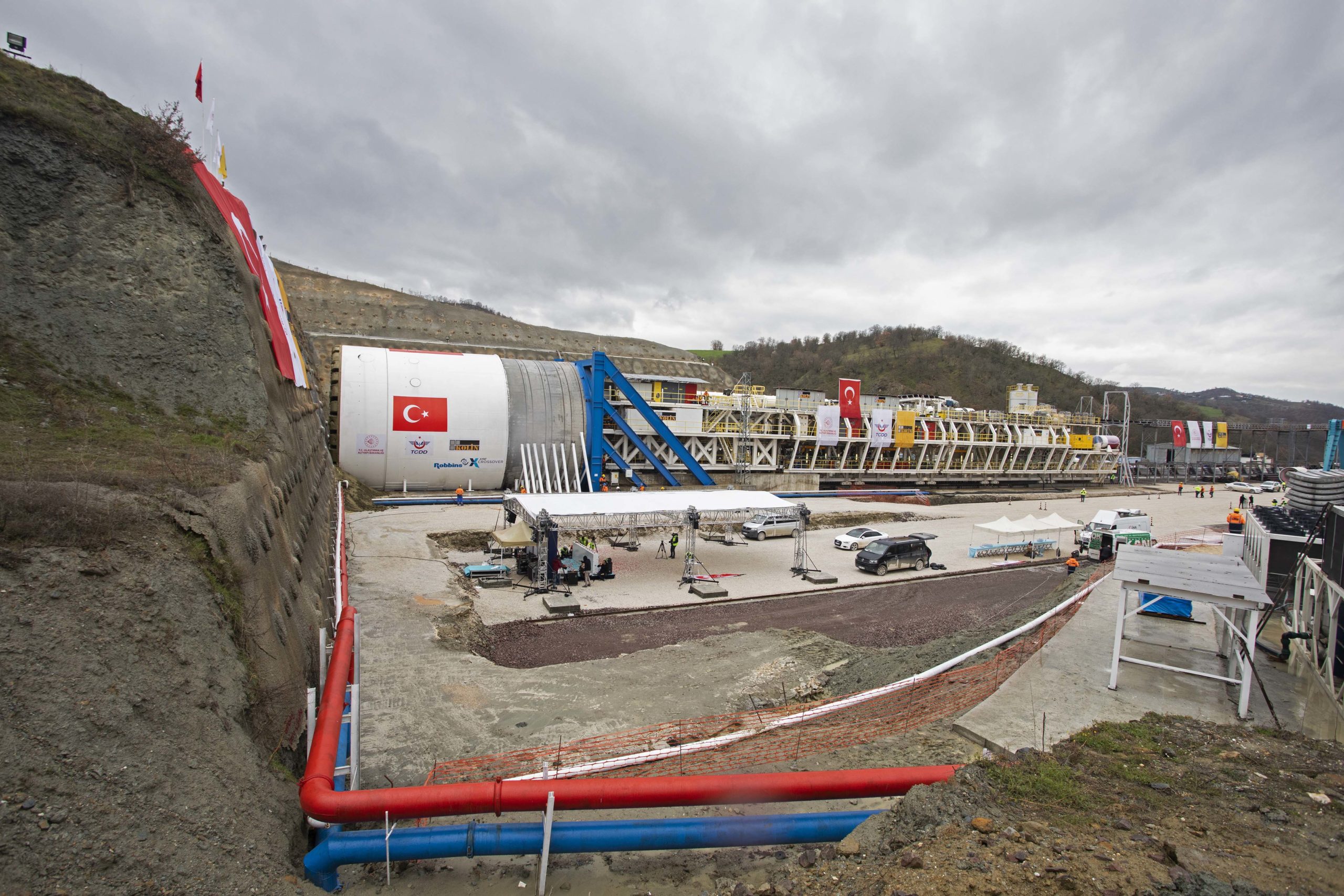
Thus far the Robbins machine has encountered a mix of mudstone and gneiss.
The Crossover TBM surpassed all previous performance rates by a machine in its size range. The closest another 13 to 14 m (42.6 to 46 ft) machine has come to these numbers was a 13.7 m (45 ft) diameter mixed ground TBM that achieved a 7 m (23 ft) average per day and a best day of 12 m (39 ft) at the Eurasia Tunnel project.
Onur Kansu, TBM Manager for project contractor Kolin Construction, attributes the machine’s success to the team operating it: “The most important reason for achieving fast advance rates is that we have an experienced and qualified team. If we open it up even further, such a team allows us to anticipate the malfunctions and to go to the solution in a very short time. In addition, all necessary maintenance is carried out on time, and the appropriate consumables are selected to increase the performance.”
The machine launched on its 3.05 km (1.90 mi) bore at the end of March 2021 as part of the Ankara-İzmir High Speed Railway Project for the Turkish State Railways (TCDD). Thus far the machine has encountered a mix of mainly mudstone with gneiss. “When we look at the overall tunnel geology,’ said Kansu, “we are excavating in complex and weak ground. In this geology, the advantages of the Robbins XRE TBM are highly favorable. The Robbins XRE TBM shows high performance in both complex and weak ground. It should also be noted that the TBM is very strong when looking at parameters such as torque and thrust.” To get through the challenging conditions, the large diameter XRE has a number of unique features. The large diameter design enables both a screw conveyor and belt conveyor to remain in place, enabling swift conversion between modes, and operation in full EPB and hard rock modes.
Regarding the future of the Turkish tunneling industry, Kansu is optimistic about the effects these new records will have: “It has been seen how well the engineers and application teams in Turkey have excelled in complex geologies and the large-scale tunneling industry. At the same time, it has shown to the whole world, especially Turkey, that with the right choices, it is possible to carry out excavations of this scale and complex geology without any problems and quickly. This project will be a pioneer in the Turkish tunneling industry, showing that faster and more economical tunnels can be built.”
