Author: Desiree Willis
A Tradition of Innovation: The 2013 Muir Wood Lecture takes a cue from Robbins’ Long History
When asked about his most memorable tunneling project, Dick Robbins narrowed it down to two: The Channel Tunnel and the Paris RER Metro. The former company president and CEO from 1958 to 1993 has seen hundreds of tunneling projects in his career, and should know. The Channel Tunnel, with its hybrid machines capable of operating under 10 bar water pressure, was challenging to say the least. But the Paris RER Metro in 1964 resulted in a radically unique machine design: “We created the world’s first below-water, pressure bulkhead shielded machine using air pressure. All future slurry and EPB designs had their genesis in this machine,” said Robbins. A sealing system using steel fingers back-supported with foam kept the gap between the machine shield and segments airtight. Wire brush seals with grease were not developed until later projects (see below).
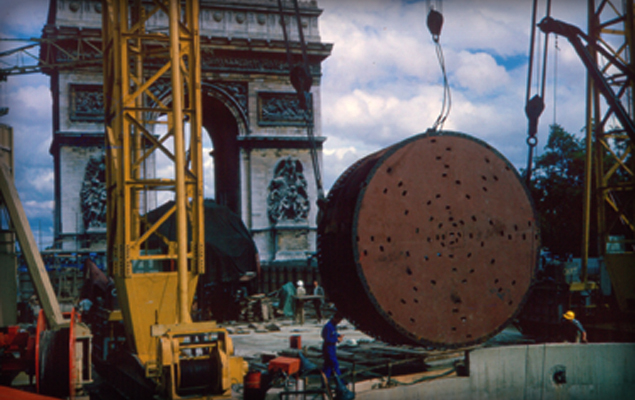
The central section of the Robbins machine at the Paris RER metro, with the Arc de Triomphe in the background.
These two projects are just a few of the highlights Dick Robbins is set to touch on during his 2013 Sir Alan Muir Wood Lecture, honoring the late tunneling statesman who initiated and served as the first president of the International Tunneling Association (ITA).
The talk, titled “A Tradition of Innovation: The Next Push for Machine Tunneling” will cover everything from the beginnings of mechanized tunneling to the era of modern tunneling when his father James S. Robbins came up with the idea of developing full-face TBMs (see picture below). Discussion will then move to modern-day marvels like the world’s largest TBM set to bore the Highway 99 Viaduct Replacement tunnel. Robbins will make the case that a culture of innovation is needed in greater force in order to push for new leaps in design that will accelerate the advancement of the industry.
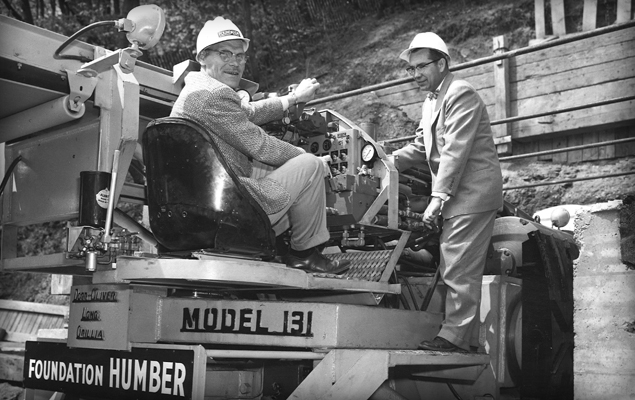
James S. Robbins (in driver’s seat), Robbins founder, at the launch of the Humber River Sewer TBM in 1956. The machine was the first ever to exclusively use rolling disc cutters.
See the Talk:
ITA-AITES World Tunnel Congress
Geneva, Switzerland
Opening Ceremony & Sir Alan Muir Wood Lecture
Monday June 3
9:00 AM to 10:30 AM
For more information on Robbins’ long history, check out the lecture Dick Robbins and colleagues made when he received the 2009 Benjamin Franklin Medal.
Salamanders, Pseudo Scorpions, and Quartz Crystals: How my Recent Site Visit proved that TBM Tunneling is the Greenest Way to Go
The Balcones Canyonlands just north of Austin, Texas, USA is a protected wildlife preserve, and it’s not open to the public. So when the city of Austin opted to build a 10.5 km (6.5 mi) long water line directly below it, there was understandably some concern—but not for humans. The inhabitants of the Canyonlands include some of the state’s most endangered species, from tiny, blind cave spiders to songbirds to the green-speckled Jollyville Plateau Salamander. And don’t forget the pseudo scorpions. The Jollyville Transmission Main, a pipeline planned to bring drinking water to the drought-ridden city, was designed deep below protected aquifers in chalk, up to 106 m (350 ft) down in limestone rock. This made tunneling the only option. But even so, how could the project avoid impacting such a sensitive environment?
When I visited the site in Autumn 2012, I got my answer. The contractor, Southland/Mole JV, is taking every precaution to mitigate impact, and they’ve been very successful thus far. An environmental consultant from the city is on the site daily, and routine inspections ensure that the minimally invasive tunnel is not encroaching on the habitat of the endangered animals.
Our guides for the visit, Kent Vest and John Arciszewski of Southland Contracting, took us to the 82 m (270 ft) deep Four Points Shaft first, which has been partially reinforced with liner plates. Kent and John explained that during excavation, water inflow from the aquifer had been high enough that the city opted to grout behind the liner plates to prevent further dewatering. Gravel in the annular space between the liner plates and shaft walls would keep any groundwater pathways intact.
