Archives: Projects
Túnel Emisor Poniente (TEP) II
Project Overview
A Robbins Crossover (XRE) TBM was chosen to bore a 5.8 km (3.6 mi) tunnel as part of Mexico City’s wastewater management efforts, making it the first Crossover machine to bore in North America. The 8.7 m (28.5 ft) diameter machine includes features of both a hard rock single shield and an EPB in order to “cross over” into vastly different types of ground. Once complete, the tunnel will prevent flooding in urban areas and will convey sewage to the area’s first wastewater treatment plant, affecting the lives of 2.1 million people.
Geology
The tunnel path travels through a mountain with cover as high as 170 m (560 ft), through fault zones and in a section with cover as low as 8.0 m (26.2 ft) above the tunnel crown. Much of the tunnel consists of andesite rock with bands of tuff, and softer material in fault zones as well as an 874 m (2,870 ft) long section in soft ground at the end of the tunnel.
Machine Design
The Robbins XRE TBM features components like a convertible cutterhead that can be changed from a Hard Rock to EPB design, a removable belt conveyor and screw conveyor, and multi-speed gearboxes to increase torque for tunneling through difficult ground. Breakout torque is one way that the shielded TBM can propel itself through fracture zones without becoming stuck—multi-speed gear boxes can be activated to achieve high torque at a low speed, similar to how an EPB operates. With multi-speed gear boxes, the cutterhead can be freed in bad ground where it might otherwise become stuck. In hard rock, the TBM can operate in a standard low torque, high RPM mode.
The Crossover XRE has other strategies in its arsenal to deal with difficult ground. The unique TBM was designed to bore below several valleys with expected water inflows. In the event of a high water inflow, a guillotine gate located on the muck chute is able to seal off the mixing chamber from the rest of the machine. In this way the TBM can passively hold high water pressures while the crew takes measures to dewater and consolidate ground.
The machine is equipped with continuous probe drilling, with a wide drilling range to investigate ground ahead of the machine. In addition to the standard probe drill, a canopy drill provides another ring for grout drilling or forepoling close to the cutterhead and in the top 120 degrees of the tunnel, while a second probe/grout drill is located further back on the machine, allowing two different patterns of holes.
Excavation
The Crossover machine was launched in August 2015 in a hard rock configuration and mounted with 20-inch diameter disc cutters—a risky move given that the first sections of tunnel were in softer soils before the TBM hit more solid rock. The machine’s advance rates picked up quickly, with project records set in December, and again in January after the machine achieved a best day of 42.8 m (140 ft) and a best week of 185.1 m (607 ft).
Early in 2016 the TBM hit the first of several contact zones, a 30 m (98.4 ft) wide fault of fractured and blocky rock. While the excavation through the contact zone was slow going, progress picked up again in the more competent andesite rock. After an intermediate breakthrough in March 2016 into an 80 m (262.5 ft) deep shaft followed by inspection and maintenance, the TBM continued on.
By June 2016, the TBM was boring in fairly competent rock and had achieved two national records for TBM advance—one for excavating 57 m (187 ft) in one day and another for boring 702.2 m (2,303.8 ft) in one month.
While boring in fractured andesite rock in autumn 2016, the TBM encountered a naturally occurring cavern believed to be the result of either a rock fall in a transition zone, or an old, underground lake body that had eroded the rock away. The cavern was approximately 90 cubic meters in size, including about 57 cubic meters of unstable floor area. The TBM was stopped and immediate measures were taken to fill the cavern.
Changing Modes
By the end of October 2016, the TBM had reached the final section of soft ground. In this final zone of low cover, the distance from the top of the tunnel to the surface is less than 1.5 times the machine diameter, and the ground has the consistency of reconsolidated soil. The residential area meant that subsidence had to be kept to a minimum, and the decision was taken to convert the Crossover machine to EPB mode.
Conversion of the TBM to EPB mode required multiple steps. The conversion process started with the modifications of the cutterhead, adding the piping for the new foam lines, changing the hard rock bucket lips into the EPB soft ground scrapers, and removing the muck buckets characteristic of a hard rock TBM. The removable plates on the cutterhead were changed to alter the opening ratio from Hard Rock optimized to EPB optimized (from 7.9% to 18.95%). Other steps include installing mixing bars into the bulkhead, switching out the TBM belt conveyor to a screw conveyor, altering the fluid system for EPB additives, and installing tails seals and articulation seals for pressurized boring.
The machine was completely converted and ready to bore at the start of 2017. The machine started its latest section with about 18 m (59 ft) of cover, which was reduced due to the ground slope to just 12 to 14 m (39 to 46 ft). By March 2017, the TBM had performed well, with just 517 rings (about 775 m, 2.543 ft) left to bore. The TBM’s best day of production in soft ground was 13 rings (19.5 m, 64 ft) in only one 12-hour shift—impressive results despite the limited boring hours due to the residential area above. Final breakthrough occurred in late May 2017.