Robbins XRE TBMs Cross the Finish Line in Massive Metro Project
In Spring 2021, the second of two 6.65 m (21.8 ft) diameter Robbins Crossover XRE TBMs made its third and final breakthrough for India’s Mumbai Metro Line 3. The first machine made its final breakthrough for the project in late April. The tunnel drives were a triumph for joint venture contractor Larsen & Toubro and the Shanghai Tunnel Engineering Company (L&T – STEC), as the crew and equipment overcame unpredictable terrain, high-pressure water ingress, and government-imposed lockdown orders during the Covid-19 pandemic.

The first of the Robbins Crossover machines broke through in April 2021.
The two custom-built machines were selected to bore parallel 2.9 km (1.8 mi) tunnels between the Cuffe Parade station and CST stations, breaking through into several station sites along the way. “It is the first time in India that Dual Mode, Crossover type TBMs equipped with a horizontal screw conveyor and high torque / high speed (two-speed) cutterhead drives were used. Overall, the performance of the Crossover TBMs was found satisfactory and we are in the process of shifting these TBMs for the L&T Chennai Metro project,” said Mr. Palwinder Singh, Head – Tunnel Construction for the L&T – STEC JV.
In another first for India, the Crossover TBMs employed a unique technique in a 554 m (1,820 ft) long section from Hutatma Chowk to CST stations. They were used in the benching of the NATM Platform tunnel through basalt rock (removal of the bottom section of rock remaining in the station after conventionally removing the top section). “This requires fine control on the operational parameters of the TBM because only 25% of the cutterhead is excavating the rock mass, while the remaining 75% of the cutterhead has no contact with rock or soil. In addition, the TBM was relaunched without using a reaction frame, instead taking reaction from half segments erected during the benching of the NATM Platform Tunnel. These innovative concepts were accomplished for the first time in India at Mumbai Metro Line-3, Package 1, and I therefore have many reasons to feel proud on the completion of tunneling,” said Singh.
L&T – STEC made impressive progress throughout tunneling despite the many exacting circumstances surrounding the scope of work. Above ground, the joint venture not only had to navigate the restrictions of working within an urban environment, such as limited work hours and the slow removal of muck due to minimal space and traffic, but also faced concern for major structures such as the Mittal Towers and the historic Bhikha Behram Well located along the tunneling route. The Crossover TBMs excavated with only 15 to 20 m (49 to 65 ft) of cover separating them from these important structures, which had to be instrumented to monitor vibrations, movements, and potential settlement.
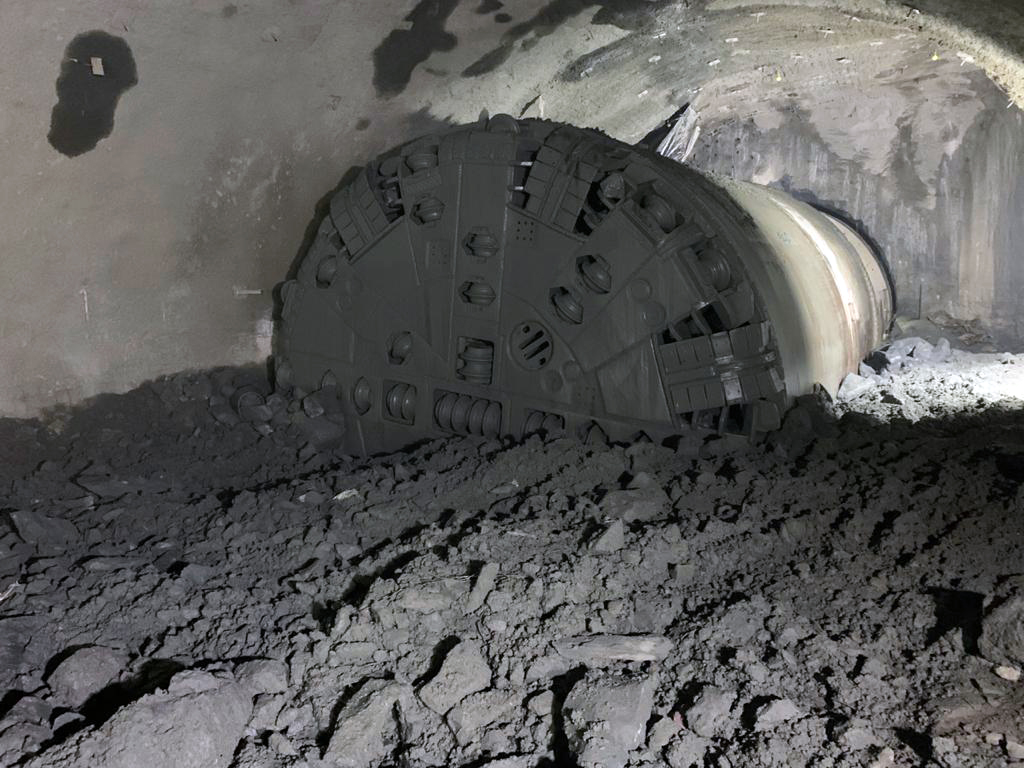
In a first for India, the Robbins Crossover TBMs were used in the benching of the NATM Platform tunnel through basalt rock in a 554 m (1,820 ft) long section from Hutatma Chowk to CST stations.
Underground, L&T – STEC faced a complex geological mix of fresh greyish basalt, soft volcanic tuffs, shale, and breccias—consolidated rocks of angular fragments of disintegrated volcanic rock. One of the biggest concerns, however, came from the tunnels’ proximity to the coastline of the Arabian Sea. During one point, TBM 1 was only 25 m (82 ft) from the coastline, with the invert level of the tunnel running approximately 22 m (72 ft) below mean sea level. As anticipated with circumstances such as these, the Crossovers faced a significant amount of groundwater with up to 300 liters/min during their excavation.
Despite these obstacles, the TBMs were still able to maintain impressive rates. TBM 2 even completed one push in a swift 14 minutes. “In fact, the boring rate of the Crossover TBMs was never an issue for us. It was only limited by the rate of muck removal and we could have finished the tunnels much faster,” said Singh.