As we descended into the unlined tunnel where a 3.25 m (10.7 ft) Robbins Main Beam TBM was averaging 55 m (180 ft) per day, we talked ground support—or the lack thereof. Three TBMs are being used to excavate portions of the tunnel in competent limestone. Southland is not permitted to do either pre-excavation drilling or grouting because of the possibility of karst cavities and groundwater pathways—areas where endangered aquatic species might live. While they plan to install wire mesh and rock bolts if it’s needed, the rock quality has so far been very good with little ground water. We took a few photos while in this tunnel (see below), and then moved on to the next site.
Our last site visit of the day was the deepest—the 106 m (350 ft) Jollyville shaft next to the similarly named Jollyville Reservoir in a much more urban location. Once we’d been lowered down the shaft, we found a small, unlined tunnel in competent limestone. A 3.0 m (9.8 ft), contractor-owned Double Shield TBM was tunneling this reach, after having been refurbished by Robbins in Solon, Ohio. Similarly, the machine was getting some fast advance rates of 46 m (150 ft) per day on average.
What I immediately noticed in this tunnel was the multitude of small, mostly dry karst cavities down the tunnel walls. These cavities could potentially be home to the blind cave spiders, though none had been found during tunneling and it was likely they wouldn’t live in such small voids. We noticed, during our ride on the muck train towards the machine, sparks of light emitting from these cavities. Once we stopped John reached into a cavity and pulled out a handful of quartz crystals. “These are all over, in all these cavities. You can take some with you,” he said. As I am part-pirate (my genealogy traces back to Sir Francis Drake on my mother’s side!), I decided to stuff my pockets with the sparkly crystals (i.e., treasure!). I had never seen anything like this before, but John explained that the minerals in the perched water in many of the pockets caused the crystals to grow. Since the pockets were small, they weren’t filled in or isolated and we could pluck quartz crystals to our heart’s content.
On a more serious note, Southland does have a plan of action if large cavities are found or if a groundwater pathway is very open and linked to the aquifer. In this case, large voids would be isolated and sealed off to protect the habitat within. If ground water inflows are severe they will install steel liner plates and grout behind them to stop the flow. But, says Southland, they don’t expect to encounter either of these since the tunnels are so far below the aquifer. In fact, one reach of the tunnel, already complete at the time of our visit, had encountered almost no groundwater in 1,300 m (4,400 ft) of tunneling.
Once back on the surface, it became clear to me that this well-designed project proved that tunneling, particularly TBM tunneling, could be used safely in even the most sensitive environments. The foresight, planning, and execution by the designers and contractors was impressive. The salamanders and pseudo scorpions thank you.
There are Urgent Projects…and Then There’s Emisor Oriente
After visiting Mexico City’s Emisor Oriente Wastewater Tunnel, I realized something: there are urgent projects, and then there are URGENT PROJECTS. Túnel Emisor Oriente, often abbreviated to TEO by those involved, is the latter. We visited the site in 2011 to see the assembly of an EPB and learn about why the project is so important.
Day 1
On a good day with light traffic, the jobsite is about an hour’s drive away from the Distrito Federal, the downtown zone of Mexico’s capital city. Our first day, I noticed how the high rise buildings and restaurants slowly dissolved into ramshackle huts as we drove further from the city to an area known as Ecatepec. Approaching the site, we crossed a bridge in our SUV that spanned an extremely slow moving grayish brown river (more about this soon).
It was a warm day in June, Mexico’s rainy season, which is quite different from the rain in my home town of Seattle in the U.S. Each day during the rainy season, the morning dawns sunny and warm–but by 4:00 in the afternoon a torrential downpour begins. The water floods city streets throughout Mexico City, whose storm drains can’t handle the sudden inundation. Sometimes the rain only lasts a few minutes, and sometimes it goes for longer. The water eventually runs into rivers like the one we crossed by the jobsite, creating flooding risks.
We exited our SUV at the Lot 1 shaft and were greeted by several Robbins Field Service guys, including our Field Service Manager for the Americas, Jeremy Pinkham. I was excited to learn more about the TEO project, where we have three EPB machines among six TBMs that are excavating an epic 62 km (39 mi) long wastewater tunnel. The tunnel will feed into the country’s largest water treatment plant, which is currently being built.
As Jeremy and the group walked towards the shaft to be lowered down the elevator, I was struck by a smell—something akin to a vast field of poorly maintained port-a-potties. I asked Jeremy about the Robbins machine, which was originally intended for Lot 5 but had been fast tracked to bore part of the tunnel section at Lot 1. I was wondering why this particular section had been deemed top priority. “Did you see that river just a few meters away from our jobsite?” he asked. “Most rivers, when you throw a stone in, it splashes or skips and then sinks. This one, you throw a stone in and it just goes ‘plop’, then sits there.” It was only then that I realized that this “river” was El Gran Canal, Mexico City’s infamous open sewer originally commissioned in 1910 by President Porfirio Díaz.
The Robbins guys as well as engineers from the Lot 1 contractor Ingenieros Civiles Asociados (ICA) then explained to me that the canal in this section, lined with shacks, was prone to flooding during each rainy season due to a loss of its slope. The effects on the people and infrastructure were severe, so the National Water Commission (CONAGUA) had fast-tracked Lot 1. A pumping station would be put in and the first section of tunnel sealed off so that wastewater from this area could be pumped into a section of the canal downstream that still maintained its negative slope. I was beginning to realize the importance and urgency of this project!
The guys gave us a tour of the TBM being assembled at the bottom of the shaft, which was specially designed for high pressure conditions under the water table.