Jaipur Metro
Twin EPBs Excavate Under Historic Structure
Project Overview
The city of Jaipur, India is encircled by a wall six meters high and three meters thick, with seven gated openings. It is below these delicate and iconic structures that Jaipur’s first Metro, Line 1, travels. For this project, Contractor Continental Engineering Corporation (CEC) decided to refurbish their two 6.52 m (21.3 ft) diameter Robbins EPBs. The machines bored twin tunnels 2.3 km (1.4 mi) in length, directly beneath the historic Chandpole Gate.
Geology
In this particular project, the geology was not anticipated as a main concern. The bores consist mainly of silty sands, with a minor amount of clay and gravels. However, the geological conditions coupled with the extremely low overburden in the area of the launch shaft, especially the section passing beneath Chandpole gate, was cause for major concern.
The Machines
The contractor opted to refurbish its two 6.52 m (21.3 ft) diameter Robbins EPBs originally used for the New Delhi Metro Project. The Robbins EPBs were refurbished in India, and customized for the Jaipur project. The original machines for New Delhi bored a straight tunnel and did not require active articulation, but a 430 m (1,410 ft) radius curve in Jaipur necessitated that the machines be articulated. The shields were essentially cut in half and another section put in to form articulation joints in the contractor’s casting yard. In addition, new a+b grouting systems were installed as well as sophisticated tunnel guidance systems to monitor each machine’s position.
Boring Below the Historic Chandpole Gate
Chandpole gate, one of the seven, is directly above the bore path for the Line 1 extension, and serves as a historical landmark. The construction materials of the walls and gate consist of irregularly-sized pieces of stone cemented together with lime mortar and faced with a sand and lime mortar render that provide little to no resistance to tunneling-induced settlement. Contractually the allowable limit for surface settlement was set at 4 mm (.16 in). Yet, there was also an Indian archeological law in place that made the stakes a bit higher. It states, “Whoever destroys, injures, mutilates, defaces, alters, removes, disperses, misuses, imperils or allows to fall into decay a protected monument, or removes from a protected monument any sculpture, carving image, bas-relief, inscription or other like object, shall be punishable with imprisonment for a term which may extend to six months with a fine which may extend to five thousand rupees or with both.”
The key to boring beneath the gate without any adverse effects relied on refining the TBM operating parameters before the TBM reached the zone of influence. As this had been achieved, these parameters were maintained after the restart and similar results were achieved up until ring No. 75, where surface heave increased slightly. Due to the increase in heave the EPB pressure was reduced to 1.2 bar and cutterhead speed to 1.1 RPM. These changes reduced the heave to within tolerance. Although vibrations levels were minimal, as the TBM approached the gate the cutterhead speed was further reduced to 1.0 RPM to reduce the risk of damage by vibration. The machine passed beneath the gate and through the zone of influence without incident using these parameters. The maximum recorded settlement in the vicinity of the gate was 2 mm (.08 in) and absolutely no adverse effects were sustained to the gate. The lessons learned on the first drive were applied to the second drive and TBM II also passed beneath the gate with minimal settlement and no damage to the gate.
Kargi Hydroelectric Project
Robbins Double Shield TBM Overcomes Challenging Conditions and Spurs the Design of Crossover TBMs
Project Overview
Driven through a mountainside with 600 m (1,968 ft) of cover in Central Turkey, the Kargi Kizilirmak Hydroelectric Project is one of the most challenging tunneling projects ever completed in the region. A 10-m (32.8 ft) diameter Double Shield TBM was supplied to contractor Gülermak to bore the headrace tunnel that would divert water from the dam to the powerhouse. The entire tunnel, with both TBM and drill and blast portions, is 11.8 km (7.3 mi) in length. The project generates 470 GWh of power annually for project owner Statkraft, an amount sufficient enough to supply approximately 150,000 homes. The extremely challenging ground conditions of this project made it necessary for the machine to be modified in-tunnel. The results of which largely contributed to the creation of the Crossover machines used today.
Geology
The expected geology along the tunnel alignment consisted of Kirazbasi complex Kargi ophiolites (including sandstone, siltstone and marl) for the initial 2,300 meters (7,545 ft), followed by 1,000 meters (3,280 ft) of Kundaz metamorphites (including marble, metalava and metapelite), and the remaining 8,500 meters (27,887 ft) consisted of Beynamaz Volcanites (including basalt, agglomerates and andesite). The anticipated strength of the rock was up to 140 MPa. Multiple fault zones and transition zones added to the complexity of the geological conditions.