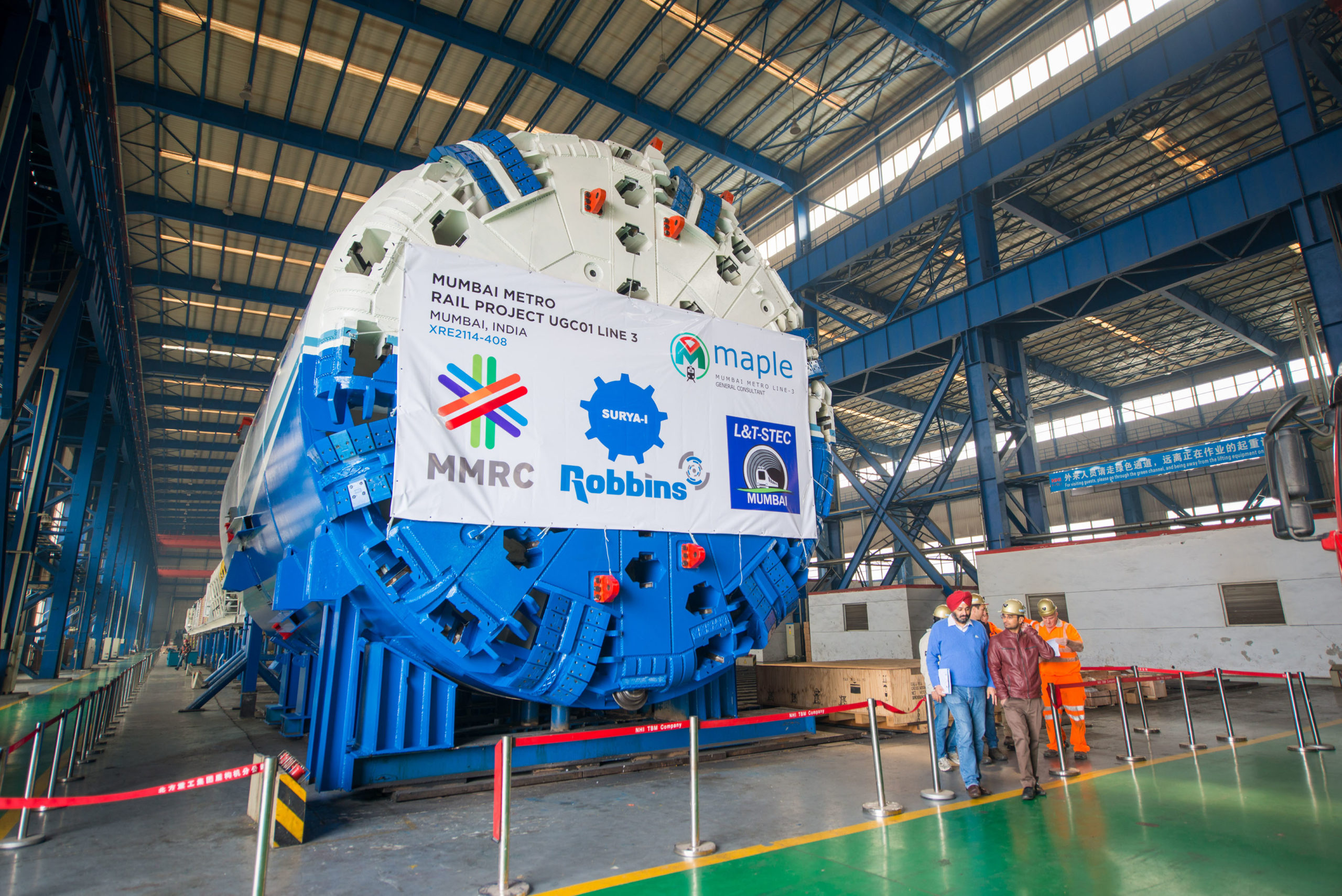
The Robbins Crossover TBMs were the first machines of their kind employed in India, using both a horizontal screw conveyor and high torque / high speed (two-speed) cutterhead drives.
L&T engineers were highly involved in the specifications and designs of the machines and worked closely with Robbins to prepare for the challenges the project presented. While L&T had extensive tunneling experience, tunneling with a Crossover machine was entirely new to them. To remedy this, Robbins provided a team of key personnel to train L&T in all aspects of the machines’ design and operation. “Working with Robbins field service was more than satisfactory. Even during the Covid-19 pandemic times, Robbins field service was available 24 hours a day, 7 days a week. What else can one expect?” said Singh.
Each milestone reached on this project is another step closer toward significantly improving the lives of Mumbai residents. As the financial capital of India and one of the most populated cities in the world, Mumbai is faced with an excessive amount of road traffic. It currently takes up to two hours to drive the 25 km (15 mi) distance from Cuffe Parade to the airport—the same trip on the finished metro will take a mere 50 minutes. The completion of Mumbai Metro Line 3, which is expected in 2025, will not only save residents transit time, but is expected to initially decrease road traffic in the area by 35%, reducing daily fuel consumption by 460,000 liters.
Cutting Edge 2021
Event Name: Cutting Edge Conference
Dates: November 15-17, 2021
Location: Dallas, Texas, USA
Come visit Robbins at the Cutting Edge Conference, and learn more about the largest hard rock TBM ever to operate in the USA at the Mill Creek Project. The 11.6 m (38.1 ft) diameter Robbins Main Beam TBM is excavating an 8 km (5 mi) long tunnel in Dallas, and is the conference’s main field trip. The annual Cutting Edge Conference examines the latest advances in tunneling technology, its methodology and how they can be harnessed to assist the nation’s major upcoming underground projects. Visit Robbins at our booth and talk to our experts with decades of experience on our latest projects and products.
The Utility Expo
Event Name: The Utility Expo 2021
Dates: September 28-30
Location: Louisville, Kentucky, USA
Venue: Kentucky Exposition Center
Booth: N1961
Covering more than 30 acres, The Utility Expo is the largest event for utility professionals and construction contractors seeking the latest industry technologies, innovations, and trends. Visit Robbins at our indoor booth N1961 and talk with our expert staff on our latest products and projects. We look forward to seeing you there!