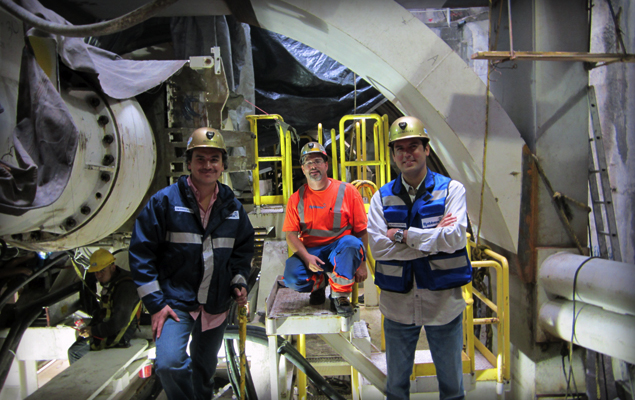
Robbins employees on the Lot 1 EPB. From left to right: Andrei Olivares, Robbins Project Engineer; Jeremy Pinkham, Field Service Manager – The Americas; Roberto Gonzalez, General Manager, Robbins Mexico
On the ride home that day we were hit by a particularly nasty rainstorm that went on for several hours. I learned via the local news later on that the very roads we had driven on to get to the jobsite were now flooded with wastewater and impassable—apparently a regular yet extremely concerning event.
Day 2
The next day we went to CONAGUA’s offices to speak with José Miguel Guevara, General Supply Coordinator for Potable Water and Sanitation. He spoke with us about the massive scope of Emisor Oriente—a project that could improve the lives of over 20 million people in the area by increasing wastewater capacity by 20% during each rainy season. The new pipeline will bolster current wastewater lines (both El Gran Canal and Emisor Central—a pipeline built in 1964) that have lost their slope due to Mexico City’s sinking lake clays.
While Guevara was optimistic, he admitted that health problems caused by El Gran Canal were numerous for the people living on its banks. When asked about future plans, he expressed grave concern that funds were not currently sufficient for a covered option to the open waterway. “At this moment,” said Guevara, “The Valley of Mexico is vulnerable. Our new treatment plant will treat 60% of the area’s water, but we need more alternatives as well. We are working on pieces to the problem, but the problem is not solved yet.”
With Emisor Oriente scheduled to be complete in 2014, I am hopeful that at least some of those problems will be alleviated. This is a great example of the magnitude that civil engineering works have on societies. I for one am proud that Robbins has a part in this monumental solution to an age old problem.After visiting Mexico City’s Emisor Oriente Wastewater Tunnel, I realized something: there are urgent projects, and then there are URGENT PROJECTS. Túnel Emisor Oriente, often abbreviated to TEO by those involved, is the latter.
Day 1
On a good day with light traffic, the jobsite is about an hour’s drive away from the Distrito Federal, the downtown zone of Mexico’s capital city. Our first day, I noticed how the high rise buildings and restaurants slowly dissolved into ramshackle huts as we drove further from the city to an area known as Ecatepec. Approaching the site, we crossed a bridge in our SUV that spanned an extremely slow moving grayish brown river (more about this soon).
It was a warm day in June, Mexico’s rainy season, which is quite different from the rain in my home town of Seattle in the U.S. Each day during the rainy season, the morning dawns sunny and warm–but by 4:00 in the afternoon a torrential downpour begins. The water floods city streets throughout Mexico City, whose storm drains can’t handle the sudden inundation. Sometimes the rain only lasts a few minutes, and sometimes it goes for longer. The water eventually runs into rivers like the one we crossed by the jobsite, creating flooding risks.
We exited our SUV at the Lot 1 shaft and were greeted by several Robbins Field Service guys, including our Field Service Manager for the Americas, Jeremy Pinkham. I was excited to learn more about the TEO project, where we have three EPB machines among six TBMs that are excavating an epic 62 km (39 mi) long wastewater tunnel. The tunnel will feed into the country’s largest water treatment plant, which is currently being built.
As Jeremy and the group walked towards the shaft to be lowered down the elevator, I was struck by a smell—something akin to a vast field of poorly maintained port-a-potties. I asked Jeremy about the Robbins machine, which was originally intended for Lot 5 but had been fast tracked to bore part of the tunnel section at Lot 1. I was wondering why this particular section had been deemed top priority. “Did you see that river just a few meters away from our jobsite?” he asked. “Most rivers, when you throw a stone in, it splashes or skips and then sinks. This one, you throw a stone in and it just goes ‘plop’, then sits there.” It was only then that I realized that this “river” was El Gran Canal, Mexico City’s infamous open sewer originally commissioned in 1910 by President Porfirio Díaz.
The Robbins guys as well as engineers from the Lot 1 contractor Ingenieros Civiles Asociados (ICA) then explained to me that the canal in this section, lined with shacks, was prone to flooding during each rainy season due to a loss of its slope. The effects on the people and infrastructure were severe, so the National Water Commission (CONAGUA) had fast-tracked Lot 1. A pumping station would be put in and the first section of tunnel sealed off so that wastewater from this area could be pumped into a section of the canal downstream that still maintained its negative slope. I was beginning to realize the importance and urgency of this project!
The guys gave us a tour of the TBM being assembled at the bottom of the shaft, which was specially designed for high pressure conditions under the water table.
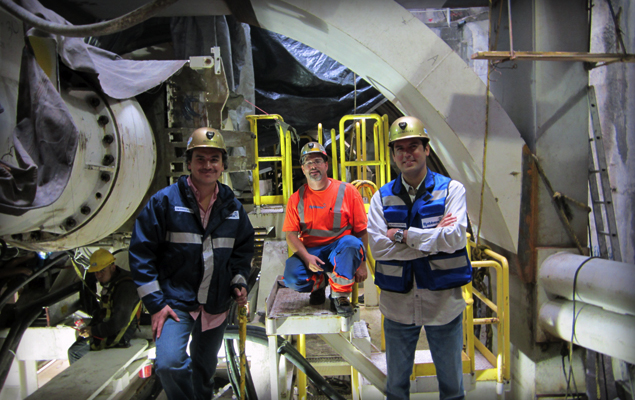
Robbins employees on the Lot 1 EPB. From left to right: Andrei Olivares, Robbins Project Engineer; Jeremy Pinkham, Field Service Manager – The Americas; Roberto Gonzalez, General Manager, Robbins Mexico
On the ride home that day we were hit by a particularly nasty rainstorm that went on for several hours. I learned via the local news later on that the very roads we had driven on to get to the jobsite were now flooded with wastewater and impassable—apparently a regular yet extremely concerning event.