Launch
Almost immediately after launch in early 2010, the machine encountered geology that was substantially more problematic that was described in the geological report. The geology consisted of blocky rock, sand, and clays. 80 meters (262 ft) into the bore the TBM became stuck in a section of collapsed ground. As a countermeasure that was immediately put into place to avoid the cutterhead becoming stuck in the blocky material, crews began boring half strokes and half resets. Despite these measures, the machine encountered a section of extremely loose running ground with high clay content. Another collapse occurred in front of the cutterhead and the weight of the material trapped the cutterhead.
After assessing all the available options, it was decided that a bypass tunnel would be required. Robbins Field Service assisted Gülermak with bypass tunnel design and work procedures to free the cutterhead and stabilize the disturbed ground. Blasting techniques were ruled out due to concern over further collapses caused by blast induced vibration; hence, the excavation was undertaken using pneumatic hand-held breakers. Hopes that the section of bad ground would be an isolated occurrence were quickly proved wrong, and the actual complexity of the geology became apparent. Six more tunnels were needed within the first 2 km (1.2 mi) of tunneling.
Both the contractor and manufacturer worked together to develop and improve bypass tunneling and hand tunneling techniques, resulting in an average bypass tunnel construction time of just 14 days. All tunnels were completed safely and in a timely manner, though there were of course significant delays associated with the downtime. Despite the setbacks of these multiple events, the TBM did succeed in crossing numerous faulted sections that would have trapped a machine with less power. Bypass tunneling was successfully completed and at that point the section of bad ground was believed to be an isolated one.
The Beginnings of the Crossover TBM
In order to improve progress in the difficult conditions, the contractor, owner, consultants, and Robbins engineers worked together to generate solutions. The contractor, with the assistance of the field service team, installed a Robbins custom-built canopy drill and positioner to allow pipe tube support installation through the forward shield. Drilled to a distance of up to 10 m (33 ft) ahead of the cutterhead, 90 mm (9 cm) diameter pipe tubes provided extra support across the top 120 to 140 degrees at the tunnel crown. Injection of resins and grout protected against collapse at the crown while excavating through soft ground. As a result of successful use of the probe drilling techniques, Gülermak was able to measure and back-fill cavity heights above the cutterhead in some fault zones to over 30 m (98 ft) and, in addition, was able to help detect loose soil seams and fractured rock ahead of the face.
To further mitigate the effects of squeezing ground or collapses, custom-made gear reducers were ordered and retrofitted to the cutterhead motors. They were installed between the drive motor and the primary two-stage planetary gearboxes. During standard boring operations the gear reducers operate at a ratio of 1:1, offering no additional reduction and allowing the cutterhead RPM to reach design speeds for hard rock boring. When the machine encountered loose or squeezing ground the reducers were engaged, which resulted in a reduction in cutterhead speed but the available torque was increased by nearly double. The net effect of the modifications allowed the Double Shield TBM to operate much like an EPB in fault zones and squeezing ground with high torque and low RPM—these methods effectively kept the machine from getting stuck. In addition, short stroke thrust jacks were installed between the normal auxiliary thrust to double total thrust capabilities.
The TBM design changes gleaned from Kargi were not considered to be isolated, and immediately began to inform the design of Robbins’ new line of dual-mode type machines, termed Crossover TBMs. Crossover TBMs are also called hybrid or Dual Mode machines, and are able to “cross over” into distinct types of geology. Crossover TBMs feature aspects of two TBM types, and are ideal for mixed ground conditions that might otherwise require multiple tunneling machines.
Innovative Results
Despite the slow progress initially, the Robbins Double Shield TBM made some remarkable advances once modifications were in place, which essentially made it a Double Shield TBM with Crossover features. An advance rate of 600 m (1,986 ft) in one month was achieved in March 2013 and a project best of approximately 723 m (2,372 ft) was achieved in spring 2014, including a daily best of 39.6 m (130 ft) in April 2014. In so doing the TBM significantly outperformed a drill and blast heading progressing from the opposite end of the tunnel. Crews at that heading progressed in relatively good ground conditions for 4 km (2.5 mi), where they achieved advance rates of nearly 300 m (984 ft) per month. The TBM bored 7.8 km (4.8 mi) of the tunnel in total, making its final breakthrough in July 2014.
Grosvenor Decline Tunnel
First TBM to be used for Mining Tunnels in Queensland
Project Overview
The Grosvenor Mine, a greenfield coal operation, was the first to utilize TBM technology for mining tunnels in Queensland. Owner Anglo American opted for an 8 m (26 ft) diameter Robbins Dual Mode “Crossover” TBM and continuous conveyor system, which was assembled on location using Onsite First Time Assembly (OFTA) with onsite support from Robbins’ experienced Field Service team. The Crossover XRE TBM was picked over the traditionally-used roadheader method for several reasons, including excavation speed and tunnel maintenance. The machine bored two decline access tunnels at grades of 1:6 and 1:8, one for conveyors and another for people and equipment.