Robbins XRE TBM bores Eşme-Salihli Railway Tunnel
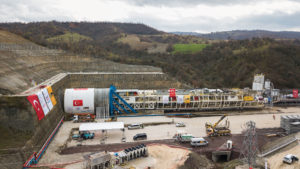
A Robbins Crossover machine is boring Turkey’s 3.05 km (1.90 mi) Eşme-Salihli Railway Tunnel through mixed conditions including sandstone, gravelstone, claystone, and siltstone for contractor Kolin Construction.
A Robbins 13.77 m (45.18 ft) diameter Crossover XRE TBM launched recently in spring 2021 in Eşme, Turkey. The large machine is boring the 3.05 km (1.90 mi) Eşme-Salihli Railway Tunnel through mixed conditions including sandstone, gravelstone, claystone, and siltstone. Contractor Kolin Construction expects some occasional groundwater and weak rock between 5 to 9 MPa (720 to 1,300 psi) UCS, with the potential for a gassy environment.
The titanic TBM was launched after more than seven years in storage, and following a few upgrades to systems to ensure they meet the newest safety and efficiency standards. “I am very happy that the TBM has been launched. Up to now, the machine has bored nearly 500 m (1,600 ft) in gneiss and mudstone. This is an opportunity for Robbins to prove that large diameter TBMs can bore in such tunnels, even in very complex geology and difficult ground conditions,” said Yunus Alpagut of ATES, Robbins’ Turkish subsidiary. Alpagut went on to explain why the project is so important: “Recently, there have been large diameter, non-Robbins machines that have failed at projects such as the high-speed railway in Bilecik, so this is very important to show the Turkish tunneling industry that large machines are up to the challenge.”
To get through the challenging conditions, the large diameter XRE has a number of unique features. The large diameter design enables both a screw conveyor and belt conveyor to remain in place, enabling swift conversion between modes, and operation in 100% EPB and hard rock modes.
In EPB mode, the screw conveyor operates as in any typical EPB machine. The screw features a replaceable inner liner and replaceable carbide wear bits for abrasion protection. A mixed ground cutterhead is fitted with knife bits that can be switched out with disc cutters in harder conditions. The machine design includes a man lock for cutterhead inspection and changes, and mixing bars inside the mixing chamber.
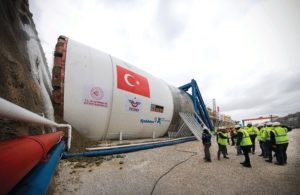
The large diameter Robbins Crossover TBM has bored nearly 500 m (1,600 ft) in gneiss and mudstone as of May 2021.
To convert to hard rock mode, the mixing bars and initial portion of the screw conveyor can be optionally retracted. EPB knife bits are then replaced with disc cutters on the cutterhead, and the EPB scrapers on the cutterhead are replaced with bucket lips. Muck paddles are installed in the cutterhead to allow the muck to fall into the muck chute. A hydraulic muck ring allows a chute attached to the bulkhead to move forward and down at a diagonal angle, allowing rock chips to be deposited in the chute and through the screw conveyor onto the TBM belt conveyor. To keep up production rates in both modes, the Robbins Torque-Shift System is used: a two-speed gearbox that enables efficient tunneling in hard, mixed, or soft ground.
The Eşme-Salihli Railway Tunnel is part of the Ankara-İzmir High Speed Railway Project for the Turkish State Railways (TCDD). The 508 km (316 mi) line will eventually connect Polatlı in Ankara Province to Izmir, the third most populous city in Turkey, surpassing the Istanbul-Ankara High-Speed Railway as the longest rail line in the country once complete. The double-track railway system will convey passengers at top speeds of 250 km/h (160 mph), completing the journey between the two cities in 3.5 hours—a journey that would normally take 6.5 hours by car.
BTS 2021
Event Name: BTS Conference and Exhibition
Dates: September 30-October 1
Location: London, UK
Venue: QEII Conference Centre
Stand: B26
Register for the British Tunnelling Society’s upcoming conference and learn about the industry’s latest trends with 800+ other tunneling professionals. Debate and analyze the latest trends and topics in underground construction, and be sure to check out the lecture by Robbins President Lok Home. Stop by our stand B26 to talk about the latest Robbins products and projects with our team of international experts.
Robbins Lecture Description
Thursday September 30
Session 3 – Innovation in Action
2:00 – 2:20 PM
Non-Circular Tunnelling: A New Way Forward – Lok Home, Robbins President
When a flat roadbed is needed, is a circular TBM the best way to go? In this exclusive presentation, Robbins President Lok Home will discuss methods and equipment currently being used in the mining industry for flat inverts, and its increasing potential for use in civil tunneling. Home will look at case studies in both mining and civil tunneling industries to demonstrate that by using non-circular TBMs, a flat invert can be safely and economically created in one pass.
The Green Alternative: Small Hydro Machines for Clean Energy
When you’re faced with a hard rock tunnel on your next small hydro project, which tunneling method works best? Intake tunnels can be at diameters as small as 2 meters and at steep grades of up to 45 degrees. Compared with the conventionally used method of Drill & Blast, small diameter tunneling machines offer increased production rates and reduction in cross section, among other benefits. The uniquely designed machines are engineered to take on steep gradients, and can bore tunnels kilometers long with minimal impacts to the surrounding environment.
In this complimentary, 60-minute webinar we discuss the use of small diameter tunneling machines on projects throughout Norway, where their popularity is increasing, as well as the method’s suitability on projects worldwide. Listen in on our conversation with Robbins Norway General Manager and Civil Engineer Sindre Log as we discuss recommendations for small hydro tunnels in hard rock. Join us for a live Q&A session at the end to get a thorough answer from our expert speaker.