Day 2
The next day we went to CONAGUA’s offices to speak with José Miguel Guevara, General Supply Coordinator for Potable Water and Sanitation. He spoke with us about the massive scope of Emisor Oriente—a project that could improve the lives of over 20 million people in the area by increasing wastewater capacity by 20% during each rainy season. The new pipeline will bolster current wastewater lines (both El Gran Canal and Emisor Central—a pipeline built in 1964) that have lost their slope due to Mexico City’s sinking lake clays.
While Guevara was optimistic, he admitted that health problems caused by El Gran Canal were numerous for the people living on its banks. When asked about future plans, he expressed grave concern that funds were not currently sufficient for a covered option to the open waterway. “At this moment,” said Guevara, “The Valley of Mexico is vulnerable. Our new treatment plant will treat 60% of the area’s water, but we need more alternatives as well. We are working on pieces to the problem, but the problem is not solved yet.”
With Emisor Oriente scheduled to be complete in 2014, I am hopeful that at least some of those problems will be alleviated. This is a great example of the magnitude that civil engineering works have on societies. I for one am proud to have a part in discussing this monumental solution to an age old problem.
The Oldest Robbins TBM still in Action? We visit a jobsite in Canada that may be using the World’s Ultimate Workhorse TBM
It’s a long-standing question in the world of tunneling: Which TBM has been operating the longest? What makes it so durable?
In May 2011, I visited the site of the Centennial Parkway Sanitary Sewer Tunnel in Hamilton, Ontario, Canada to find some answers. The rock portion of the tunnel, located in the shale of the Niagara Escarpment, is being bored by a Robbins Main Beam TBM in operation since 1968. The 2.7 m (8.8 ft) diameter machine was first used for a Hydroelectric Tunnel in Tasmania, and is now owned by McNally Construction, who has used it on multiple sewer tunnels in Toronto and Ottawa since 1972.
I arrived at the Centennial Parkway site on a sunny Friday afternoon along with Tunnels & Tunnelling North America editor Nicole Robinson, where we were greeted by McNally Project Sponsor Dave Bax and Field Technician Kenny Baxter.
After giving us some safety instructions, we were handed full rubber suits and boots. “You’re going to need these,” said Kenny. “It’s muddy on the shaft floor, and the material is red. It gets everywhere.” A quick look around the jobsite confirmed his statement—red clay-like material caked nearly everything, from trailers to trucks to boots.
We climbed down a long ladder into the shaft, and were given a tour of the small diameter tunnel. Kenny explained that the ring beams and wooden lagging installed at the tunnel entrance were due to the softer clay material encountered at that point. The rest of the rock portion of tunnel was being supported with rock bolts and steel straps. “The shale material is being recycled to use as brick. The clay was used by a local gun club for berms on their grounds.”
Single track muck cars rolled out as we walked out of the tunnel, carrying more heaps of reddish shale, before they were lifted by a crane and dumped on the surface.
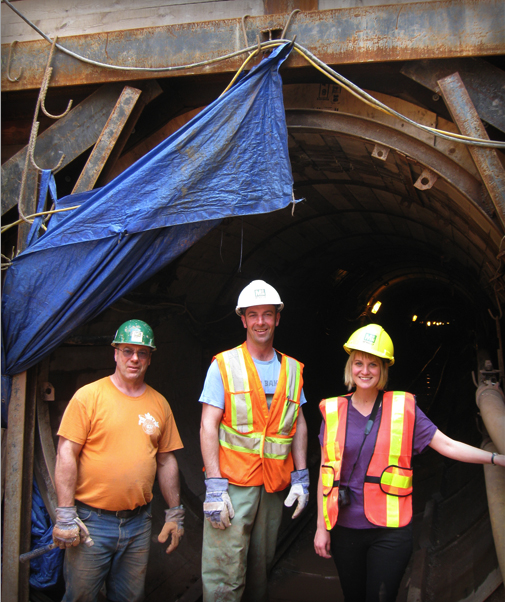
From left to right: Mark Walker, Laborer; Kenny Baxter, Field Technician; Nicole Robinson, T&T N. America, at the tunnel entrance.
Bax and Kenny mentioned that daily maintenance shifts have helped keep the veteran machine in good working order. Crews regularly check the 12-inch (304 mm) diameter disc cutters, and inspect the cutterhead and critical sub-systems. “We are not expecting a lot of wear. Our estimated completion for this tunnel is about two months,” said Bax. At the time of our Centennial visit, the TBM had advanced 200 m, at 1.8 to 2.1 m (6.0 to 7.0 ft) per hour, with no major issues.
The competent shale rock is certainly also a factor in limiting wear to the machine’s cutterhead and main bearing. Robust core components, including the main beam and gripper system, are key in keeping a TBM running for a long time (43 years, in this case).
Overall, the machine looked to be well equipped for its latest tunnel drive, and though it is impossible to know if it’s the world’s oldest working Robbins machine, it is certainly on the list. If you know of a Robbins machine that’s been operating longer, drop us a line in the comments section. We’d be interested to hear about it, and maybe even visit it!