Geology
Ground conditions varied throughout each tunnel. Both drifts contained geology consisting of mixed soil and rock conditions, with the first 300 m (984 ft) or so of each tunnel containing the majority of the mixed ground such as soft clays and soils.
Machine Design
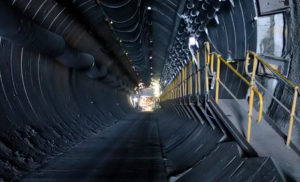
OLYMPUS DIGITAL CAMERA
The machine’s Crossover capabilities enabled it to operate in both hard rock and mixed ground. In addition, the TBM was required to operate in gaseous conditions. The unique TBM design included a cutterhead capable of interchanging hard rock and soft ground cutting tools, a two-stage center-mounted screw conveyor, a “quick removal” shield system, and flame-proof machine components due to the possibility of methane gas in the underground environment. A machine with EPB capabilities was chosen not only due to the presence of softer ground, but also to contain the methane gas where it could then be diluted or safely removed from the tunnel.
Excavation and Breakthrough
Construction on the Grosvenor project began in July 2012. The first of the decline tunnels, for conveyors, was excavated between the end of December 2013 and the beginning of May 2014, after achieving advance rates of up to 90 m (295 ft) per week. The Quick Removal System was a success, allowing the TBM inner core to be retracted back to the surface from a 160 m (525 ft) depth using specially designed transport dollies. In order to transport the machine to the next tunnel 2 km (1.2 mi) away, the TBM had to be split into two sections and required a large 600 metric ton lift.
The machine was re-commissioned for the men & materials tunnel with a new set of shields, and commenced boring in November 2014. Excavation was completed in 88 days at an average of 10.9 m (35.7 ft) per day, with a best day of 25.2 m (82.7 ft). The TBM averaged 70 m (229.7) a week, about 14 times faster than a roadheader. The bore itself was similar to the first, with few challenges encountered other than elevated methane gas levels that required several temporary stoppages in order to safely remove the gas from the tunnel. Final breakthrough was reached on February 9, 2015. Upon completion of the second tunnel, the machine shields were again left in place to provide continuous support.
Black River Tunnel
Onsite Assembly on the Banks of the Black River
Project Overview
In 2000, the Ohio EPA ordered the City of Lorain to address overflows that violated the City’s National Pollutant Discharge Elimination System (NPDES) permit. After studying options, including the construction of an equalization basin in downtown Lorain, a deep tunnel option was selected. In order to construct the tunnel, the city required the assistance of a USD $65.87 million loan from the Water Pollution Control Loan Fund through Ohio EPA’s Division of Environmental and Financial Assistance. The major components of the Black River Tunnel include the launch shaft and reception shaft – approximately 11 m (36 ft) in diameter and 50 m (165 ft) deep – and the main 1.7 km (1.0 mi) long tunnel with a finished diameter of 5.8 m (19 ft). The project route runs along city property roughly parallel to the Black River, beginning at the launch shaft near the Black River Wharf and terminating near the Black River Wastewater Treatment Plant.
Geology
Ground conditions consisted of soft Cleveland shale, at times layered and laminated in the tunnel crown area.
Onsite First Time Assembly
The mammoth 7.0 m (23 ft) diameter Double Shield machine was built using Onsite First Time Assembly (OFTA)–a Robbins-developed method that saves contractors in shipping time, costs, and man-hours worked. Using the OFTA approach, individual systems are tested prior to delivery but the machine is never fully assembled in the shop. Robbins field service technicians work on location with the contractor to assemble the machine and provide support. Launch of the TBM took place on November 18th, 2013 — approximately three months after assembly began.
Excavation and Breakthrough
Construction of the main tunnel began in late autumn 2013 with both the Double Shield TBM and continuous conveyor system running at the site. Robbins supplied an in-tunnel continuous conveyor system and space-saving J-type vertical conveyor to provide more open area in the launch shaft.
The Double Shield machine was used in a unique manner during boring. The soft shale was excavated with minimal cutter wear, and rather than concrete segments, ring beams were erected within the tail shield for installation as the machine passed. The lagging was spaced at 45 cm (18 inch) intervals with wire mesh panels.
Cleveland shale made for speedy excavation; so fast that it was challenging for the continuous conveyor system to keep up at times. The contractor confirmed that the TBM was mining so fast it could not excavate at its maximum rate. Rehak explained that the fairly soft ground also made for minimal cutter wear, with only seven cutters changed during course of the bore—four of them as a precautionary measure only.
About 13 sections of bad ground 30 m (100 ft) across were encountered during tunneling, or about 25% of the soft shale geology, which made ground support difficult at times. Those sections consisted of layered and laminated rock that broke from the tunnel crown before ring beams could be expanded, requiring extra chipping and rock relief to expand each rib to the correct diameter. Once workers fine-tuned the technique, they were able to do 12 to 14 rings per day–compared to just one or two rings before the process was refined–even in the sections of bad ground. In more stable sections production averaged 18 to 20 rings per day—a rate the contractor considered very good considering they were erecting steel ribs. Now that tunneling is complete, a final monolithic pour will solidify the lining.