Watch the Recording
Most Momentous: 2021 Global Project Updates
From China’s largest Crossover TBM launch to an epic 13.77 m diameter XRE that began boring recently in Esme, Turkey, we’ve compiled the year’s most momentous events thus far. Read on to find out about Robbins machines embarking on tunnels large and larger.
Twin Crossover TBMs for Chongqing
Two 6.91 m (22.6 ft) diameter XRE machines are currently boring sections of the Chongqing Metro Phase 2 in ground conditions ranging from weathered mixed granite to weathered pegmatite and adamellite. The twin machines are the first of their kind in China, and are part of a trend towards more geologically challenging tunnels in China. To date, the machines have achieved up to 365 m (1,197 ft) advance in one month, with rates expected to ramp up as the machines progress.
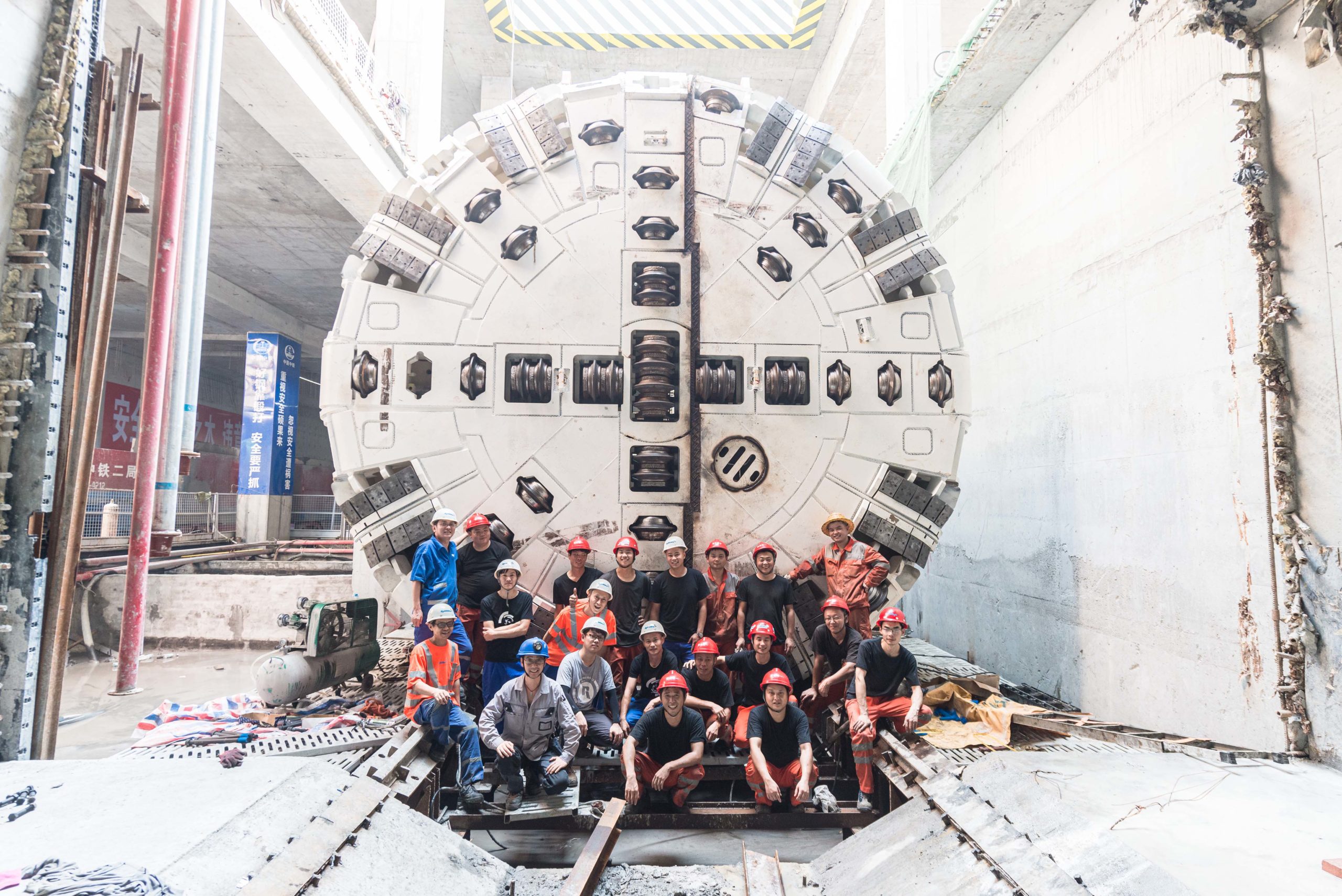
The team takes a moment to mark the assembly of one of two Robbins Crossover machines in Chongqing, China.
An Epic XRE Launch in Esme
In Esme, Turkey, a massive 13.77 m (45.2 ft) diameter Crossover XRE TBM began its bore for contractor Kolin Construction. Launched in late March 2021, the unique TBM is designed to tackle mixed ground conditions including sandstone, gravelstone, claystone and siltstone along the 3.05 km (1.9 mi) Esme-Salihli Railway Tunnel. The XRE can swiftly convert between hard rock mode using a belt conveyor and EPB mode using a screw conveyor, as both remain in place inside the machine.