Visiting Mexico City’s Newest Metro Tunnel: How the Country’s Capital is Upgrading its Aging Infrastructure
I was lucky enough to visit the jobsite of the Mexico City Metro Line 12 tunnel in October, along with Tunnels & Tunnelling International’s features editor Nicole Robinson. The country’s largest TBM, a 10.2 m (33.5 ft) diameter Robbins EPB, is excavating Mexico’s first new rail route in 10 years, below southern areas of the city. The 7.7 km (4.8 mi) long Mexico City Metro Line 12 is being excavated just 7 m (23 ft) below downtown areas in mixed ground including watery clay and boulders up to 800 mm (32 in) in diameter. The project is one of two major tunnels being constructed in Mexico City, the other being the 62 km (39 mi) long Emisor Oriente wastewater project, using six TBMs including three 8.93 m (29.3 ft) diameter Robbins EPBs.
During our visit to the site, the machine was between its first and second cut and cover station sites (it will hole through into seven such sites during the course of tunneling). We walked through the tunnel to view the machine, and later sat down with metro director Enrique Horcasitas of the Mexican Federal District for an interview on the current state of tunneling in Mexico.
Interview with Metro Director Enrique Horcasitas
Q: Were other methods besides tunneling with an EPB TBM considered for this tunnel?
A: Originally, the line was envisioned to be constructed using a technique of slurry walls cast in place. Most of Mexico City’s underground lines were built using this method. However, opening and closing city streets was not possible for a large portion of this route, while open cutting would interfere with existing municipal facilities and fragile archeological sites. In addition, cost estimates placed open cut excavation of the entire 24 km (15 mi) line at 19.5 billion pesos (USD $1.57 billion).
Our engineers needed a solution that would reduce risks and adverse impacts to traffic flow, as well as reduce project cost. For several weeks, methods were studied, and it was ultimately determined that a solution using multiple methods would work best. The 7.7 km (4.8 mi) long tunnel between Mexicaltzingo and Mixcoac would be excavated using a mixed ground EPB TBM, while the rest of the line between Atatonilco and Tláhuac, in much more difficult ground, would be constructed on the surface. Smaller portions of the tunnel would be constructed using cut and cover methods. The overall plan has a budget of 17.58 billion pesos (USD $1.41 billion).
Q: What does the city forecast for future ridership?
A: In the short term, it is expected this project will meet an average demand of 437,000 users per weekday. By 2030, this number is expected to grow to 600,000 users.
Q: How was the route of this line determined?
A: There is a long history associated with Mexico City’s metro plan. Engineers used to think it was impossible to excavate underground, given Mexico City’s highly complex geology. But in the 1950s and 60s, crews hand-mined the city’s main wastewater line, Emisor Central, about 100 m (330 ft) below ground. After the encouraging results, about 41 years ago, the project’s current contractor ICA (Ingenieros Civiles Asociados) began to make feasibility studies about metro lines running through the city. ICA was contracted to excavate the capital’s first metro lines, and 10 years later ICA gave the Federal District a gift: A master plan with over 300 km (185 mi) of rail that would serve as our template for decades to come.
The master plan is reviewed every 10 years, and it was most recently determined to build Line 12. The alignment is almost entirely true to the master plan, though it was made a bit longer after being reviewed by advisors, to match public demand for transportation.
Q: Are there any other metro expansions that the city is considering?
A: We are looking at doing an extension of the new Line 12, depending on the available budget. This extension would include 1,400 m (4,600 ft) of tunnels west of Mixcoac.
The next line we are considering in the master plan is Line 15, which would run directly below Insurgentes, the longest avenue in the world (18.8 km/11.7 mi), which goes straight through the city. A metro is absolutely needed on this route, as there are currently about 10,000 people per hour riding on just buses alone in each direction.
Q: Do you think current opinion about TBMs is changing in Mexico? What is the current climate towards TBMs?
A: I think the public can see the success of this tunnel—we arrived into the first station with precision, only 1 cm (0.4 in) to the side. We are monitoring settlement, and have detected only about 2 cm (0.8 in) at maximum—well within the limits and not enough to affect buildings. The public voted on where to excavate the next new line, they decided where to go, and so there is a consensus in society. I think that is why there has been a high degree of acceptance.
The operation of TBMs is seen as more favorable than hand mining or open cut, because there is less inconvenience at the surface, and building the tunnel itself is safer. For this reason, I think TBM tunneling will continue to increase in Mexico.
With the six TBMs currently excavating or being readied to excavate the new Emisor Oriente wastewater line, we now have seven TBMs operating in the country—this has never happened before. I think this is a tunneling boom!
Ground Control: Mitigating the Inherent Risks of Urban Tunneling
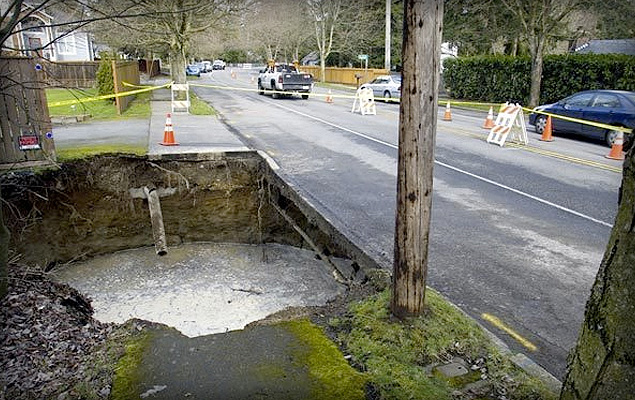
Sinkholes, as seen here at the Brightwater Conveyance Tunnels, can be an unfortunate end result of settlement. Photo Credit: TunnelTalk.com
Settlement. It is one of the biggest risks in urban tunneling and the cause of sinkholes, cracked building foundations, and tunnel collapses. Surface subsidence and upheaval have vexed contractors and equipment suppliers worldwide, but there are some proven ways to minimize ground movement, even in low cover tunnels.