By the time of the machine’s breakthrough on April 29, 2014, the TBM was averaging 21 m (70 ft) per day, and getting up to 24 m (80 ft) per day for multiple days in a row. After tunneling was completed, a final monolithic pour solidified the tunnel lining.
Alimineti Madhava Reddy (AMR)
Project Overview
At 43.5 km (27 mi), the Alimineti Madhava Reddy (AMR) Project will be the longest tunnel without intermediate access in the world when complete. The tunnel will transfer floodwater from the Krishna River to arid regions of India’s Andhra Pradesh state, providing irrigation to 1,200 km2 (400,000 acres) of farmland and clean drinking water to 516 villages.
Contractor Jaiprakash Associates Ltd. (JAL) won the USD $413 million engineer-procure-construct contract in 2005 from the Andhra Pradesh government to construct a head regulator and two tunnels, including the main 43.5 km (27 mi) tunnel. On May 26, 2006, JAL awarded a complete contract to The Robbins Company for two 10.0 m (32.8 ft) diameter Double Shield TBMs, as well as conveyor systems, back-up systems, spare parts, personnel, and technical support.
The first of the two machines was launched in March 2008 after an unprecedented onsite assembly. Both of the machines were initially assembled onsite using the Onsite First Time Assembly (OFTA) process. OFTA, rather than assembling the machine in a manufacturing facility, saves both time and money to the contractor in terms of personnel and shipping costs.
Assembly of the first machine took place in a large launch pit at the outlet portal site, using gantry cranes to hoist components into place. Machine parts including the cutterhead, gripper system, forward shield, and telescopic shield were then assembled in a concrete “cradle”. The assembled TBM and back-up then crawled forward by reacting against invert segment pieces installed progressively up to the tunnel entrance. The second Robbins machine was assembled onsite at the opposite end, or the inlet portal.
Geologic conditions consist of quartzite zones up to 450 MPa (65,000 psi) UCS, layered and separated by shale for approximately 50% of the length, with granite (160 to 190 MPa/ 23,000 to 28,000 psi UCS) for the remaining 50%. Both machines feature back-loading 20-inch diameter cutters for longer cutter life in the abrasive conditions. Other design modifications include specially designed drive motors to run each machine at a higher than normal rpm for optimal penetration rates in the hard rock.
TBM Launch
AMR Outlet Tunnel
Initial conditions at the AMR outlet included intermittent power outages, which were supplemented by onsite generators, as well as difficult geology. Severely blocky ground at the outset tore the conveyor belt and slowed the tunneling process. Large rock blocks made their way through the muck buckets, stopping in transfer hoppers and point loading the conveyor system. To counteract this problem, the spacing of grizzly bars on the muck buckets was reduced and additional bars were added so the boulders could not pass onto the conveyor system. Grill bars were also added to the AMR inlet machine in anticipation of similar ground conditions. In good ground, the grill bars can be removed to allow a higher flow of material into the muck hopper.
AMR Inlet Tunnel
The Inlet machine was one week away from launch in October 2009 when a 100-year monsoon hit the region. The natural coffer dam wall at the inlet site was not designed to withstand a major flood, and was breached by the flood waters. Flood control doors were not opened in time to release the water downstream, causing the significant rise in water levels. The launch pit was inundated with over 20 m (66 ft) of water, leaving the crown of the TBM beneath over 10 m (33 ft) of water for approximately ten days until it could be pumped out.
The TBM and backup were jacked back 12 m from the tunnel face to allow removal of the cutterhead and inspection of the main bearing. Cleanup lasted approximately 14 days which included jet washing the machine and removing silt 300 to 400 mm (12 to 16 in) thick which was left on the machine. A major portion of the TBM components were replaced to get the machine back to running condition.
Tunnel Excavation
The beginning of 2010 (6th km) was marked by the first cutterhead refurbishment, deemed necessary to restore bucket lip housings and face wear plates that were severely worn out after excavation of unusually abrasive and hard rock. After refurbishment, the monthly advance slowly improved to within the range of 300-330m. However, consistently challenging conditions during the same time period in 2010 meant average machine utilization was 21.7%.
To help avoid sudden breakdowns or delays caused by the constant extremely high vibrations propagating from the cutterhead up to the back-up bridge gantry, a careful inspection of all the exposed components was implemented during and after each stroke, or at any time that a sudden change in boring values or other anomalies occurred. All the cutter fasteners, bucket lip bolts, grill bars, main bearing studs, seal clamp rings, seals and wear bands suffered from the excessive stresses induced and needed to be checked constantly. With the implementation of this regime it was possible to reduce the number of blocked cutters and any possible damage to the head. A second cutterhead refurbishment was planned and carried out in the 12 weeks between June and September 2011 by replacing and removing all damaged carbide wear plates, in particular in the outer/gage section of the head.