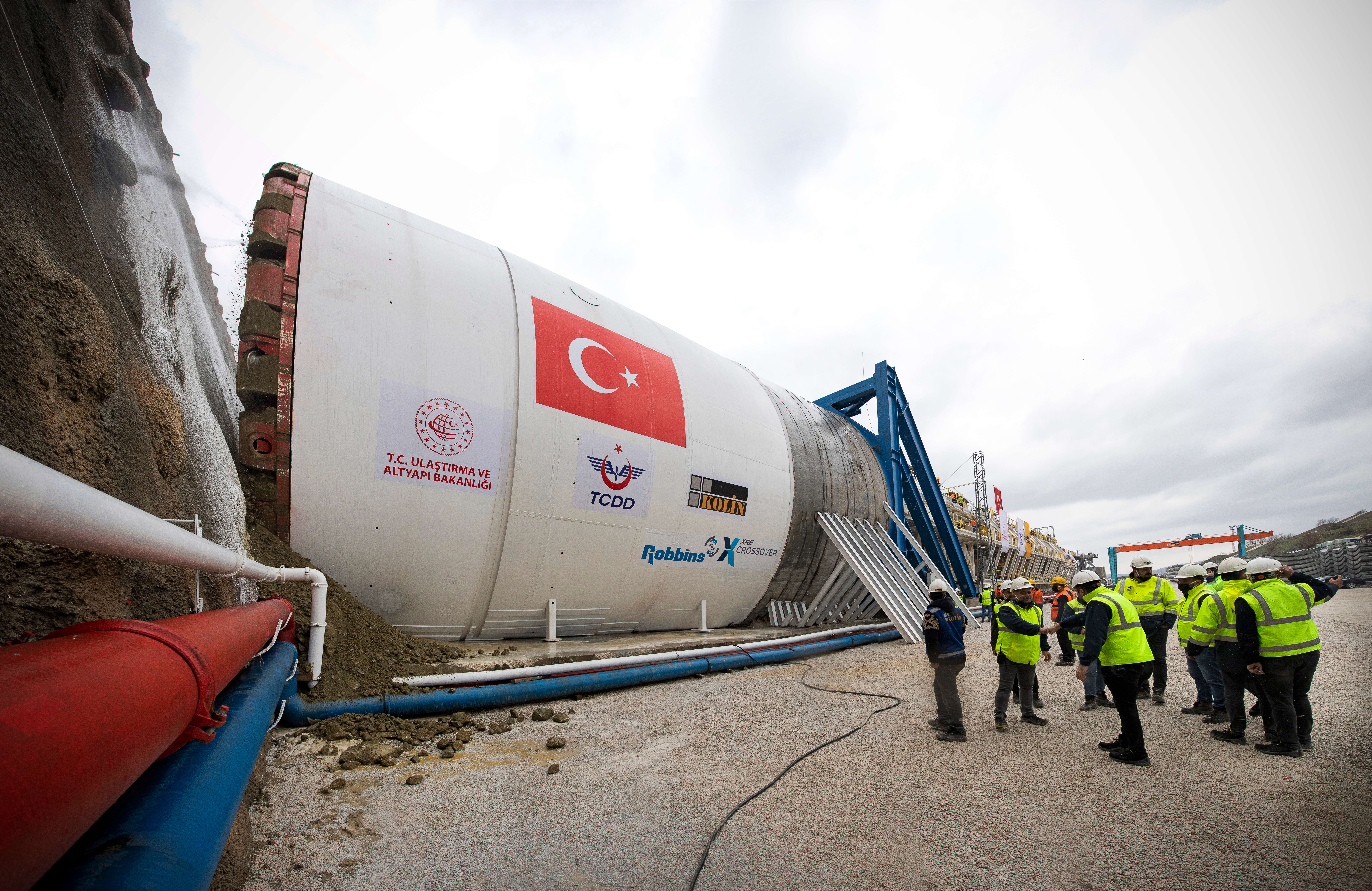
Launch of the 13.77 m diameter Robbins XRE TBM for Turkey’s Esme-Salihli Rail Tunnel.
Tunneling below Lake Ontario
A Robbins 7.95 m (26.1 ft) diameter Single Shield TBM launched recently on March 26th from an 85 m (280 ft) deep, 14 m (46 ft) diameter shaft. The machine, for the Ashbridges Bay Outfall with contractor Southland Holdings LLC in Toronto, ON, Canada has the task of boring a 3.5 km (2.2 mi) long tunnel below Lake Ontario. The completed tunnel will connect up to 50 in-lake risers to enable efficient dispersion of treated effluent over a wide area of the lake.
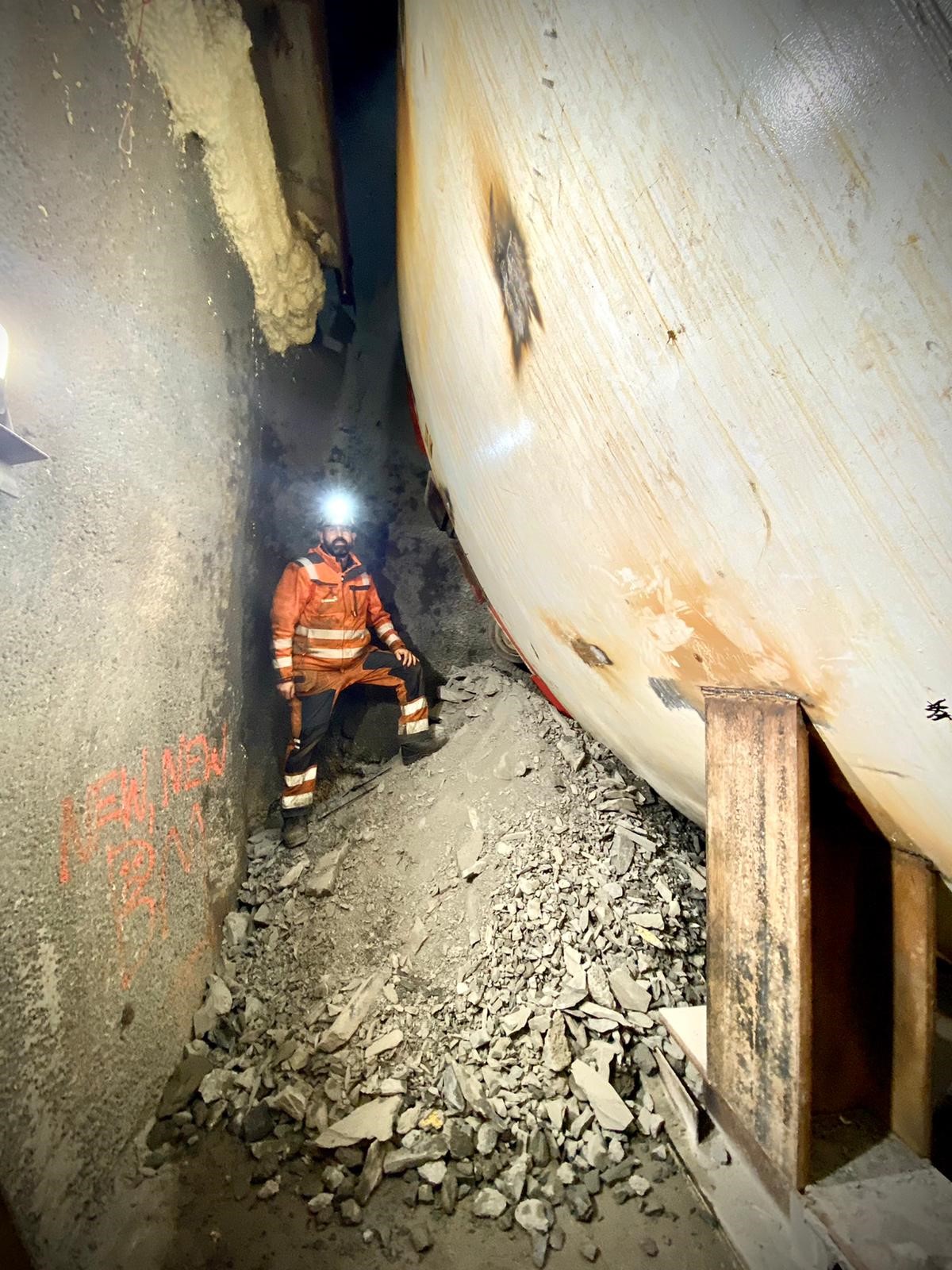
The Robbins Single Shield TBM for the Ashbridges Bay Outfall Tunnel launched on March 26, 2021. Photo: Alfredo Garrido