Tunneling at Mexico City Metro’s Line 12 provides a good, recent example of settlement prevention. The 7.7 km (4.8 mi) route is being excavated just 7.5 to 14 m (25 to 45 ft) below downtown Mexico City. The 10.2 m (33.5 ft) diameter Robbins EPB is surfacing into eight cut and cover station sites during excavation, all along major downtown streets.
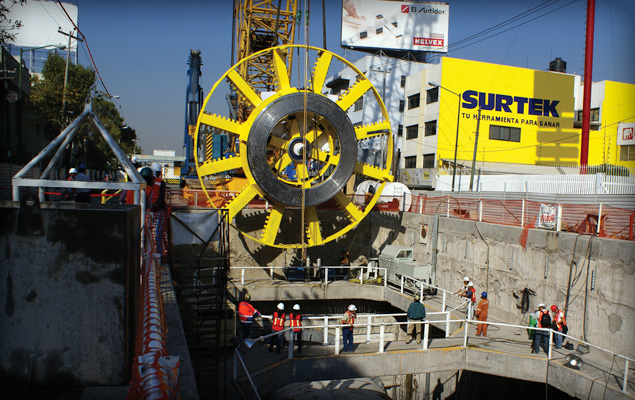
The Robbins EPB is boring just 7.5 to 14 m (25 to 45 ft) below city streets. Photo Credit: Yazmin Reyes
The ground, which consists of watery clays, sand, and large boulders up to 800 mm (2.5 ft) in diameter, makes settlement a concern. Ismail Benamar, Tunnel Manager for contractor Ingenieros Civiles Asociados (ICA), spoke about the measures they are taking to control the ground: “We have an extensive monitoring program to detect displacements and pore pressure on the surface, underground, inside the tunnel, and in the most critical structures next to the tunneling line.” The risk of surface subsidence and vibration is also being controlled by regulating the rate of advance and controlling earth pressure at the front of the machine, as well as the back-fill grouting pressure.
In particularly low cover areas, Benamar cited a reduction in EPB cutterhead rotation as one of the primary means of avoiding ground disturbance. Cutterhead rotation is kept low (around 1.5 RPM) while torque is kept relatively high.
In addition, the machine’s two-component back-filling system is used to further stabilize the space between concrete segments and bored tunnel. The liquid mixture consists of water and bentonite cement plus an accelerant, which are combined in the tail shield and harden rapidly after injection. Because the two liquids are kept separate, high pressure concrete pumps, which can disrupt the surrounding geology, are not needed.
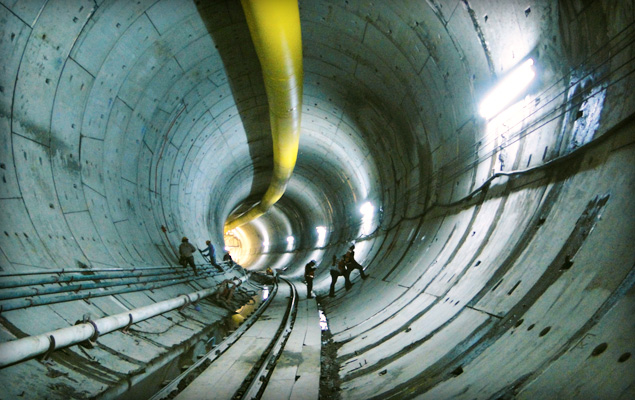
The Robbins EPB is utilizing two-component back-filling behind segments as one way of minimizing settlement. Photo Credit: Yazmin Reyes
By May 21, 2010, the machine had broken through into Mexicaltzingo Station—the first of eight cut and cover station sites along the tunnel route. Little to no settlement issues were recorded during tunneling.
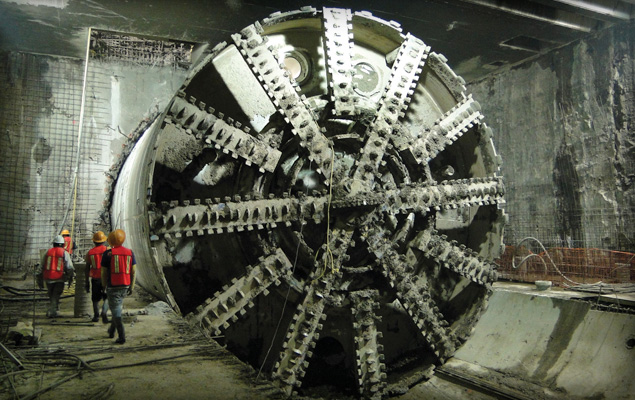
The Robbins EPB broke through into an intermediate station in May 2010. Photo Credit: Yazmin Reyes
Taken together, the methods at Mexico City Metro show the best ways to minimize settlement in urban EPB tunneling. Settlement can be due to multiple factors, including over-excavation, improper ground conditioning, inadequate back-filling, or loss of face pressure. Despite the risks, proper machine design, continuous monitoring, and a knowledgeable crew can keep ground under control.
For more about the causes of settlement and tunnel collapse, visit an online forum at tunneltalk.com
Multiple Machines: The Challenges and Successes of Delivering Three TBMs for Malaysia’s Longest Water Tunnel
Simultaneous delivery of TBMs, some of the most complex machines in the construction industry, is no easy task. Robbins TBM assembly is most often a local process—one that requires skilled workers with knowledge of components designed and manufactured all over the world.