When tunneling with limited geological data in a remote location, it is quite often necessary to find technical and practical countermeasures, particularly in the case of AMR where adverse excavation conditions where a large diameter machine is boring one of the world’s longest tunnels. Constant monitoring of the boring data, and a routine maintenance regime play a significant role in the system performance. While hard rock conditions are continuing to be a challenge for both the inlet and the outlet portal tunnels, training of the crew members as to how to deal with the unusually abrasive and hard rock has been invaluable.
As of November 2020, both machines have excavated at least 70% of their respective tunnels. Since the jobsite has continually experienced very hard, abrasive rock conditions, it has allowed for research and testing of harder, more durable cutter rings because of the extreme conditions.
Upper NW Interceptor Sewer
Project Overview
The Upper Northwest Interceptor (UNWI) sewer system in Sacramento, CA is comprised of nearly 30 km (18 mi) of tunnel. The system was created to ensure both present and future sewer needs are met, particularly during severe wet weather storms when existing systems are at risk of overflowing. The UNWI system was split up into nine sections with Section 1 starting in Natomas and Section 9 ending in Citrus Heights neighborhoods. Sections 3 through 9 were completed by 2008. The system is capable of conveying up to 560 million liters (148 million gallons) of wastewater per day.
On August 22nd, 2007, Sacramento Regional County Sanitation District (SRCSD) awarded the USD $97.3 million construction contract to Traylor/Shea JV to complete Sections 1 & 2 of the UNWI Sewer Project. Traylor/Shea chose a 4.25 m (13.9 ft) Robbins EPB optimally designed for ground consisting of clay and running sand.
EPBM
The Robbins EPBM was equipped with a spoke-type cutterhead and wear resistant cutterhead plates. Bentonite foam injection ports in the cutterhead allowed for stabilization of the tunnel face and smooth muck flow. Muck was removed using a 500 mm (20 in) diameter shaft-type screw conveyor emptying onto a Robbins continuous conveyor system. Two-component backfill grout was used to further stabilize ground behind segments, helping to reduce the risk of surface subsidence. The advantage of using a two-component grout was that the mixture could be pumped using a standard concrete pump, rather than the high-pressure pumps often needed with one-liquid concrete fills. By reducing the pump pressure, there was less chance of disturbing the surrounding soils.
The machine, which used active articulation rather than passive articulation, was able to negotiate curves down to a 400 m (1,300 ft) radius. Active articulation was chosen because it allows the front and rear shield to turn independently of the thrust cylinders, eliminating the common problem of ring deformation in curves.
Tunnel Excavation
The EPB began boring in January 2009 from the New Natomas Pump Station. The tunnel profile below the spring line consisted mostly of sand, while the top part of the tunnel face was primarily in clay. The tunnel invert ranged from 7 to 14 m (23 to 46 ft) below the surface, with groundwater present throughout.
To shorten construction time, Traylor/Shea and the SRCSD wanted to use a new type of tunnel liner, one never before used in the United States. Precast concrete segments 228 mm (9 in) thick were molded with embedded PVC sheets 1.8 mm (0.07 in) thick. The PVC liner protects the concrete from degradation due to corrosive sewer gases. The final result is a finished tunnel that requires no final carrier pipe, reducing time for the pipeline to become functional.
Continuous conveyors were also chosen by Traylor/Shea due to the increased efficiency, reduced startup time, and higher availability than muck cars in most situations. The conveyor system was specially designed for the 5.7 km (3.6 mi) tunnel in varying ground conditions. Features included sealed transfer points and receiving hoppers, with urethane rubber being used to seal points and minimize spillage. The foam and bentonite additives helped maintain a smooth consistency of muck which flowed on the conveyor even when significant ground water was present.
Throughout the bore, the machine achieved some of the highest rates in soft ground TBM tunneling with multiple advances of 210 m (690 ft) per week, as well as daily rates of 50 m (165 ft) in three eight-hour shifts. In addition, the continuous conveyor system operated at over 90% availability for the duration of tunneling. Boring was completed on Nov. 21, 2009, when the Robbins EPBM broke through more than two months ahead of schedule.
West Qinling Rail Tunnels
Twin TBMs set World Records under High Cover
Project Overview
The West Qinling tunnels are part of the Chinese Government’s Lanzhou to Chongqing Railway, a massive 820 km (500 mi) long scheme that links the capital of Gansu Province (Lanzhou) with southwestern Chongqing, a mega-city of over 35 million people. The parallel rail tunnels are for freight, and link the city of Longnan with the towns of Waina, Luotang and Fengxiang within Gansu Province. The new railway, at a cost of USD $11.3 billion, shortens transport times from 17.5 hours to 6.5 hours and enables an annual freight capacity of 100 million metric tons (110 million US tons). Trains run on the double track lines at 160 km per hour (100 mph), with a 50-train daily maximum.