China’s Largest Crossover TBM
The largest ever Crossover (XRE) TBM in China launched in late March 2021 in Guangzhou for contractors Sichuan Jinshi Heavy Equipment Leasing Co., Ltd and CREC Bureau 2. Onsite First Time Assembly (OFTA) was utilized to build the 9.16 m (30 ft) diameter Robbins TBM, taking just four months from contract signing to machine launch. The hybrid machine is boring the 2.5 km (1.6 mi) long Pazhou Line Lot PZH-1 of the Pearl River Delta Intercity Railway Project, which will offer better commutes for Guangzhou residents traveling to and from University City.
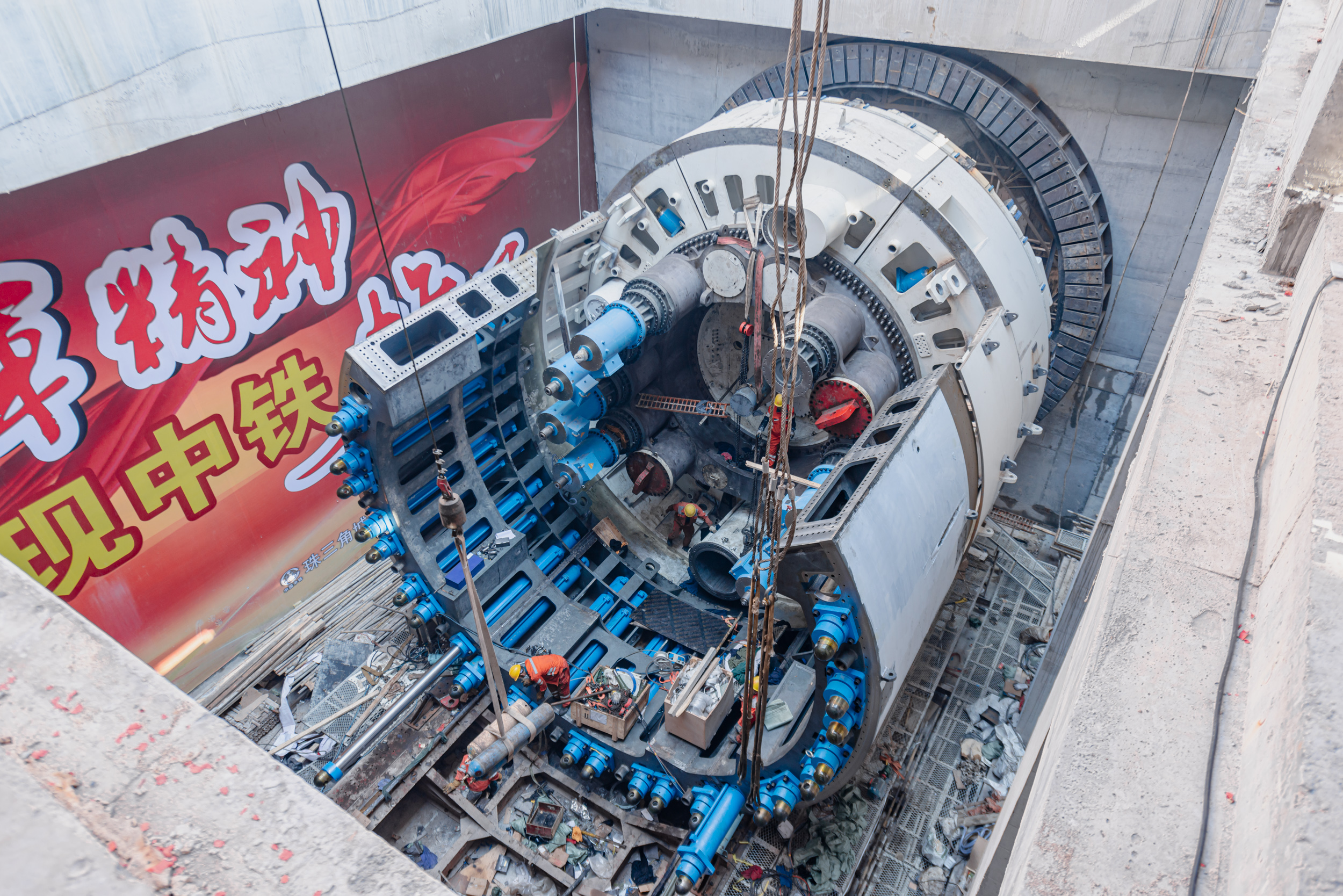
The Robbins Crossover XRE TBM at the Pearl River Delta site was assembled using Onsite First Time Assembly in just four months from contract signing.