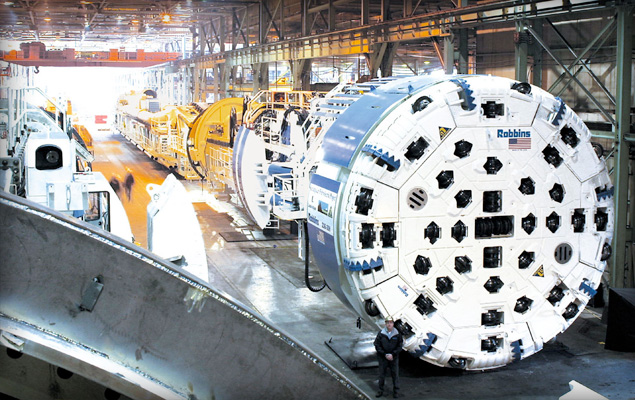
Robbins Main Beam TBMs assembled in the U.S. manufacturing facility.
Robbins use of local or nearby shops can often cut down on delivery times. A partial video of the TBM assembly process in the Robbins China-Shanghai facility is available here:
The video depicts the recent assembly of one of three 5.2 m (17.2 ft) diameter Robbins Main Beam TBMs. The machines are being built simultaneously for Malaysia’s Pahang Selangor Raw Water Tunnels, and are a good example of the assembly process.
Each machine is built at a workshop in Shanghai from components manufactured in the U.S. and China. After assembly of each machine is complete, the TBM and continuous conveyor system are shipped from Shanghai to Port Kelang in Malaysia. Once at the port, the components are trucked to the jobsite.
“One of the most difficult processes is finding a single shop that can manage the volume of fabrications and machining. The delivery times for the Malaysian TBMs are one month apart, which means that at one point you are disassembling and shipping the first machine, testing the second machine and starting assembly of the third machine,” said Kolenich. On average, each TBM requires a skilled crew of 20-30 fabricators, welders, and technicians, but shorter delivery schedules can require up to 60 people in two shifts. “We have an experienced group in China that has been building machines for many years,” he added.
Assembly of TBM #3, the first machine to be built, was completed in early July 2010. Assembly of the machine began with core components, including the main bearing and back-up structures, and finished with installation of the electrical and hydraulics systems, as well as outer components including cutterhead pieces and ground support.
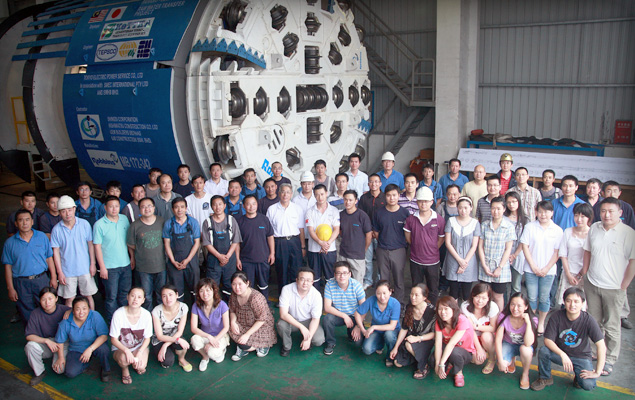
The first of three Robbins Main Beam TBMs was completed in July 2010.
“We perform all of the same quality inspections in our shops, regardless of location,” adds Kolenich. “At the end of assembly there is a two to three week no-load testing period to ensure that each machine is set up and functioning properly per the contractual and engineering requirements.”
The two other Robbins Main Beams will be completed later in 2010, with the factory acceptance for TBM #1 scheduled in August and TBM #2 in mid-September. The three machines will be launched between December of 2010 and March 2011.
For more about the Pahang Selangor Raw Water Transfer tunnels, visit the Malaysian Government’s Ministry of Energy, Green Technology, and Water.
View a short video about the project here:
Ground Support for High Cover Tunnels: What is the Best Method?
Conditions in high cover tunnels are often challenging. At the Olmos Trans-Andean tunnel, crews face 2,000 m (6,500 ft) of hard quartz porphyry, andesite, and other volcanic rocks under high stress. At two rail tunnels in China’s Gansu Province, open-type machines are boring beneath 1,400 m (4600 ft) of weak phyllite and sandstone.
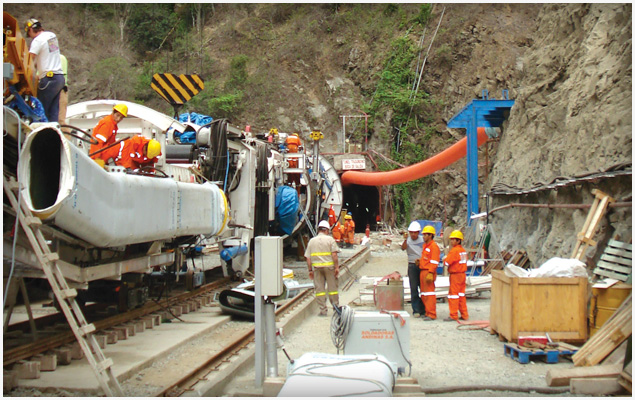
Launch of the Robbins TBM at Peru’s Olmos project, the world’s second deepest tunnel
Ground support, particularly in deep tunnel projects, is a highly debated topic. However, recent successes have pointed to several systems that work in a variety of situations. The Robbins Main Beam at Olmos was launched in 2007, and began to experience significant rock bursting and cathedralling under sections of high cover. “We encountered a 1,200 m (4,000 ft) section of highly fractured ground, with over 8,500 recorded rock bursts. Cavities also formed during tunneling that had to be injected with grout,” said John Simm, Robbins Field Service Superintendent.