In January 2009, China Railways signed a contract with Robbins for the supply of twin 10.2 m (33.5 ft) diameter Main Beam machines. The TBMs would be used to excavate two 16.6 km (10.3 mi) tunnels through the Qinling Mountains.
Geology
Geology in the two tunnels consisted of 30 to 80 MPa (4,300 to 11,600 psi) UCS sandstone and phyllite rock beneath more than 1,400 m (4,600 ft) of cover. The corresponding ground support program consisted of continuous mesh and rock bolts, with either ring beams or steel straps, for the length of the tunnel. Rather than roof shield fingers, protected mesh windows were used to install ground support immediately behind the cutterhead. In the event that extremely poor ground was encountered, the mesh pockets could be easily modified to use the McNally Support System, patented by C&M McNally Engineering of Toronto, Ontario, Canada for exclusive use with Robbins TBMs. The McNally System utilizes steel or wood slats to provide continuous support along the roof area of the tunnel, protecting workers from falling rock.
Main Beam TBMs
The two machines, for contractor China Railways 18th Bureau (Group) Co., were assembled at a local workshop and transported to the jobsites, where they were assembled on bridges spanning a deep valley. The first machine, for the Left Line, was launched at the end of June 2010 after being walked through a 2.0 km (1.2 mi) long adit tunnel. The second machine, for the Right Line, was launched on July 17, 2010. The TBM tunnels were just 40 m (130 ft) apart and located approximately 1,000 m (3,280 ft) above sea level, about halfway up Qinling Mountain.
Tunnel Excavation
The two Robbins TBMs advanced at world record rates in exceedingly difficult conditions. The first Main Beam Machine advanced 235 m (771 ft) in one week and 841.8 m (2,761 ft) in one month during Spring 2011 – rates much higher than any ever recorded for TBMs in the 10 to 11 m diameter range. The fast advancing Left Line machine also broke through into an intermediate adit tunnel on May 28, 2011 at the 5.5 km (3.4 mi) mark, where it underwent planned maintenance and inspection. Within several weeks the machine was launched again to bore the rest of its tunnel.
Despite the conditions of phyllite and limestone with high quartz content, only about 100 cutters were changed on the Left Line TBM. The Right Line machine, launched a month later and about 1,000 m (3,280 ft) behind, also experienced good cutter wear. By 2013, both machines had made their final breakthroughs in their respected tunnels.
Pula Subbaiah Veligonda Project
Double Shield bores Water Transfer Tunnel beneath Indian Tiger Sanctuary
Project Overview
Beneath India’s largest tiger sanctuary, the Nagarjuna Sagar National Park, tunnel boring machines are orchestrating one of the largest water transfer schemes in India. A Robbins Double Shield TBM is boring tunnel No. 2 of the Pula Subbaiah Veligonda project for Coastal Projects Ltd. (CPL), of the CPL/ Hindustan Construction Company (HCC) JV.
On the Krishna River, on the right bank of the Srisailam Canal, lies the future inlet site for the Pula Subbaiah Veligonda Project. Once complete, the system will draw 1.2 billion cubic meters (317.0 billion gallons) of flood water annually from the foreshore of the Srisailam reservoir. Two parallel, 19.2 km (11.9 mi) long tunnels will transfer water via a network of five canals to over 1,600 square kilometers (395,368 acres) of farmland in the three districts of Prakasam, Nellore, and Kadapa. Up to 243 cubic meters per second (64,193 gallons per second) of water will travel through the bored tunnels to a feeder canal.
In October 2007, a USD $180 Million contract was awarded to Coastal Projects Pvt. Ltd (CPPL). In November, CPPL signed a contract for a 10.0 m (32.8 ft) diameter Robbins Double Shield TBM and continuous conveyor system. In addition to the machine and conveyor, spares and key operating personnel were sent to the jobsite to excavate tunnel No. 2 starting from the outlet end.
The Veligonda tunnel No. 2 is located in sedimentary rock on the western margin of the Cuddapah Basin, where a number of faults and folds make for complex geology. Rock includes quartzite with interbedded shale (60%) and shale with limestone and phyllite (40%) ranging from 90 to 225 MPa (13,000 to 33,000 psi) UCS. Two major faults are present along with some ground water.