China’s Largest Robbins Crossover TBM launches on Intercity Railway
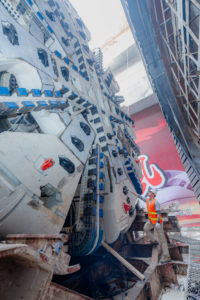
A crew member inspects the cutterhead of the Robbins Crossover XRE TBM during assembly in Guangzhou.
The largest ever Crossover (XRE) TBM in China launched in late March 2021 in Guangzhou for contractors Sichuan Jinshi Heavy Equipment Leasing Co., Ltd and CREC Bureau 2. Onsite First Time Assembly (OFTA) was utilized to build the 9.16 m (30 ft) diameter Robbins TBM, taking just five months from the start of assembly to machine launch. The hybrid machine is boring the 2.5 km (1.6 mi) long Pazhou Line Lot PZH-1 of the Pearl River Delta Intercity Railway Project, which will offer better commutes for Guangzhou residents traveling to and from University City.
The machine will encounter various ground types during its bore, from moderately to strongly weathered argillaceous shales and sandstone to mixed face conditions. Much of the rock is fractured, while the quartz content is as high as 50 percent. “Not only are there poor ground conditions such as soft to hard uneven, fractured zones and full-face hard rock, but these sections appear to alternate frequently, which is the biggest challenge of the project. It will be a test of performance and tunneling efficiency for the machine,” said Yongsheng Qi, Project Manager for Robbins China. The tunnel is also expected to cross under rivers and other bodies of water with a cover of 20 to 31 m (65 to 100 ft). The ground strata connects to the river and is highly permeable, resulting in expected water pressures above 7 bar. The project’s success lies in stabilizing the water pressure at the face while ensuring acceptable advance rates and construction safety.
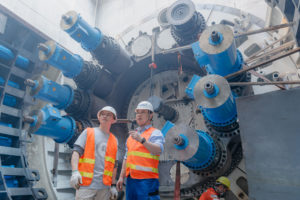
Onsite First Time Assembly (OFTA) of the Crossover XRE took just five months from start of assembly to launch.
The Crossover TBM features both hard rock and EPB modes and is optimized for the rapidly changing ground found on the project. An adaptable cutterhead design and two-speed gear reducers known as the Robbins Torque-Shift system enable efficient tunneling in hard, mixed, and soft ground. An adaptable screw conveyor can be mounted in the center or bottom of the mixing chamber depending on the mode. To combat high water pressures the machine is fitted with high pressure seals and can statically hold up to 30 bar. The XRE TBM began its excavation in EPB mode and will shift to hard rock mode to continue excavation after 1.5 km (0.9 mi) has been bored.
The unique project is one of several mixed ground operations using Robbins Crossover TBMs in China. Two 6.91 m (22.6 ft) diameter XRE machines are currently boring sections of the Chongqing Metro Phase 2 in ground conditions ranging from weathered mixed granite to weathered pegmatite and adamellite. The project is under the same contractors as the Pearl River Delta bore. “At the Chongqing Metro project, we won the trust of the contractor with the performance of the Crossover machines; to date the highest monthly advance rate in Chongqing is 365 m (1,197 ft). This is one of the main reasons the contractor again selected a Robbins Crossover TBM for the Pearl River Delta project,” observed Qi.
With rates at Chongqing Metro as a precedent, the Pearl River Delta tunnel is scheduled to be completed by the end of 2021 and put into operation in 2023.
Robbins enters a New Chapter
Global TBM Company, newly established by industry veteran Lok Home, is proud to announce the recent purchase of substantially all the assets of The Robbins Company. The company will operate as Robbins and with Mr. Home as the President and CEO. The acquisition will result in a seamless transition for a number of ongoing projects throughout the world, as Robbins renews its commitment to service, quality underground equipment, and top-notch support that its customers have come to expect. For a brief message from Lok Home, view the video here.
Home said the company has a bright future as a result of the transaction. We are starting off the new year with a respectable backlog of orders,” he noted. “In 2021 and beyond, our clients can depend on Robbins to deliver high quality machines, and technically superior machines for very difficult projects,” said Home. “That’s where Robbins really stands out.”
Home went on to say that Robbins is starting 2021 with no significant bank or institutional debt. “We have many projects to look forward to,” he continued. “Robbins is currently delivering Crossover machines and TBMs equipped for challenging geological conditions in many countries including the U.S., Norway, India, China and Canada.” The company’s conveyor and small boring machine divisions will also continue to deliver equipment worldwide.
Home emphasized that Robbins has always been focused on building the best and strongest machines. He pledged that they will continue to do that. “We still have our strong engineering team and we plan to continue our many industry involvements including the International Tunneling Association (ITA) and its associate member organizations. We’re glad to be a part of this community and this industry,” Home added.
The company expects to continue with exciting new developments as well, including a soon-to-be-unveiled non-circular rock boring machine. Robbins remains focused on creativity and innovation to solve the industry’s greatest challenges.
About Robbins
Robbins is one of the world’s foremost developers and manufacturers of advanced, underground construction machinery. Headquartered in Solon, Ohio, USA, Robbins is a total supply firm offering customized Tunnel Boring Machines, conveyors, cutters, and more, as well as knowledgeable field service personnel and technical support. The company has been an active industry participant and innovator for nearly 70 years.
From the first modern Tunnel Boring Machine built in 1952 to recent innovations such as the Crossover TBM for varied ground conditions, Robbins engineering and innovations have made a success of the world’s most difficult tunneling projects.