To better contain the fractured rock, the machine’s roof shield fingers were removed and replaced with the McNally Support System, supplied by C&M McNally Engineering of Toronto, Ontario, Canada. The McNally support System provides the benefit of continuous support along the roof area of the tunnel, which protects workers from falling rock. The system works by replacing the curved finger shield plate for a curved assembly of pockets with rectangular cross-sections. Steel or wood slats are extruded from the pockets and bolted to the tunnel crown using a steel strap, effectively supporting and minimizing collapsing ground. As the machine advances, slats are reloaded into the pockets.
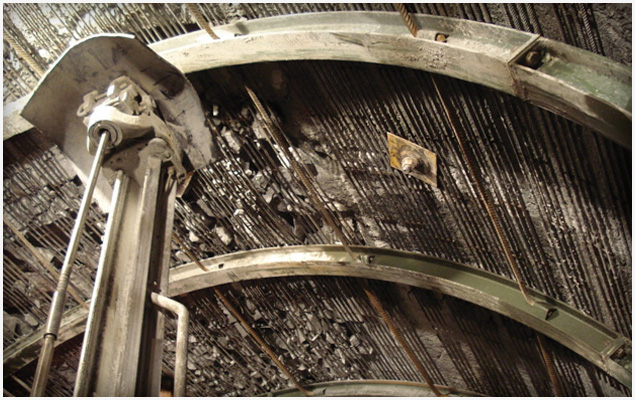
McNally slats supporting rock in the Olmos Trans-Andean Tunnel
The below video shows the crew loading McNally slats into the pockets:
The system successfully contained numerous high-pressure rock bursts at Olmos, as seen in the below video courtesy of Dean Brox from Hatch Mott MacDonald:
For the machines at China’s West Qinling tunnels, the answer is a versatile ground support system that can be adapted depending on the ground conditions. The two 10.2 m (33.5 ft) diameter Main Beam TBMs are the first Robbins Main Beam machines built with specialized ground support and no finger shields. Instead of the roof fingers, the machines are designed with mesh pockets beneath a protective shield for workers to safely install mesh panels.
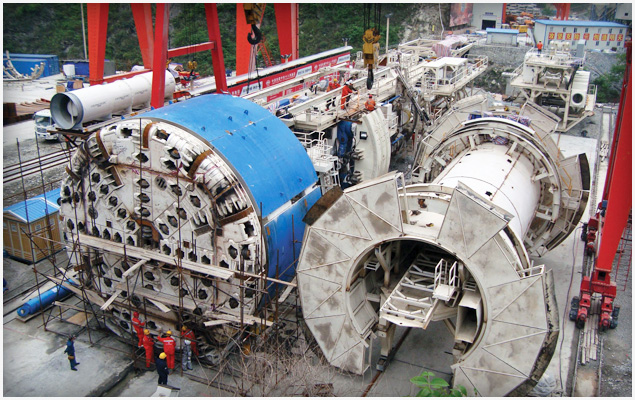
Assembly of two Robbins Main Beams with specialized ground support at China’s West Qinling Tunnels
The machines can also use the McNally Support System if needed. Modified pockets can be bolted inside the mesh windows, allowing space for short slats of steel or wood.
In addition, streamlined materials handling and separate roof and probe drills allow for improved progress in high cover conditions. Redesigned ring beam installers allow for loose assembly and expansion against the tunnel walls, and can be easily converted to install steel straps rather than full rings.
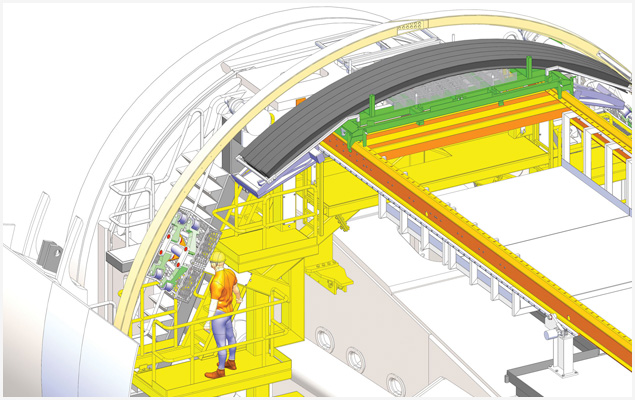
Materials including ring beams and mesh panels are transported on a remotely operated carriage, requiring fewer transfer points
Both machines are currently excavating 16.6 km (10.3 mi) long rail tunnels.
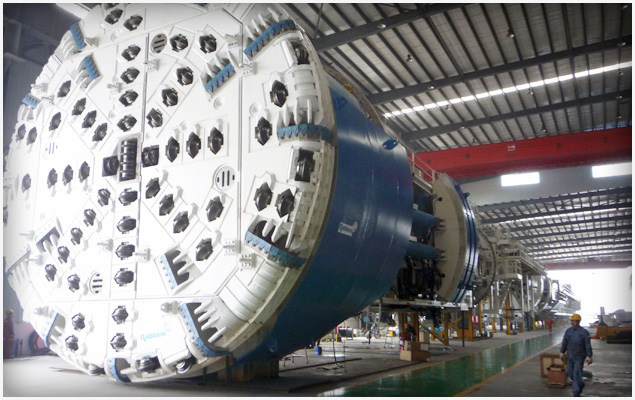
The two 10.2 m (33.5 ft) TBMs were launched in June and July 2010
For more information on ground support in large diameter tunnels, check out this recent technical paper: Large Diameter TBMs_WTC2010
Recent Posts
- Tunneling in Turkey: The Esme Salihli Railway
- Incredible India: Machines on the Move in Agra and Delhi
- Notice of Retraction and Apology
- Four Things You Need to Know about Probe Drilling and Pre-Grouting
- The Latest Updates: Records in Toronto, the News from Nepal, and More