Equipment Design
The Double Shield machine utilizes sixty-seven 20-inch diameter back-loading cutters to combat the tough ground conditions. Specially designed drive motors allow the machine to run at a higher than normal RPM, compensating for low penetration rates in the hard rock. In squeezing ground, the cutterhead is also capable of vertical movement allowing for overboring. The machine also has a probe drill which allows for verification of geology 30 m (98 ft) ahead of the TBM. The drill is capable of 360º rotation and can alternatively serve as a grout consolidation drill. Large 40 kW (54 hp) dewatering pumps located on the back-up system have been specially designed to pump any water away from the tunnel face. As the TBM bores, it erects 300 mm (12 inch) thick concrete segments in a 6+1 arrangement, making the final tunnel diameter 9.2 m (30 ft).
Muck haulage requires one of the most extensive conveyor systems ever used in India. The continuous steel cable belt, the longest single flight ever provided by Robbins, will eventually extend 19.2 km (11.9 mi) and requires four main drives and three booster drives.
Launch and Assembly
The machine was assembled in just four months using Onsite First Time Assembly (OFTA). OFTA is a process that allows machine components to be initially assembled at the jobsite, rather than in a manufacturing facility, typically providing savings in terms of man-hours and shipping costs. Assembly went well despite harsh local temperatures, which can climb to 45˚C (113˚F) daily. In addition, some components could only be installed at night due to thermal expansion in the midday heat.
Excavation
The Robbins TBM was launched into difficult ground at rates of up to 330 m (1,080 ft) per month, by adopting an extensive program of probe drilling and pre-grouting. Multiple drill holes were bored 30 m (100 ft) ahead prior to every machine push, and grout was then injected at depths of 25 to 30 m (80 to 100 ft). The Robbins TBM then advanced into an unforeseen area of disturbed geology and was inundated with flowing material. The machine became stuck, despite the probe drilling program. It was freed by excavation of a bypass tunnel and continues to excavate in difficult geology.
Updates of this project will be posted as boring continues.
Kota City Water Supply Project
Project Overview
After many failed attempts, spanning the course of eight years, just three hard rock crossings remained on a vital water supply line in Kota City, Rajasthan, India. Previous contractors had attempted to excavate the crossings in hard quartzite using hand mining and HDD, which were later abandoned due to low production rates. Simply hand mining the 11 m (36 ft) long by 4.5 m (15 ft) wide launch pit took four months, at rates of 200 to 300 mm (8 to 12 in) per day. In 2008, Contractor Vichitra Constructions Pvt. Ltd. was contracted to complete the difficult 50 m (164 ft) long crossings.
The 13 km (8 mi) pipeline, part of the government’s Rajasthan Urban Infrastructure Development Plan (RUIDP), was used to increase water supply and fight water contamination problems in the city. The finished system provides 24 million liters (6.3 million gallons) of water per day to about 70,000 people.
After researching various technologies, Vichitra purchased a 1.5 m diameter Robbins Small Boring Unit (SBU-A) with 11.5 inch disc cutters and a Robbins 60-1270 Auger Boring Machine (ABM). The technology was supplied by Robbins Tunneling and Trenchless Technology (India) Pvt Ltd, a local subsidiary based in New Delhi who also provided the contractor with technical support, crew members, and cutter rebuild services.
Geology
Much of the crossings consisted of quartzite rock (200-250 MPa / 29,000-36,000 psi), with some tracts of soil and mud. The excavation was remarkable considering the machine bored rock strengths outside the normal range generally excavated by SBU-As.
SBU-A
Small Boring Units, available in diameters from 24 to 72 inches, are typically used on crossings up to 500 ft in length utilizing a standard Auger Boring Machine (ABM) and steel casing. During excavation, the SBU-A is welded to the lead casing while the ABM provides both torque and forward thrust to the cutting head. The circular cutterhead is fitted with single disc cutters to excavate hard rock, or a combination of single disc cutters, two-row tungsten carbide insert cutters, and carbide bits in mixed ground. Disc cutters penetrate the rock face, creating a “crush zone” through which fractures propagate. Material between adjacent crush zones then falls from the face. Muck scrapers scoop the muck into openings on the cutterhead. Muck is then transferred through a full-face auger for removal.
Crossing Excavation
Three rail bores were completed by autumn 2008 in abrasive, hard rock. The crossings below a railroad were excavated in two 50-m (164-ft) long passes from either side of the tracks. The first pass, with advance rates of 1.5-m (5-ft) per hour, broke through into a center pit located between the two sets of tracks. A third 14-m (46-ft) long bore was added underneath a roadway after difficulties with open-cut operations in hard rock.
Recent Posts
- Twin Robbins EPBs make milestones near Taj Mahal
- Long Haul TBM: Use of a Rebuilt Main Beam Machine at the DigIndy Tunnel System in Indianapolis, IN
- Evaluating TBM Design and Performance, 30 Years Apart: The Lesotho Highlands Water Tunnel, Phase 1 and Phase 2
- Overcoming Mountainous Geology at Nepal's Sunkoshi Marin Project
- Swift Robbins TBM breaks through 11 Months Early